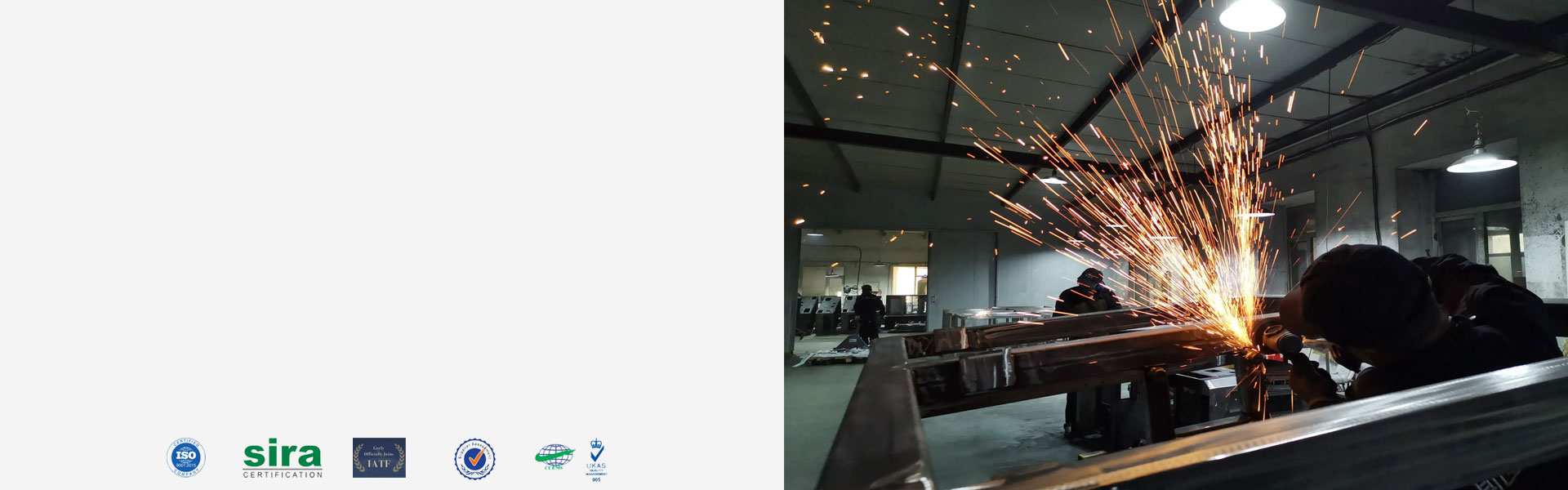
Sheet Metal Fabrication Service
From sheet metal fabricating parts to assembly and finishing, Pintejin is proud to deliver exceptional engineering services. Via a skilled team and advance machinery and processes,We’ve been dedicated to building better parts and have helped countless industries find value and performance along the way.Here at Pintejin, quality comes first to deliver exceptional value to clients through optimized processes and sheet metal manufacturing practices. Explore our website to learn more about our services, industries served or capabilities. You can also reach out to a customer service representative for more information on working with the advance sheet metal fabrication experts at Pintejin!
Quality Sheet Metal Prototyping、Medium To High Volumes Companies China
If you want to find a cost-effective and quality sheet metal prototyping solution for your manufacturing needs, Pintejin can be a good choice for you. Based on extensive experiences and professional expertise, our sheet metal fabrication services are available for both prototypes and low to high volume production runs. Working with Pintejin,Over 15 years of experience in layout and fabrication in China , ISO 9001:2015 certified precision sheet metal fabricator of custom metal parts, electromechanical enclosures and panels. Capabilities include CNC machining, laser cutting, turret punch pressing, CNC forming, resistance and fusion welding, grinding and polishing. Capable of fabricating parts up to 0.250 in. ga. material thickness, 60 in. sheet metal width and +/-0.010 in. tolerance. with thicknesses of 3/8 in. Finishing services include deburring, polishing, painting, plating, anodizing, silk screening, passivation and heat treating.
CAD/CAM prototype design services are also available with in-house rapid machining and tooling for prototyping in low to high volumes. Our custom sheet metal fabrication service provides durable and affordable sheet metal components that meet your specifications for automotive, medical, aerospace, electronics, food, construction, security, marine, and more industries. Fast to send your inquiry or submit your drawings to get a free quote in the shortest time.
