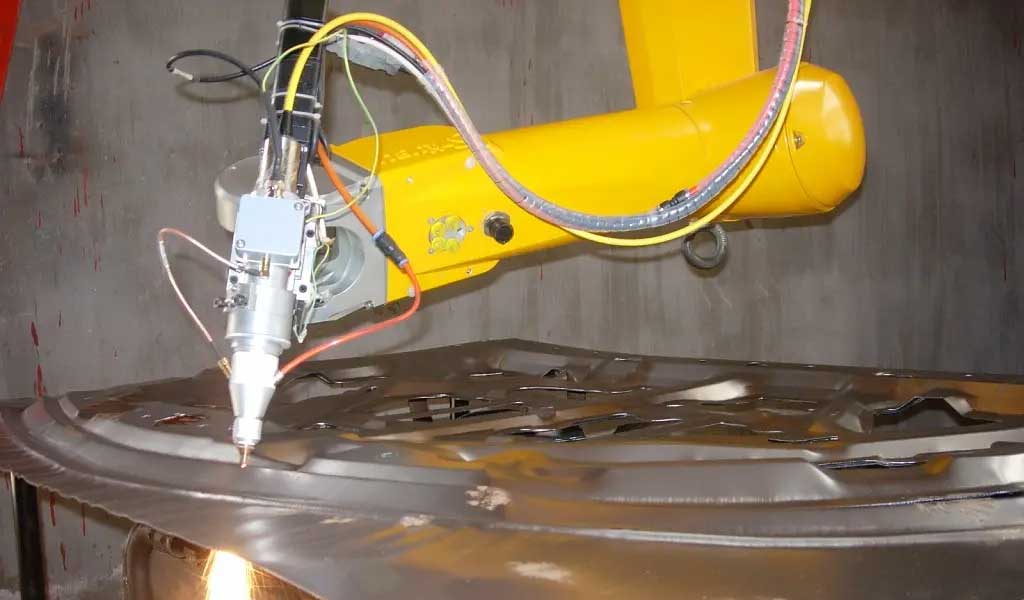
In the manufacture of surgical, orthopaedic, and other medical devices, some traditional machining techniques—some even hundreds of years old—still play a very important role. However, recent advances in laser source and control technology have opened new doors for precision beading, drilling, and thermal processing of medical devices. When combined with other machining processes, designers can find an optimal way to measure a product’s manufacturability. What follows will introduce the reader to how new and old technologies work together to meet the unique needs of medical device manufacturing.
Challenging History
In 1957, Earl Bakken worked with C. Walton Lillehei, a renowned cardiac surgeon at the University of Minnesota, to develop a portable pacemaker using a transistorized metronome. This was the beginning of the global implantable medical device manufacturing industry.
Since then, issues of proper device function, biocompatibility, manufacturability and ultimately cost have followed. How to make implanted prostheses function properly and live in harmony with bodily tissues is always a challenge. With advances in micromachining technology, designs in this area have improved over the past few years. Choosing the right material also makes biocompatibility issues less daunting.
In order to produce highly consistent and reliable life-saving products, production engineers are under tremendous pressure to find ways to design unique solutions to ensure that the entire process is under control, supported by statistical process control (SPC) technology. , and ultimately produce a reliable product. Next is the question of cost. If a product is produced that most of those who need it cannot afford, what is the point of the product for our society?
Unfortunately for Earl Bakken, there were no industrial lasers in his day, and in early design and production, traditional materials and tools were difficult to produce the required components. It wasn’t until CO2 and Nd:YAG lasers were used in materials processing that things started to change rapidly. Before the 1990s, there were mainly two types of lasers used in the development and manufacture of metal medical devices: carbon dioxide and flashlamp-pumped Nd:YAG lasers.
In the mid-1990s, improved Nd:YAG lasers began to be used in critical processes such as material “cold” removal (ablation) and spot welding. Ablation with high technical requirements generally uses excimer laser technology (spot size is generally 25-50 microns, wavelength is generally 0.2-0.4 microns), although expensive, but extremely effective.
