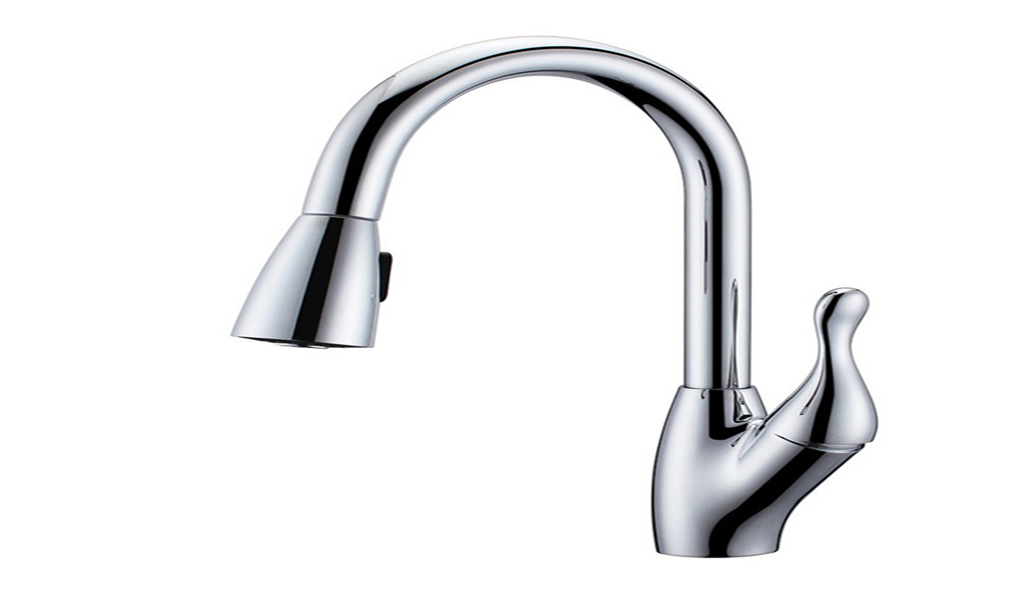
Valuable technical improvements and technical enhancements are concentrated in the automated transportation of automotive stampings, automated transfer devices, as well as in the automatic loading of stamping equipment and product-oriented stamping production processes. The conceptual distinction between traditional stamping and automation is a prerequisite for flexibility in stamping production processes and a product-oriented configuration of stamping equipment. Stamping machines can be differentiated according to the conveying system in the stamping machine, eg by contrasting traditional cam-driven mechanical conveying with advanced swing arm conveying. In the traditional cam-driven stamping equipment, the control cam of the stamping stroke is designed according to the stamping requirements of the workpiece. Regardless of the complexity of the workpiece being punched, the punching machine moves according to the stroke prescribed by the cam, which ultimately results in the same man-hours spent punching a simple workpiece as it would be spent punching a complex workpiece.
For decades, stamping production has been mass production to guarantee stable production conditions. Flexibility was not on the agenda at the time, as it was clearly known that it would still take a considerable amount of time to produce the same product under the same production conditions, so the strategy of permanent use of the mold was adopted. The requirements for stamping production at that time were: the continuity and reliability of the production of deformation fabrication equipment, and flexibility was secondary.
After investigation, it was found that this “old-fashioned” stamping technology can only conditionally and partially meet the requirements of modern product-oriented and flexible stamping production. In order to adapt the stamping production technology to the needs of future development, the stamping production technology and the equipment itself must also be changed. The current situation is that there are not only products that can be processed by old-fashioned stamping machines with high production capacity, but also products that need to be produced by new high-tech stamping production machines with high performance and high production flexibility. , the intertwining of old technologies will continue for some time.
So far, the various topics about the “future stamping plant” are gradually converging, mainly due to the consideration of capital costs, hoping to have high-performance stamping production equipment with better performance than the current one. This kind of stamping production line is not only used in automobile production enterprises today, but also can be seen in some auto parts suppliers. Among them, replacing the products produced by the stamping equipment and increasing the variety of products has become an important factor to measure whether the design and integration capabilities of the stamping equipment are outstanding.
