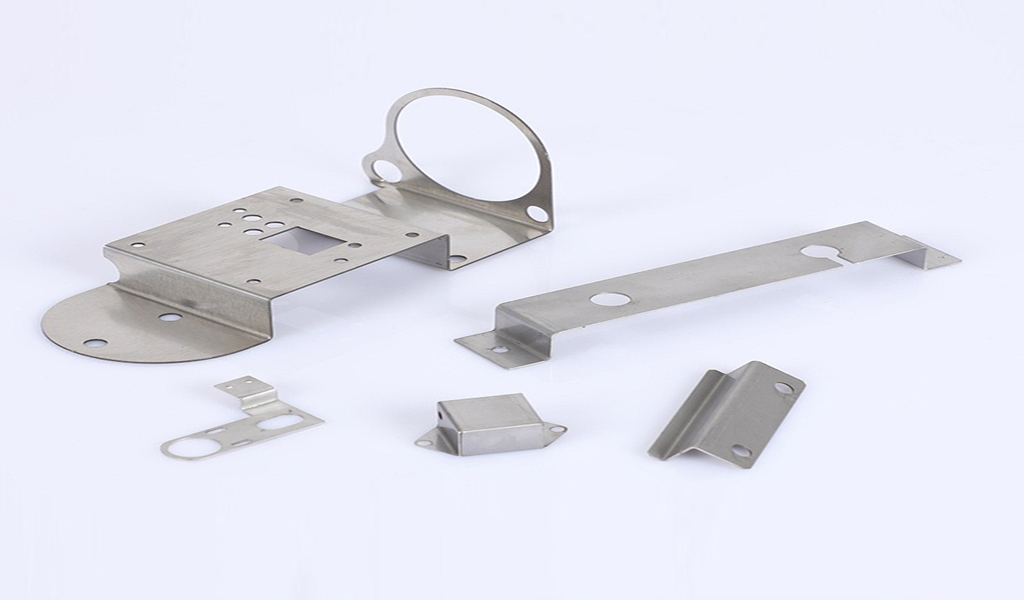
At present, when making automobile stamping parts, most of them are made by cold stamping, and when making stamping parts, the material of stamping die must be debugged before it can be used in production. After years of research, engineers have formulated strict requirements for the debugging of cold stamping dies, so that after these detailed debugging, these cold stamping dies can exert more energy in the process of making stamping parts.
However, it is said that cold stamping dies have to go through some step-by-step processes before producing stamping parts for automobiles. Generally, in the debugging, the first step must be to determine whether these cold punches can be used on the punching machine. Assuming that it can be installed on the punching machine for use, it means that there is no problem in the general structure of the cold punching die, and the next step of debugging can be carried out.
After judging that the cold stamping die can be used on the stamping machine, the next thing that needs to be determined is whether the specified blank can be processed into the specified stamping part in this cold stamping die through this cold stamping die. Generally, in this step of debugging, it is necessary to use these blanks to process stamping parts, because in the debugging, the basis for judging the matching of this blank with the cold die can not be confirmed after one debugging. In this step of debugging, it is necessary to pass a certain number of operations to produce stamping parts, and through the effect of a certain amount of data calculation, it can be determined that the blank and the cold stamping die are completely consistent after all.
Now that the first two operations are completed, we need to check whether the stamping parts produced by these cold stamping dies meet the requirements in the production of car stamping parts. Generally, in the process of checking whether these stamping parts meet the requirements, we not only need to compare the design drawings of the stamping parts with the manufactured products, because the assembly of the car is a complicated process. In the assembly process, if any part of the stamping If the parts are not made in accordance with the stakes, it may cause the car to not be produced and put into use smoothly after all. When checking whether these produced stamping parts meet the requirements, if it is found that these processed stamping parts do not meet the requirements, the reasons should be found from the aspects of fabrication technology and cold stamping, after all, this type of stamping parts can match the design of the drawings. are common to ensure that the car can travel safely.
After judging that the stamping parts produced by the cold die meet the requirements of the drawings, we also need to check the standards and sizes of these stamping parts in the next debugging. In case of non-compliance, the standard and size of these cold dies can be adjusted until compliance is discontinued.
After seeing the above introduction, some people think that the debugging of the cold stamping die is not over yet. In fact, the real debugging operation is not over. After the requirements, the severe operation process should be determined for this cold stamping simulation, so that this cold stamping die can be used by more people in practical operation.
