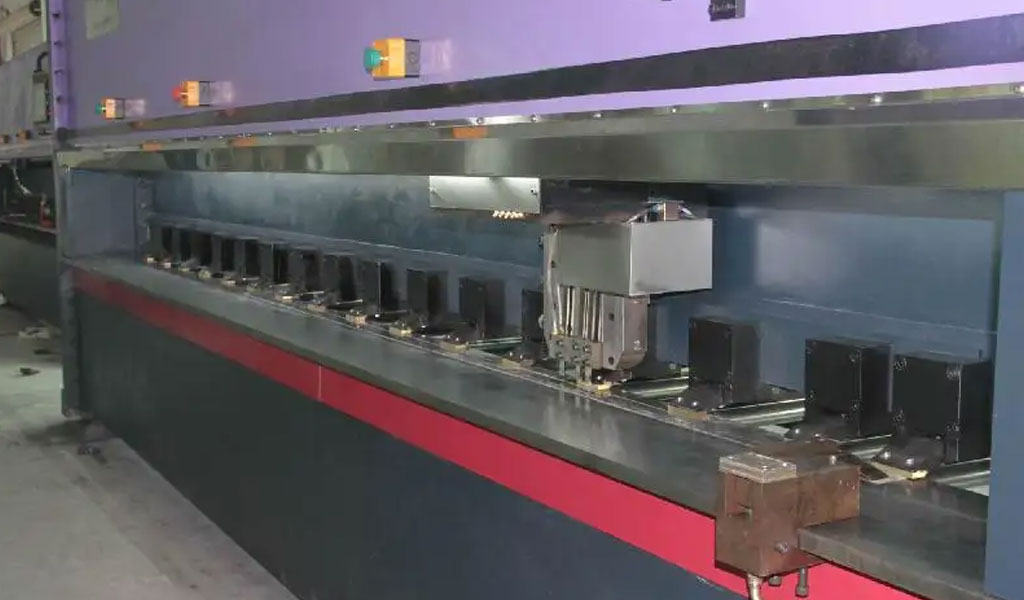
Sheet Metal Notching
Sheet metal fabrication is an indispensable part of mechanical processing, especially in aviation, home appliances, automobiles, elevators and other industries, sheet metal parts are widely used. As the only single forming process in sheet metal fabrication, the bending process is one of the most important processes in sheet metal fabrication. The quality of the bending process will directly affect the forming size and appearance of the product. Therefore, how to ensure the forming size and angle of the workpiece during the bending process is a key research content in the bending process.
With the development of the economy and the improvement of people’s living standards, the goals of people’s senses are also rising. In the metal decoration of some high-end places, the more complex the bent shape of the metal sheet jewelry, the more it can reflect the designer’s design level and trendy style, so as to attract the attention of our customers. At the same time, the workpiece should also meet the process requirements such as the arc radius of the bending edge as small as possible, no creases on the surface of the workpiece, and no indentation on the decorative surface. Traditional bending machines can no longer meet this special process requirement. Therefore, the process of sheet metal notching and bending on metal sheets came into being.
Traditional Bending Methods And Their Limitations
The traditional bending process is to use the two edges of the lower die opening and the edge of the upper die to bend the metal sheet under the pressure of the upper and lower dies of the bending machine, and the metal sheet undergoes elastic deformation to plastic deformation. The bending angle is determined by the depth of the upper die entering the lower die, and the bending radius is R2 and the thickness t (Fig. 1). In today’s society, people have higher and higher requirements for the shape of workpieces.
Some workpieces with complex shapes are shown in Figure 2, which cannot be bent using traditional free bending, bending machine bending and even three-point bending processes.The bending method cannot control the radius of the bending fillet, and it is difficult to achieve the process requirements of traceless bending. Therefore, New type bending process—the grooved bending process came into being.
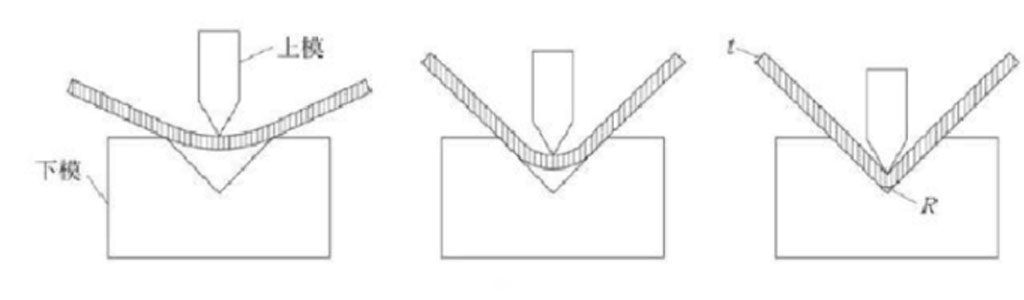
The Features Of Grooving And Bending Process
The grooving and bending process is a process in which a planer is used to scribe a V-shaped groove at the position where the metal sheet needs to be bent, and then it is bent on an ordinary bending machine according to the requirements. The characteristics of the grooving and bending process mainly include the following three aspects.