The realization of various stamping processes has its basic motion mechanism. This motion is closely related to the mold. The structural design and mechanical design of various molds are ultimately to meet the requirements of specific motion. Whether the designed die can strictly complete the motion required to realize the stamping process directly affects the quality of the automotive stamping parts, so the mechanical motion should be controlled in the die design. At the same time, in order to meet the requirements of product shape and size, it should not be rigid or limited to the basic movement modes of various processes, but should continue to develop and innovate, and use mechanical movement flexibly in mold design.
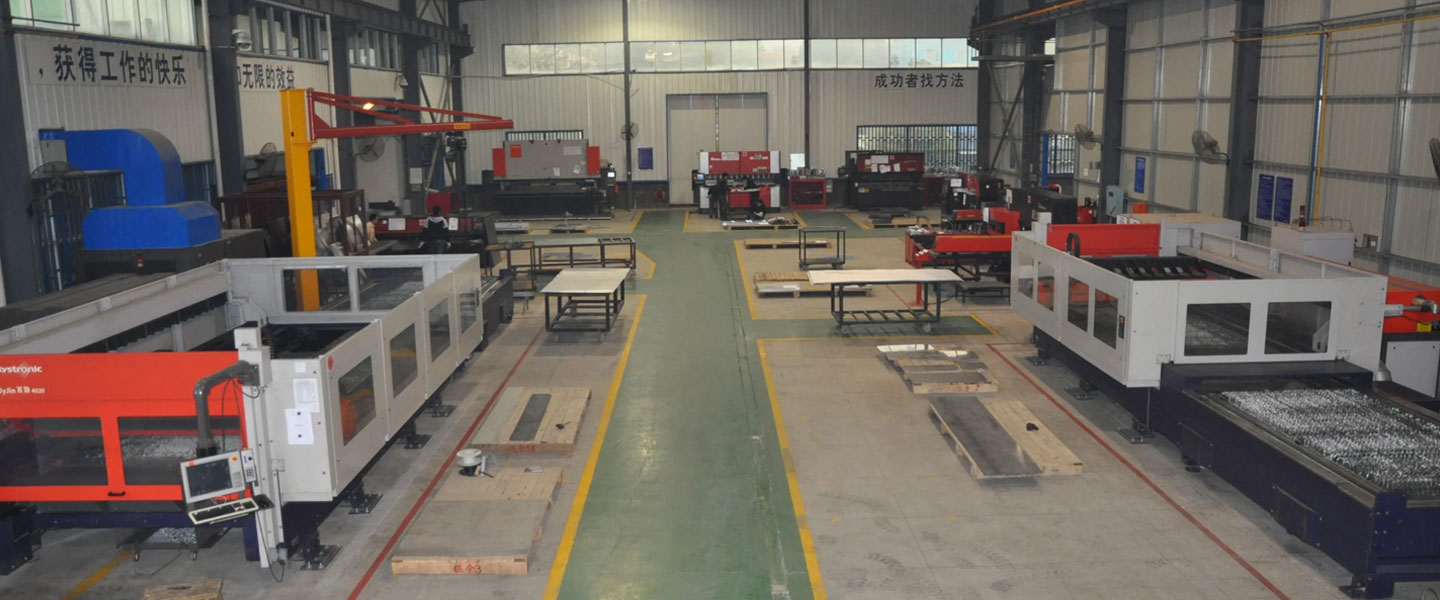
Pintejin Sheet Metal shop offers a cost-effective solution for a wide range of industries with our custom metal stamping and custom sheet metal fabrication capabilities. Our stampnig operations include a variety of sheet-metal forming manufacturing processes, such as punching, blanking, embossing, bending, flanging, and coining. Our professional, experienced and well-trained engineers can execute the complex metal stamping operations with precision and accuracy.
No matter what your metal fabrication needs are, Pintejin can offer the right solution: from single sheet metal part or sub-assembly of stamped metal parts to turnkey solutions for mechanical and electrical assemblies. We have the technology, equipment and the experience to fabricate customised metal products from aluminium sheet metal fabrication, steel, zinc plated steel, stainless steel sheet metal fabrication, brass and copper. Designs that require CNC machining of surfaces or components can be accommodated. We can supply polished, galvanized, zinc coated or powder coated finishes for any sheet metal work or stamped metal components. Coupled with our accurate and reliable metal fabricating equipment, we guarantee precision and repeatability in custom sheet metal work. You’ll be taking advantage of the best sheet metal fabrication china can produce.