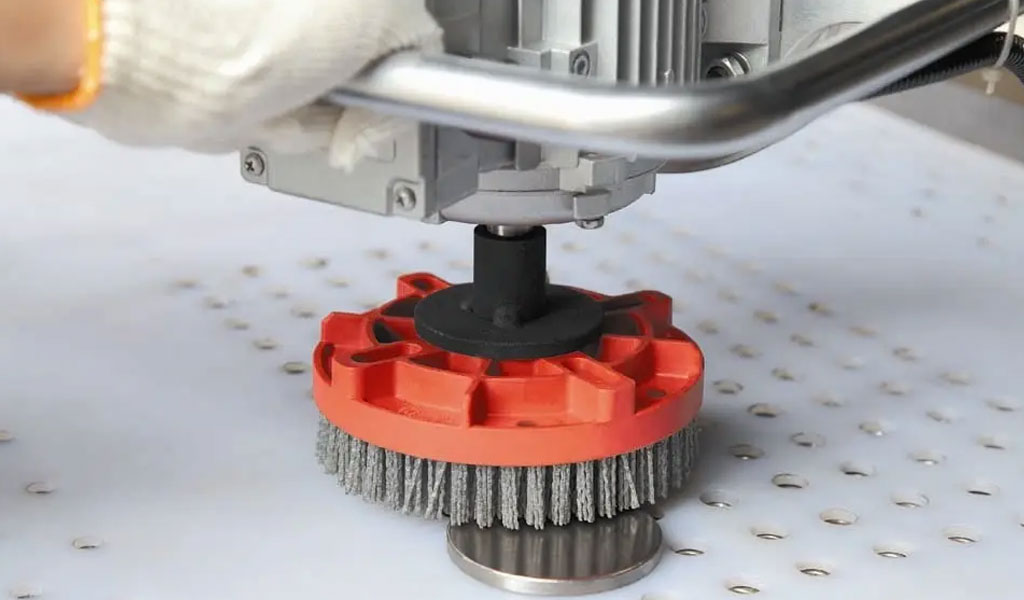
Sheet Metal Grinding Service
In the production process of sheet metal parts, the surface needs to be grinding.Which products need to be grinding and polished?
- All sprayed parts (only for those with stricter appearance requirements) such as: front panel, top cover, right panel
- There are large burrs after welding, such as: chassis (thick material (above 1.5mm)
Pintejin Sheet Metal company has never conceded the fight to produce high-volume sheet metal manufacturing at “globally competitive costs” for precision parts made out of Sheet Metal Grinding Service in the china. We are known for being an extremely advanced in-house device applying and developing the best technology to reliably supply high quality at very competitive costs. Customers have told us we are “indispensable”, their “best performing” supplier, and our customer service is simply “awesome”.
The Weld Grinding Of Sheet Metal Structural Parts
