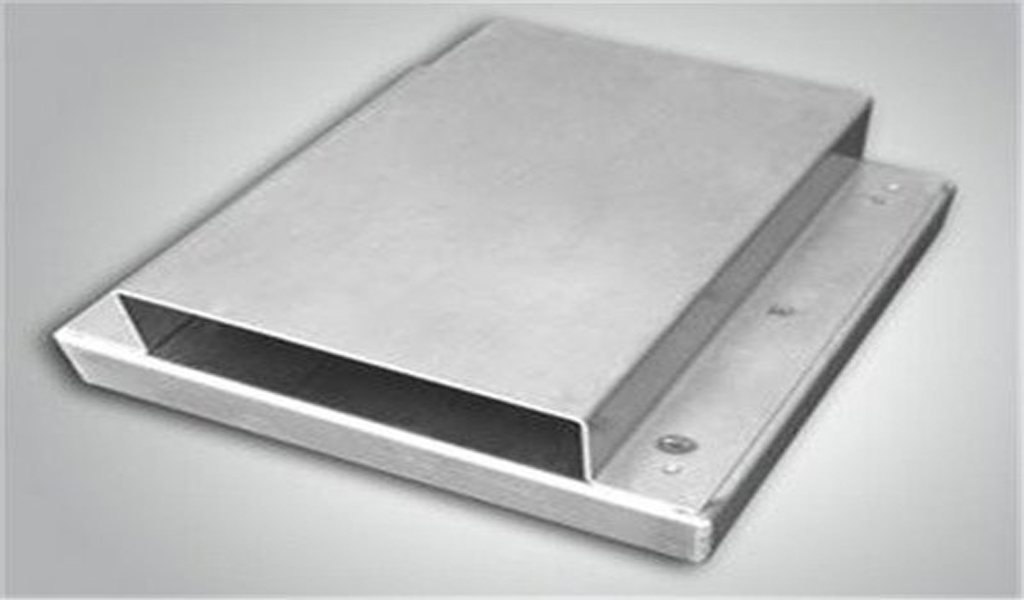
Automobile sheet metal parts are a fabrication method for automobile maintenance, also known as cold work. To put it directly, if the appearance of the body is damaged and deformed, the process of sheet metal is required to restore the original appearance. Basically the tool used is a hammer. Hammers of different shapes, put iron blocks behind the sheet parts, and beat them repeatedly to make them take shape. Appearance restorers are also used when necessary.
Automobile sheet metal parts are a fabrication method for automobile maintenance, also known as cold work. To put it directly, if the appearance of the body is damaged and deformed, the process of sheet metal is required to restore the original appearance. Basically the tool used is a hammer. Hammers of different shapes, put iron blocks behind the sheet parts, and beat them repeatedly to make them take shape. Appearance restorers are also used when necessary. This thing actually belongs to welding. Weld the hoop to the body and pull it out with the hook. Used to repair sunken areas. A large flat body is generally difficult to get back in place, so it is sometimes used to close the fire. It is to cool down after local heating, so that the iron sheet shrinks. The ultimate goal is to restore the damaged body to its original appearance.
Many car owners do not know the operation process very well. The following summarizes the whole process of repairing dents in sheet metal:
- (1) Disassembly of sheet metal parts. The sheet metal parts of the damaged parts of the collision vehicle are detached from the original body by cutting or other methods.
- (2) Damage confirmation. After cleaning the damaged area, confirm the degree of damage and establish a repair method.
- (3) Remove the old paint film. Sand the original car paint on the damaged part until the iron plate is exposed.
- (4) Flatten the sheet metal parts. According to the damage degree of the sheet metal parts, the corresponding sheet metal tools are used to level the recessed parts of the auto parts. After the leveling operation, the surface of the sheet metal part should be fine-tuned for flatness.
- (5) Fire treatment. Through the fire treatment, the tensile and extrusion stress generated in the process of restoring the original shape and thickness of the metal is eliminated, and the rigidity and strength of the sheet metal part are maintained.
- (6) Sand the feathered edge. Grind a buffered slope at the connection between the damaged part and the surrounding paint film, so that the newly sprayed paint surface can be better connected with the original car paint surface.
- (7) Apply epoxy primer. Clean and degrease the polished damaged surface again, apply epoxy primer and dry it for anti-rust treatment. The above sheet metal operation procedures are suitable for sheet metal parts with little damage. If the collision of the car body is serious and the frame is injured, it is necessary to correct the whole vehicle frame on the frame straightening machine, and the operation will be more difficult.
Painting operation process (continuation of the above sheet metal process):
- (1) Scratch putty. After cleaning and degreasing the damaged sheet metal parts coated with epoxy primer, scrape and apply putty, which is what we often call putty. After the putty is dry, it is sanded and the punch line is confirmed.
