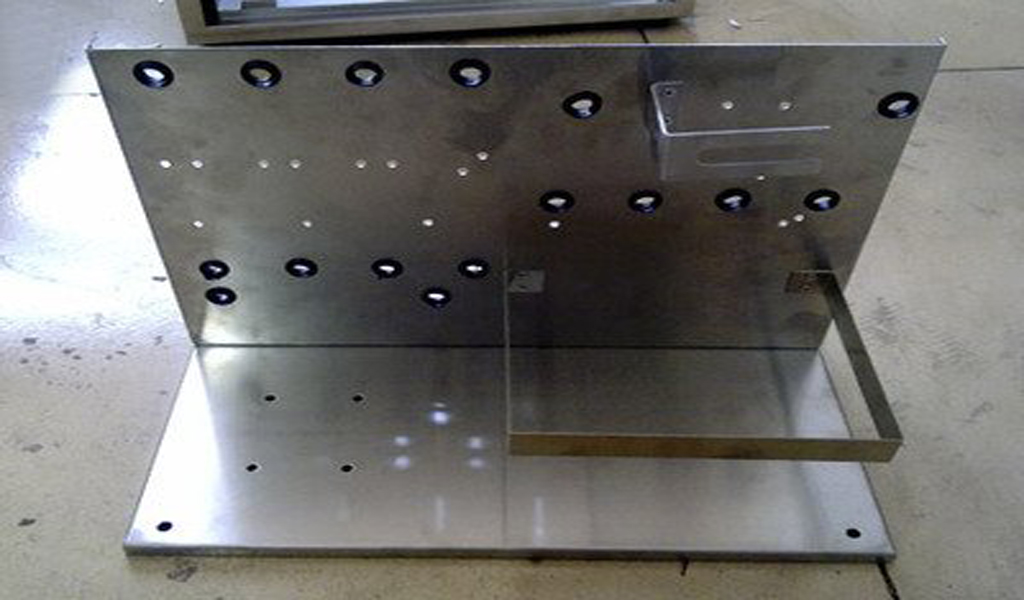
The fabrication of automobile stamping parts is one of the practical processes for the forming and production of large-scale parts. Die failure is an easy problem in stamping production, which often causes production stoppage and affects the product production cycle. Therefore, it is necessary to find the cause of the mold failure as soon as possible and repair it reasonably.
mold damage
Mold damage refers to mold cracking, breaking, opening, etc. To solve the problem of mold damage, it is necessary to find the reasons from the design of the mold, the manufacturing process and the use of the mold. If foreign objects enter the mold, parts overlap, waste obstruction, etc. are not dealt with in time, and continue fabrication and production, it is easy to damage the blanking plate, punch, lower template and guide post of the mold. The spring force design is too small or the height of the sleeve is not equal, which will cause the spring to break and the blanking plate to tilt, resulting in overlapping punches and damage to parts. If the quenching temperature of the mold is too high, the quenching method and time are unreasonable, and the number of tempering and temperature, and the selection of elbows are improper, it will cause the mold to be damaged after entering the stamping production. Improper fixing of the punch or insufficient strength of the screw. It will cause the punch to drop or break. The working height adjustment is too low, and the guide column is not lubricated enough. Usually, the heat treatment process of the mold material has a great influence on it. The size or depth of the blanking hole is not designed enough, which can easily block the slot and cause damage to the blanking plate. When the mold is used, the position and direction of the parts are installed incorrectly or the bolts are not fastened properly.
Card mold
The main reasons for the die are: incorrect orientation and tilt of the die. Otherwise, it will expand the failure, resulting in mold damage. Cause the deformation of the mold, such as the hardness and thickness of the mold base and the template are too small, and are easily deformed by the impact of external force; the position of the mold is not installed correctly, and the positioning error of the upper and lower molds is out of tolerance. At this time, the strength of the punch should be increased and the guide protection of the stripper plate should be enhanced.
Or the precision of the press is too poor, causing the mold to interfere; the strength of the punch is not enough, and the position of the large and small punches is too close, so that the lateral force of the mold is unbalanced. During the stamping process, once the mold clamping is inflexible or even stuck, it is necessary to stop production immediately, find out the cause of the stuck mold, and eliminate the fault.
Die damage and repair
The die cost of stamping production is high. Usually, the die cost accounts for 1/5-1/4 of the total cost of the part. The one-time repair cost exceeds 70% of the original cost of the die, or the die life is approaching. When the mold maintenance technology is too complicated, the mold repair cost is too large, and the difficulty is high, the maintenance cycle will be too long, which will seriously affect the normal production of stamping. Generally speaking.