For welding methods such as gas shielded welding and argon arc welding, the labor intensity of grinding to remove the welding excess is often high. As shown in the figure below, the average height of the weld is 2mm, the width of the weld is 5~6mm, and the total length of the three welds is 1m. High-efficiency abrasive belt grinding equipment can smooth the weld in one minute, while traditional manual grinding takes more than ten minutes.
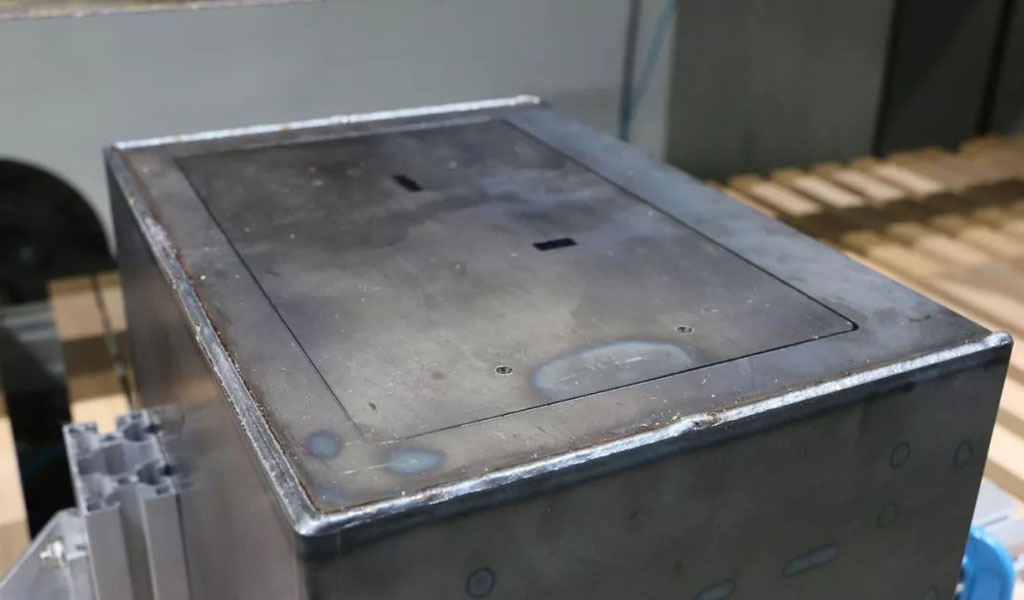
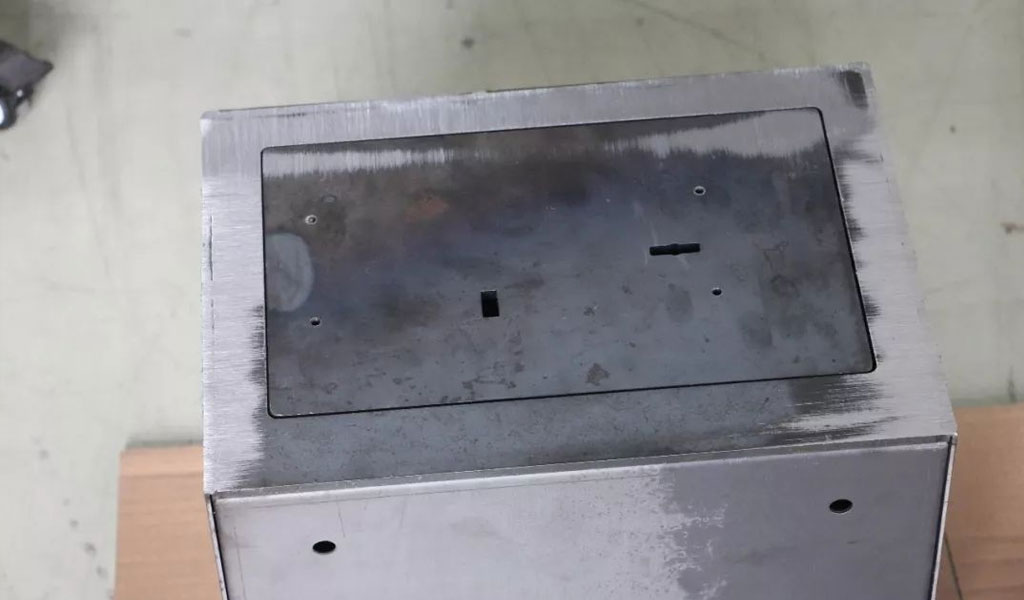
The Surface Grinding And Brushing Of Stainless Steel And Aluminum Sheet Metal Parts
For occasions with high appearance requirements, such as stainless steel sheet metal parts, not only welding points and seams should be polished, but also the consistency of the overall silk pattern of the workpiece, and even flawless and color-free, which truly endows metal products with noble artistic charm , the grinding efficiency and grinding effect of the long belt grinder have obvious advantages
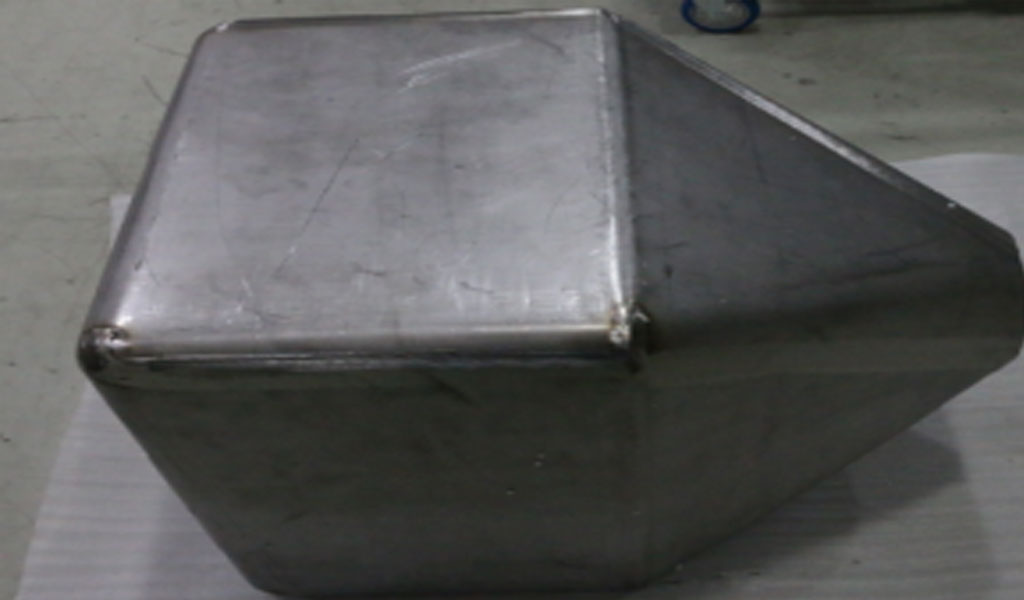
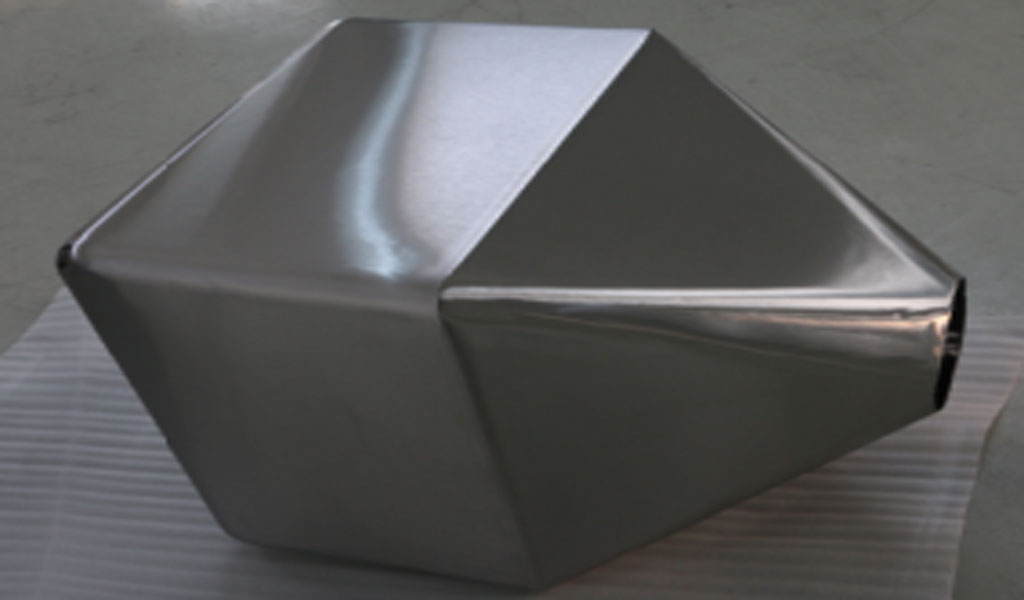
The Grinding And Brushing Of Extra Large Sheets