The Arc Radius Of The Workpiece Is Small, And The Workpiece Has No Creases
It can be seen from the bending process that the radius of the edge arc of the workpiece after bending is proportional to the thickness of the plate. The thicker the plate, the larger the arc radius formed by bending. After V-grooving the metal sheet, the remaining thickness of the sheet becomes half of the original, or even smaller, which can greatly reduce the radius of the edge arc after the workpiece is bent. In addition, because the remaining plate thickness at the bending position after planing is relatively thin, the deformation force during bending will be correspondingly reduced, and will not spread and affect the unbent area, so there is no crease on the surface of the workpiece after bending, and due to the bending The thickness of the plate is thinner, and the reduction of the required pressure during bending can well avoid the risk of indentation on the decorative surface. In this way, in the metal decoration of hotels, banks, commercial centers, airports and other high-end places, the process requirements of the workpiece edge arc radius are small, the surface has no creases, and the decorative surface has no indentation.
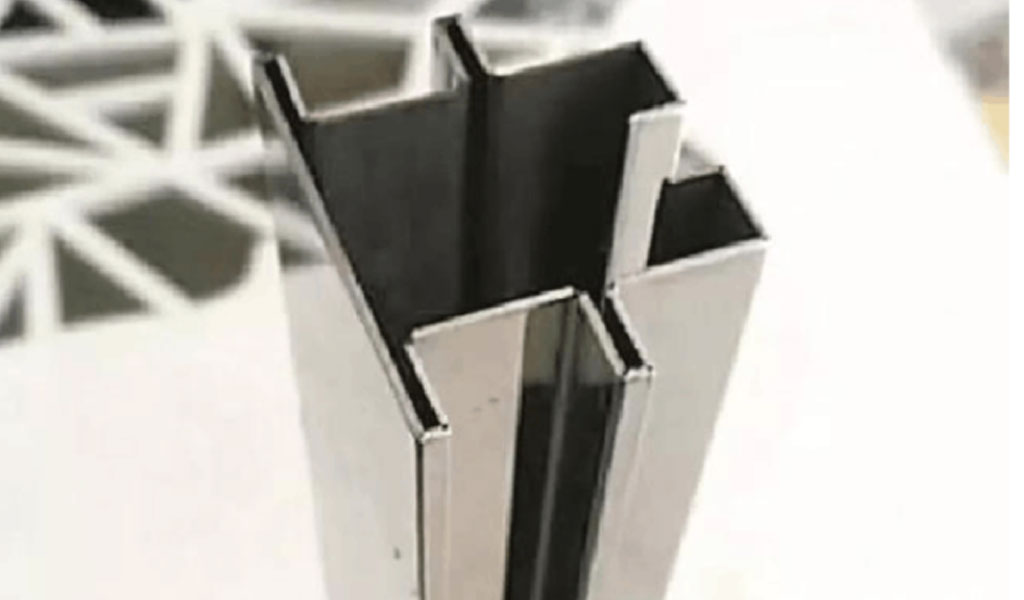
Reduced Equipment Tonnage Required
In the bending process, the required bending force of the metal sheet is proportional to its thickness. The greater the thickness of the sheet metal, the greater the required bending force and the corresponding increase in the required equipment tonnage. After the V-shaped groove is performed on the bending part of the metal plate before bending, the remaining thickness of the plate at this place is greatly reduced, so that the bending force required for bending the plate will be correspondingly reduced, so that the thick plate can be used in a small tonnage. Bending on the bending machine. This not only reduces the investment in equipment, but also saves energy and space.
Bending Of Complex-Shaped Workpieces And Control Of Springback
The part shown in the figure above cannot be bent and formed on a general bending machine, but it can be formed by hand-bending after opening a V-shaped groove at the bend. In addition, the control of springback force and springback angle can also be achieved by controlling the remaining thickness of the plate. If the remaining plate thickness after gouging is controlled to the left and right, the springback angle can be made very small, and the springback can be basically ignored.