Choose The Right Laser
Here’s a look at the four types of lasers used today for material processing (cutting, drilling, and welding) in medical device manufacturing, and how to choose the right laser for that type of processing.
It’s important to remember: the laser is just one component of a laser system that acts like a car’s engine. For production systems that manufacture medical devices based on laser technology. Not only lasers, but also other components such as motion systems, control systems, process sensors and auxiliary components must be considered.
We first briefly discuss the following four types of lasers: CO2, pulsed Nd:YAG, Yb fiber, and ultrashort-pulse lasers, and three common material processing methods in medical device manufacturing: cutting, drilling, and welding.
CO2 laser: CO2 laser is a gas laser with CO2 gas as the working substance. The discharge tube is filled with CO2 gas and other auxiliary gases (mainly helium and nitrogen, and generally a small amount of hydrogen or xenon). This is one of the earliest recorded types of lasers used in manufacturing, with the earliest recorded use in this industry being for its cutting and welding in 1966. Its wavelength is in the far-infrared (IR) band around 10.6 microns.
Nd:YAG Laser: This laser was originally excited by one or more high-intensity xenon lamps to excite Nd-doped Yttrium Aluminum Garnet crystals; later, laser diodes were used to excite. Its wavelength is in the near-infrared band of 1.06 microns. The Nd:YAG lasers in use today are mainly of the pulsed type; CW versions are largely replaced by fiber lasers.
Fiber laser: Doping the fiber with Yb (ytterbium) ions to activate it, using diode excitation. While there are other options, Yb is considered the most cost-effective in high-power applications for material processing. The wavelength of this laser is also in the near-infrared band of 1.07 microns. Fiber lasers are divided into continuous fiber lasers and pulsed fiber lasers according to the output laser characteristics.
Ultrashort-pulse lasers: Generally defined as solid-state pulsed lasers with pulse widths on the order of picoseconds (10-12 seconds) to femtoseconds (10-15 seconds). These lasers usually have a fundamental wavelength. The fundamental frequency is in the near-infrared band at 1.06 microns and can typically be doubled, doubled or tripled to visible or ultraviolet wavelengths. There are many benefits to using shorter wavelengths for processing, such as when a smaller size laser beam is required than can be achieved with the fundamental wavelength. A common feature of this type of laser is the ability to produce a very high quality laser beam, high frequency and extremely short pulses, usually between kHz and MHz.
It is clear from the manufacturer’s reports that both CO2 and Yb fiber laser types are capable of cutting and welding a wide variety of thin and thick materials for general materials used in the manufacture of medical devices. Ultrashort pulse lasers are best used for cutting and drilling thin materials that require little or no heat affected zone (HAZ), or for post-processing of finished parts.
Likewise, while recent advances have turned our attention to high peak power fiber lasers, pulsed Nd:YAG lasers are still the only lasers that can drill high aspect ratio holes. There are many studies looking at the application of this type of laser in drilling. If drilling high aspect ratio holes is now required, the only option is a pulsed Nd:YAG laser. It enables a variety of cutting and edge trimming applications, but at lower speeds than other types of lasers can achieve. It can be used for some autogenous welding, but welding with filler material is beyond the capabilities of standard pulsed Nd:YAG lasers.
Selecting a laser for a combination of cutting and welding is a relatively easy job, but it is much more difficult to select a laser for a combination of drilling and cutting, or a combination of drilling and welding, or even a combination of all three. A little careless, the entire laser system can not give a satisfactory solution to meet the requirements of three processing methods at the same time.