After the mold is damaged, there is also a choice of maintenance and scrapping. but. Therefore, timely maintenance of the mold and prevention of mold damage can greatly reduce the mold cost of stamping production. When the hinge parts of the mold are severely damaged, sometimes the convex and concave molds are damaged at the same time. This is because, in addition to the difficulty and high cost of mold manufacturing. Unnatural wear failure of stamping dies, such as failure of non-hub parts.
Under normal circumstances, the main failure mode of stamping die is excessive wear. Manufactured from new molds for delivery. Until the burrs of the punched parts exceed the standard, the size and shape accuracy of the parts are out of tolerance, and the mold can no longer be repaired or has no repair value at all, the mold can only be scrapped. From the new mold being put into use to the failure and scrapping.
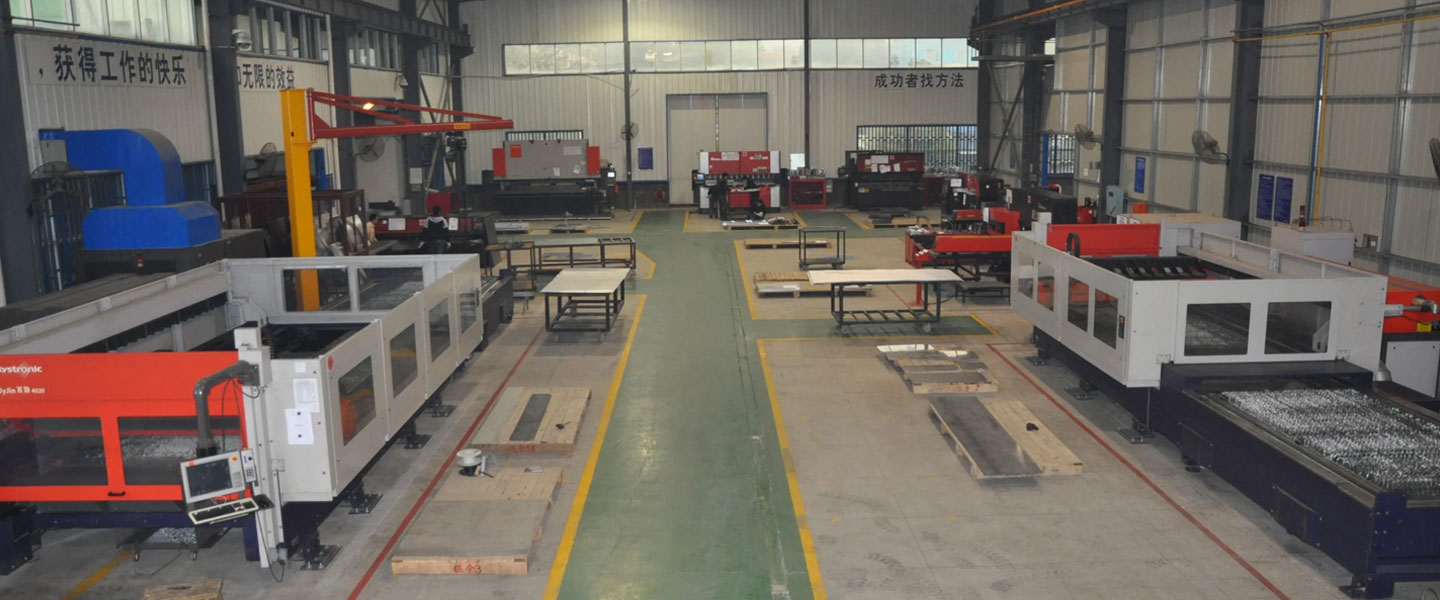
Pintejin Sheet Metal shop offers a cost-effective solution for a wide range of industries with our custom metal stamping and custom sheet metal fabrication capabilities. Our stampnig operations include a variety of sheet-metal forming manufacturing processes, such as punching, blanking, embossing, bending, flanging, and coining. Our professional, experienced and well-trained engineers can execute the complex metal stamping operations with precision and accuracy.
No matter what your metal fabrication needs are, Pintejin can offer the right solution: from single sheet metal part or sub-assembly of stamped metal parts to turnkey solutions for mechanical and electrical assemblies. We have the technology, equipment and the experience to fabricate customised metal products from aluminium sheet metal fabrication, steel, zinc plated steel, stainless steel sheet metal fabrication, brass and copper. Designs that require CNC machining of surfaces or components can be accommodated. We can supply polished, galvanized, zinc coated or powder coated finishes for any sheet metal work or stamped metal components. Coupled with our accurate and reliable metal fabricating equipment, we guarantee precision and repeatability in custom sheet metal work. You’ll be taking advantage of the best sheet metal fabrication china can produce.