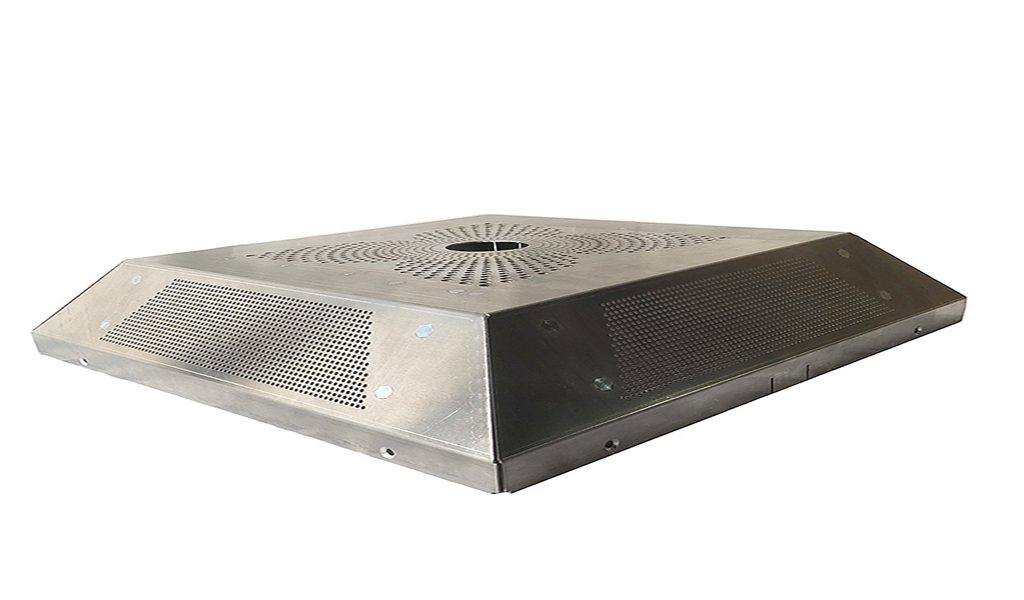
Stamping die is a necessary process equipment in the stamping production process, which plays a decisive role in improving the quality of products and improving production efficiency. The durability of the stamping die is determined by the total number of parts punched by the punch when the punch and the die lose their working scale due to frequent wear and tear after a period of operation, and can no longer meet the technical conditions of the parts. From design, machining, installation, adjustment to installation and application of a pair of stamping die, there are many processes, long cycle and high fabrication cost. Therefore, in addition to the requirement of high production efficiency and the punched parts fully meet the quality requirements and technical conditions for the stamping die, The durability of the stamping die itself is also very important.
Therefore, in order to prolong the service life of the stamping die, it is necessary to improve the durability of the stamping die. The following points should be paid attention to in ordinary stamping operations:
1. Improve the planning of fine stamping dies
Whether the stamping die design is reasonable is the basis for improving the durability of the stamping die. Therefore, when designing the stamping die, effective measures should be taken to deal with the unfavorable conditions in the product forming to improve the durability of the stamping die. For example, the life of the small-hole punching die is often reflected in the punch for punching the small hole. For this type of stamping die, the length of the small punch should be shortened as much as possible during planning to increase the strength. At the same time, the guide sleeve should be used to strengthen the protection of the small punch. In addition, in the design of stamping die, factors such as the mode of the mold base, the fixing method and guiding method of the convex and concave mold, the determination of the pressure center and the rigidity of the upper and lower mold plates should be fully considered. Especially for the blanking die, the selection of the void value has a great influence on the durability. When planning, the gap of the stamping die should be selected reasonably, and the gap value should not be too small, otherwise it will affect the service life and durability of the stamping die. Practice has proved that without affecting the quality of stamping parts, properly expanding the gap can greatly improve the durability of stamping dies, sometimes even several times and dozens of times.
2. Correct selection of die material
Different die materials have different strength, resistance and wear resistance. The use of advanced materials under certain conditions can improve the durability several times. For example, the watt-hour meter magnetic pole punching die made of T10A steel has a much lower one-time sharpening life than the similar punching die made of Cr12 and Cr12 MoV. The average grinding life of G35 titanium carbide steel hard alloy is 5-10 times higher than that of Cr12 steel die. 20-30 times improvement. Therefore, in order to improve the durability of the die, it is necessary to select a good material.
3. Reasonable forging and heat treatment of die parts
While selecting high-quality die materials, reasonable forging and heat treatment are required for materials with the same raw materials and different properties, which is one of the primary ways to improve the durability of the die. For example, during quenching, if the product is overheated during heating, it will not only make the workpiece too brittle, but also easily cause deformation and cracking during cooling, reducing durability. Therefore, when making a die, it is necessary to reasonably grasp the heat treatment process.
