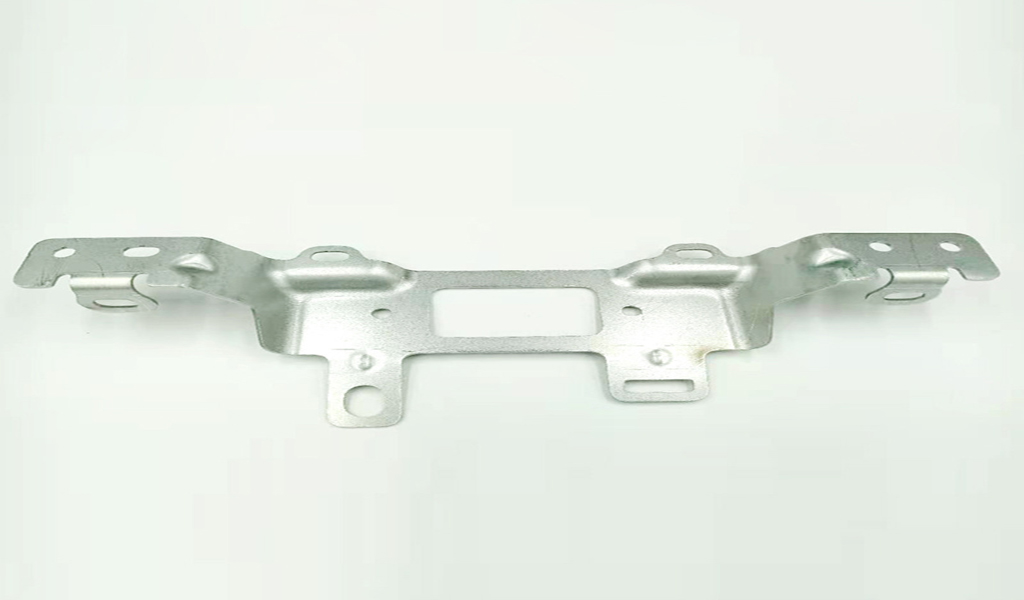
The springback of automobile stamping parts means that after the load is removed, the shape of the deformed body is partially restored, and the shape and size of the part do not match the shape and size of the working surface of the stamping part, resulting in the size of the part not within the tolerance range, affecting the product. Assembly accuracy.
Stamping parts will undergo plastic deformation and elastic deformation during the forming process. After unloading the forming load, the part will spring back to some extent. Springback is the deformation that will occur after the sheet metal is formed and the formed part is removed from the mold, which will affect the shape of the part. Springback directly affects the geometric accuracy of the workpiece, which is also a defect that is difficult to overcome in the forming process.
Stress change curve after unloading
- 1) Stamping parts with different material properties and strengths, from ordinary sheets to high-strength sheets, have different yield strengths. The higher the yield strength of the sheet, the easier it is to spring back. Generally, hot-rolled carbon steel sheets or hot-rolled low-alloy high-strength steel sheets are used as the material for the thick plate parts. Compared with cold-rolled sheets, hot-rolled sheets have poor surface quality, large thickness tolerances, unstable mechanical properties, and low elongation.
- Stress change before and after springback
- 2) Material thickness During the forming process, the thickness of the sheet has a great influence on the bending properties. As the thickness of the plate increases, the springback phenomenon will gradually decrease, because with the increase of the plate thickness, the material participating in the plastic deformation increases, and then the elastic recovery deformation also increases, so the springback becomes smaller.Tangential stress at the metal plate interfaceWith the continuous improvement of the material strength grade of thick plate parts, the dimensional accuracy problem of parts caused by springback is becoming more and more serious. Mold design and post-process debugging require an understanding of the nature and scale of part springback in order to take appropriate countermeasures and remedial plans.For thick plate parts, the ratio of bending radius to plate thickness is generally small, and the stress and its change in the plate thickness direction cannot be ignored.
- 3) There is a big difference in the springback of parts of different shapes. Generally, a forming sequence is added to the parts with complex shapes to prevent the springback phenomenon when the forming is not in place, while some parts with special shapes are more prone to springback. phenomena, such as U-shaped parts, therefore springback compensation is considered during analysis and forming.
- 4) The larger the bending center angle, the larger the accumulated springback value, which will cause serious springback phenomenon. The deformation length of the stamping part increases with the increase of the bending center angle.
- 5) Clearance fit of the mold When designing the mold, leave a gap twice the thickness of the material in the relevant working part, and accommodate the product in this gap. To achieve better material flow, parts of the mold should be prepared after mold machining. Especially for bending dies, the greater the clearance of the working part, the greater the springback. If the tolerance range of the sheet thickness is larger, the springback is larger, and the clearance of the mold cannot be well determined.
