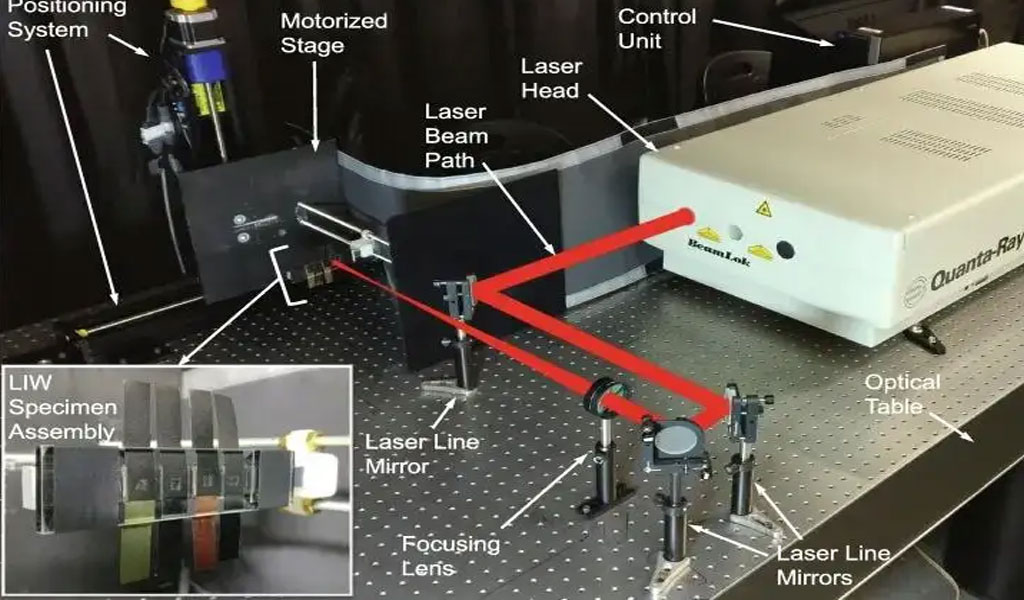
Titanium alloy has the advantages of low density, high specific strength, excellent corrosion resistance and high temperature mechanical properties. In terms of civil aircraft, Boeing and Airbus continue to increase the amount of titanium alloys in the replacement of aircraft. The titanium alloy consumption of Boeing 757 and A320 is 6% and 4.5% respectively, and the titanium alloy consumption of Boeing 777 and A340 is 7% and 7% respectively. 6%, while the titanium alloy content of the new generation Boeing 787 and A380 has reached 15% and 10% [3]. In terms of military aircraft, Su-27, F-16 and F-18 use a large amount of titanium alloys, especially the fourth-generation fighter F-22 titanium alloys use 41% of the total weight of the structure [4].
However, due to the characteristics of titanium alloy itself, the large machining allowance and low material utilization rate (generally less than 10%) of large titanium alloy parts manufactured by traditional “forging + machining” technology have led to the manufacture of titanium alloy parts. High cost and long production cycle [5]. In particular, some titanium alloy structural parts with complex shapes cannot be formed by traditional manufacturing techniques. The above reasons seriously restrict the development and production of aviation equipment in my country.
Laser forming technology is a new manufacturing technology of metal powder melting and direct deposition, which is a combination of high-power laser plating technology and prototyping technology [6]. Melting deposition, directly using the three-dimensional mathematical model of the part to complete the forming and manufacturing of high-performance “near-net forming” complex parts in one step, with outstanding advantages of high material utilization, small machining allowance, short trial production cycle, and high process flexibility, in the field of aerospace applications There is great potential [6-8].
Advances In Laser Forming Technology And Application Of Titanium Alloy Structural Parts For Aviation
The United States first applied laser forming technology to the aviation field. In 1997, AeroMet carried out the application research of laser forming titanium alloy aircraft structural parts with the support of the relevant research programs of the US Air Force, Army and National Defense. In 2000, the ground verification test of laser-formed titanium alloy full-scale aircraft wing structural parts was completed. By 2005, the company’s Ti6Al4V alloy parts manufactured by laser forming had been installed on aircraft such as F/A-18E/F carrier aircraft and F-22 fighter jets, and developed special technical standards (AMS 4999) [ 9-10].
