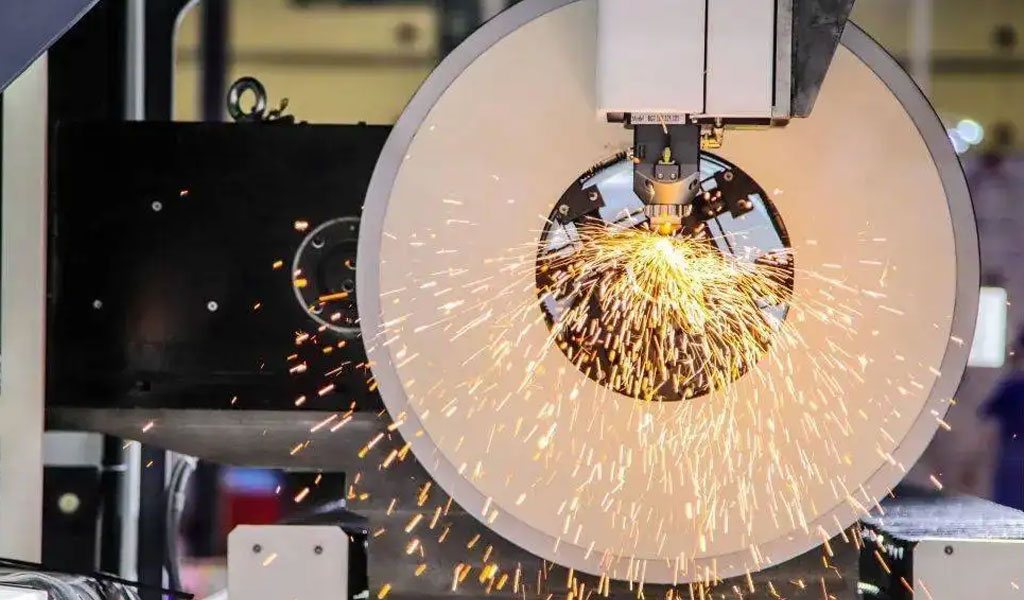
Glass has been a well-known material for thousands of years, used in a wide variety of transparent or colored products. Glass is now produced with significant ecological advantages, mainly thanks to its inexhaustible raw materials such as sand, soda ash, limestone and cullet, which are recycled at rates as high as 80% in industrial countries, and in some places ( Germany, for example) also has an efficient recycling system. Due to its excellent durability, mechanical strength and chemical resistance, glass is a fascinating material with a very wide range of applications (Figure 1), although polymers have also taken market share over the past 50 years .
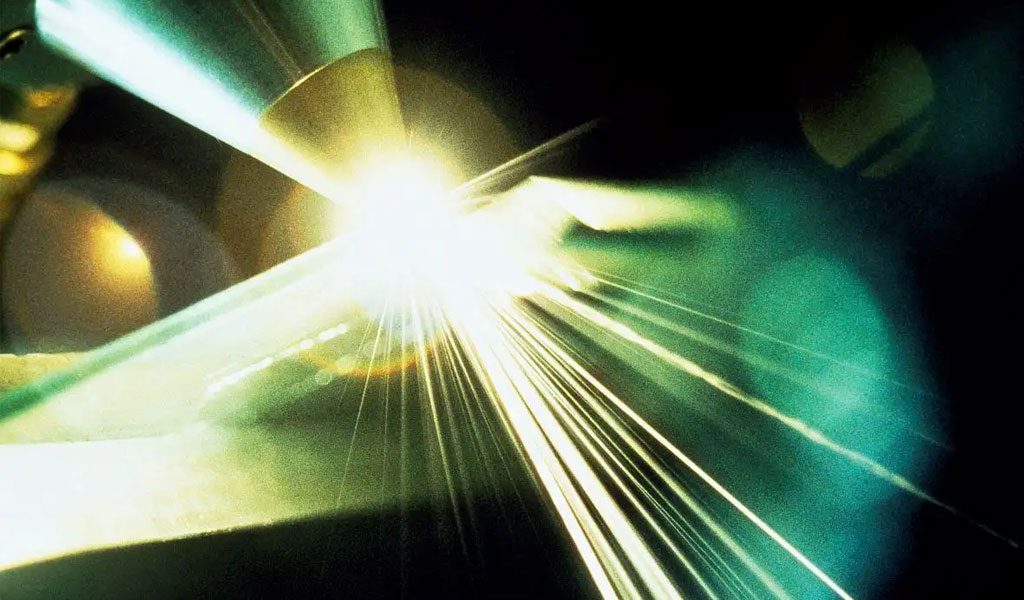
In order to maintain the original market and open up new ones, the research and development activities of glass manufacturing enterprises are continuous. One of them is the move towards very thin glass (20-200μm thickness) for lightweight and flexible products in the consumer and electronics sectors. For thicker glass, researchers are constantly trying to increase its mechanical strength or further improve the optical properties of glass products to meet the high demands of consumer electronics, medical devices, optics, and applications in construction, automotive, aerospace, solar, and more.