4. Reasonably arrange the die making process and ensure the machining accuracy
The machining accuracy of the die has a great influence on the durability of the die. For example, due to the uneven installation gap in the blanking die, under the action of shear force, the die will often be damaged and the life of the die will be affected. At the same time, the surface finish of the die is too low, which will also reduce the durability of the die. Therefore, it is necessary to pay full attention to the size of the hole spacing, the verticality of the support surface of the punch to the fixed plate during installation, the uniformity of the die distance, and the guide accuracy level of the guide sleeve and guide post. The higher the production and installation accuracy and the higher the surface roughness of the working part, the higher the durability of the die.
5. Correct selection of presses
In order to improve the durability of the stamping die, a press with higher precision and higher rigidity should be selected, and its stamping tonnage should be more than 30% greater than the stamping force. Generally speaking, the use of servo punch can correspondingly improve the life of the mold by dozens of times.
6. Reasonable use and maintenance of fine stamping dies
In order to improve the durability of the stamping die, the operator must use and maintain the stamping die reasonably, and the stamping die should be frequently repaired to avoid the stamping die from being sick.
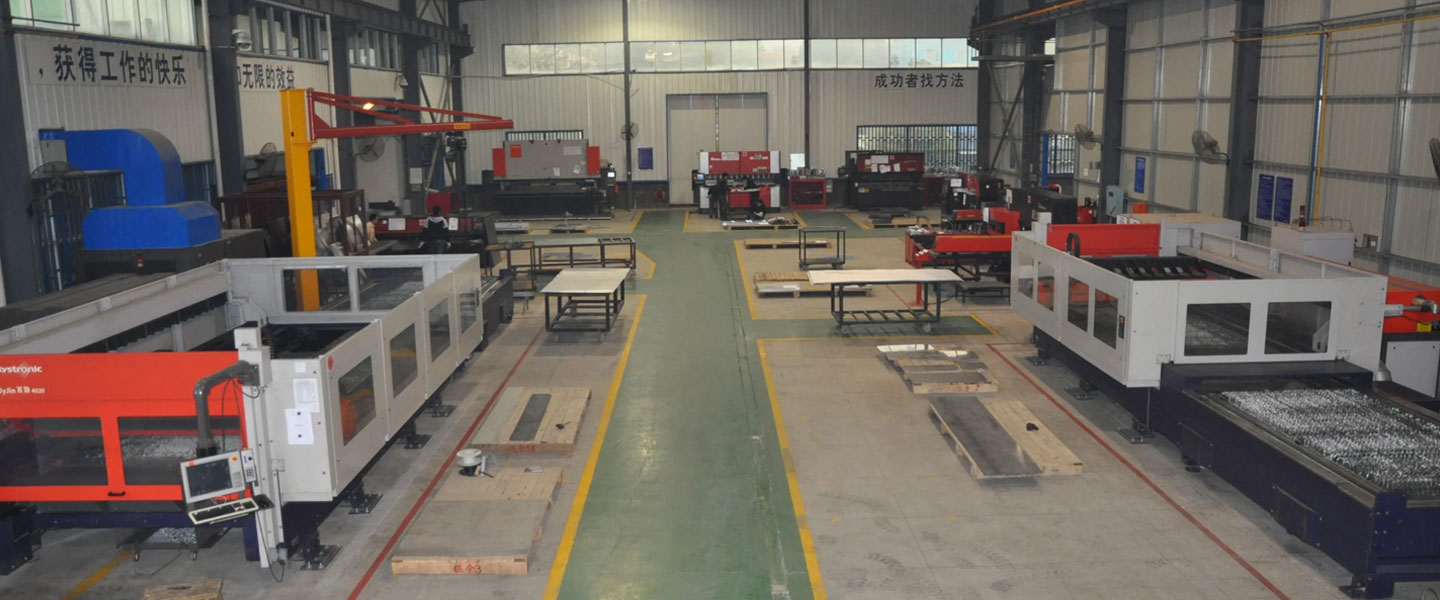
Pintejin Sheet Metal shop offers a cost-effective solution for a wide range of industries with our custom metal stamping and custom sheet metal fabrication capabilities. Our stampnig operations include a variety of sheet-metal forming manufacturing processes, such as punching, blanking, embossing, bending, flanging, and coining. Our professional, experienced and well-trained engineers can execute the complex metal stamping operations with precision and accuracy.
No matter what your metal fabrication needs are, Pintejin can offer the right solution: from single sheet metal part or sub-assembly of stamped metal parts to turnkey solutions for mechanical and electrical assemblies. We have the technology, equipment and the experience to fabricate customised metal products from aluminium sheet metal fabrication, steel, zinc plated steel, stainless steel sheet metal fabrication, brass and copper. Designs that require CNC machining of surfaces or components can be accommodated. We can supply polished, galvanized, zinc coated or powder coated finishes for any sheet metal work or stamped metal components. Coupled with our accurate and reliable metal fabricating equipment, we guarantee precision and repeatability in custom sheet metal work. You’ll be taking advantage of the best sheet metal fabrication china can produce.