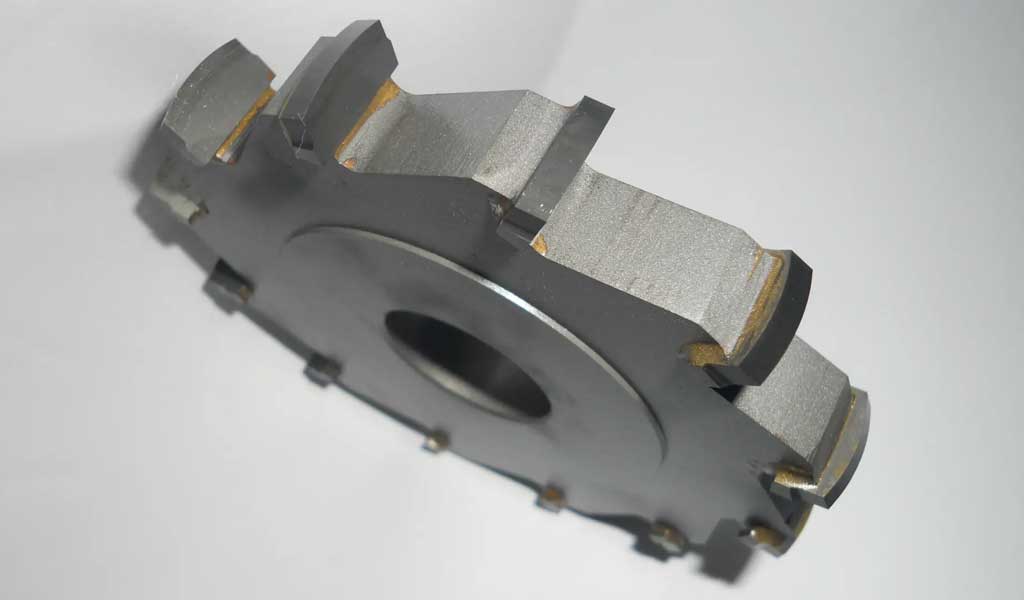
At present, the processing of aluminum parts is mainly divided into two categories: deformed aluminum alloy and cast aluminum alloy. So what milling cutter is used for processing aluminum alloy? Is it better to use aluminum alloy special milling cutter or aluminum alloy special tool? This article talks about the best milling cutter for processing aluminum alloy from the aspects of milling characteristics, machining tools and cutting parameters of aluminum alloy.
The CNC Machining Characteristics Of Aluminum Alloy
Milling aluminum alloy mainly has the following characteristics;
1.Low Hardness Of Aluminum Alloy
Compared with titanium alloys and other hardened steels, the hardness of aluminum alloys is lower, of course, the hardness of heat-treated or die-cast aluminum alloys is also very high. The HRC hardness of ordinary aluminum plates is generally below HRC 40 degrees. Therefore, when machining aluminum alloys, the load of the tool is small. And because the thermal conductivity of aluminum alloy is better, the cutting temperature of milling aluminum alloy is relatively low, which can improve the milling speed.
2.Aluminum Alloys Have Low Plasticity
Aluminum alloy has low plasticity and low melting point. When machining aluminum alloys, the sticking problem is serious, the chip evacuation performance is poor, and the surface roughness is relatively high. In fact, the processing of aluminum alloy is mainly due to the poor effect of sticking and roughness. As long as the two major problems of sticking the knife and the quality of the machined surface are solved, the problem of aluminum alloy processing will be solved.
3.The Tool Is Easy To Wear
Because of the use of unsuitable tool materials, when machining aluminum alloys, the tool wear is often accelerated due to problems such as sticking and chip removal.
What Milling Cutter Is Used For Machining Aluminum Alloy?
Generally, 3-blade aluminum milling cutters are used to process aluminum alloys. Secondly, due to the difference in processing conditions, 2-blade ball-end knives or 4-blade flat-bottomed knives are likely to be used. However, Dongguan Dahai suggests that in most cases, a 3-blade flat-bottom end mill can be used.
1.Selection Of Tungsten Steel Milling Cutter For Aluminum
The number of blades is generally 3, and the material is generally YG-type cemented carbide, which can reduce the chemical affinity between the tool and the aluminum alloy. General CNC tool brands have special milling cutter series products for processing aluminum alloys, such as 3P series of DaElement brand, AL series of Swiss Fraisa, etc.
2.High-Speed Steel Material
High-speed steel aluminum milling cutters are relatively sharp, and can also process aluminum alloys well.
Cutting Parameters For Milling Aluminum Alloy
High-speed and high-feed milling can generally be selected for processing ordinary aluminum alloys. Secondly, choose a larger rake angle as much as possible to increase the chip space and reduce the phenomenon of sticking. If it is finishing aluminum alloy, water-based cutting fluid cannot be used to avoid the formation of small pinholes on the machined surface. Generally, kerosene or diesel oil can be used as the cutting fluid for processing aluminum plates.
The cutting speed of aluminum alloy milling cutters varies due to the material and parameters of the milling cutters and different processing techniques. The specific cutting parameters can be processed based on the cutting parameters given by the manufacturer.