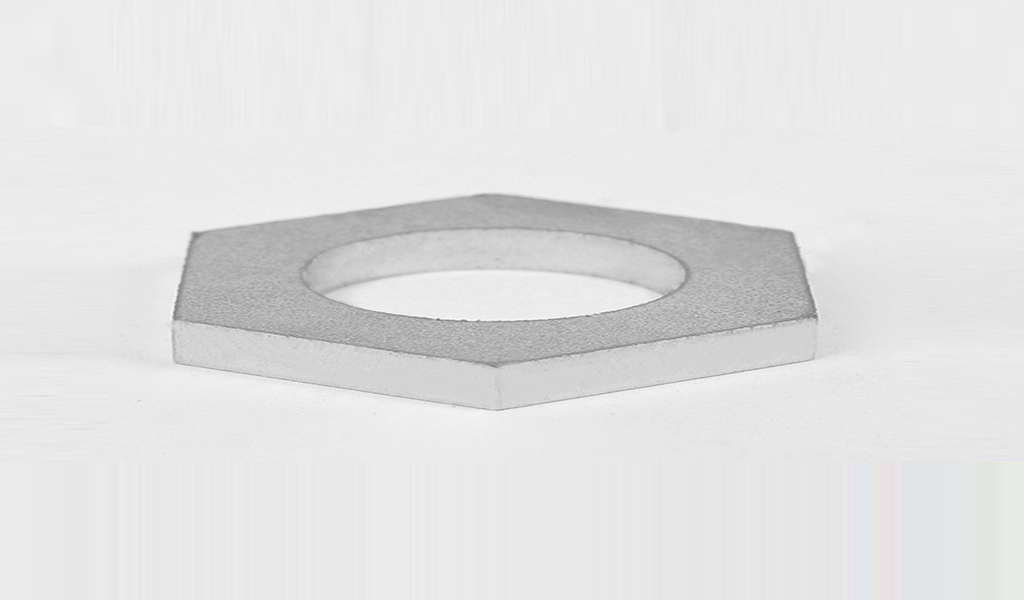
In recent years, with the improvement of people’s living standards, the demand for automobiles has also increased, and the competition among automobile factories has become increasingly fierce. New models with cost competitiveness are constantly being invested to seize the market. Natural resources such as iron ore and coke are increasingly scarce. Improving the utilization rate of materials can not only reduce the manufacturing cost of automobiles and improve the competitiveness of automobile brands, but also conform to the environmental protection concept of energy saving and consumption reduction.
For some special-shaped stamping parts, the arrangement of blank sheets in the uncoiling blanking die can be optimized to reduce waste, unwind as many blank sheets as possible, and improve material utilization. In order to improve the market competitiveness and enrich the sales product front, every year, the automobile factory will invest in new models, and the new model parts will have new specifications and materials. When the mass production of the model ends, the corresponding special steel will occupy the inventory due to the slow consumption. Therefore, each new specification of steel will increase the inventory and management costs. The car factory must ensure the versatility of the steel as much as possible. The number of varieties of steel.
When multiple parts are produced on a set of molds at the same time, one or more small parts are produced by using the waste at the holes of the large parts to achieve the effect of improving the material utilization rate.
When designing the mold, the left and right symmetrical parts are designed to be stamped together. Through process optimization, two parts are stamped out of two sheets instead of one sheet.
By adjusting the positioning of the blank sheet in the drawing die, the process supplement of the excess material other than the drawing bead is reduced, thereby reducing the size of the blank sheet required for the part and improving the utilization rate of the material.
When producing steel coils and steel plates, steel mills have a certain control range for the thickness tolerance of the products. Table 1 is the control standard for coil size. If the thickness of the steel coil is delivered to the automobile factory according to the positive tolerance, the thickness of the uncoiled blank sheet will be thicker within the qualified range, which will cause the actual weight of the blank sheet and stamped parts to be higher than the process rated weight. , will cause the actual number of sheets uncoiled from the steel coil to be less than the theoretical number, resulting in a reduction in the yield.
When some parts are uncoiled and blanked, there will be wastes with a large area that are not used. These wastes are used for the production of other small parts on the car body. Automobile stamping parts can avoid the separate procurement of materials for small parts, saving costs, At the same time, the material utilization rate of the vehicle is also improved.
The stamping process provides material suppliers with packaged coils. After unpacking, the coils are cut into various shapes required for stamping by uncoiling equipment, and then various parts are punched out. When uncoiling, it is necessary to cut the outer and inner circles of the coil, and at the same time, the head and tail of the coil need to pass through the uncoiling equipment. The head and tail of each coil are about 15 meters away from the normal production loss. Therefore, the larger the unwinding batch, the heavier the average weight of the coil, the higher the unwinding efficiency, and the less the average loss of the coil.