For extra-large plates, if the surface needs to be removed oxide scale, or the original plate is brushed and polished to a mirror effect, or the surface is brushed to improve adhesion, the manual grinding workload is huge, and because the pass-through wire drawing and polishing equipment uses a wider width The abrasive belt on the surface is used for grinding, but the width of the abrasive belt should not be too wide, otherwise it will be difficult to control and the grinding effect will be poor. The advantage of the long belt grinder in this case is unique. Figure 6 shows the field application of Pintejin extra-large belt grinder.
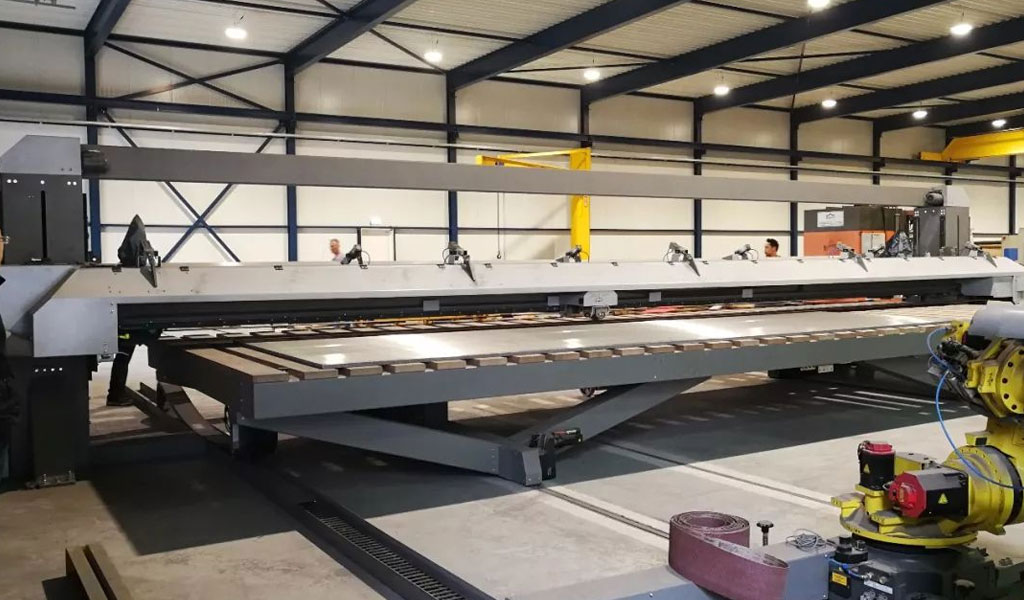
How To Formulate The Best Sheet Metal Grinding Process Route
At present, many sheet metal factories are looking for better sheet metal grinding solutions, but there are cases of failure due to blind investment. Therefore, before the introduction of new grinding processes and equipment, it is necessary to sort out the existing sheet metal production process, clarify the goals of grinding, clarify the correlation between the previous and previous processes and grinding, and solve all possible problems in advance. Analysis, so as to formulate the most suitable grinding process solution for yourself.