Simplify your custom metal fabrication and machining requirements with reliable sheet metal fabricators
Couldn’t Find What You Looking For?
Generally, there are stocks of common sheet metal stock or raw materials in our warehouse. But if you have special demand, we also provide customization service. We also accept OEM/ODM. We could print your logo or brand name on sheet metal parts body and color boxes.
-
Sheet Metal Frame
-
Sheet Metal Enclosure
-
Sheet Metal Bracket
-
Sheet Metal Chassis
-
Sheet Metal Cabinet
-
Sheet Metal Box
-
Sheet Metal Case
-
Sheet Metal Cover
-
Sheet Metal Support
-
Sheet Metal Housing
-
Sheet Metal Caps
-
Sheet Metal Industry
What Is Sheet Metal
Sheet metal has not yet had a relatively complete definition, the current relatively perfect definition is a comprehensive cold working process for sheet metal. According to a definition in a foreign professional journal, it can be defined as: Sheet metal is a comprehensive cold working process for metal sheets (usually below 6mm), including shearing, punching/cutting/compounding, folding, riveting, splicing, Forming (such as car body), etc. Its remarkable feature is that the thickness of the same part is the same. . Sheet metal has the characteristics of light weight, high strength, electrical conductivity, low cost, and good mass production performance. It has been widely used in the fields of electronic appliances, communications, automobile industry, medical equipment, etc. Sheet metal is an essential part of the process.
As the application of sheet metal becomes more and more extensive, the design of sheet metal parts has become an important part of the product development process. Mechanical engineers must be proficient in the design skills of sheet metal parts, so that the designed sheet metal can meet the requirements of the product. Function and appearance requirements, but also make the stamping die easy to manufacture and low cost. In addition, the basic equipment of sheet metal includes shearing machine, CNC punching machine, laser, plasma, water jet cutting machine, bending machine, drilling machine and various auxiliary equipment.
Why Choose Custom Sheet Metal Fabrication Services at China?
- China Capabilities in fabrication, machining and finishing enable us to offer one-stop shopping
- Sheet metal fabrication service supplies durable parts for prototype and end-use
- A wide selection of material and surface metal finishing or treatment processes
- Accurate dimensions and specifications based on your demands and a variety of instruments
- Quick free quote within 24 hours and fast turnaround in average one week
- Competitive prices and the highest standard quality provide the most economic solution
- No minimum order quality. You can order a prototype of thousands of metal parts
Common Materials List Of Sheet Metal Fabrication
Sheet metal is a widely used form of raw material, usually 0.006 and 0.25 inches thick sheet used in sheet metal fabrication. Use the sheet metal gauge chart on our site to designate the thickness. Here are some popular sheet metal materials, stainless steel grade 304 is one of the most common options due to its good corrosion resistance, formability and weldability. If your applications are pumps, valves, chemical equipment, and marine product, grade 316 is recommended. For aluminum, the four most common aluminum grades available as sheet metal are 1100-H14, 3003-H14, 5052-H32, and 6061-T6. Brass is also widely used in the sheet metal fabrication process, it has more strength, corrosion resistance, and formability when compared to copper while retaining its conductivity.
- Aluminum: Al 5052, 6061
- Copper: C101, C110, brass (C260)
- Stainless Steel: SS 301, 304, 316/316L
- Steel: low carbon steel
The Common Types of Sheet Metal Fabrication Surface Treatment
If you require special treatment or post-processing for your parts, please check out the following sheet metal finishing options. If you can’t find what you want, welcome to send your inquiry to us, a wide range of surface finishes are available at Junying, a fast quote will be offered. Custom materials finish making your sheet metal fabricated parts achieve improved appearance and performance.
- Bead Blast
- Anodize
- Plating (Nickel Plating, Silver Plating, etc.)
- Powder Coating
- Chromate Conversion Coating
- Custom finishing services
The Recommended For Sheet Metal Fabrication Sizes and Tolerances
1.Dimensions of sheet metal fabrication parts
- Size: 47 in. x 119 in. OR 1,193.8mm x 3,022.6mm (max)
- Bend length: 10 ft. OR 3.048m (max)
- Flat part: 0.5 in. x 0.5 in. OR 12.7mm x 12.7mm(min)
- Formed part: 1.5 in. x 1.5 in. OR 38.1mm x 38.1mm (min)
2.Sheet metal fabrication tolerances of different features for reference.