When the mechanical properties or other specific properties of glass do not meet the requirements of an application, other types of transparent brittle materials are considered. Given that glass is mostly amorphous (eg freeze-melt), alternative inorganic materials are either composed of pure crystals or transparent ceramics. All of these materials go through a lengthy production cycle to finally get the desired shape and properties. To this day, the vast majority of fabrication steps still rely on traditional machining techniques, including forming, scribing, drilling, grinding, or polishing.
Fabrication glass and crystals with lasers has been quite challenging, mainly because of their low absorption in the visible and near-infrared (NIR) spectrum and low thermal shock resistance. The most prominent and “obvious” application is laser marking on glass using the high absorption wavelength of CO2 lasers. Over the past few years, more sophisticated ways of marking surfaces or glass have emerged on the market – using femtosecond lasers. However, due to the higher price of these lasers, their applications are mainly concentrated in medical equipment or the packaging of high-end cosmetics and fragrances.
Numerous Options
The market continues to drive laser cutting manufacturers and system integrators to develop alternatives to traditional fabrication technologies due to the rising demand for reduced fabrication steps, material waste, and water in production. Some operations in the micromachining field specifically require more precise and less water-consuming techniques, such as cutting and punching. Various approaches have been used in the past with greater or lesser success, allowing lasers to be successfully used for cutting glass or other transparent and brittle materials. These processes are divided into:
• Scribing and breaking;
• Thermal separation of glass for specific stress distribution;
• Pure laser ablation;
• Bottom-up fabrication;
• Intra-glass scribing with high energy density optical breakdown;
• Traditional fusion cutting;
• Filamentation within the reaction volume (eg long, narrow variants).
Most of these methods have advantages, but at the same time there are many limitations. For example, it is interesting to mechanically separate brittle materials with thin cross-sections (thickness less than 0.5mm) using scribing and breaking after surface scribing with ultrafast lasers. But it is only suitable for straight line and low to medium speed (10 to 100mm/s, depending on thickness) scribing, and often leaves a non-straight edge after breaking, and the flexural strength of the scribed and broken edges is also There will be differences. However, we have successfully used laser scribing and breaking in sapphire scribing to produce light-emitting diodes (LEDs).
The use of NIR solid-state lasers to replace standard CO2 lasers in laser thermal separation is based on multiple laser beam absorption (MLBA), which is guided from the outside by laser-induced stress distribution inside the material. crack. The separated walls are of quasi-perfect, microcrack-free quality, resulting in a flexural test breaking strength close to the theoretical glass level. But it also has its drawbacks: it is difficult to guide the cracks to propagate along the contour in a predetermined curve and to close the contours without any deviation, since the propagation of the cracks depends to a large extent on the current tension distribution in the glass. Recent developments in this area include ultrafast lasers to achieve similar effects and edge quality, but contour cutting remains a problem. Therefore, thermal separation sometimes needs to be combined with pure laser ablation
Pure laser ablation can be used on a surface or even an entire cross-section to precisely remove material and ultimately create a kerf. Disadvantages include relatively low ablation rates (especially on thick sections), cutting speeds typically 1-10mm/s for materials up to 0.5mm thick, unavoidable taper angles of 10-12°, when A very pronounced heat-affected zone is created when the ablation depth exceeds 200 μm. Pure ablation methods can also be used to punch holes in glass and other transparent materials, preferably using a combination of ultrafast lasers and five-axis punch heads to achieve vertical hole walls. Of course, the machining speed on thicker (0.3-0.7mm) materials is quite low, taking nearly ten seconds per hole.