The successful application of US laser forming technology in the aviation industry has greatly promoted the research boom in this field in my country [10-13]. Such as Northwestern Polytechnical University, AVIC Beijing Institute of Aeronautical Manufacturing Engineering, Beihang University, Beijing Nonferrous Metal Research Institute and other units actively carry out research work on laser forming technology, CNC machining titanium and parts manufacturing, and have achieved rapid development.
1TA15 Alloy
TA15 alloy has good comprehensive mechanical properties and process properties such as forging, welding, heat treatment, etc., and has a wide range of applications in aircraft load-bearing structures [14]. It is one of the earliest titanium alloys used in laser forming technology in my country [15-19 ]. As early as 2005, Beihang used “plane contact/dynamic sealing/inert atmosphere protection” laser forming equipment to form TA15 alloy parts with excellent mechanical properties, and made a comprehensive comparison with the TA15 alloy sheets in the hot-rolled and annealed state. It can be seen from Table 1 that the tensile properties of the laser-formed TA15 alloy and the hot-rolled annealed TA15 sheet are comparable at room temperature, but the elongation is lower at a high temperature of 500 °C. It is worth noting that the high temperature durability of the laser formed TA15 alloy under the condition of 500℃/471MPa is very excellent, which is more than twice that of the hot rolled annealed TA15 sheet. In terms of fatigue properties, related studies suggest that laser-formed TA15 alloys are slightly lower than forgings and hot-rolled thick plates. At present, the TA15 alloy non-load-bearing structural parts manufactured by Beihang University using laser forming technology have been installed and tested [16].
2TC4 Alloy
TC4 alloy has excellent comprehensive properties and is mainly used in the aviation industry to manufacture fans, compressor discs and blades of engines, as well as important load-bearing components such as beams, joints and bulkheads in aircraft structures [20]. At present, there are many reports on laser forming of TC4 alloys [21-26]. The research group of Xigong Dahuang Weidong found that the plasticity of the formed parts is extremely sensitive to the oxygen content. With the increase of the oxygen content, the elongation drops sharply. When the mass fraction of oxygen exceeds 0.4%, the titanium alloy will lose its engineering application value due to poor plasticity. . Therefore, atmosphere protection is required during the forming process of TC4 alloy to ensure that the mass fraction of oxygen in the formed parts is controlled within the range of 0.08% to 0.4% [21-22]. The tensile strength of the TC4 alloy prepared by the research group is as high as 1200MPa, and the elongation rate is 5%. Through solution aging treatment, excellent comprehensive properties can be obtained. The tensile strength is 1040MPa, the elongation rate is 13%, and the section shrinkage rate is as high as 41%. . The basic mechanical properties fully meet the requirements of the American titanium alloy forging standard ASTM B381-05 [13]. Gao Shiyou of Beijing Institute of Nonferrous Metals successfully prepared TC4 alloy with excellent performance by laser forming technology under the condition of airtight argon protective atmosphere. The mechanical properties are better than TC4 castings and close to TC4 forgings [23]. Table 2 compares the mechanical properties of the laser-formed TC4 alloy with those specified in the American Ti6Al4V laser block forming specification AMS 4999A and the titanium alloy forging standard ASTM B381. It can be seen that the basic mechanical properties of my country’s TC4 alloy laser forming parts generally meet the requirements of the American aerospace material specification AMS 4999A. Figure 2 is a photo of TC4 alloy beam parts.