In view of the fact that most of the workpieces in sheet metal factories cannot be satisfied by one or two grinding tools or equipment, it is suggested that the following issues should be considered in-depth when planning the grinding production line:
- How to reduce the workload of manual grinding as much as possible, and use more equipment for automatic grinding?
- How to improve the grinding working environment as much as possible?
- What are the suitable grinding tools or abrasives?
- How to reduce the influence of the grinder itself on the grinding result?
- How to balance the grinding effect and grinding efficiency?
- How to control the leveling rate in the automatic grinding process?
- How to match the welding quality requirements with the grinding rhythm?
- How does the grinding station adapt to the material flow in the sheet metal workshop?
The advanced level of sheet metal factories in Europe is not mainly in the degree of automation of grinding equipment, but in the most reasonable process flow and the most reasonable use of grinding tools or equipment. The following points are summarized:
- Although there are many situations where automatic grinding methods can be used, manual grinding is still inevitable for sheet metal parts with different shapes, but the grinding environment of most European sheet metal factories is not like what we think” Dirty, messy, poor”, its standard centralized dust removal system ensures a comfortable operating environment, all kinds of hand-held grinding tools are complete, and the grinding workers are familiar with the application of each grinding tool and abrasive, and can be quickly replaced according to different scenarios. Corresponding abrasive tools and abrasives to achieve the best grinding efficiency and grinding effect! However, many domestic sheet metal factories still only rely on traditional angle grinders to achieve all grinding.
- The long abrasive belt grinder is widely used in sheet metal factories. The long abrasive belt grinding equipment is used in sheet metal grinding. It can achieve high efficiency and excellent results for relatively regular surfaces. It has become an improvement in sheet metal factories. An important weapon for sharpening efficiency. Although many domestic sheet metal factories have introduced belt sanders, most of them are idle. On the one hand, because most of the domestic traditional triangular belt sanders are based on the application of the wood industry, the grinding of metal surfaces is still immature, with little efficiency and effect. Advantages, and the control performance is relatively weak; on the other hand, many technicians in sheet metal factories lack experience in the application of abrasive belt grinding.
The Advantages Of Belt Grinding
Abrasive belt is a kind of belt-shaped tool that can be used for grinding and polishing, which is made by using adhesive to bond abrasives to flexible materials such as paper and cloth. It is a main form of coated abrasives. Its basic composition is: substrate, abrasive and binder, collectively known as the three elements of the belt. The abrasive belt grinding technology has gradually developed into an independent processing technology with a complete range and a relatively complete technical system. The advantages of abrasive belt grinding are summarized as follows:
- The abrasive grains on the abrasive belt have stronger cutting ability than the abrasive grains of the grinding wheel, which is more than 5 times that of the ordinary grinding wheel, so its grinding efficiency is very high.
- The size of the abrasive belt can be large, which is suitable for high-efficiency processing of large areas and a wide range of processing materials.
- Due to the less heat generated by friction and good heat dissipation conditions, the deformation and burn of the workpiece can be effectively reduced.
- The abrasive belt is in flexible contact with the workpiece, and the abrasive belt can be reversely attached to the curved surface to grind various complex forming surfaces, and has a good running-in and polishing effect.
- The auxiliary time is small. After the workpiece is positioned once, the abrasive belt can be replaced multiple times to complete the entire processing, without the need for balancing and dressing work like the replacement of the grinding wheel.
At present, the grinding efficiency of the advanced abrasive belt grinding equipment on the market can reach more than ten times that of manual grinding in some occasions.