The pure ablation process starts at the upper end of the sample, whereas the “bottom-up” fabrication method starts with the laser from the bottom of the workpiece to disintegrate the transparent material, and the powdered material falls under the action of gravity, thereby leaving Ablation area. By moving the focus upwards in a continuous manner, various shapes of punching can be achieved. Frequency-doubling nanosecond or picosecond pulses at 515–532 nm are used because the process relies on the high transparency of the laser wavelength. On 3mm thick soda lime glass, a hole of 1mm diameter can be punched in 1 second, and the cutting speed of the free-form profile is in the range of 3mm/s. In addition to the relatively slow fabrication speed, there are other disadvantages, such as the inability to process strengthened glass with this method, and the obvious gaps at the edges (about 50-10 μm from the fabrication edge).
By using the high energy density of ultrafast pulses, coupled with deep focusing down to a few microns, optical breakdown can be achieved in virtually any transparent medium. With fast relative motion and active control of the focus position, scribing speeds of up to 1000mm/s can be performed within reaction volumes, such as 100-200μm thick sapphire LED wafers. The applicable material thickness is as low as 50 μm. It is necessary to separate the cut parts by a mechanical fracturing process. Disadvantages include high roughness in the scribed area, and it is difficult to control cracking that occurs from the central scribe to the edges, which can result in uneven cut walls.
Finally, there are two other fabrication methods that offer distinct advantages for mass production of glass and other transparent brittle materials.
The Fusion Cutting Of Sapphire And Ceramics
Sapphire is one of the hardest transparent materials in existence. Its mechanical and optical properties make it ideal for components such as watch glass, mobile device displays, digital camera protectors or LED carriers. Sapphire cutting with solid-state lasers, such as lamp-pumped solid-state lasers, has been going on for many years, and it has become an advanced industrial process. However, the speed and cut quality it can achieve are limited, and the running costs are relatively high. Recent advances in fiber lasers have brought the performance of the thermal sapphire cutting process to a whole new level. Cutting speed and quality are greatly improved, while running costs are much lower.
During thermal cutting, the laser beam is usually focused to a small spot on the workpiece. The temperature of the workpiece rises locally above the melting point. At room temperature, about 85 percent of the laser radiation will pass through the polished sapphire substrate, about 14 percent will be reflected, and less than 1 percent will be absorbed and begin to melt. Once sapphire is melted, its absorptivity rises sharply, and it can easily remain at the melting point temperature. Therefore, the beginning of this process (in-coupling phase) is the most critical part of thermal cutting of sapphire (Figure 3). Because sapphire has a higher thermal conductivity than other glassy phase materials, the laser intensity must be very high. Typically, hundreds of megawatts per square centimeter are required to induce melting. Due to its high thermal conductivity, heat is rapidly dissipated, and there is less risk of localized heat storage or thermal damage than other glass materials.