- (2) Spray primer with middle coat. After the putty is sanded, clean and degrease, start spraying the primer, and bake it to dry. When applying the primer during spraying, pay attention to the necessary shielding of the parts that do not need to be sprayed.
- (3) Primer during sanding. Grind the primer to the same height as the original paint to confirm the flatness.
- (4) Toning. Although the original paint is generally available in the special service shop at present, because the color of the topcoat is different from the original paint after the vehicle has been used for a long time, the paint sprayer needs to manually adjust the paint.
- (5) Spray topcoat. Add the adjusted topcoat to the spray gun tank, adjust the air pressure, paint volume and spray width of the spray gun, and then start to spray evenly on the sheet metal parts. The process of spraying different topcoats is also different. In fact, the literal understanding of sheet metal is: sheet, that is, the meaning of plate, thin plate, is the meaning of serial fabrication of thin metal plates, including folding, shearing, punching, welding, riveting, splicing and other processes.
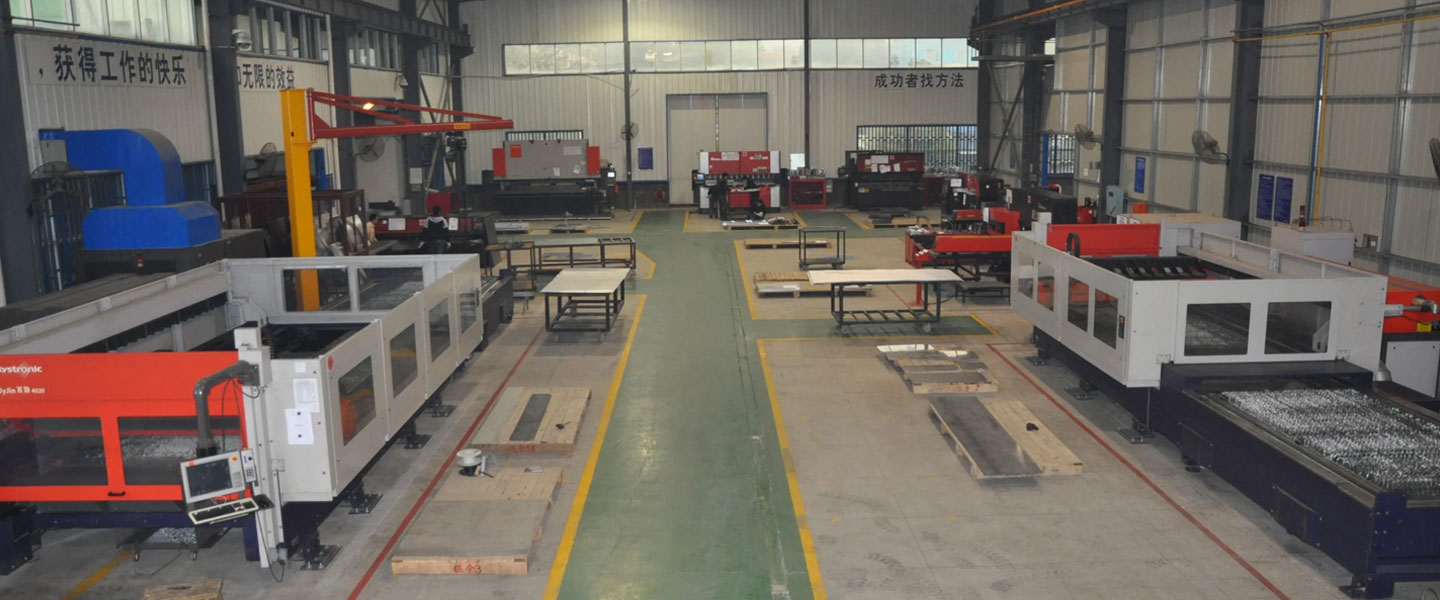
Pintejin Sheet Metal shop offers a cost-effective solution for a wide range of industries with our custom metal stamping and custom sheet metal fabrication capabilities. Our stampnig operations include a variety of sheet-metal forming manufacturing processes, such as punching, blanking, embossing, bending, flanging, and coining. Our professional, experienced and well-trained engineers can execute the complex metal stamping operations with precision and accuracy.
No matter what your metal fabrication needs are, Pintejin can offer the right solution: from single sheet metal part or sub-assembly of stamped metal parts to turnkey solutions for mechanical and electrical assemblies. We have the technology, equipment and the experience to fabricate customised metal products from aluminium sheet metal fabrication, steel, zinc plated steel, stainless steel sheet metal fabrication, brass and copper. Designs that require CNC machining of surfaces or components can be accommodated. We can supply polished, galvanized, zinc coated or powder coated finishes for any sheet metal work or stamped metal components. Coupled with our accurate and reliable metal fabricating equipment, we guarantee precision and repeatability in custom sheet metal work. You’ll be taking advantage of the best sheet metal fabrication china can produce.