3TC21 Alloy
TC21 titanium alloy integrates high strength, high toughness, and damage tolerance, and has great application prospects in the manufacture of high-performance aviation and aerospace vehicle structural parts. At present, there are relatively few reports on laser forming of TC21 alloy, and it is limited to the study of the properties of the alloy itself. The TC21 alloy was prepared by the TC21 spherical powder prepared by the plasma rotating electrode method by the research group of Xigong Dahuang Weidong. The basic performance data are shown in Table 3. The tensile strength and yield strength of laser-formed TC21 alloy are as high as 1265MPa and 1175MPa, which exceed the design value requirements and are even better than forgings, but their plasticity is poor, and the elongation is only about 5% [27]. By analyzing the microstructure of the laser-formed TC21 alloy, it was found that except for the acicular martensite on the surface, the interior was similar to the forged TC21 alloy’s basket structure, which was more uniform and finer than the forged structure [28].
At present, the research on the mechanical properties of laser-formed titanium alloys mainly focuses on the static strength index. From the above data, the tensile properties and plasticity of laser-formed titanium alloys have been significantly close to or even better than forgings. However, modern aircraft structures, especially titanium alloys for main load-bearing structures, must comply with the requirements of fatigue resistance, durability and damage tolerance while satisfying static strength and stiffness. Therefore, if the titanium alloy laser forming technology is to be applied to the aircraft load-bearing structure, its comprehensive performance must be fully researched and assessed.
Problems Existing In Titanium Alloy Laser Forming Technology
The process of laser forming a single multi-layer cladding layer is shown in Figure 3, in which the height of the molten pool and the new cladding layer is H, the height of the remelting zone is h, and the Z-axis rise increment of the CNC table is ΔZ. During the laser forming process, the material is melted, solidified and cooled under extremely fast conditions, so metallurgical defects are easily generated inside the part. After the research on laser forming technology at home and abroad, the defects that have been found are mainly cracks (see Fig. 4), pores (see Fig. 5) and lack of fusion (see Fig. 6), etc. [29-31].
1 Deformation and cracking
Because laser forming is a fast cooling process, cracking is easy to occur during the forming process, or residual stress and deformation are formed in the formed parts, which seriously affects the geometric dimensions and mechanical properties of the parts. Therefore, it is necessary to prevent the cracking behavior during the forming process and strictly control the residual stress and deformation of the formed parts. However, there are few reports at home and abroad on effectively solving the problems of deformation and cracking.
1.1 Residual stress
The period of damage caused by residual stress is often long, and it is easy to cause deformation and cracking of the parts in combination with the service environment of the parts (such as temperature and medium). If the balance state of residual stress is destroyed under the action of external factors or aging, the rigidity and dimensional stability of the part will decrease and secondary deformation will occur; the combined action of residual stress and external load will increase the working stress of the part, which will cause the part to be loaded Instability and premature fracture; the combined effect of thermal stress and residual stress in high temperature environment will cause thermal cracking; in corrosive medium, the existence of residual tensile stress will cause stress corrosion cracking, leading to parts damage and reducing the service life of formed parts.
1.2 Cracks
The problem associated with stress is crack. Crack is the most common and destructive defect in the forming process. Once a crack occurs during the forming process, the part can only be scrapped. Therefore, controlling crack generation during laser forming is a key issue. Northwestern Polytechnical University believes that cracks are prone to occur when the line energy and powder feeding amount are large, and the occurrence of cracks can be prevented and eliminated by strictly controlling the forming process parameters [32-34].
Internal Defects
2.1 Stomata
Due to the adsorption of powder or the gas encapsulated by the hollow powder, it fails to escape in time during the solidification process of the molten pool, and remains in the solidified structure to form pores. Stomatal defects are generally smooth in inner wall, mostly spherical or nearly spherical, and the center is mostly bright white under the optical microscope, as shown in Figure 5, all of which are distributed in laser forming parts, and most of them are distributed inside the grain. Zhang Fengying et al. believed that the quality of titanium alloy powder is the main reason for the formation of pore defects through the research on the formation of defects in the process of laser forming of titanium alloys [30]. In order to reduce or eliminate pores, the milling process should be strictly controlled. The titanium alloy powder used should have a regular shape, smooth surface, avoid internal looseness, and the particle size of the powder should also meet the requirements [30-31].