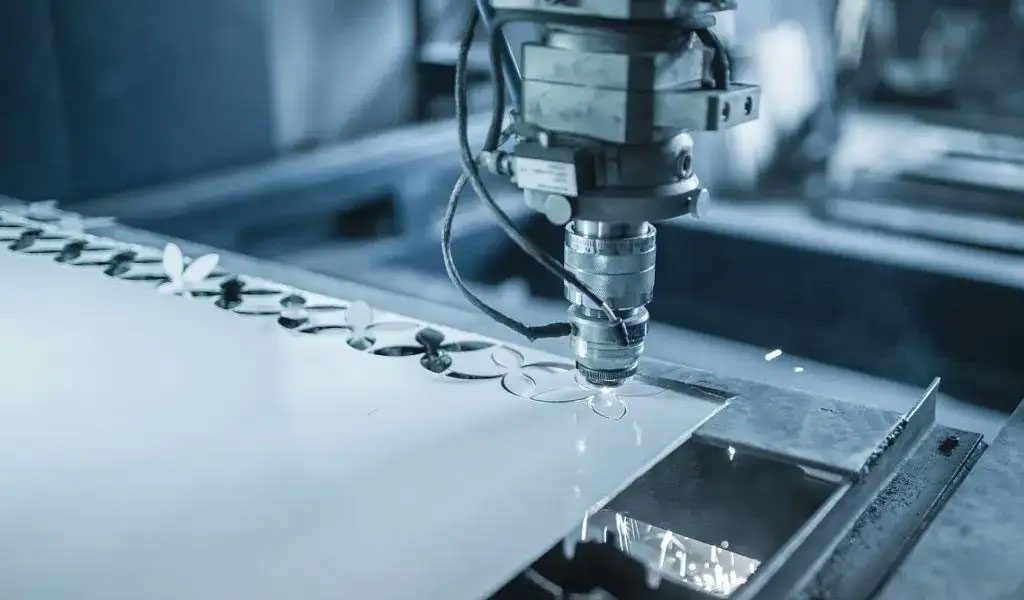
A jet of gas (nitrogen, compressed air, or in some cases helium) is injected into the laser beam to blow the melt away from the cut. The type of gas has an important influence (chemical reaction) on the edge quality of the cut.
Long-pulse fiber lasers, such as the Rofin-Lasag LFS 150, have become a very powerful alternative to lamp-pumped or diode-pumped solid-state lasers because of their high average and peak powers, as well as excellent beam quality. Since sapphire and other brittle materials are very sensitive, the laser parameters must be carefully selected and controlled. To avoid microcracks and gaps, the location of the focal point on the sapphire surface is very important. Proper focal position allows the incision to be free of any cracks and the size of the edge gap to be less than 10-20 μm.
Due to the nature of the thermal cutting process, only one cut of the part is required. Therefore, the cut taper can be kept to a minimum, usually below 2°, based on the thickness of the sapphire. In addition, excellent surface roughness values are obtained, Ra < 1.5μm. The maximum cutting speed depends mainly on the quality requirements and the complexity of the part. For sapphire thicknesses between 6 and 0.2mm, the cutting speed is between 3-25mm/s. The smallest kerf width can even be lower than 20 μm.
Using fiber lasers to melt cut sapphire and ceramics machining has become a state-of-the-art, highly automated manufacturing process for the production of mobile device components such as buttons, protective windows, etc. Compared to other cutting processes, if the correct laser parameters are selected, the cost-effectiveness will also be higher.
Laser Wire Cutting
There is a very different approach to the techniques described so far that can resonate enormously in the market, as it varies in fabrication speed, edge quality (roughness, flatness, surface damage), material thickness range and a wide range of materials Sexually excellent performance.
This new approach uses ultrafast lasers with specialized properties for very high aspect ratio variants in transparent media, what we call “laser filamentation”. In a schematic diagram, filamentation depends primarily on two competing processes. First, due to the nonlinear optical Kerr effect, the spatial distribution of the intensity of the laser pulse acts as a focusing lens, which leads to a further increase in the self-focusing of the beam and the energy density. At a certain peak intensity, a low-density plasma is created, which reduces the refractive index at the center of the optical path and causes the beam to be defocused again. By using a complex optical structure, the dynamic behavior between Kerr effect self-focusing and plasmonic defocusing leads to the formation of stable filaments that extend over several millimeters in length in optically transparent materials. Usually the filament diameter is in the range of 1-2mm.
In order to achieve substantially zero clearance cutting or perforating lines, these laser-generated filaments are brought into close proximity by relative motion of the workpiece and/or fabrication head at 100-1000mm/s, depending on the thickness of the material and cutting the desired geometry.