Cut
In laser cutting, the focused laser beam is absorbed by the surface of the workpiece to melt the material. At the same time, a gas coaxial with the laser beam is used to provide mechanical energy (in some cases chemical energy) to remove the material melted by the laser. Lasers can be used to achieve “clean cuts” on many materials, and with the help of some inert gases, such as nitrogen, argon or helium, to ensure that the cut surface is not chemically reacted, relatively free of burrs and debris, thermal effects The zone (HAZ) is also small. The latter depends on the laser parameters, the motion system and the shape of the workpiece. Ultrashort picosecond (ps) and femtosecond (fs) pulsed lasers typically do not require these gases to assist, as material is removed while vaporizing and/or sublimating, sometimes referred to as “cold ablation.” This combination of low energy, short pulse duration and high repetition rate results in very little heat absorbed by the workpiece. The end result is a cut with very small edges and virtually no heat affected zone (HAZ).
Percussion drilling and flight drilling are primarily built on high pulse energies of tens of pulses per second. Each pulse melts and vaporizes a portion of the material while creating a high pressure in the melt chamber (during the evaporation process, the volume of material in the orifice expands dramatically, creating a lot of pressure). This results in the removed molten material forming a molten melt. The size of the melt depends on the specific laser parameters and the chemical composition of the material.
Rotary drilling: The laser beam is focused to a diameter smaller than the desired hole diameter. The material is punched with a small initial hole in the center of the desired hole, and the laser is then moved in several larger and larger circular orbits above the workpiece, expanding the initial hole until a hole of the desired diameter is formed.
Ablation: Stepwise ablation of the material with an ultrashort pulsed laser until a hole is formed. The focal diameter of the laser is generally relatively small, and is related to the required aperture. The laser beam is typically delivered to the workpiece by sophisticated beam steering techniques (raster scanning) at relatively high speeds until the desired shape is formed, either circular or spiral until a circular hole is formed. Material is gradually removed until the desired depth is reached or a hole is formed. No auxiliary gas is required here. The advantage of this method is the high speed, but the low energy of the laser pulse makes the method unsuitable for thin materials or shallow ablation.
Rotary drilling performs well in terms of quality (roundness, taper, heat affected zone) and throughput (number of holes drilled per second). Using fly-drilling and ablation methods, drilling speeds can exceed 100 holes per second. However, the actual speed also depends on the depth, diameter and required mass. In general, high-quality beams—millisecond pulsed Nd:YAG lasers—have proven over extended periods of time to provide a good balance of throughput and precision for drilling holes in medical device component manufacturing. .
Welding
Laser welding can be divided into two categories:
Autologous Laser Welding: Dissimilar materials are fused together without the addition of additional materials. This form of laser welding requires a high level of fixtures, as well as the precision of the kinematics and joint preparation. In the whole welding process, a very critical point is to ensure that the welding material is controlled on the required welding point. Any change in material can result in substandard welds or even failure of the entire weld.
Flux Soldering: Material is added to the weld, usually in the form of wire or powder. When added, the fit requirements at the joint are more flexible, and even an imperfect fit may result in a desired weld. The addition of wire or powder at the joint brings an additional control variable to the overall weld that we need to consider carefully before choosing this method.
Laser welding often requires the use of inert gases to prevent oxidation. Inert gas distribution depends on the material being welded and the configuration of the joint, including simple on-axis or off-axis nozzles used to generate a bolus of inert gas in a specific area to enter a fixture or critical point, a process controlled by a motion system controlled by the controller.
Summary
In any medical device manufacturing application, laser source selection is now easier and more complex (more new options are emerging). Production engineers and management should not rely solely on past experience, old information and conclusions that are at least five years old.
Welding remains one of the largest application markets for lasers in medical device manufacturing. These applications range from cardiac pacemakers and battery assemblies to surgical device assemblies and non-metallic catheter assemblies. As medical device designs change rapidly, laser systems are also following in the footsteps of size reductions, innovations in beam delivery, performance improvements, and increased flexibility, greatly expanding the variety of possibilities in medical device manufacturing. application of processing methods.
Cutting and drilling with a single laser system is often the first choice for many manufacturers today because of its smaller size, customizable design and improved finish quality. This will continue to expand the application of fiber lasers and drive down the price of the lasers themselves.
Designers are always trying to find new solutions when facing challenges, which is an important driving force for new applications to emerge in an endless stream.