In fact, in the whole process of debugging cold stamping dies to make car stamping parts, debugging personnel must pay attention to the fact that when debugging assumptions are found to affect the stability and batch production of cold stamping dies, debugging personnel should adjust the cold stamping dies in time. After all, it is the cold stamping dies. Able to achieve the purpose of safe production.
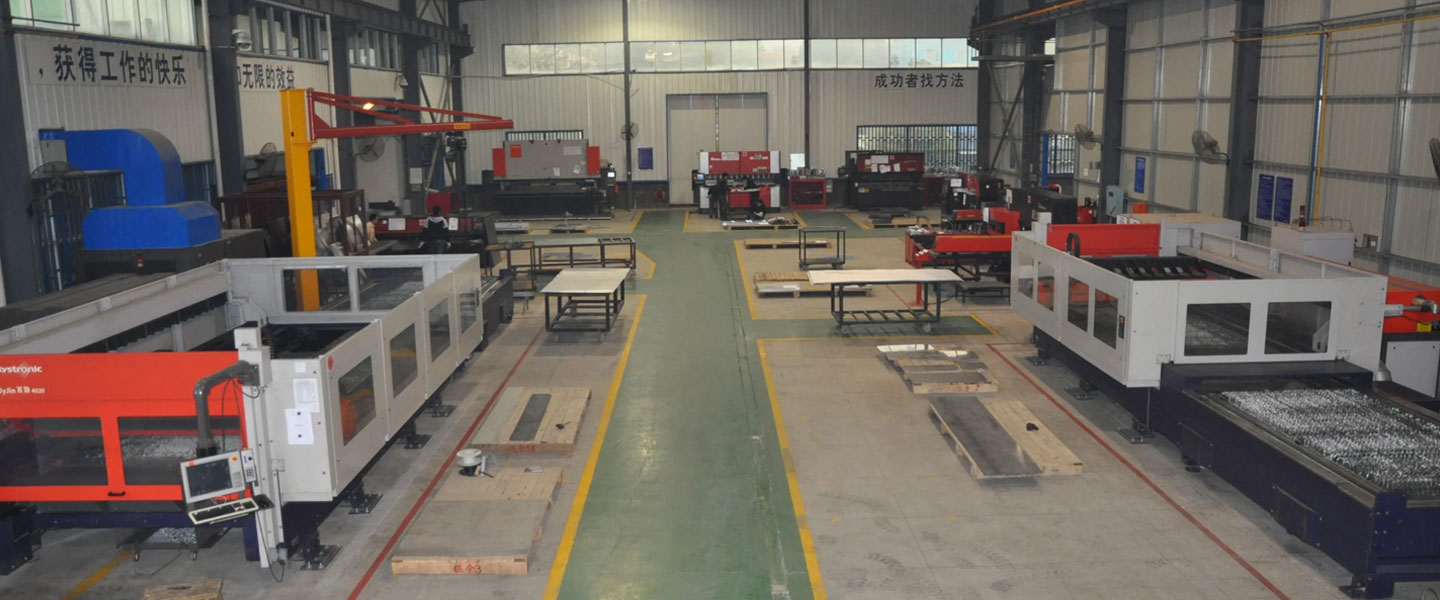
Pintejin Sheet Metal shop offers a cost-effective solution for a wide range of industries with our custom metal stamping and custom sheet metal fabrication capabilities. Our stampnig operations include a variety of sheet-metal forming manufacturing processes, such as punching, blanking, embossing, bending, flanging, and coining. Our professional, experienced and well-trained engineers can execute the complex metal stamping operations with precision and accuracy.
No matter what your metal fabrication needs are, Pintejin can offer the right solution: from single sheet metal part or sub-assembly of stamped metal parts to turnkey solutions for mechanical and electrical assemblies. We have the technology, equipment and the experience to fabricate customised metal products from aluminium sheet metal fabrication, steel, zinc plated steel, stainless steel sheet metal fabrication, brass and copper. Designs that require CNC machining of surfaces or components can be accommodated. We can supply polished, galvanized, zinc coated or powder coated finishes for any sheet metal work or stamped metal components. Coupled with our accurate and reliable metal fabricating equipment, we guarantee precision and repeatability in custom sheet metal work. You’ll be taking advantage of the best sheet metal fabrication china can produce.