- Bends: +/- 2 degree
- Offsets: +/- 0.024 in. (+/- 0.608mm)
- Hole Diameters: +/- 0.010 in. (+/- 0.254mm)
- Edge to Edge/Hole; Hole to Hole: +/- 0.010 in. (+/- 0.254mm)
- Hardware to Edge/Hole:+/- 0.020 in. (+/- 0.508mm)
- Hardware to Hardware: +/- 0.030 in. (+/- 0.762mm)
- Bend to Edge: +/- 0.020 in. (+/- 0.508mm)
- Bend to Hole/Hardware/Bend: +/- 0.030 in. (+/- 0.762mm)
- Features Separated By Two or More Bends: +/- 0.060 in. (+/- 1.524mm)
The Advantages of Sheet Metal Fabrication
- High malleability and durability to withstand pressures and last a long time
- Reduced tooling time to cut or bend the metal, save on the production cost
- Easy to handle custom simple or complex projects, whether prototypes or large scale
- Standard sheet metal thickness used in laser cutting or bending
- Inexpensive but high-quality end-use sheet metal products
- Improved construction quality, easier to maintain
- Sheet metals can be formed into virtually any desired shape
- Sheet metal parts are recyclable and not harmful to the environment
- High strength and high resistance to corrosion, sun, and moisture
How Does Sheet Metal Fabrication Work?
The common sheet metal fabrication process starts with material removal, during the stage, the raw material is cut to the desired shape by different cutting tools. A variety of subtractive machining processes can complete the operation. The second stage of sheet metal fabrication is material deformation. The piece that has been cut needs to be formed into a 3D shape with the forming process like bending. No materials are removed during the stage. The last step is to assembly several pieces into a complete product if there are multiple parts. Sometimes, surface treatment is needed to provide a better surface finish.The Detailed Manufacturing Process Is As Follows:
Workpiece Blanking In Sheet Metal
After the drawings are in hand, choose different blanking methods according to the different development drawings and batches, including laser, CNC punching, shearing, molds, etc., and then make corresponding deployments according to the drawings. The CNC punch is affected by the tool. For the processing of some special-shaped workpieces and irregular holes, there will be large burrs on the edges, and post-deburring processing is required, which will have a certain impact on the accuracy of the workpiece; no tools for laser processing. It is suitable for the processing of special-shaped workpieces, but it takes a long time to process small workpieces. A workbench is placed next to the CNC and laser, which is convenient for the sheet material to be placed on the machine for processing and reduces the workload of lifting the sheet. Some scraps that can be used are placed in designated places to provide material for the trial during bending.
After the workpiece is blanked, the corners, burrs and joints should be trimmed (grinding), and the tool joints should be trimmed with a flat file, and the workpieces with larger burrs should be trimmed with a grinder. Use the corresponding small file to trim to ensure the beautiful appearance. At the same time, the trimming of the shape also guarantees the positioning during bending, so that the workpiece rests on the bending machine in the same position during bending, and ensures the same size of the same batch of products.
Sheet Metal Lower Pass Process
After the blanking is completed, it enters the next process, and different workpieces enter the corresponding process according to the processing requirements. There are bending, riveting, flanging and tapping, spot welding, convex hull, and level difference. Sometimes the nut or stud should be pressed after one or two bends. Among them, the convex hull and level difference of the mold should be considered. Processing first, so as to avoid interference in other processes after processing first, and the required processing cannot be completed. When there are hooks on the upper cover or lower shell, if they cannot be welded after bending, they must be processed before bending.
When bending, it is necessary to first determine the tool and kerf used for bending according to the size and material thickness on the drawing. Avoiding the deformation caused by the collision between the product and the tool is the key to the selection of the upper die (in the same product, it may be used The upper die of different types), the selection of the lower die is determined according to the thickness of the sheet. The second is to determine the order of bending. The general rule of bending is first inside and then outside, small then large, special first and then ordinary. For the workpiece with the edge to be pressed, first bend the workpiece to 30°-40°, and then use the leveling die to press the workpiece to death.
When riveting, consider the height of the stud and select the same and different molds, and then adjust the pressure of the press to ensure that the stud and the surface of the workpiece are flush, so as to avoid the stud not being pressed firmly or pressing out beyond the workpiece surface, causing the workpiece scrapped.
