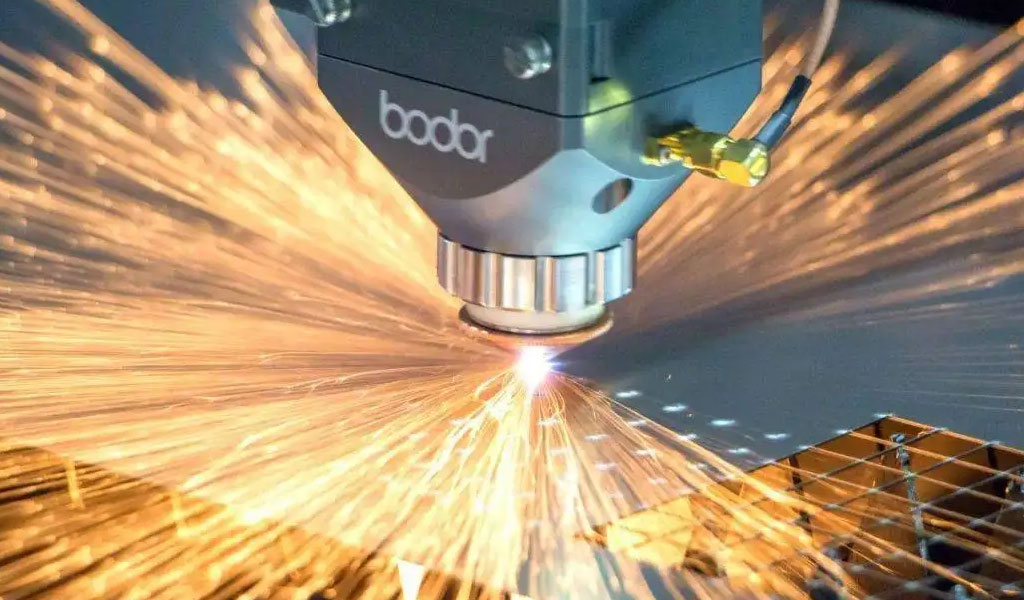
The article briefly explains the application characteristics and welding characteristics of aluminum alloys, from the aspects of welding preparation, adding welding seam shielding gas, using double-spot laser welding, laser wire filling welding or laser-MIG hybrid welding, and adjusting process parameters. As a quality assurance method, the existing high-end laser head can also be used to stabilize the welding quality in industrial production.
The Application Characteristics Of Aluminum Alloy
Aluminum alloy is widely used in many fields such as aviation, aerospace, automobile, machinery manufacturing, shipbuilding and chemical industry due to its light material, corrosion resistance, low temperature performance and good mechanical comprehensive performance. With the country’s pursuit of energy-saving economy in recent years, the demand for aluminum alloys has reached a new level. At present, the main aluminum alloys used in the automotive industry are Al-Mg (5000 series), Al-Mg-Si (6000 series) and Al-Mg-Zn (7000 series). 6000 series or 7000 series alloys are used for parts with high strength requirements such as beams and columns. Studies have shown that the use of aluminum alloy materials to appropriately reduce the weight of the car can reduce fuel consumption by 37%; the load of the suspension device can be reduced by 18%; the vibration intensity can be reduced by 5%. While major automobile factories increase their investment in aluminum alloy processing R&D and manufacturing, aluminum alloy welding has become a basic problem that has to be solved.
The Welding Characteristics Of Aluminum Alloys
At present, conventional methods such as TIG welding and MIG welding are mainly used to weld aluminum alloys. Using conventional welding methods, large heat input results in wide welds and shallow penetration, aluminum alloys conduct heat quickly, and a large amount of hydrogen is dissolved at high temperature during metallurgy. It is metallurgical pores; the moisture in the incompletely melted oxide film is decomposed into pores formed by hydrogen due to thermal decomposition, which is called oxide film pores); due to the fast metallurgical speed, the welding seam metal grains are coarse, and the softening of the welded joint can reduce the strength to 40%. %; Aluminum alloy has a low melting point and fast thermal conductivity, and the molten metal has poor fluidity, which makes the welding seam unsightly; the heated area is large, and the processing material is easily deformed, which affects the processing dimensional accuracy. The conventional welding quality of aluminum alloys is difficult to guarantee, and the welding speed is difficult to meet the requirements of mass production.
