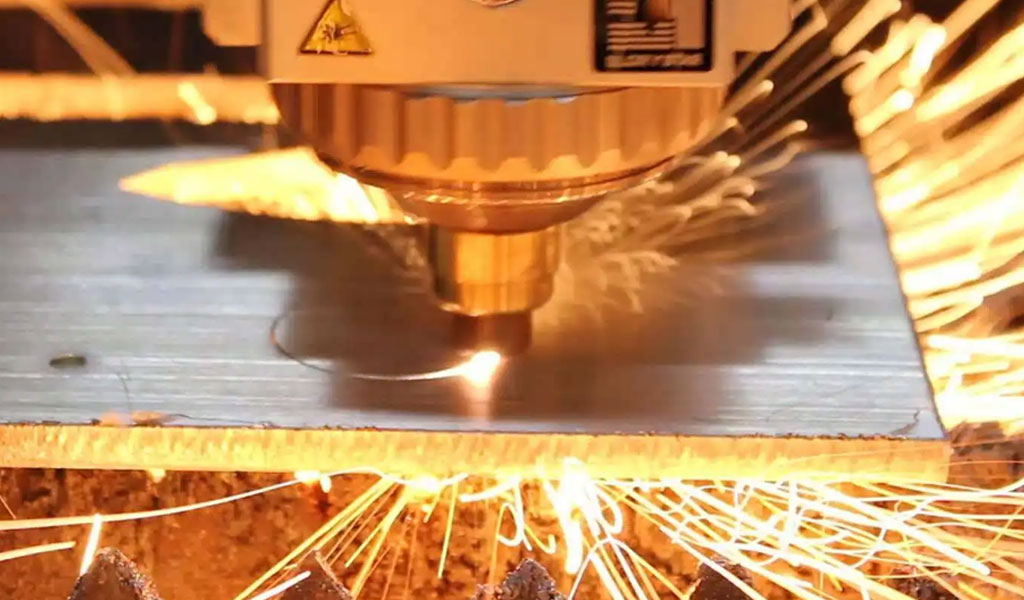
Industry requirements for lightweight design and cost-effective production techniques are increasingly challenging, including the trend towards more design-based and reduced batch sizes, resulting in a market requiring more accessible and flexible production processes, while longer distances Laser welding technology is one possible solution. The lightweighting of automotive structures is becoming more and more interesting, driven by the concept of metal composites, such as aluminum-steel structures, as well as locally adjusted strength distributions. The long-distance controlled laser process can be used to directly connect aluminum-steel T-joints and local laser-quenched trajectories, thereby significantly improving the crash performance of steel profiles.
Laser Local Strengthening For Lightweight Design
Parts that are locally stressed are often large in size because the wall thickness must be designed for the highest loads. In areas of low stress, the thickness of the steel plate can exceed the desired range, adding unnecessary weight to the component. In addition, a wide variety of expensive high-strength steels with good formability have been developed. But there’s always a compromise between the quality and cost of components and crash safety, and that’s something we need to address.
In order to precisely adjust the properties of components according to the local load situation, an innovative method of laser hardening based on flexible remote control technology was developed. Depending on the quenching potential of the treated steel, the high hardness of the remelted track or the flat overlay weld track can lead to tensile strengths in excess of 1500 MPa, roughly twice that of the untreated substrate. Of particular importance is the need to test the bending stresses of impact-resistant parts, such as front and rear shocks, B-pillars and various reinforcement profiles, so that the design can be optimized for weight and load.
With the help of numerical simulations, we can achieve an impact-optimized trajectory design for bending stresses, for example, a frontal impact or a side impact on a tree. With the help of laser remote technology, trajectory design can already be realized in actual parts. Compared to the reference, it is possible to halve the deflection of the locally laser fused tubular section, although only about 3% of the volume of the part is locally hardened.
Long-Distance Laser Welding Enables Multi-Material Designs
The production of composite parts with good mechanical properties requires new joining methods, especially in laser applications. A steel-aluminum composite slot (web-slot) connection with selective laser melting is one solution. In order to realize the direct joining process, especially the composite T-joint, it is necessary to combine the long-distance laser control process with a new integrated design method. The formation of intermetallic compounds can be avoided by selective melting processes. These include selective melting of low melting point materials through a highly controlled long-distance laser cutting process. Specifically, the joint design on the aluminum side needs to be adjusted. For this purpose, a laser-implemented slot structure design for T-joints was developed
By optimizing the long-distance laser process, joints of different shapes can be realized. Basically, the scan width, scan speed and laser power can be adjusted to ensure that only the aluminum side is melted (Fig. 4a). In addition, the optimization of the single-sided laser process also allows the shaping of double-sided aluminum assemblies (Fig. 4b). Metallographic analysis showed that small innocuous intermetallic phases formed in the boundary region between steel and aluminum. In the intensity-related intersection (“laser rivet head”), no iron content was detected.
For components like running boards, chassis rails and bumpers, the state-of-the-art is resistance spot welding, which is typically welded with a lap flange width of 20mm. In order to meet the conventional size of structural body parts, the steel-to-steel spot welding size of the crash structure is determined to be 80 × 80 × 900 mm, and the width of the lap flange is 20 mm. Thanks to these new laser technologies, we can eliminate overlapping flanges and reduce component weight by approximately 20%. For additional weight savings, the low stress-loaded steel cover was replaced by an aluminium sheet, resulting in a further 10% weight reduction
The results of the vehicle crash test showed that the reduction in bending stiffness caused by the elimination of welded flanges of composite parts compared to conventional spot-welded designs can be compensated by joints with higher structural stiffness. This is the result of replacing point connections (spot welds) with linear welds (slot connections). In addition, three-point crash tests have shown that deflection can be reduced by additional localized laser hardening of the composite structure