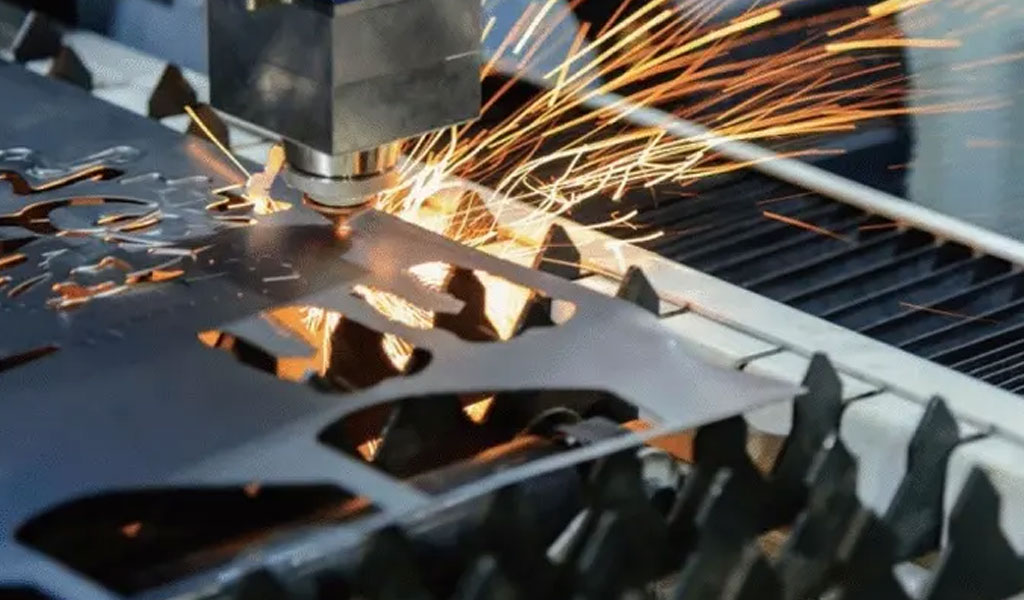
Laser shock forming [1-3] is a new moldless technology that uses the shock wave pressure generated by laser action to deform materials. It uses the force effect of high-amplitude shock wave pressure induced by high-energy laser instead of thermal effect to realize the plastic forming of metal sheet. When the laser shock metal sheet is deformed, the shock wave pressure reaches several gigapascals, which is much greater than the dynamic yield strength of the material, thereby causing plastic deformation of the material and improving the performance of the metal sheet.
Laser shock forming, a new high-energy manufacturing method, is very suitable for the frequent changes of product models in the aerospace industry, small batches, complex and diverse shapes of parts, high dimensional stability and high precision requirements, and the surface of the metal sheet after impact forming is formed. High-amplitude residual compressive stress can significantly improve its fatigue life. For sheet metal parts with fatigue resistance requirements, such as aircraft wing skins, the conventional strengthening process can be subtracted. The forming of forming materials also has great application potential, so it has received more and more extensive attention. At this stage, most of the analysis of the deformation of metal sheets under laser shock adopts the method of combining experimental research and theoretical analysis to carry out research on the manufacturing mechanism and process of laser shock forming. With the development of finite element, neural network and computer technology, finite element Simulations and neural networks are also beginning to be used in laser shock forming research. This paper summarizes the research status of laser shock forming technology from three aspects: laser shock forming process and optimization research, residual stress analysis of laser shock forming and limited simulation of laser shock forming, and points out the existing problems and development trends.
The Principle Of Laser Shock Forming
The basic principle of laser shock forming of sheet metal is shown in Figure 1 [4]. A high power density (109W/cm2 level), short pulse (10-9s level) strong laser acts on the energy covering the surface of the metal sheet The converter, the energy converter has the dual functions of an energy absorption layer and a confinement layer. Its main function is to convert the thermal energy generated by the laser beam into mechanical energy (shock wave pressure), improve the utilization rate of the laser energy, and protect the surface of the workpiece from laser damage. thermal damage. The thin layer on the contact side of the converter and the metal sheet is vaporized due to energy absorption, and the vaporized vapor rapidly absorbs the laser energy to form a plasma and explodes. The material undergoes plastic deformation under the action of this stress wave.
By selecting the laser pulse energy, impact trajectory and pulse number, under the control of the numerical control system, the local or large area forming of the sheet material can be realized. Laser shock profiling can be achieved by using a pre-made concave mold. It can be seen that laser shock forming is a composite process that integrates sheet metal forming and strengthening.
