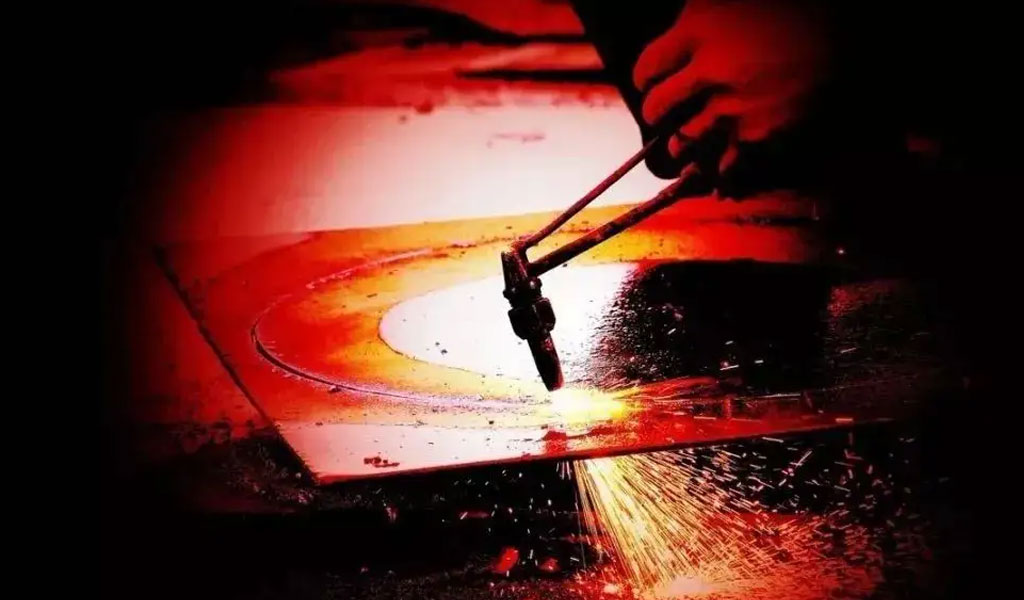
Due to local heating and rapid cooling during gas cutting, three-dimensional deformation will occur in the cutting area and the thin plate parts will warp. Due to the action of the gas cutting heat source (mainly the combustion heat reaction), the material in the incision area is heated to deform, and the surrounding material is also affected by the heat, and the binding force is reduced, so part of the deformation cannot be recovered during cooling, resulting in permanent deformation. At the same time, during the cutting process, due to the thermal expansion and contraction of the material, there will be displacement, even if the high-precision gantry cutting machine and NC cutting machine are used, the cut parts will still have a large dimensional deviation. Therefore, preventing and reducing cutting deformation is an important measure to ensure cutting accuracy.
The Methods And Measures To Prevent And Reduce Cutting Deformation
1.Limit Excess Heat Input.
The more the material is heated, the greater the deformation will be. Therefore, it is necessary to avoid unnecessary and excessive heating of the material. The main methods are:
- Select the appropriate cutting nozzle number according to the thickness of the plate, and it should not be too large.
- On the premise of ensuring the quality of the cutting surface, speed up the cutting speed as much as possible. If the diffusion type cutting nozzle and the oxygen curtain cutting nozzle are used, a faster cutting speed can be obtained, especially the latter cutting nozzle, the protective oxygen has a certain cooling effect on both sides of the incision. Another example is the straight line cutting of medium and thin plates, the cutting torch is tilted back to speed up the cutting speed. In addition, the application of high-purity oxygen can also speed up the cutting speed.
- When the material is numbered, the edges of adjacent parts are combined to form a common cutting line. This not only reduces the number of cuts, reduces the heat of the material, but also improves the cutting efficiency.
2. Heat The Symmetrical Sides Of The Workpiece At The Same Time.
The two symmetrical sides of the material or workpiece are heated at the same time, especially when cutting strips, because the thermal deformation directions are opposite and can cancel each other out. This greatly reduces deformation. The specific method is:
- Two symmetrical sides of the material are cut at the same time, or when one side is cut, the other side is heated at the same time.
- When cutting long and narrow slats, use double cutting nozzles or multiple cutting nozzles to cut at the same time. When using a semi-automatic cutter, an additional torch can be added for dual-tip cutting.
- When using a single cutting nozzle to cut the slats, the symmetrical edge cutting method is adopted.
3. Limit Part Deformation Method
Limit thermal deformation of parts during cutting, which is especially common in photoelectric tracking and CNC cutting. The main methods are:
- Set the “Bridge Method”. That is, on the cutting line of adjacent parts, according to the shape of the part, a small section (the length of which is 10~15mm) is not cut temporarily (this temporarily cut section is called “bridge”), so that the parts can be restrained and restrained. its deformation and displacement. Wait until all parts of the material have been cut, and then cut the “bridge” with a hand torch.
- End limit method. When cutting the slats from the whole steel plate, use a manual torch to cut a long hole of 3~5mm*50~80m at both ends of the steel plate and near the cutting line 5~10mm away from the end edge, and then use a semi-automatic cutting machine to cut Start cutting at the long hole, and cut all the cutting lines one by one, and finally cut along the cutting line at the end of the board. Since the two ends of the slats are fixed, and the lateral bending is restricted by the adjacent slats, the cut slats basically have no side bending.
- The circuitous cut-in method. When cutting parts on the nested steel plate, in order to avoid the trouble of drilling and cutting from the inside of the plate, the method of cutting from the edge of the plate is often used.
4. Use The Proper Cutting Sequence
When cutting kit parts, reasonable selection of the starting point, cutting sequence and cutting direction can reduce the deformation, which is one of the effective methods to obtain good cutting accuracy. The choice of cutting sequence depends on the nesting condition on the steel plate and the shape of the part. The general principle is to keep the scrap, residual material, etc. as closed as possible to limit the deformation and movement of its internal parts. The specific essentials are:
- First, cut the parts with small size, complex shape and high precision requirements from the inside of the board, and then cut the parts with large size and simple shape.
- Cut the hole inside the part first, and then cut the shape.
- After cutting the nesting parts on the steel plate, cut off the surrounding waste edges.
5. Sprinkling Water Cooling Method
Sprinkling water near the cut for cooling during the cutting process is also an effective way to prevent gas cutting deformation. Water cooling significantly shortens the duration of the material at the plastic deformation temperature, and the temperature around the cutting line also decreases, which means that the constraint on plastic deformation increases, thereby greatly reducing the occurrence of deformation. This method is more suitable for automatic cutting applications such as portal cutting machines and CNC cutting machines.