There are many ways to improve the material utilization rate, and more methods need to be verified by practice. For example, when blanking the stamping cover, change the existing linear knife or arc knife to a wave knife, and shorten the slab by changing the shape of the slab. This method needs to calculate the investment and maintenance cost of the mold and the income relationship after improving the material utilization rate. In a word, improving the material utilization rate is to reduce the complete cost of the whole vehicle. When making the material utilization rate improvement plan, it is necessary to combine the model output and consider the relationship between the investment cost and the income.
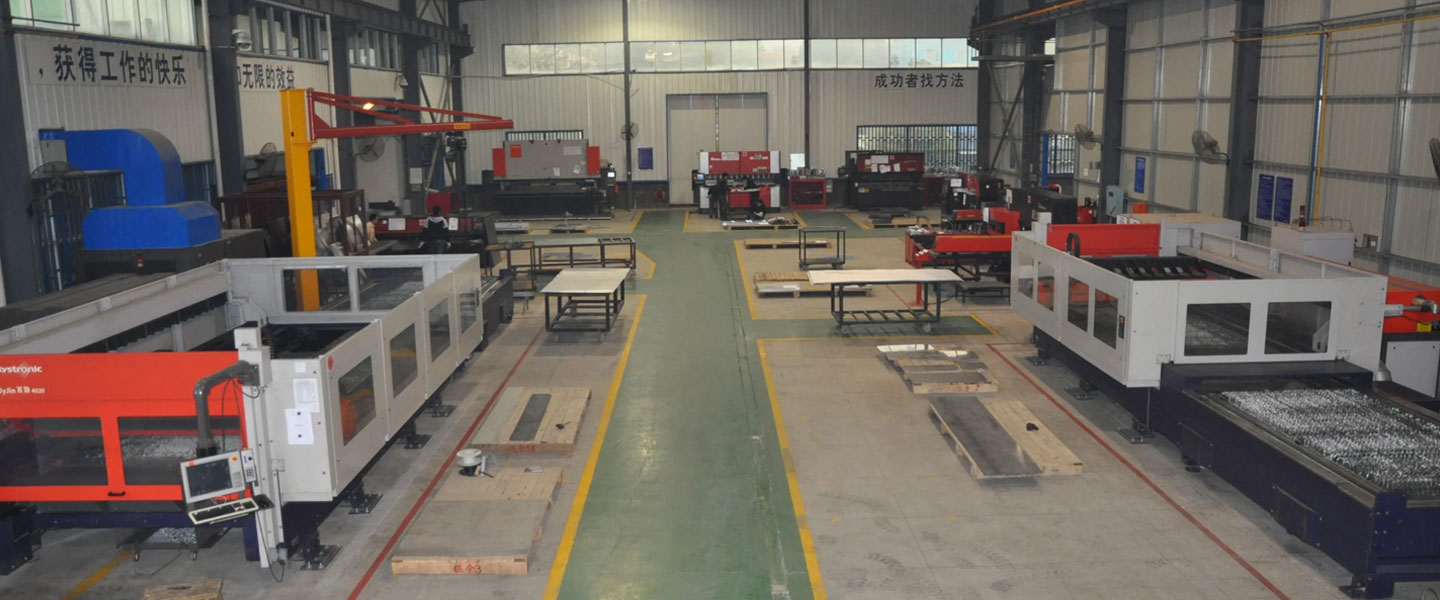
Pintejin Sheet Metal shop offers a cost-effective solution for a wide range of industries with our custom metal stamping and custom sheet metal fabrication capabilities. Our stampnig operations include a variety of sheet-metal forming manufacturing processes, such as punching, blanking, embossing, bending, flanging, and coining. Our professional, experienced and well-trained engineers can execute the complex metal stamping operations with precision and accuracy.
No matter what your metal fabrication needs are, Pintejin can offer the right solution: from single sheet metal part or sub-assembly of stamped metal parts to turnkey solutions for mechanical and electrical assemblies. We have the technology, equipment and the experience to fabricate customised metal products from aluminium sheet metal fabrication, steel, zinc plated steel, stainless steel sheet metal fabrication, brass and copper. Designs that require CNC machining of surfaces or components can be accommodated. We can supply polished, galvanized, zinc coated or powder coated finishes for any sheet metal work or stamped metal components. Coupled with our accurate and reliable metal fabricating equipment, we guarantee precision and repeatability in custom sheet metal work. You’ll be taking advantage of the best sheet metal fabrication china can produce.