2.2 Unfused
The lack of fusion refers to the poor fusion defect caused by the lack of dense metallurgy between the cladding layers due to improper control of process parameters during the laser forming process. The inner walls of the holes caused by unfusion are rough, and the morphology is mostly irregular, and most of them are distributed in the lap joints between layers or tracks, as shown in Figure 6. When the overlap ratio is too small, irregular-shaped fusion is likely to occur between adjacent cladding tracks; when ΔZ is too large, poor fusion is likely to occur between the cladding layers [30]. Therefore, in order to eliminate non-fusion defects, the energy density, overlap ratio and Z-axis single-row layer stroke ΔZ should be reasonably controlled to achieve a good match of each process parameter [31].
A large number of found pores and unfused defects are below 50μm in size. Common inspection methods such as ultrasonic flaw detection or X-ray generally have a maximum sensitivity of 0.1mm, and cannot detect pores and unfused defects below 0.1mm. Studies have shown that these undetectable defects are one of the main factors that reduce the fatigue life of laser-formed parts, especially unfused defects below 50 μm will be the fatal source of fatigue initiation of load-bearing structural parts. This is bound to be one of the hidden dangers affecting the reliability of laser forming parts [20].
Therefore, the control of internal defects such as pores and lack of fusion is the key to the widespread application of titanium alloy laser forming technology. At present, the powder metallurgy and casting technology of aerospace titanium alloys at home and abroad generally combine the hot isostatic pressing technology to eliminate defects such as shrinkage porosity, shrinkage cavities and pores, so as to improve the internal quality [35-38]. Li Huaixue of AVIC Beijing Institute of Aeronautical Manufacturing Engineering formed TB6 titanium alloy through laser forming combined with hot isostatic pressing technology, and concluded that hot isostatic pressing can greatly reduce the pore defects of laser formed titanium alloy, but it is difficult to eliminate unfused Defects, and the plasticity of the TB6 titanium alloy prepared by adjusting the forming parameters to eliminate the unfusion improved nearly 1 times [39]. AeroMet Company of the United States also processes laser formed parts by hot isostatic pressing or forging to achieve the purpose of reducing internal defects. However, at present, the laser forming Ti6Al4V alloy has not yet achieved a breakthrough, and the fatigue performance is significantly lower than that of the forgings. It can be seen that the fatigue life of the workpiece after laser forming + hot isostatic pressing or forging treatment is comparable to the highest level of casting or the lowest level of forging, but is significantly lower than the highest level of forging.
Concluding Remarks
Laser forming technology does not require special molds. It can directly use titanium alloy powder to form parts of any complex shape according to the three-dimensional digital model of the part. It is especially suitable for the manufacture of rapid prototyping parts and the manufacture of special structural parts with particularly complex shapes. It has a good application in the aviation field. prospect. At present, my country has made significant progress in the research of key technologies such as forming equipment, manufacturing technology, process control, and process stability in this field. The key technologies such as deformation and crack prevention, internal quality inspection and control, and comprehensive mechanical property control of formed parts have put forward very high requirements. For the main load-bearing structural parts, the research and assessment of comprehensive performance such as fatigue resistance, durability, and damage tolerance performance must be carried out. deformation cracking problem.
The author suggests that, in view of the development status of titanium alloy laser forming technology in my country’s aviation field, this technology is more suitable for rapid prototyping parts manufacturing and high-value material parts manufacturing during prototype trial production. In terms of production efficiency, it cannot be compared with die forgings in the short term. Therefore, laser forming technology should first focus on the manufacture of complex non-main load-bearing structural parts and special functional structural parts that are difficult to be formed by conventional processes. Structural designers should strengthen their understanding of the characteristics of laser forming equipment, expand design ideas according to the characteristics of the technology, construct more diverse structural forms, give full play to the advantages and functions of titanium alloy laser forming technology, and develop higher performance and lighter weight. aircraft structure.
In addition, high-quality titanium alloy powder is the key to obtaining high-quality laser forming structural parts. Therefore, it is also necessary to strengthen the research on high-quality laser forming titanium alloy powder to solve the problem of domestic independent guarantee of high-quality titanium alloy powder.