Welding includes argon arc welding, spot welding, carbon dioxide shielded welding, manual arc welding, etc. For spot welding, the welding position of the workpiece should be considered first, and positioning tooling should be considered during mass production to ensure the accurate spot welding position.
In order to weld firmly, make bumps on the workpiece to be welded, so that the bumps can be evenly contacted with the flat plate before electric welding, so as to ensure the uniform heating of each point, and at the same time, the welding position can also be determined. Similarly, to weld, it is necessary to Adjust the pre-pressure time, pressure holding time, maintenance time and rest time to ensure that the workpiece can be spot welded firmly.
After spot welding, there will be welding scars on the surface of the workpiece, which should be treated with a flat grinder. Sub-arc welding is mainly used when two workpieces are large and need to be connected together, or when the corners of a workpiece are processed to achieve a smooth surface of the workpiece. ,smooth. The heat generated during argon arc welding can easily deform the workpiece. After welding, a grinder and a flat grinder should be used for processing, especially in the corners.
Surface Treatment
The workpiece should be surface treated after bending, riveting and other processes. The surface treatment methods of different plates are different. Generally, surface electroplating is carried out after cold plate processing. After electroplating, no spraying treatment is carried out. After chemical treatment, spray treatment should be carried out. The surface of electroplated boards is cleaned, degreased, and then sprayed. Stainless steel plate (mirror panel, fog panel, wire drawing panel) can be drawn before bending, without spraying, if necessary, it needs to be roughened; aluminum plate is generally oxidized, and different colors are selected according to spraying. Oxidized undertones,
Commonly used are black and natural color oxidation; the aluminum plate needs to be sprayed with chromate oxidation treatment and then sprayed. Surface pretreatment can clean the surface, significantly improve the adhesion of the coating film, and double the corrosion resistance of the coating film. The cleaning process first cleans the workpiece, first hangs the workpiece on the assembly line, first passes through the cleaning solution (alloy degreasing powder), then enters the clean water, secondly passes through the spray area, and then passes through the drying area, and finally removes the workpiece from the assembly line. Remove.
Spray Treatment
After the surface is pre-treated, it enters the spraying process. When the workpiece is required to be sprayed after assembly, the teeth or part of the conductive holes need to be protected.
Protection Fabrication
Tooth holes can be checked with soft glue sticks or screwed into screws. If conductive protection is required, high temperature tape should be used to attach them. Positioning tooling is used in large quantities for positioning and protection, so that it will not be sprayed inside the workpiece during spraying, and can be seen on the outer surface of the workpiece. The nut (flanging) hole that arrives is protected with screws, so as to avoid the need for back teeth at the nut (flanging) hole of the workpiece after spraying.
Some large batches of workpieces also use tooling protection;
When the workpiece is not assembled and sprayed, the areas that do not need to be sprayed are covered with high temperature resistant tape and paper to block some exposed nut holes and protected with screws or high temperature rubber. If the workpiece is sprayed on both sides, use the same method to protect the nut (stud) hole; small workpieces are sprayed together with lead wires or paper clips and other items; some workpieces have high surface requirements and should be scraped before spraying; The characters are protected with special high temperature resistant stickers.
When spraying, the workpiece is first hung on the assembly line, and the dust on the surface is blown off with an air pipe. Enter the spraying area for spraying, after spraying, follow the assembly line into the drying area, and finally remove the sprayed workpiece from the assembly line.
There are also two types of manual spraying and automatic spraying, so the tooling used is different.
Assembly Process
After spraying, enter the assembly process. Before assembly, tear off the protective sticker used in the original spraying to make sure that no paint or powder has been spilled into the threaded holes of the parts. During the whole process, wear gloves to avoid dust on your hands. On the workpiece, some workpieces have to be blown clean with an air gun.
Packaging Step
After the assembly is completed, it enters the packaging process. After the workpiece is inspected, it is placed in a special packaging bag for protection. Some workpieces without special packaging are packaged with bubble wrap. Before packaging, cut the bubble film into a size that can package the workpiece, so as not to cut one side of the package and affect the processing speed; for large batches, special cartons or bubble bags, rubber pads, trays, wooden boxes, etc. can be customized. After packing, put it in the carton, and then put the corresponding finished or semi-finished product label on the carton.