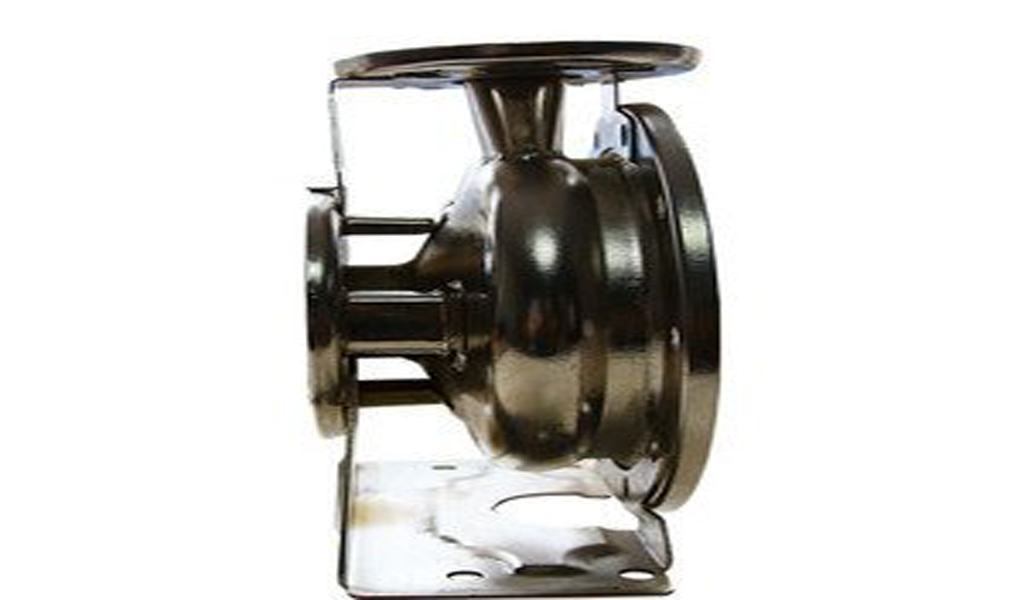
Methods of turning over and twisting stamping parts:
- 1) In daily mold production, attention should be paid to maintaining the sharpness of the punching convex and concave mold edges. When the punching edge is worn, the tensile stress on the material will increase, so that the stamping parts tend to turn over and twist.
- 2) The unreasonable blanking gap or the uneven gap is also the reason for the turning and distortion of the stamping parts, which needs to be overcome.
- 3) Reasonable mold design. In the progressive die, the arrangement of the blanking sequence may affect the forming accuracy of the stamping parts. For the blanking of small parts of stamping parts, generally a larger area of blanking is arranged first, and then a smaller area of blanking is arranged to reduce the impact of blanking force on the forming of stamping parts.
- 4) Hold down the material. Overcome the traditional mold design structure, and open a material-holding gap on the unloading plate (that is, when the mold is closed, the material can be pressed. The key forming part, the unloading plate is made into a block-type structure to facilitate the long-term solution The wear (pressure) loss caused by the pressing part of the stripper plate caused by the stamping, and the material cannot be compressed.
- 5) Add strong pressure function. That is to increase the thickness of the pressing part of the unloading insert (the normal thickness of the unloading insert is H+0.03mm) to increase the pressure on the material on the side of the die, so that the stamping parts are turned over and distorted during punching.
- 6) The end of the punch edge is trimmed with a bevel or arc. This is the way to reduce the buffering force. Reducing the buffer cutting force can reduce the tensile force on the material on the die side, so as to achieve the effect of turning over and twisting the stamping parts.
Stamping defect level:
In automobile manufacturing enterprises, after the defect types and judgment standards of stamping parts are clarified and unified within the enterprise, inspectors and manufacturing personnel will have “laws to follow”, which is also more conducive to the rectification of mold problems and the rectification of stamping parts problems and quality. Improve, shorten the mold cycle and save costs, so as to better create good stamping parts. According to the severity of quality defects and the degree of user acceptance, it can be divided into four categories: A, B, C and D.- Class A defects: defects that are unacceptable to customers, will cause stability complaints or cause stability hazards; surface defects and theoretical deviations have obvious deviations, which will attract the attention of untrained customers or cause functional failures. Such defective metal stamping parts It is unacceptable to the user, and the stamping parts need to be frozen immediately after discovery.
