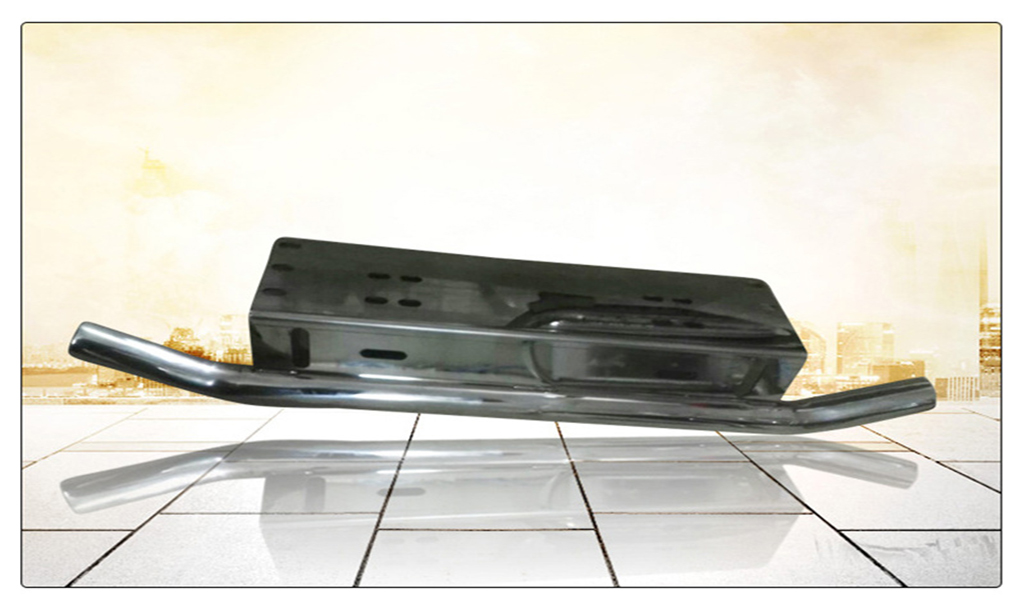
The hardness test of metal stamping parts adopts Rockwell hardness tester. Small, complex-shaped stampings can be used to test small planes that cannot be tested on ordinary benchtop Rockwell hardness testers.
The fabrication of metal automobile stamping parts includes blanking, bending, deep drawing, forming, finishing and other processes. The materials for stamping parts are mainly hot-rolled or cold-rolled (mainly cold-rolled) metal sheet and strip materials, such as carbon steel sheets, alloy steel sheets, spring steel sheets, galvanized sheets, tin-plated sheets, stainless steel sheets, copper and copper alloys Plate, aluminum and aluminum alloy plate, etc.
The PHP series of portable surface Rockwell hardness testers are ideal for testing the hardness of these stampings. Alloy stamping parts are commonly used parts in the fields of metal fabrication and machinery manufacturing. Stamping fabrication is a fabrication method that uses a mold to separate or form a metal sheet. Its application range is very broad.
The main purpose of the hardness testing of metal stamping materials is to determine whether the annealing degree of the purchased metal sheet is suitable for the subsequent stamping fabrication. Different types of stamping fabrication techniques require sheets of different hardness levels. The aluminum alloy plate used for stamping parts can be tested with a Webster hardness tester. When the material thickness is greater than 13mm, a Barcol hardness tester can be used instead, and a barcol hardness tester should be used for pure aluminum plates or low-hardness aluminum alloy plates.
In the stamping industry, stamping is sometimes called sheet forming, but it is slightly different. The so-called plate forming refers to the forming method of plastic working with plate, thin-walled pipe, thin profile, etc. as raw materials, which is collectively referred to as plate forming. At this time, the deformation in the direction of the thick plate is generally not considered.
1. Touch inspection
Wipe the surface of the outer cover clean with a clean gauze. The inspector needs to wear touch gloves and touch the surface of the stamping part along the longitudinal direction of the stamping part. This inspection method depends on the experience of the inspector. When necessary, the car sheet metal parts can be polished and verified by grinding the detected suspicious areas, but this method can be regarded as an effective rapid inspection method.
2. Whetstone grinding
1. First wipe the surface of the outer cover with a clean gauze, and then use a whetstone (20×20×100mm or larger) for polishing, and use a relatively small whetstone to polish the places with arcs and hard-to-reach places ( For example: 8×100mm semi-circular whetstone)
2. The choice of whetstone particle size depends on the surface condition (such as roughness, galvanizing, etc.). Fine-grained Whetstone is recommended. The direction of whetstone grinding is basically carried out in the longitudinal direction, and it fits well with the surface of the stamping parts, and some special places can also supplement the horizontal grinding.