With the improvement of the popularization level of laser cutting applications, the use of laser welding of aluminum alloys has a small heat input and a concentrated heat source. Especially after the advent of fiber lasers, the energy density of laser welding aluminum alloys is more concentrated, the laser wavelength is shorter, and the high reflection can be obtained. improve. Through laser wire filling, laser-MIG hybrid welding, dual-spot laser welding and other processes, the forming effect of aluminum alloy welding can be significantly improved, and the welding quality is improved.
No matter what kind of welding method is used, the preparation work before welding of aluminum alloy is indispensable, which has a great influence on the welding quality of aluminum alloy. Wipe the surface of aluminum alloy parts with anhydrous alcohol or acetone before welding to remove impurities such as water or oil adsorbed on the surface. In order to prevent the workpiece from being oxidized in the air, the workpiece needs to be mechanically ground or chemically treated and dried to complete the welding as soon as possible. In order to speed up the fluidity of the molten pool during welding of aluminum alloys, a copper pad can be added to the back of the aluminum alloy workpiece to improve the weld formation. When welding, use Ar gas protection to isolate the air and reduce the generation of pores.
Specific Measures To Optimize Laser Welded Aluminum Alloys Quality
At the beginning of aluminum alloy laser welding, there is a high reflection phenomenon, which seriously affects the absorption of laser energy by the material. The shorter the wavelength, the better the absorption of light by the material. Therefore, fiber laser is better than CO2 laser for the absorption of aluminum alloy. The beam pattern of the fiber laser will also be better than that of the CO2 laser, and the energy density will be more concentrated. Once the material begins to absorb light energy, the reflectivity of the liquid metal to light drops significantly.
The use of double-spot laser welding can significantly improve the porosity, mainly because the two beams form a relatively large keyhole when welding with double beams, which improves the stability of the keyhole and is conducive to the escape of gas; Compared with serial double beams, when parallel double beam welding is used, the temperature gradient inside the molten pool is smaller, which reduces the solidification speed of liquid metal, prolongs the escape time of bubbles, and helps reduce the tendency of porosity; parallel double beam laser welding can also Improve the stability of wire feeding, which is beneficial to stable welding quality.
Using laser wire filler welding, compared with aluminum alloy laser self-fusion welding, it can get better forming. Laser wire filler welding can be compatible with the high energy density of laser welding and the high bridging ability of wire filler welding, and can ensure a good forming effect for welds with a certain gap. Moreover, through the selection of different filler materials, different chemical metallurgy can be performed on the base metal, which plays a role of supplementing and strengthening certain alloy elements.
Using laser hybrid welding, through the combination of laser and arc, the influence of plasma formed by laser welding can be effectively eliminated. By adjusting parameters such as filament spacing, air blowing, and welding torch angle, beautiful welds can be obtained, and good welds can be formed without grooves or only small grooves for thick plates.
The powerful laser head can stabilize the welding quality. With the in-depth development of laser processing, more and more powerful laser heads have been rapidly applied. At present, the laser heads developed by Scansonic and HighYAG can float up, down, left and right within a certain range without changing the spot size or affecting the matching of the optical fiber. Welding defects caused by deviation.
Using appropriate welding process parameters can ensure the welding quality. Figure 8 is a graph showing the relationship between the optimal parameter range of laser power and welding speed for 6061 aluminum alloy laser wire filling welding. It can be seen from this figure that the optimal matching parameter curve of laser power and welding speed increases linearly, and the slope remains basically unchanged. For each given laser power value, there is an optimized welding speed corresponding to it on the optimized parameter curve, and the welding speed can be changed within a certain range to obtain a weld with good forming quality. This area belongs to the welding stable area. . At a certain power value, when the welding speed is too high, the heat input becomes small, and the aluminum alloy sheet cannot be welded through. At this time, if the welding speed is too high, it will exceed the range of the stable zone and belong to the non-penetration zone; when the welding speed is too small, If the heat input is too large, the molten pool collapses seriously, and it belongs to the molten pool collapse area. To obtain stable weld formation, suitable welding process parameters need to be matched.