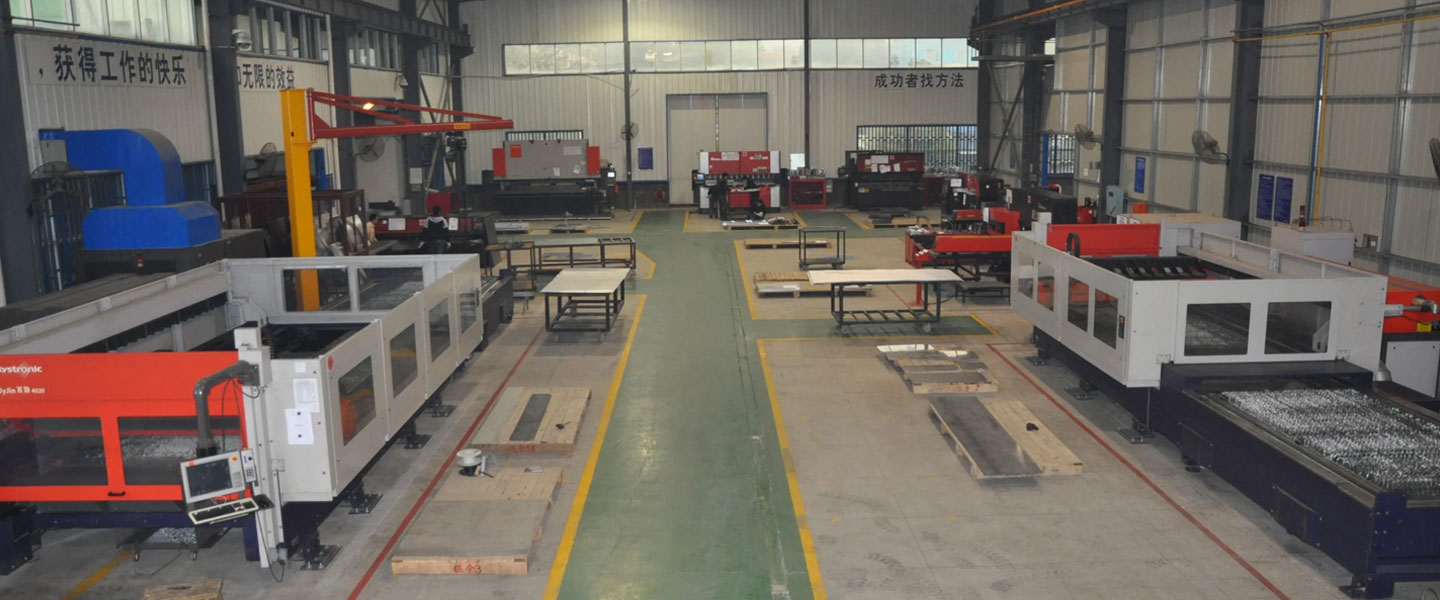
Pintejin Sheet Metal shop offers a cost-effective solution for a wide range of industries with our custom metal stamping and custom sheet metal fabrication capabilities. Our stampnig operations include a variety of sheet-metal forming manufacturing processes, such as punching, blanking, embossing, bending, flanging, and coining. Our professional, experienced and well-trained engineers can execute the complex metal stamping operations with precision and accuracy.
No matter what your metal fabrication needs are, Pintejin can offer the right solution: from single sheet metal part or sub-assembly of stamped metal parts to turnkey solutions for mechanical and electrical assemblies. We have the technology, equipment and the experience to fabricate customised metal products from aluminium sheet metal fabrication, steel, zinc plated steel, stainless steel sheet metal fabrication, brass and copper. Designs that require CNC machining of surfaces or components can be accommodated. We can supply polished, galvanized, zinc coated or powder coated finishes for any sheet metal work or stamped metal components. Coupled with our accurate and reliable metal fabricating equipment, we guarantee precision and repeatability in custom sheet metal work. You’ll be taking advantage of the best sheet metal fabrication china can produce.