- 6) The relative bending radius is proportional to the springback value, so the greater the curvature of the stamping part, the more difficult it is to bend.
- 7) Forming process The forming process is an important aspect that restricts its springback value. In general, the rebound effect of corrected bending is better than that of free bending. If the same fabrication effect is achieved in the production of the same batch of stamping parts, the bending force required for correct bending is much greater than the bending force required for free bending, so if the same bending force is used for both methods, the effect will be different. The greater the correction force required to correct the bending, the smaller the springback of the stamping part, and the correction of the bending force will lengthen the fibers inside and outside the deformation zone, so as to achieve the forming effect. After the bending force is unloaded, the inner and outer fibers are shortened, but the rebound directions of the inner and outer sides are opposite, thus reducing the outward rebound of the stamping parts to a certain extent.
Solutions for stamping springback:
- 1) Product design First of all, in terms of materials, on the premise of meeting product requirements, materials with small output should be selected or the thickness of materials should be appropriately increased. Secondly, the shape design of stamping parts and the springback of stamping parts also have a very important influence. During bending, it is difficult to eliminate springback due to complex stresses in all directions and other factors such as friction. Therefore, in the shape design of the product, for complex stamping parts, several parts can be combined to solve the springback problem.In addition, anti-rebound ribs can be provided, which can also effectively solve the rebound defect. On the premise of meeting the requirements of stamping parts, anti-rebound ribs can be added according to product requirements and the amount of rebound, and the shape of the product can be changed. The springback defect can also be solved by reducing the R angle value of the curved part.
- 2) Process design First of all, the mold design pre-forming process, adding the pre-forming process can make the stamping parts formed at one time distributed in different processes, which can eliminate the internal stress in the forming process to a certain extent, so as to solve the springback defect. Secondly, by reducing the gap between the concave and convex molds, it can be adjusted to about double the thickness of the material, thereby maximizing the adhesion between the material and the mold. At the same time, hardening the mold can also effectively reduce the pulling phenomenon of stamping parts and reduce the wear of the mold.
- Products are also being reinvented. If the design of the product cannot be changed at will, the stamping part can finally be reshaped, which is also the ultimate means. There are some other ways to solve the springback defect, such as using hydraulic punching equipment and setting the footer of the punch, which can solve the springback defect to a certain extent.
- 3) The forming process of blank holder force stamping parts is an important technological measure. By continuously optimizing the blank holder force, the flow direction of the material can be adjusted and the internal stress distribution of the material can be improved. Increasing the blank holder force allows the part to be drawn more fully, especially on the side walls and R corners of the part. If the forming is sufficient, the difference between the internal and external stress will be reduced, thus reducing the springback. 4) Drawbeads and drawbeads are widely used in today’s technology. The reasonable setting of the drawbead can effectively change the flow direction of the material and effectively distribute the feeding resistance on the binder surface, thereby improving the formability of the material. Setting drawbeads on parts that are prone to springback can make the parts more fully formed and the stress distribution is more uniform, thereby reducing springback.
Solutions for Bend Springback
- 1) Correct the bending force to concentrate the punching force in the bending deformation area, forcing the inner metal to be squeezed. After correction, both the inner and outer layers are stretched. After unloading, the springback can be reduced by counteracting the springback tendency of the two crush zones.
- 2) Annealing before bending, reducing its hardness and yield stress can reduce springback and bending force, and then hardening after bending.
- 3) In the production of excessive bending, due to elastic recovery, the deformation angle and radius of the sheet will become larger, and the rebound can be reduced by the deformation degree of the sheet exceeding the theoretical deformation degree.
- 4) Hot bending adopts heating bending. Springback can be reduced if the material has enough time to soften.
- 5) Tensile bending This method applies tangential tension when bending the metal plate, changes the stress state and distribution inside the metal plate, so that the entire section is within the plastic tensile deformation range. After unloading, the springback tendencies of the inner and outer layers cancel each other out, reducing the springback.
- 6) Local compression The local compression technology increases the length of the outer plate by thinning the thickness of the outer plate, so that the rebound trends of the inner and outer layers cancel each other out.
- 7) Multiple Bending Divide the bending into multiple times to eliminate springback.
- 8) The blunting of the fillet compresses from the inside of the bend to eliminate springback. This method works better when the plate is U-shaped because the sides are curved symmetrically.