The Rofin SmartCleave FI wire-forming process can cut 0.05-10mm thick transparent brittle materials in any shape without taper (Figure 4). The surface of the product after cutting is clean and tidy without chipping. Usually the Ra value (surface roughness value) is less than 1mm, which makes the bending strength of the cut part very high. In the presence of a sufficient level of internal stress in the chemically or thermally strengthened glass, the filamentation regions will automatically separate. Non-strengthened glass (such as but not limited to soda lime glass, borosilicate glass, and aluminosilicate glass), sapphire or ceramic can be easily separated by lower mechanical or thermal forces. The latter can be achieved, for example, by a CO2 laser heating process.
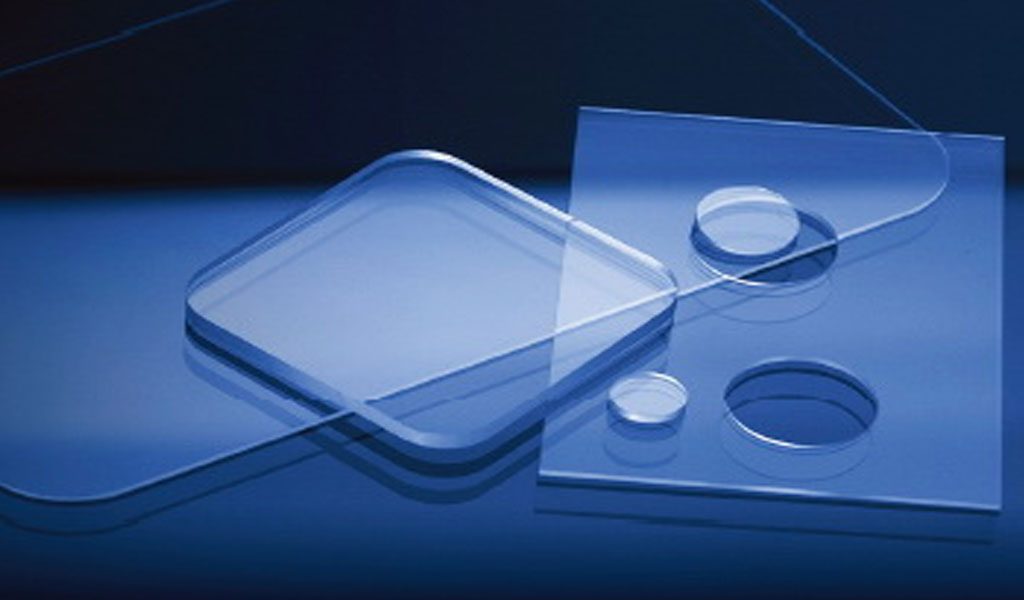
The laser filamentation process cleverly simplifies a lengthy and labor-intensive machining chain to just a few steps. Applications for SmartCleave FI technology include mobile phone displays made of reinforced or non-strengthened glass and sapphire, displays for TVs, computers and tablets, LED and OLED products, and other microelectronic applications, as well as integration Glass substrates for circuits, optical devices, watches, architectural and household glass, medical equipment, semiconductors or ceramics and other fields.
Ultrafast lasers suitable for filamentation have been developed that build MOPA chains that can achieve very high repetition rates. This patented and exclusively licensed burst mode provides pulse packets with nanosecond intervals and programmable power ramps. This offers more flexibility than the regenerative amplifier concept, which Rofin has made the first choice for designing its new family of industrial-grade ultrafast lasers (Figure 5). In addition, its chosen hybrid MOPA (Main Oscillator Power Amplifier) design combines the best of both lasers. It combines the robustness, high repetition rate and beam quality of a fiber laser with the power tunability of a round rod laser.
Summary
Fabrication glass and other transparent and brittle materials has always been a challenge in the field of lasers. Many different process approaches have been used in the past, but they have mostly been limited to a fairly narrow field of application. Two of these methods have promising potential for wider industrial applications – laser melting and cutting of sapphire or ceramics using long-pulsed fiber lasers, and laser filamentation using ultrafast lasers with specialized pulse characteristics .