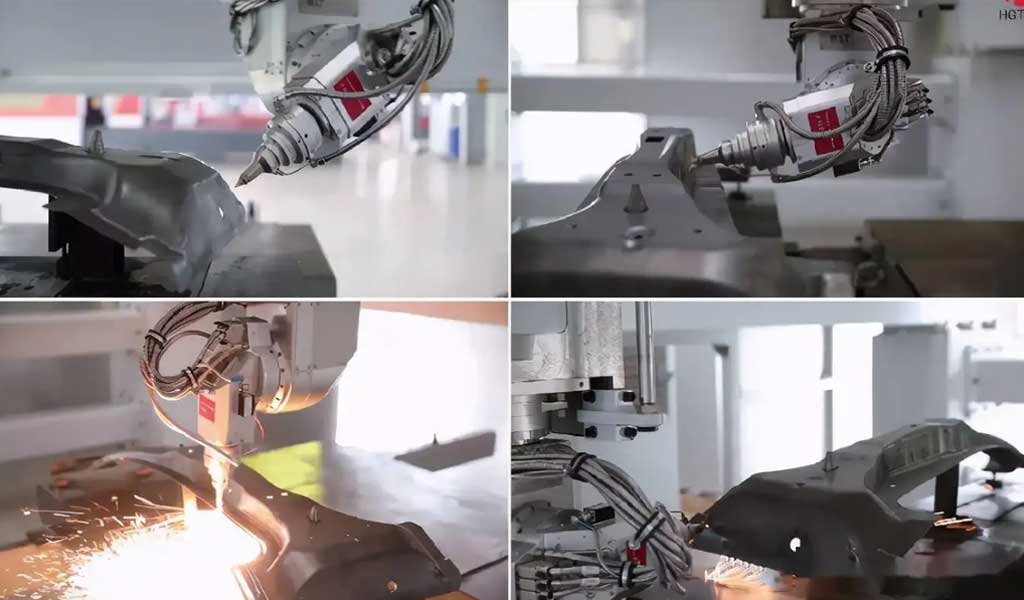
Machinery manufacturing is a pillar industry in my country and plays an indispensable and important role in social and economic development. It has great potential for development and broad prospects. In order to realize the dream of a powerful country and occupy a place in the development of the world, relevant machinery manufacturing enterprises should innovate independently to ensure the production of high-quality products. An important aspect of independent innovation is to carry out technological innovation, which also includes laser processing technology, an internationally recognized advanced technology. Continuous improvement and perfection of laser processing technology can effectively promote the development of machinery manufacturing industry.
The Basic Principle Of Laser Manufacturing Technology
Laser processing technology is an advanced comprehensive processing technology, which integrates optics, electricity, mechanics, etc., to a certain extent, it can be called the universal processing technology of the new era. The emergence and update of laser processing technology has effectively promoted the Advances in machinery manufacturing. The essence of laser is a photon beam, which occurs when atoms are hit by energy such as electric current, and is concentrated in one direction and has a certain amount of energy. The chain reaction of photons and atoms can produce very high energy. The laser beam containing very high energy is irradiated toward the surface of the workpiece. Combined with computer numerical control technology, it can be combined to form a processing equipment. Laser processing metal and non-metal materials, cutting, drilling and welding. Laser processing technology has very high precision in processing and manufacturing mechanical products, and is a very important and necessary technology in the machinery manufacturing industry.
The Advantages Of Laser Manufacturing Technology
As a high-precision advanced technology, laser processing technology is widely used in many aspects of mechanical manufacturing and processing, and has broad application prospects. The main advantages of laser processing technology are: laser processing has high precision, material utilization rate and processing efficiency, and of course the economic benefits are also high. Using a laser cutting machine with a price of 300,000 yuan for normal processing, the cost can be recovered and profitable in one and a half years. The laser uses the light source as the energy medium and has extremely fast processing speed. The processing speed of 3G laser cutting machine is beyond doubt. Laser processing has good anti-interference, is not easily influenced by environmental factors, and can ensure the quality of processed parts. Laser processing can effectively utilize materials and can save 10%-30% of materials compared with other processing technologies. Because laser processing does not need to touch the workpiece, it can effectively save consumables and reduce production costs. There are many suitable materials for laser processing, which can process both metal materials and non-metal materials, and can realize the processing of different shapes such as straight lines, curves and even special-shaped figures.