- 9) Change the overall drawing to local bending forming, and then use bending forming for one part, and then use drawing forming to reduce springback. This method is effective for products with simple two-dimensional shapes.
- 10) Control the residual stress tensile delay, increase the local convex hull shape of the tool surface, and eliminate the increased shape in the subsequent process, thereby changing the residual stress balance in the material and eliminating springback.
- 11) When machining the tool surface with negative springback, try to make the metal plate produce negative springback as much as possible. After the upper die is returned, the workpiece reaches the required shape by springback.
- 12) The electromagnetic method uses electromagnetic pulses to impact the surface of the material, which can correct the shape and size errors caused by rebound.
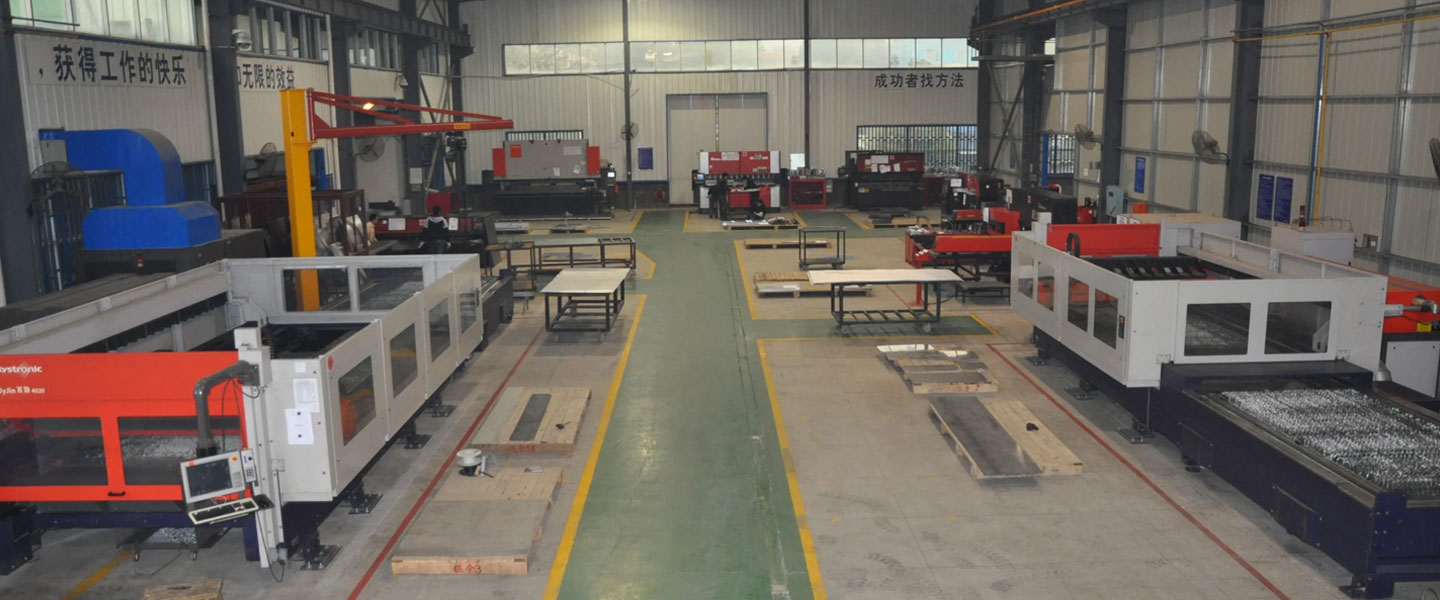
Pintejin Sheet Metal shop offers a cost-effective solution for a wide range of industries with our custom metal stamping and custom sheet metal fabrication capabilities. Our stampnig operations include a variety of sheet-metal forming manufacturing processes, such as punching, blanking, embossing, bending, flanging, and coining. Our professional, experienced and well-trained engineers can execute the complex metal stamping operations with precision and accuracy.
No matter what your metal fabrication needs are, Pintejin can offer the right solution: from single sheet metal part or sub-assembly of stamped metal parts to turnkey solutions for mechanical and electrical assemblies. We have the technology, equipment and the experience to fabricate customised metal products from aluminium sheet metal fabrication, steel, zinc plated steel, stainless steel sheet metal fabrication, brass and copper. Designs that require CNC machining of surfaces or components can be accommodated. We can supply polished, galvanized, zinc coated or powder coated finishes for any sheet metal work or stamped metal components. Coupled with our accurate and reliable metal fabricating equipment, we guarantee precision and repeatability in custom sheet metal work. You’ll be taking advantage of the best sheet metal fabrication china can produce.