Laser Shock Forming Process And Optimization Research
During the laser shock forming process, the plasma and the blast wave supported by the laser energy form a high-pressure shock wave that is transmitted into the workpiece, so that the sheet metal is plastically deformed under the force effect of the shock wave. Since the laser beam is used as the loading tool, and the parameters such as the pulse energy, spot size and pulse interval width of the laser are precisely controllable, the relative motion trajectory of the laser impact head and the sheet can be controlled by the numerical control system, and the local forming of the sheet can be realized by a single impact. , the optimized laser parameters can also be used to impact the sheet material at multiple points and multiple times, so as to realize the flexible stamping and forming of the sheet material. Its technological process is shown in Figure 2.
In the research of laser shock forming process, Zhou Jianzhong et al. [5-7] used Nd: Glass pulsed laser to carry out laser shock deformation experiments on LD31 sheet with a thickness of 0.8mm. According to the theory of detonation wave and explosion gas dynamics
Pm is the peak pressure generated by the laser pulse; A is the absorption coefficient, usually 0.8~0.95; γ is the adiabatic index of the plasma, which is 1.67; Zt0, Zc0 are the acoustic impedances of the target and confinement layer materials; K0, Kc are the Energy absorption is a parameter related to the density of the confinement layer; ρ is the plasma density, which can be regarded as the synthesis of the confinement layer material, the energy absorption layer and the vaporization of the workpiece material; It0 is the laser power density. Yang Chaojun et al. [8] introduced the mechanism of laser shock deformation and the causes of shock waves, and established a sheet metal deformation model under laser shock.
W is the maximum deformation of the sheet; σs is the yield strength of the material; h is the thickness of the sheet; a is the radius of the action circle of the shock wave pressure; m is the unit mass of the sheet participating in the deformation. This lays the foundation for exploring the relationship between sheet metal deformation, laser energy and shock wave pressure. The minimum laser energy estimation and experimental study of the deformation of the metal sheet by laser shock were also carried out [9], and the minimum required laser energy formula was established:
d is the spot size; τ is the laser pulse width; KF is the coefficient, which is taken as 1.1; t0 is the thickness of the sheet; d2 is the aperture of the constrained concave die. In order to study the effect of different laser energy, different impact paths and impact times on the deformation of TA2 titanium alloy sheet, Gao Li et al. [10] used a high-power Nd: Glass laser shock wave device to conduct experiments, and obtained titanium alloys under different conditions. Deformation data of the sheet. The results show that with the increase of laser energy, the deformation of the sheet increases; the larger the geometric size and thickness of the sheet, the more difficult it is to deform the sheet; the unevenness of the impact area increases with the increase of the distance between the front and rear spots, Decrease as the spot spacing decreases. Wang Guanglong et al. [11] studied the response of sheet metal under pulsed laser irradiation, the deformation characteristics of sheet under laser shock, the effect of laser pulse energy on the deformation of sheet metal, and the distribution of shock wave pressure in the pulsed laser spot. , a single impact deformation test was carried out on the LD31 board using a high-power neodymium glass laser system. The results show that the deformation of the sheet metal under laser shock is viscoplastic; the laser pulse energy is the main factor affecting the deformation of the sheet metal, and the deformation size of the sheet metal increases nonlinearly with the increase of the pulse energy; the effect of the laser spot during laser shock The shock wave pressure in the region is not uniformly distributed, but decreases radially. Tong Yanqun et al. [12] designed and applied a simple and novel optoelectronic test system to test the dynamic and high-speed forming process of aluminum sheets subjected to strong and short laser shocks, and established a mathematical model of sheet deformation consistent with theoretical analysis and experimental data:
The first half of the plus sign represents the damping vibration of the plate; A0 represents the initial amplitude of the vibration, the amplitude decays exponentially, and the speed of decay depends on the coefficient t0; the frequency and initial phase are represented by the coefficients f0 and φ0; the second half of the plus sign Represents the dynamic elastic-plastic deformation process caused by metal ductility; A1 represents the deformation amplitude; f1 and φ1 represent the frequency and initial phase, respectively; y0 represents the final plastic deformation value.
Experimental studies have shown that there are many factors affecting the forming of laser shock sheets, mainly including laser energy, spot diameter, material properties, plate thickness, plate diameter and constraint boundary conditions. Because the manufacturing process is nonlinear and strongly coupled, the change of a certain parameter will cause the change of the sheet size. Therefore, it is of great significance to carry out the process optimization research of laser shock forming to promote its application. Ren Xudong et al. [13] studied the coating thickness in laser shock technology, the relationship between the interaction mechanism between laser and coating and the performance of the coating itself, and deduced the vaporization rate and optimal theoretical thickness of the coating. The influencing factors of the coating thickness are analyzed, which provides the basis for the correct application of the coating thickness calculation formula.