The Application Of Laser Cutting Technology
Laser cutting technology uses a high-energy-density laser beam to irradiate the device with strong light, and the irradiation temperature rises extremely quickly. After the material is vaporized, the steam is quickly discharged or melted in a short time, and the auxiliary gas helps to discharge the liquid smoothly. Corresponding slits are thus created. Laser cutting technology is the main cutting method for industrial materials, and laser and numerical control technologies are also developing continuously.
When the laser equipment is cutting, the laser beam can be focused into a very small spot, which maximizes the power of the laser cutting machine, the cutting speed is very fast, and of course the accuracy is quite high, at the same time, it ensures that the workpiece will not occur. deformation. The laser cutting technology uses thermal cutting to realize the operation, and the affected area is very small when the cutting is carried out, and it will not spread to a large area, and it can also process some non-metallic materials. Laser cutting technology has a lot of energy and can easily control the density, and it is also suitable for local operations. In automobile manufacturing, laser 3D cutting is used to update the original stamping and trimming molds when producing body panels. In this way, new cars can be put into production as quickly as possible after they are developed, and the production time of automobiles can be greatly reduced. Among machinery manufacturing enterprises, Japan regards laser cutting as a standard process, which accelerates the development of new products, improves product quality, and makes enterprises more competitive. Some machinery manufacturing enterprises in China also vigorously advocate and promote the use of laser cutting technology. Laser cutting technology is also widely used in the aerospace industry. The parts to be cut include titanium alloy skins, engine flame tubes, aircraft frames and titanium alloy thin-walled machines. On the whole, large-format laser cutting machines have been used by many heavy industrial enterprises around the world.
At present, two types of laser cutting machines are mainly used for processing construction machinery sheets: CO2 laser cutting machine and fiber laser cutting machine. The propagation of the fiber laser is carried out in the fiber, which has better passability, and the energy beam is also very high, but the thermal influence is smaller, and a narrower cutting line will be formed, so that the cutting efficiency will be high, and it can be used more effectively material, and further reduce the thermal deformation of the plate during blanking.
The Application Of Laser Welding Technology
Welding technology is a key process in machinery manufacturing, which has an important impact on the production cost and cycle of products. Arc welding, a traditional welding method, has the disadvantage of deforming mechanical products, requiring post-weld orthopedics, time-consuming and poor quality assurance. Laser welding has a variety of functions, strong adaptability and reliability, high power density, small heat input, narrow heat affected zone, high speed and small welding deformation, and it is very easy to achieve automation. touch the workpiece. Applying laser welding to machine manufacturing can increase the strength of the weld, reduce post-weld correction work, and make the appearance and structure more perfect. Laser welding is widely used in construction machinery bulldozers, and the process of laser welding of thick steel plates has been optimized.
The application of laser welding gear technology to the processing of automobile transmission not only has high production efficiency but also does not waste raw materials. When laser welding gears, it has a narrow heat-affected zone of the weld seam, high strength, and the weld seam has an aspect ratio of 12:1, and the mechanical properties of the weld seam are equivalent to or even higher than the base metal, so that the transmission to the gear is greater. The torque provides a guarantee; heating and cooling can be achieved very quickly, the deformation of the welding gear can be controlled very small, and the gear does not need to be finished after welding; the stability and accuracy of the processing process are high, and the speed is also fast, Dissimilar materials can also be welded. Laser-welded gear technology has greatly improved the manufacture of mechanical transmission gears.
The application of laser welding technology in automobile manufacturing can not only increase the strength of the car body, but also make the appearance of the weld more beautiful and smooth with its advantages. The cabs of some construction machinery such as forklifts and bulldozers are bulky and rigid in appearance. Introducing laser welding in their design and manufacture is an inevitable method, and the mechanical appearance will give people a beautiful and lively feeling.
