
Stamping is classified according to the process and can be divided into two categories: separation process and forming process. The separation process is also called blanking, and its purpose is to separate the stamping parts from the sheet along a certain contour line, while ensuring the quality requirements of the separation section.
Stamping is an efficient production method. The use of composite molds, especially multi-station progressive molds, can complete multiple stamping processes on one press, and realize the complete process from strip uncoiling, leveling, punching to forming and finishing. Automatic production. The production efficiency is high, the labor conditions are good, and the production cost is low. Generally, hundreds of pieces can be produced per minute. The purpose of the forming process is to plastically deform the sheet without breaking the blank to make a workpiece of the desired shape and size. In actual production, multiple processes are often integrated into a workpiece. Blanking, bending, shearing, deep drawing, bulging, spinning, and straightening are several major stamping jobs.
Castings are metal forming objects obtained by various casting methods, that is, the smelted liquid metal is poured into the pre-prepared casting mold by pouring, injection, suction or other casting methods, and after cooling, it is subjected to falling sand, cleaning and post-fabrication. Processing, etc., the resulting objects of certain shape, size and properties
The difference between metal automobile stamping parts and castings: with the characteristics of thin, uniform, light and strong, stamping can produce workpieces with ribs, ribs, undulations or flanging that are difficult to manufacture by other methods to improve their rigidity. Due to the use of precision molds, the accuracy of the workpiece can reach micron level, and the repeatability is high and the specifications are consistent, and holes, bosses, etc. can be punched out.
The hardness test of metal stamping parts adopts Rockwell hardness tester. Small, complex-shaped stampings can be used to test small planes that cannot be tested on ordinary benchtop Rockwell hardness testers.
The properties of the casting itself directly affect the quality of the fabrication, and the hardness value is an important indicator to determine the fabrication of the casting.
- 1. Brinell hardness: It is mainly used to measure the hardness of castings, forgings, non-ferrous metal parts, hot-rolled billets and annealed parts. The measurement range is ≯HB450.
- 2. Rockwell hardness: HRA is mainly used for high-hardness test pieces to measure the hardness of materials and surfaces with hardness higher than HRC67, such as cemented carbide, nitrided steel, etc., with a measurement range of HRA>70. HRC is mainly used for hardness measurement after quenching or tempering of steel parts (such as carbon steel, tool steel, alloy steel, etc.), the measurement range is HRC20~67.
- 3. Vickers hardness: used to measure the hardness of thin parts and steel plate parts, and can also be used to measure the hardness of surface hardened parts such as carburizing, cyanidation, and nitriding.
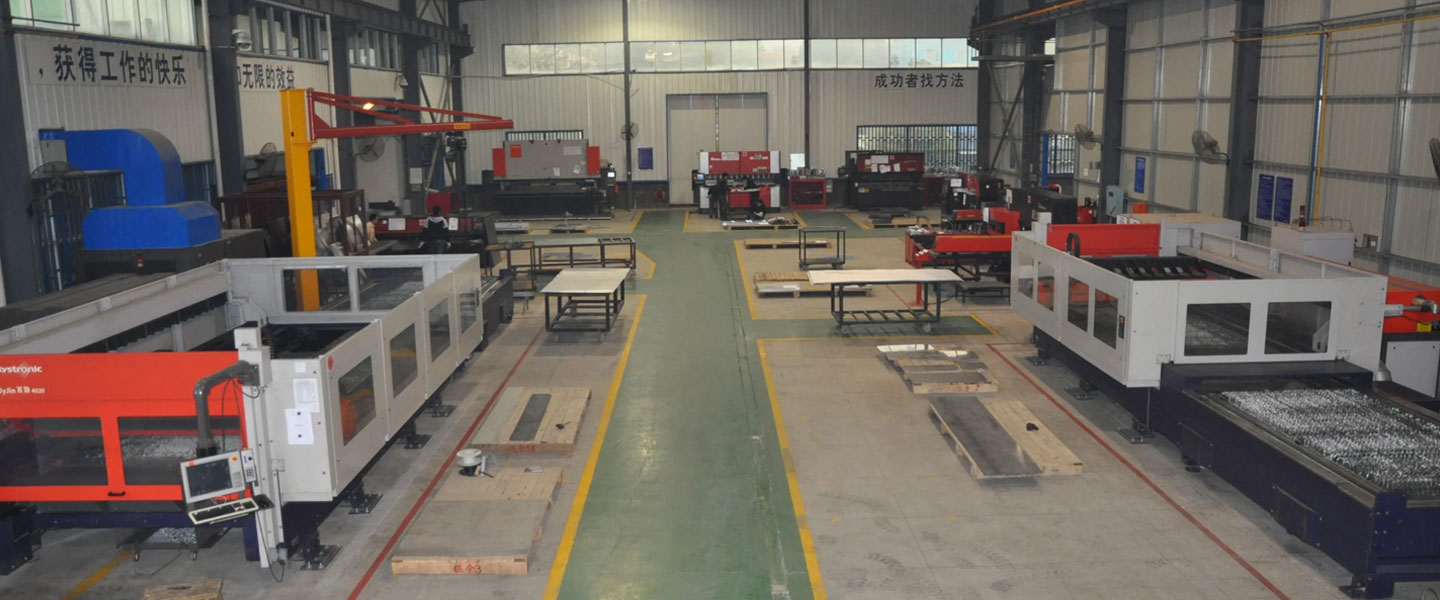
Pintejin Sheet Metal shop offers a cost-effective solution for a wide range of industries with our custom metal stamping and custom sheet metal fabrication capabilities. Our stampnig operations include a variety of sheet-metal forming manufacturing processes, such as punching, blanking, embossing, bending, flanging, and coining. Our professional, experienced and well-trained engineers can execute the complex metal stamping operations with precision and accuracy.
No matter what your metal fabrication needs are, Pintejin can offer the right solution: from single sheet metal part or sub-assembly of stamped metal parts to turnkey solutions for mechanical and electrical assemblies. We have the technology, equipment and the experience to fabricate customised metal products from aluminium sheet metal fabrication, steel, zinc plated steel, stainless steel sheet metal fabrication, brass and copper. Designs that require CNC machining of surfaces or components can be accommodated. We can supply polished, galvanized, zinc coated or powder coated finishes for any sheet metal work or stamped metal components. Coupled with our accurate and reliable metal fabricating equipment, we guarantee precision and repeatability in custom sheet metal work. You’ll be taking advantage of the best sheet metal fabrication china can produce.