A is the absorption system of the laser on the surface of the material; I0 is the power density of the laser incident on the surface of the material; τ is the laser impact time; ρ is the density of the material; L is the heat of vaporization; c is the specific heat capacity; Tb is the vaporization temperature; T0 is The initial temperature. In order to solve the problems that the deformation of the metal sheet is difficult to control and the test parameters are difficult to optimize under different test parameters, Yin Sumin et al. [14] proposed a method based on neural network to control the deformation of the sheet, and established the laser manufacturing parameters and the maximum deformation of the sheet. The corresponding control software was written and verified by impact tests of 4 kinds of SUS304, LD31, TA2 and Al-Mg sheets under different conditions. The results show that the method can effectively optimize the impact test parameters and control the deformation of the sheet metal. Deng Zhonglin et al. [15] summarized the influencing factors of the maximum deformation of laser shock sheet forming, and based on the simulated annealing genetic algorithm, the analysis problem of the influencing factors of the maximum deformation of the sheet was expressed as a kind of combinatorial optimization problem, and the influence of the maximum deformation of the sheet was established. Based on the diagnostic knowledge base of factors, the diagnostic control parameters of the influencing factors of the maximum deformation are set, and the adaptive stretching method of simulated annealing is used to discuss the optimization method to effectively improve the diagnosis accuracy of the influencing factors of the maximum deformation of the sheet. The results show that the convergence speed of the simulated annealing genetic algorithm is 13.2% higher on average than the simple genetic algorithm, and the recognition accuracy is 7.44% higher on average. The lower temperature regulation coefficient α must be as close to 0.985 as possible to get an ideal solution. The method of predicting the maximum deformation of laser shock sheet based on the objective function generated by various influencing factors can effectively improve the manufacturing efficiency in actual production. Jiang Yinfang et al. [16] conducted a half-mold laser shock dynamic analysis, and proposed a method of forming precision control by optimizing laser shock energy, a mold correction and compensation method based on reverse analysis, and a half-mold laser shock forming accuracy characterization method. The results show that the laser energy for precise control of half-die forming is 15J, and the forming error can be reduced by more than 50% by means of die correction and compensation, which lays a foundation for the precise control technology of laser shock forming and its popularization and application.
Research On Residual Stress In Laser Shock Forming
One of the important features of laser shock forming is that it can form residual compressive stress on the surface of the workpiece, which can strengthen the aviation structural parts with fatigue resistance requirements. Therefore, residual stress is an important aspect of laser shock forming research. Yang Jianyang et al. [17] tested the residual stress on the forming surface of the sample by the roll fixation method, and discussed the influence of the inner diameter of the workpiece support seat and the top arc radius of the 90° apex angle punch on the forming of the titanium alloy plate. The research shows that when the bottom of the plate is unconstrained and supported, the surface residual stress of the concave and convex surface of the plate is all compressive stress; when punch impact forming is used, the change trend of the surface residual stress is not clear, sometimes it is compressive stress, sometimes it is tensile stress. Zhang Yongkang et al. [18] studied the residual stress distribution characteristics of 3A21 anti-rust aluminum plate formed by laser shock forming. The residual stress in three directions was measured by X-ray stress tester, the calculation formula of principal stress was established, and its formation mechanism and distribution characteristics were analyzed. The test results show that: under the action of pulse energy of 42J, pulse width of 23ns, and pulse power of 1.2×109W, the residual stress generated on the front and back sides of the sheet is less than -100MPa, and both are compressive stress, except that the principal stress direction of the vertex of the deformation area is 0° In addition, the principal stress direction of other points is about -30°, and the stress in the diagonal direction of the square sheet is greater than the stress in the length direction of the center side. Ren Xudong et al. [19] studied the effects of different pulse power densities and coatings on the residual stress of titanium alloys. A 1mm thick residual stress hardening layer can be formed on the surface of the impact specimen, and the maximum residual compressive stress on the surface can reach -301MPa. Yuan Dingguo et al. [20] also used the X-ray diffraction method to study the surface residual stress distribution of the metal sheet after laser shock forming. The results show that the concave surface of the sheet after forming has a large residual compressive stress, while the convex edge has a small residual tensile stress. The residual stress increases with the increase of laser energy, but there is a maximum value. There is also a threshold for the aperture of the die. When it is smaller than the threshold, the residual stress increases with the increase of the aperture of the die. When it is greater than the threshold, the residual stress decreases with the increase of the aperture of the die.