The Application Of Laser Cladding Technology
Mechanical remanufacturing has developed rapidly in recent years. On the one hand, the state advocates green manufacturing and advocates energy saving and consumption reduction; on the other hand, remanufactured mechanical products have performance as good as new products, but the price is only about 2/3 of new products. It can be recognized by users, and the manufacturing cost of the enterprise is only about 50%, and it is also willing to engage in remanufacturing. The remanufacturing of parts is mainly to replace some seals and wearing parts, and to repair the wear of the mechanism. The most important technology used in this is laser cladding technology, that is, high-efficiency laser surfacing technology. The basic principle of laser cladding technology is to make a high-power and high-density laser beam act on the surface of the substrate, so that a micro-melting layer appears, and the fused alloy powder with a specific composition can be preset and added simultaneously, so as to uniformly repair the damaged surface. Worn parts, which is an additive manufacturing technology. The flexibility of laser cladding technology is strong, the surfacing area and material of the parts are optional, and the performance is also optional, which provides a strong technical support for differentiated customized products. For example, if the crawler tensioning spring cylinder used for the chassis of a high-power bulldozer is worn and needs to be repaired, the laser cladding technology can be used to perform additive processing on the worn area (see Figure 1 for a schematic illustration), and the wear resistance indicators and cladding status can be detected from multiple aspects. The layer hardness gradient is reasonable, the surface hardness reaches the standard, and the metallographic structure is also very good, which effectively prolongs the life of the high-power bulldozer spring barrel by 3 times. Not only limited to mechanical remanufacturing, the application of laser cladding technology to replace the original chrome plating and pre-induction heat treatment technology on new products will also greatly enhance the competitiveness of the products.
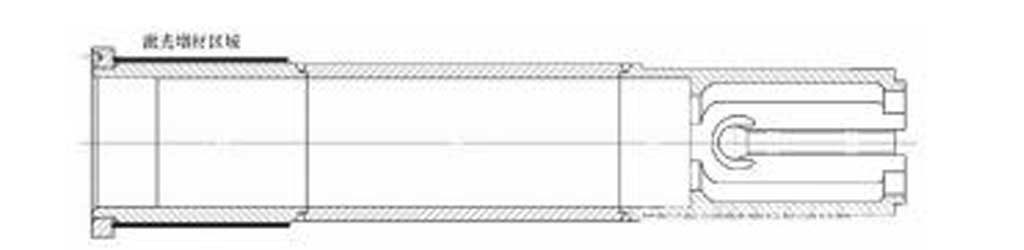
The Application Of Laser Marking Technology
Different parts of mechanical products must be marked, such as barcodes, company logos, serial numbers and production dates, which help companies create and promote their brands. The traditional pneumatic marking machine is slow, noisy, unclear, and consumes a lot of spare parts, which lags behind the modernization of production.
Laser marking technology irradiates the workpiece locally through a high-energy-density laser, causing the surface material to vaporize or change in color, and use chemical reactions to retain permanent marks.
Laser marking technology has obvious advantages over traditional marking methods:
- (1) There is no contact with the workpiece, no cutting force occurs, and the thermal influence is small, which can effectively maintain the accuracy of the workpiece, can be applied to a variety of materials, and the marking is fine and durable.
- (2) The laser has good controllability in time and space, and has a large degree of freedom for the material, size, shape and processing environment of the workpiece, and is especially suitable for automatic processing and special surface processing.
- (3) The laser has the characteristics of fine scribing, and the marks made are difficult to change and imitate.
- (4) It is easy to cooperate with computer numerical control technology to produce a variety of different characters, symbols and patterns, and the patterns can be designed, marked or changed through software to meet the requirements of modern production.
- (5) Clean and pollution-free, green and environmentally friendly. Laser marking technology is widely used in various industries because of its advantages, and plays an important role in establishing a mechanical brand image for modern manufacturing enterprises.
Conclusion
In order to better achieve the goal of “Made in China 2025”, it is necessary to change the previous low-end, low-efficiency and high-energy consumption machinery manufacturing production situation. Laser processing technology is a cutting-edge high-precision mechanical manufacturing technology, which meets the needs of modern production and should be actively explored and promoted. In the context of strengthening technology research and development, laser processing technology will continue to improve, equipment will be more intelligent and miniaturized, and processing functions will be diversified, so that China’s machinery manufacturing level will continue to improve.