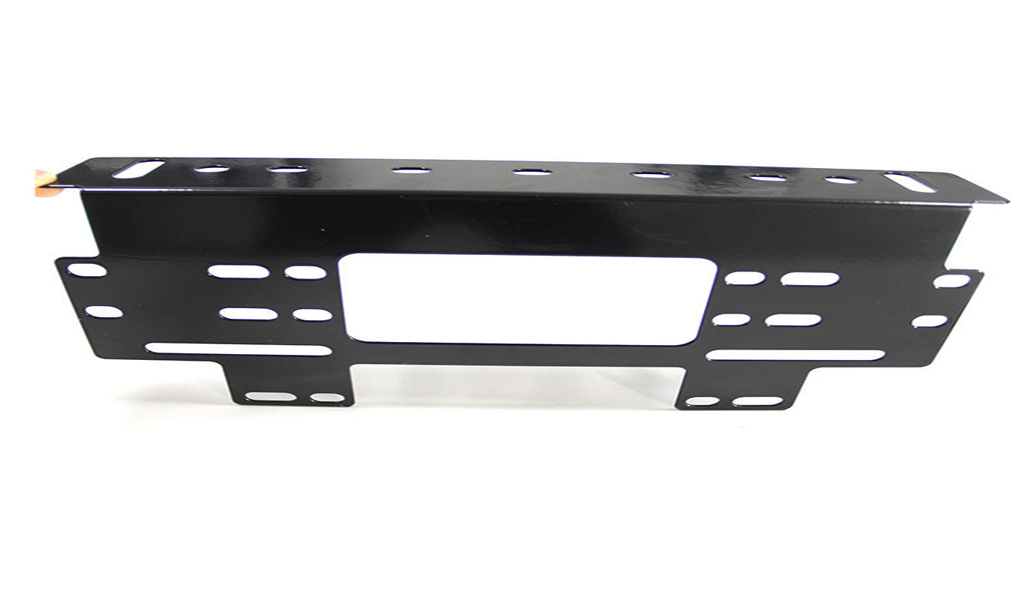
When the stamping die is trimmed, there is generally a phenomenon of iron filings falling off, especially around the lower die scrap knife. The iron filings not only seriously affect the product quality and the cleanliness of the mold appearance, but also reduce the production efficiency.
Automobile stamping parts manufacturers analyze that this is not perpendicular to the trimming edge, the workpiece does not conform to the mold surface, the secondary shearing of the vertical edge trimming, the unreasonable edge clearance, the poor edge finish, and the secondary cutting of scrap knives. Cutting, insufficient cutting edge hardness, too deep cutting edge penetration, unreasonable mold process design, etc.
In order to prevent this phenomenon from happening, we can take the following measures to control it.
1. Iron filings are generated at the scrap knife part
The production of iron filings at the scrap knife is mainly caused by the mold process. The measures to be taken are: change the shape 10mm before the edge of the upper die trimming waste to make a breakthrough edge shape, and mill the lower die waste edge to empty. (Introduction: The classification of casting molds is very different)
2. The plate does not conform to the shape and the cutting edge clearance is unreasonable
The measures to be taken when the plate does not conform to the shape and the cutting edge clearance is unreasonable is to use the OP10 drawing plate buckle to repair the profile of each part of the edge mold, and at the same time, the upper and lower cutting edge clearances are adjusted and the penetration depth is adjusted.
3. Edge trimming
When trimming the vertical edge, in order to improve the quality of the section and the life of the cutting edge, the following three measures can be adopted:
- 1) The fillet of the upper edge of the trimming should be 3mm larger than the fillet of the trimmed part, so as to ensure that when the upper and lower molds are completely closed, the edge of the trimming will be cut into 1-3mm, and the transition will be slow.
- 2) The vertical edge of the trimming edge of the upper die and the vertical edge of the trimming piece are at an angle of 10°.
- 3) Install the guide block as much as possible to eliminate the lateral force on the cutting edge.
4. Mold process design
- 1) Use two or more trimmings. The advantages of adopting this measure are that burrs and trimming iron filings will not be produced under the condition of reasonable cutting edge clearance, which facilitates the removal of waste materials, and the quality of the parts is stable and the production efficiency is high.
- 2) Trimming the whole side as a whole. The advantages of adopting this measure are that burrs and trimming iron filings will not be produced under the condition of reasonable cutting edge clearance, which facilitates the removal of waste materials, and the quality of the parts is stable and the production efficiency is high.