- Class B Defects: Unpleasant defects, usually complained about by users, cause general user dissatisfaction, and usually urge rework.
- Class C defects: Defects that need to be improved will cause claims (dissatisfaction) from discerning users. They are ambiguous and determined after careful inspection. Such defective stamping parts are repaired and repaired in B area, C and D areas. However, the repaired parts are not easy to be found by customers and need to meet the repairing standards of stamping parts.
- Class D Defects: Minor defects that may cause user dissatisfaction.
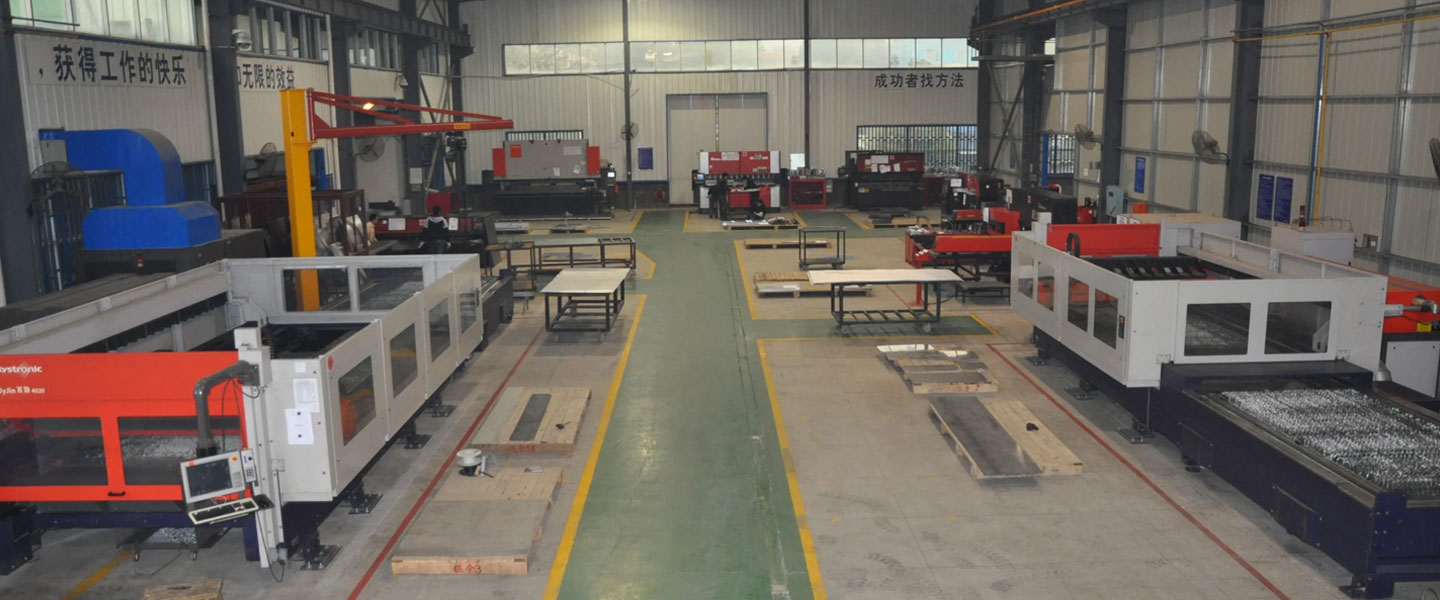
Pintejin Sheet Metal shop offers a cost-effective solution for a wide range of industries with our custom metal stamping and custom sheet metal fabrication capabilities. Our stampnig operations include a variety of sheet-metal forming manufacturing processes, such as punching, blanking, embossing, bending, flanging, and coining. Our professional, experienced and well-trained engineers can execute the complex metal stamping operations with precision and accuracy.
No matter what your metal fabrication needs are, Pintejin can offer the right solution: from single sheet metal part or sub-assembly of stamped metal parts to turnkey solutions for mechanical and electrical assemblies. We have the technology, equipment and the experience to fabricate customised metal products from aluminium sheet metal fabrication, steel, zinc plated steel, stainless steel sheet metal fabrication, brass and copper. Designs that require CNC machining of surfaces or components can be accommodated. We can supply polished, galvanized, zinc coated or powder coated finishes for any sheet metal work or stamped metal components. Coupled with our accurate and reliable metal fabricating equipment, we guarantee precision and repeatability in custom sheet metal work. You’ll be taking advantage of the best sheet metal fabrication china can produce.