3, flexible gauze polishing
Wipe the surface of the outer cover clean with a clean gauze. Use a flexible sand mesh to close to the surface of the stamping part and grind it to the entire surface in the longitudinal direction, and any pitting and indentation will be easily found.
4. Oil inspection
Wipe the surface of the outer cover clean with a clean gauze. Then use a clean brush to apply oil evenly to the entire outer surface of the stamping in the same direction. Put the oiled stamping parts under strong light for inspection. It is recommended to erect the stamping parts on the body position. With this method, tiny pits, slumps, and ripples on stamping parts can be easily found.
5. Visual inspection
Visual inspection is mainly used to find abnormal appearance and macroscopic defects of stamping parts.
6. Inspection tool
Put the stamping parts into the inspection tool, and test the stamping parts according to the operation requirements of the inspection tool manual.
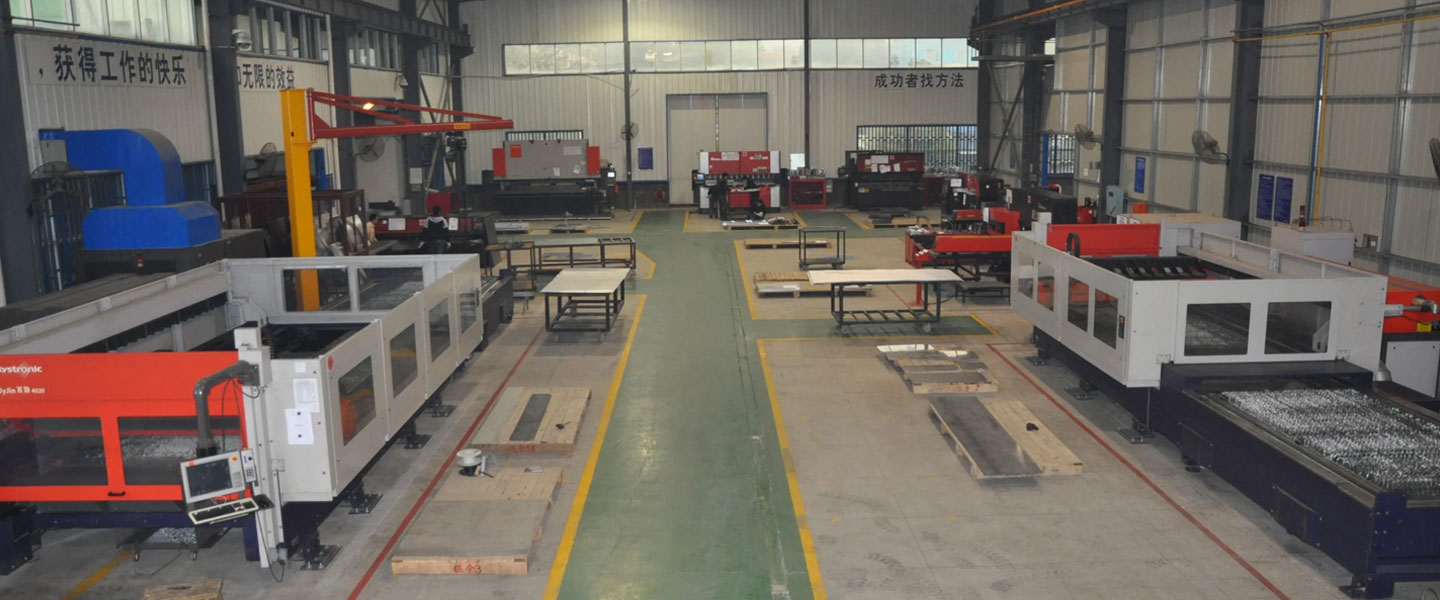
Pintejin Sheet Metal shop offers a cost-effective solution for a wide range of industries with our custom metal stamping and custom sheet metal fabrication capabilities. Our stampnig operations include a variety of sheet-metal forming manufacturing processes, such as punching, blanking, embossing, bending, flanging, and coining. Our professional, experienced and well-trained engineers can execute the complex metal stamping operations with precision and accuracy.
No matter what your metal fabrication needs are, Pintejin can offer the right solution: from single sheet metal part or sub-assembly of stamped metal parts to turnkey solutions for mechanical and electrical assemblies. We have the technology, equipment and the experience to fabricate customised metal products from aluminium sheet metal fabrication, steel, zinc plated steel, stainless steel sheet metal fabrication, brass and copper. Designs that require CNC machining of surfaces or components can be accommodated. We can supply polished, galvanized, zinc coated or powder coated finishes for any sheet metal work or stamped metal components. Coupled with our accurate and reliable metal fabricating equipment, we guarantee precision and repeatability in custom sheet metal work. You’ll be taking advantage of the best sheet metal fabrication china can produce.