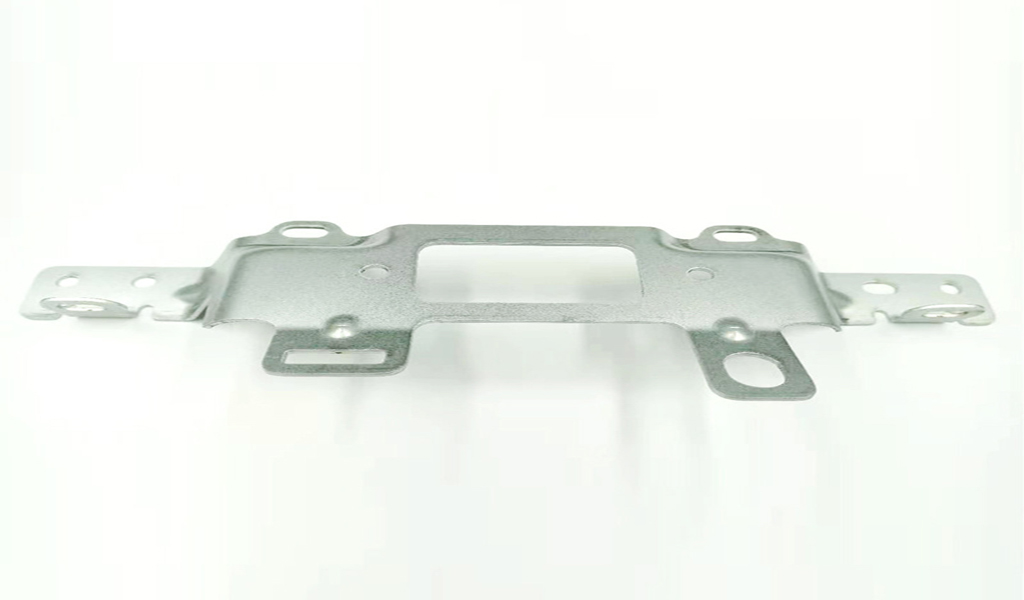
The unreasonable structural design of stamping parts determines that the material utilization rate is low, and due to the low material utilization rate caused by the structural design of the stamping parts, it cannot be improved. The shape of the stamping parts determines the upper limit of the material utilization rate. Therefore, the design of the stamping parts is reasonable and Whether it determines the level of material utilization in the later stage.
1. Reasonable division of stamping parts:
Through the discussion with the department, the structure is optimized as much as possible on the premise of meeting the performance of the stamping part in the early design stage of the stamping part, so as to achieve a large material utilization rate of the part, as shown in Figure 3. Both ends of the stamping data are protruding, which is not conducive to the formulation of the mold process in the later stage, and also greatly affects the material utilization rate.
2. Reasonable shape of stamping parts:
Through the SE project, the material utilization rate of each stamping part is optimized as much as possible through the study of the structure of the stamping parts and the layout layout. The material utilization rate is high, as shown in Table 2.
Therefore, it is very important to choose a reasonable modeling structure in the design stage of stamping parts, which also directly affects the manufacturing cost of the whole vehicle.
At present, automobile manufacturers pay more and more attention to the quality and economy of the whole vehicle, and the body, as a unit with a large proportion of the vehicle’s mass, bears a greater pressure to reduce the quality of the vehicle. raised more demands. The use of steel plates and very steel plates (usually above 1000 MPa) enables the design to meet the strength requirements while reducing the amount of rice and material thickness, thereby achieving the purpose of reducing the quality of the body (improving economy); on the other hand, the use of steel plates can Make it easier for the body to achieve stability performance indicators. The current cold stamping process has obvious shortcomings in forming the steel plate and cannot meet the design requirements, and the hot forming process can make up for this defect. Therefore, hot forming technology is currently widely used in various models of major automobile companies, and is used in parts with high collision requirements, such as door sills, front bumper beams, B-pillars, side door bumpers, etc.
The production cost of automobile stamping parts includes fixed cost and variable cost. Fixed costs refer to the equipment and mold costs required to produce stamping parts, and variable costs refer to material costs and labor costs. The proportion of fixed and variable costs is 35% to 65%, respectively. Among the fixed costs, it is mainly fixed investment such as tooling and equipment, which is decomposed into the cost of a single piece; among the variable costs, the proportion of material costs is more than half. Therefore, in order to reduce the production cost of stamping parts, the material cost should be controlled.
Ways to reduce the material cost of stamping parts:
1. Optimize the layout method:
The arrangement of the blanking parts on the sheet or strip is called the layout of the blanking parts. When determining a reasonable layout method, the layout of all the metals should be established, and the process waste should be reduced to improve the utilization rate of materials.
2. Material grade optimization:
The material grade has a greater impact on the material price. The higher the material grade, the higher the material price. Therefore, in the case of meeting the requirements of the forming process and the use requirements of the part, the low-grade grade materials should be used for fabrication as much as possible.