Research On Finite Element Simulation Of Laser Shock Forming
The laser shock forming process is a complex process involving many disciplines such as the interaction between laser and material, the propagation of shock wave and its loading mechanism on the material, the theory of dynamic plastic forming, and the stamping forming process. Restricted by hardware conditions such as lasers, there are not many research institutions that can carry out laser shock forming tests in China at present, and the test costs are expensive. If many influencing factors are tested and researched, not only the cost is high and the workload is heavy, but also the mutual influence relationship between each factor is difficult to be reflected in the test. These reasons greatly limit the research of laser shock forming technology. With the rapid development of computer and finite element technology, finite element numerical simulation has become an important research method. The finite element simulation research of laser shock forming can be used for the rational optimization of various parameters in the manufacturing process and the deformation process of sheet metal. The effective control, analysis and realization of laser shock forming of large-area metal sheets will provide a basis for the application of laser shock forming technology to production practice.
Zhou Jianzhong et al. [21] used ABAQUS software to numerically simulate the deformation process of sheet metal under laser shock, and explored the relationship between the main parameters of laser shock and sheet metal deformation. The results show that there is a direct relationship between the laser pulse energy and the deformation of the sheet under a single laser impact loading. With the increase of the laser energy, the deformation of the sheet presents a nonlinear increasing trend. The numerical model can effectively simulate the deformation process of laser impacted sheet metal, and provide a basis for the realization of flexible laser stamping forming of large-area metal sheet. Ji Weimin et al. [22] used ANSYS/LSDYNA software to conduct a finite element simulation of the influence of parameters such as laser energy and constrained aperture on the deformation of SUS304 stainless steel sheet. The results show that: with the increase of laser energy, the deformation of the sheet increases; the larger the initial confinement aperture of the sheet, the easier the sheet is deformed; the larger the geometric size and thickness of the sheet, the harder the sheet is to deform. Du Jianjun et al. [23] also used ABAQUS software to numerically simulate the deformation process of sheet metal under laser shock, compared the influence of different laser parameters on the deformation of sheet metal, and discussed the laser single point impact forming on the basis of laser shock forming. Multi-point impact forming. The deformation amount obtained by the simulation guides the production practice. Zhang Yongkang et al. [24] carried out finite element simulation of laser shock forming with ABAQUS software. The results show that: with the increase of laser energy, the deformation of the sheet increases; the larger the geometric size and thickness of the sheet, the more difficult it is to deform the sheet; the amount of deformation of the sheet varies with the impact sequence, and the deformation of the sheet varies along the sheet. the length direction and the symmetrical impact is the largest. The relevant parameters of laser shock can be optimized through numerical simulation, and the deformation of sheet metal can be predicted.
Gao Li [25] used ABAQUS software to carry out a finite element analysis of the effect of different spot spacing on the laser shock deformation of SUS304 stainless steel plate. The results show that as the spot spacing decreases, the impacted area becomes smoother. Ding Hua et al. [26] used aluminum alloy plate workpieces with different thicknesses to conduct finite element analysis of laser shock forming, and studied the transient and static deformation of the plate under specific conditions. The results show that there are two different mechanisms for laser shock forming depending on the thickness of the sheet. When the thickness of the sheet is less than 0.6mm, it is the deformation form of the die, and when the thickness of the sheet is greater than 0.9mm, it is the deformation form of the punch.
Existing Problems And Development Trends
- In terms of laser shock forming process research, at present, more research is on the deformation behavior of single-point single-shot laser shock, while in practical applications, more and more laser shocks are performed at multiple points. The research on the multiple laser shock forming process and its optimization has a higher reference value for the application of the laser shock forming technology. In addition, there are many process parameters that affect the quality of laser shock forming, and the test equipment is small and expensive. Therefore, it is very practical and feasible to use methods such as orthogonal tests to determine the main control factors affecting the quality of laser shock forming and to obtain optimized process parameters. research ideas.
- The research on residual stress of laser shock forming The current research mainly focuses on the research on the distribution characteristics of residual stress, and involves few influencing factors. Therefore, the residual stress distribution characteristics that comprehensively consider various factors and the residual stress distribution based on residual stress distribution characteristics should be carried out. Process parameter optimization research.
- In the finite element simulation of laser shock forming, the current idea is to simplify the laser shock process to the analysis of the deformation process of the sheet under the action of time-varying shock pressure. The simulation of the laser forming process is not accurate enough, so the laser Finite element simulation analysis of plasma explosion process to obtain more accurate shock wave pressure. In addition, laser shock forming is a high strain rate deformation process. The current material model acquisition method cannot achieve such a high deformation rate, and the adiabatic temperature rise in the deformation process is not involved. The research of thermal-mechanical coupling finite element simulation of shock forming process will become an important research direction in finite element simulation of laser shock forming.
