
When we use the terminal die for stamping fabrication, in order to avoid the stamping workpiece from being damaged or unable to be used normally, we also need to pay attention to the following matters. The interval between the inner guide feet should be kept correct and uniform, and the imprinting process will reduce the interval. Therefore, it is necessary to control the imprint depth and suppress the lateral reflex of the guide feet.
The front section of the inner guide foot in the lead frame requires high flatness, and the flat area is at least 0.1MM or more (greater than three times the diameter of the gold wire), so imprinting must be used. The flatness of the lead frame is required to be high, which is conducive to the timely stability and smoothness of the subsequent project during transportation. The corresponding strategy is that when punching the guide feet, the amount of recurve should be suppressed to a small degree and the direction of the recurve should be consistent. In addition, the lead frame material before stamping should be subjected to stress relief work.
The deformation requirements such as twisting or offset of the guide feet in the lead frame are required to be small, which is beneficial to the operation of subsequent projects. The solution is to pay attention to the strong pressure design of the pressing plate in the mold, set the appropriate mold gap and functional components (punch and female mold), the knife part should be kept in good condition, and the rigidity of the mold guide device should be high.
The positional accuracy of the inner guide feet must be kept correct to facilitate the actual adhesion of subsequent projects. The corresponding strategy is to punch the inner guide feet first and then the outer guide feet. The punching sequence should be properly designed, and the adjustment station should be designed during the punching process. , in order to suppress the offset of the lead frame guide foot position during stamping.
In the daily life of precision stamping, there will be problems that the punching size is too large or small and the size of the punch is quite different.
When the punching edge is worn, the tensile stress of the material increases, and the tendency of the stamping parts to turn over and twist increases. When the material is turned over, the size of the punching hole will become smaller.
The strong pressure of automobile stamping parts on the material causes plastic deformation of the material, which will cause the size of the punching hole to increase. When the strong pressure is reduced, the size of the punching hole will become smaller.
Punch edge shape. If the end is trimmed with an inclined plane or an arc, due to the slowing down of the punching force, the punching piece is not easy to turn over and twist.
Precision metal stamping can produce workpieces with ribs, ribs, undulations or flanging that are difficult to manufacture by other methods to improve their rigidity. Due to the use of precision molds, the accuracy of the workpiece can reach micron level, and the repeatability is high and the specifications are consistent, and holes, bosses, etc. can be punched out. In the daily production of stamping parts, the punching size will be too large or small (may exceed the specification requirements) and the size of the punch is quite different. In addition to the blanking gap and other factors, the above aspects should also be considered.
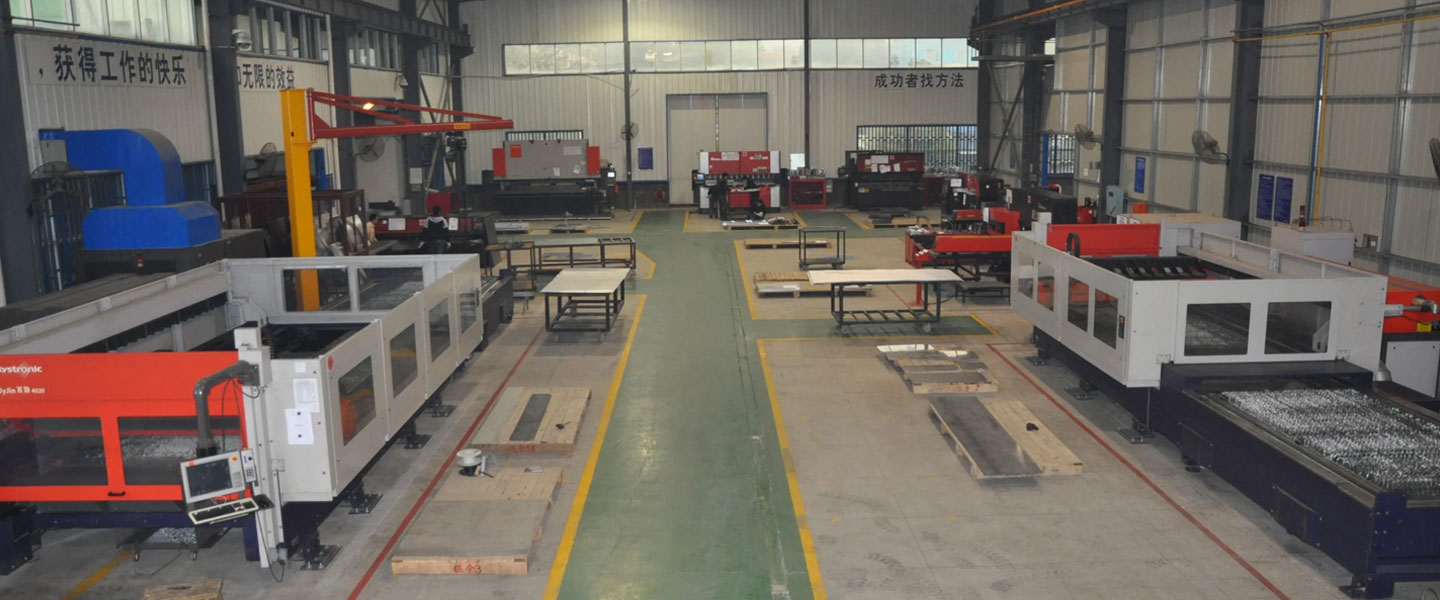
Pintejin Sheet Metal shop offers a cost-effective solution for a wide range of industries with our custom metal stamping and custom sheet metal fabrication capabilities. Our stampnig operations include a variety of sheet-metal forming manufacturing processes, such as punching, blanking, embossing, bending, flanging, and coining. Our professional, experienced and well-trained engineers can execute the complex metal stamping operations with precision and accuracy.
No matter what your metal fabrication needs are, Pintejin can offer the right solution: from single sheet metal part or sub-assembly of stamped metal parts to turnkey solutions for mechanical and electrical assemblies. We have the technology, equipment and the experience to fabricate customised metal products from aluminium sheet metal fabrication, steel, zinc plated steel, stainless steel sheet metal fabrication, brass and copper. Designs that require CNC machining of surfaces or components can be accommodated. We can supply polished, galvanized, zinc coated or powder coated finishes for any sheet metal work or stamped metal components. Coupled with our accurate and reliable metal fabricating equipment, we guarantee precision and repeatability in custom sheet metal work. You’ll be taking advantage of the best sheet metal fabrication china can produce.