- 3) Trimming of the separation area in the middle of the double piece. Originally, in the production process, through the cooperation of the upper die pressing material core and the lower die punch, the plate is pressed, and the upper and lower die waste cutting edges cooperate to cut the waste to realize the separation of waste. The change to the middle scrap is to achieve the final separation of the scrap through the forced breakthrough and cutting of the upper die breaking knife and the cooperating and cutting of the trimming edges of the convex and concave dies on both sides. In this way, the lower die waste has a large space for chip removal, and the waste is easy to discharge.
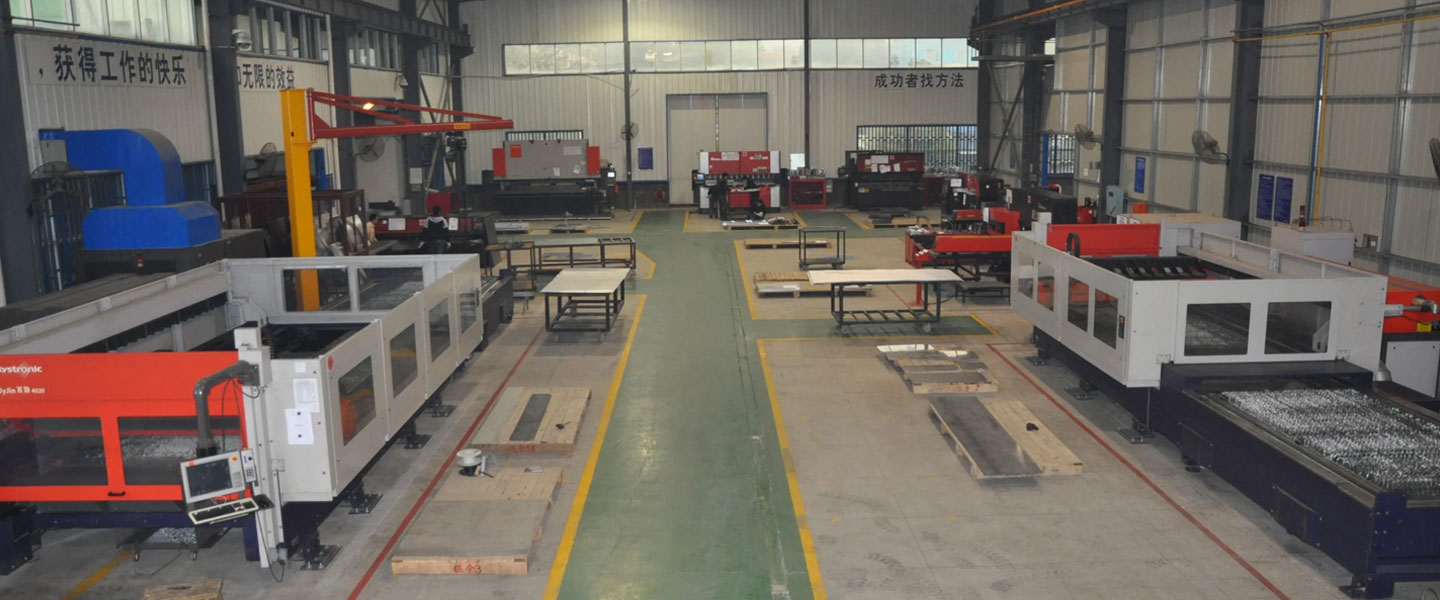
Pintejin Sheet Metal shop offers a cost-effective solution for a wide range of industries with our custom metal stamping and custom sheet metal fabrication capabilities. Our stampnig operations include a variety of sheet-metal forming manufacturing processes, such as punching, blanking, embossing, bending, flanging, and coining. Our professional, experienced and well-trained engineers can execute the complex metal stamping operations with precision and accuracy.
No matter what your metal fabrication needs are, Pintejin can offer the right solution: from single sheet metal part or sub-assembly of stamped metal parts to turnkey solutions for mechanical and electrical assemblies. We have the technology, equipment and the experience to fabricate customised metal products from aluminium sheet metal fabrication, steel, zinc plated steel, stainless steel sheet metal fabrication, brass and copper. Designs that require CNC machining of surfaces or components can be accommodated. We can supply polished, galvanized, zinc coated or powder coated finishes for any sheet metal work or stamped metal components. Coupled with our accurate and reliable metal fabricating equipment, we guarantee precision and repeatability in custom sheet metal work. You’ll be taking advantage of the best sheet metal fabrication china can produce.