Concluding Remarks
Laser shock forming is a fast, efficient and accurate forming new technology that uses the force effect of laser-induced high-amplitude shock waves to produce plastic deformation of sheets. It has the characteristics of good performance and no pollution. It is a new moldless and flexible forming process. It can give full play to the advantages of high laser energy. It is a new application of laser in the field of sheet metal forming, with broad application prospects and huge development potential. It is of great significance to carry out research on laser shock forming technology for promoting the development of forming and manufacturing technology for key components in the aerospace field in my country.
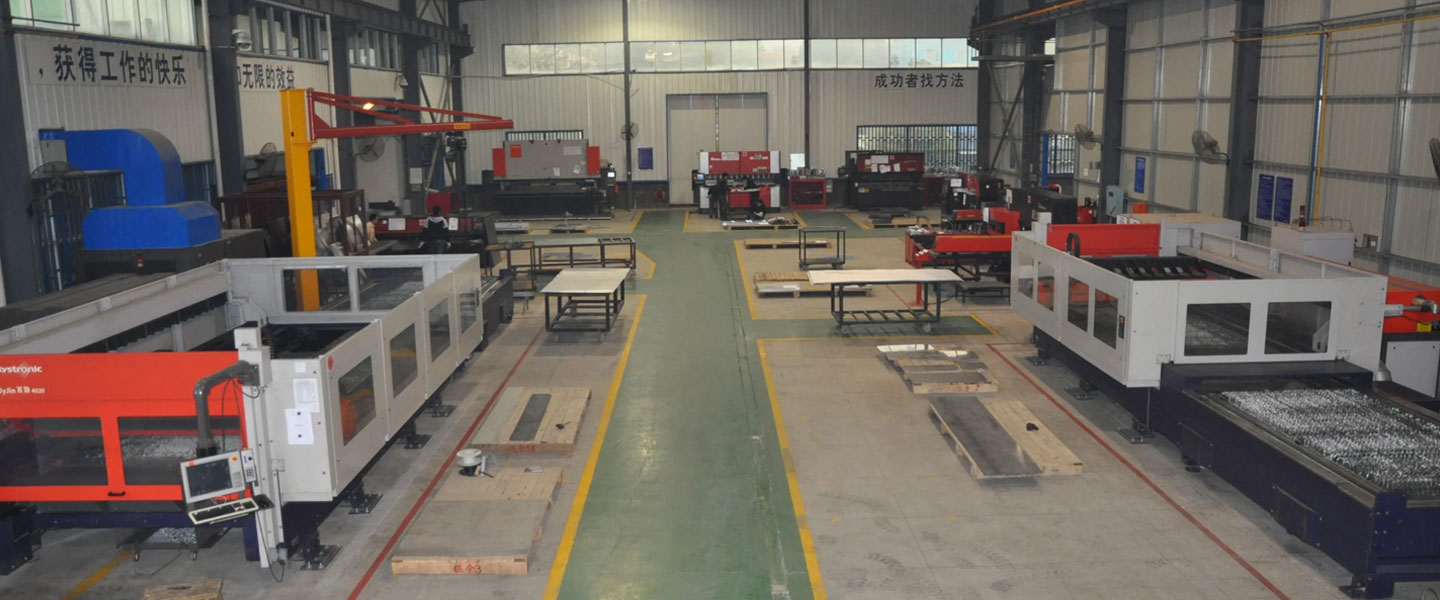
Pintejin Sheet Metal shop offers a cost-effective solution for a wide range of industries with our custom metal stamping and custom sheet metal fabrication capabilities. Our stampnig operations include a variety of sheet-metal forming manufacturing processes, such as punching, blanking, embossing, bending, flanging, and coining. Our professional, experienced and well-trained engineers can execute the complex metal stamping operations with precision and accuracy.
No matter what your metal fabrication needs are, Pintejin can offer the right solution: from single sheet metal part or sub-assembly of stamped metal parts to turnkey solutions for mechanical and electrical assemblies. We have the technology, equipment and the experience to fabricate customised metal products from aluminium sheet metal fabrication, steel, zinc plated steel, stainless steel sheet metal fabrication, brass and copper. Designs that require CNC machining of surfaces or components can be accommodated. We can supply polished, galvanized, zinc coated or powder coated finishes for any sheet metal work or stamped metal components. Coupled with our accurate and reliable metal fabricating equipment, we guarantee precision and repeatability in custom sheet metal work. You’ll be taking advantage of the best sheet metal fabrication china can produce.