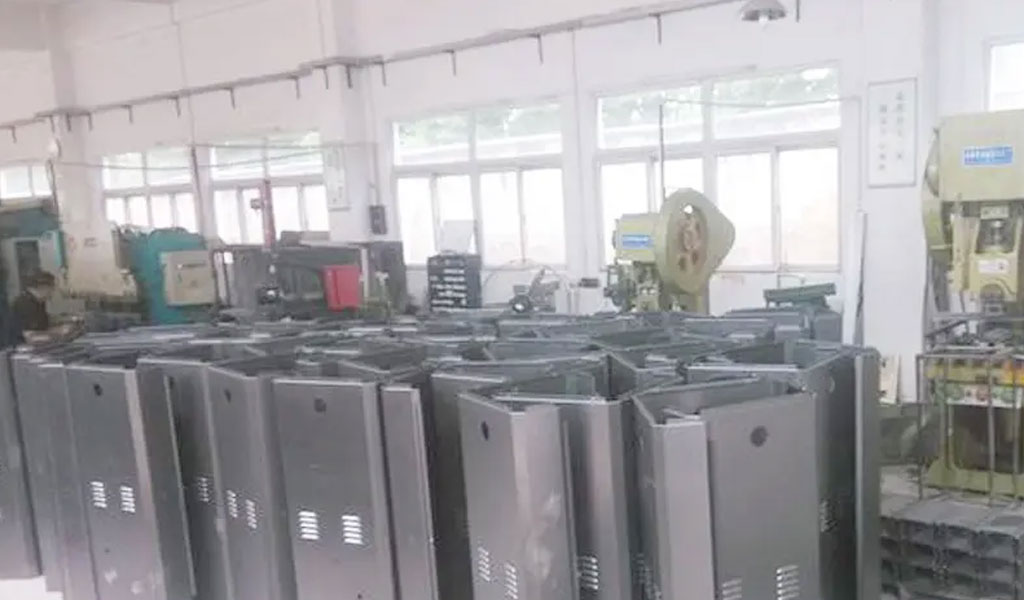
The precision sheet metal fabrication planning module includes a set of sheet metal features specially used for modeling, and is completely integrated with UG composite modeling, enabling planners to start from the concept of planning and production, rationalize the planning process, and create the basis for any production situation. The physical design, can define and simulate the production process, and can capture the production information in any situation (running or unfolding). In addition, the generated precision flat pattern data can be used as a reference for blank data.
The sheet metal fabrication and production module provides auxiliary production processes such as punching, punching, laser and infrared cutting for sheet metal parts. The nesting module provides nested nesting consisting of user-selected, parameter-controlled, optimized, and multiple NC programs. The two modules of production and layout generate the file output of the tool position source file (CLS), and then the UG post-fabrication program generates the NC data.
The sheet metal fabrication and sheet metal layout module provides interactive graphics and automatic methods for the NC programming of stamping, laser cutting, infrared and plasma cutting sheet metal parts, so as to minimize the programming time and use the least data. The UG solution can combine all the advantages of the user’s machine tool controller (including subroutines and standard cycles) to establish a dedicated post-processor for the NC source program, making the program size smaller.
In sheet metal forming fabrication, advanced sheet metal fabrication technologies and equipment such as laser cutting and CNC punching are constantly breaking through and innovating. The technology and equipment for removing edges, burrs, slag and oxide scale after these processes have also continued to develop and progress. The following editor will explain it.
Deburring Technology In The Sheet Metal Fabrication Industry
Types of burrs in sheet metal fabrication
The types of burrs are different according to the different profiles, different structural shapes and different fabrication methods, and the types of burrs formed are also different.
The cold cutting burr is the plastic deformation caused by the grain shear slip and plastic deformation of the workpiece under the action of the cutting force, so that the processed material is squeezed and torn, resulting in the occurrence of fracture stretching on the surface of the part or at the junction. Deformation burrs. When the plastic deformation zone is not deep into the cutting surface, the workpiece surface generally does not produce burrs. For example, the workpiece after CNC punching and shearing will leave sharp edges or trace burrs on one side.
Thermal cutting means that after laser cutting of carbon steel plate, stainless steel plate, galvanized plate, copper, aluminum and other metal materials, the cutting surface of the workpiece leaves a sharp cutting edge and a small amount of burrs that can easily cause human scratches. If the laser head is not adjusted properly, sharp and difficult to remove burrs and slag and oxides attached to the cutting edge area will appear. The cutting edge of carbon steel by laser cutting will also leave oxide scale of different thicknesses, which will affect the quality of the next coating process.
The surface of the workpiece after plasma and flame cutting will also leave a large number of sharp burrs or slag and thick oxide skin. These burrs, cutting edges or oxides will cause human injury and affect the next fabrication process, resulting in serious product quality problems. Therefore, the workpieces after laser, plasma, and flame cutting all require the removal of slag, burrs, and grinding and filleting. This requires professional fabrication equipment to complete.
Sheet metal fabrication deburring method
In the traditional sheet metal fabrication process, after the workpiece is blanked, the corners, burrs, and joints need to be polished. At the tool joints, use a flat file for trimming. For workpieces with large burrs, use a grinder to trim them. Use a corresponding small file for trimming at the small inner hole joints. The manual operation error is large, the appearance cannot be guaranteed, and the special-shaped groove or quality Products with high requirements cannot be satisfied by manual fabrication.
In order to improve the industrial economy, the universal roller brush deburring equipment designed and developed by our company. Advanced automation technology is adopted as the core control system of the equipment to automatically and flexibly control all fabrication actions of the equipment. Integrating the equipment into the production line realizes the automatic assembly line fabrication of the equipment and reduces the number of on-site operators, which not only improves the fabrication efficiency, but also saves the production cost.
Shearing and punching process for precision sheet metal fabrication
The raw material of the sheet metal fabrication process is the output of the rolling process, usually the sheet metal is sold as a standard-sized flat rectangular sheet, or in rolls if the sheet is very long. So the first step in any sheet metal craft is to cut the correct shape and select the “blank” from the larger worksheet. Sheet metal fabrication is an important process for many industries, which are among the largest manufacturers of household appliances (refrigerators, washing machines, dryers, vacuum cleaners, etc.), electronic products (DVD and CD players, stereos, radios, etc.), amplifiers etc.), toys and personal computers. Most of these products have metal casings made by cutting and bending sheet metal. Let’s look at some basic sheet metal cutting and forming processes.
Cutting in precision sheet metal fabrication is similar to the process of using scissors to cut a sheet of paper, however, the machines used are a bit different, there are two typical machines used to cut sheet metal – the first is a shearing machine, which has A long blade used to cut straight lines; it is used to cut long sheets of metal into smaller sheets. The operation is similar to that of a decoupage machine: a sheet of metal is held on top of a hardened die, and a shearing blade cuts down, usually driven by an electric or hydraulic punch.
Another sheet metal punch-cut tool is a punch, a piece of hard tool steel, which is punched to cut a hole in the sheet. The punch is a turret punch – the turret is a rotary tool holder that can hold dozens of dies of different shapes and sizes, with typical shapes being rectangular and circular. Through a series of punching, long grooves can be cut. A typical punch operation is similar to what you might have used to punch holes to hold paper in a three-ring binder.