To achieve the optimization of material grades for stamping parts, it is necessary to simplify the shape of the stamping parts and the structure of the stamping die. The shape and structure of the product is extremely important. In the design process, it should be considered to simplify the product shape as much as possible on the premise of realizing the product function.
For those whose structure is small and can be simplified, it is generally adopted to expand the fillet R of the product drawbead, reasonably arrange the position, length and height of the drawbead, control the flow rate of the material, and avoid quality problems such as wrinkling and cracking of the parts.
3. Optimize the nominal size of the material:
In the stamping process, in order to pursue the minimization of the nominal size of the material, it is necessary to realize the minimization of the binder surface in the waste area and the process supplementary surface.
For product quality, a binder surface that prevents wrinkling than the product is essential. On the premise of meeting the functions of stamping parts, the material should be reduced in size.
Processing of stamping parts production problems:
- 1. Twisting: due to uneven stress, poor matching of drawbeads or poor control of the press slider, the r-corner part or the embossed part of the workpiece is tortuous and strained.
- 2. Wrinkles: Wrinkles at the edges or r parts are caused by poor adjustment of the press slider, low press precision, inappropriate adjustment of the air cushion pressure, and large punch or r parts.
- 3. Adhesion and scratches: defects on the surface of the workpiece or mold due to the friction between the material and the punch or die.
- 4. Burr: mainly occurs in the shearing die and blanking die, and the gap between the cutting edges is large or small, which will produce burrs.
- 5. Line offset: When the part is formed, the part that needs to be in contact with the mold is extruded and a line is formed.
- 6. Concave and convex: There are foreign objects (iron filings, rubber, dust) mixed in the uncoiled line to cause convex and concave.
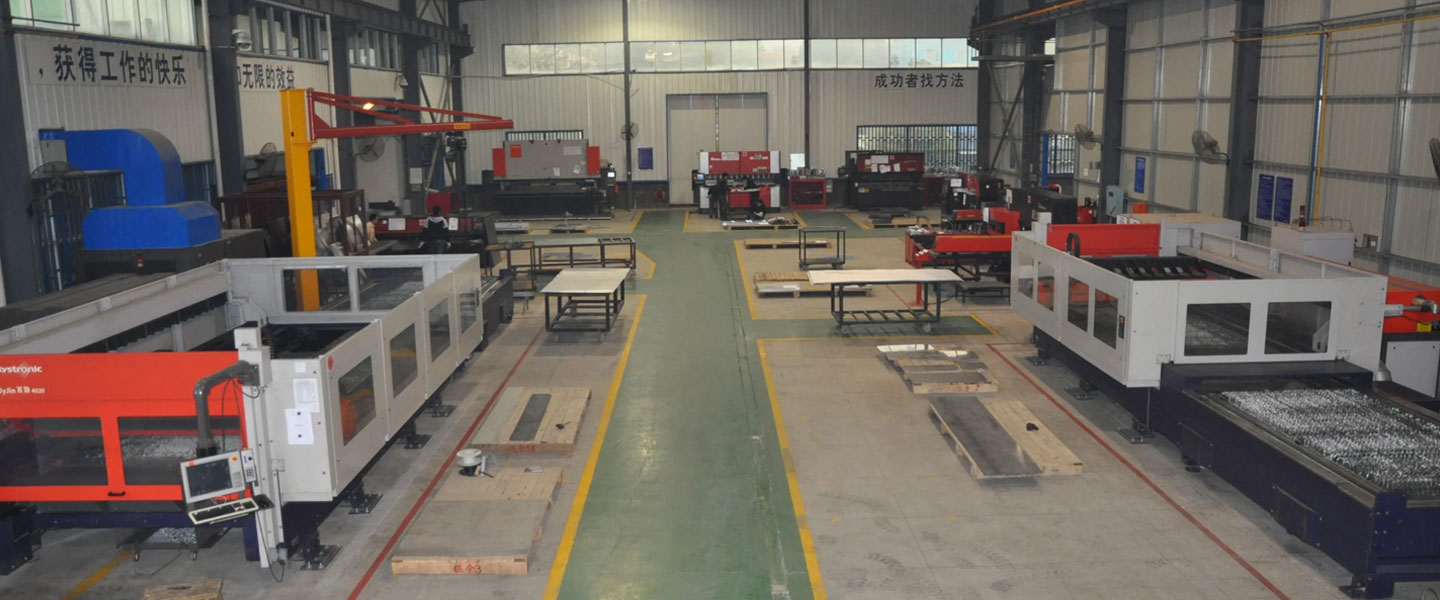
Pintejin Sheet Metal shop offers a cost-effective solution for a wide range of industries with our custom metal stamping and custom sheet metal fabrication capabilities. Our stampnig operations include a variety of sheet-metal forming manufacturing processes, such as punching, blanking, embossing, bending, flanging, and coining. Our professional, experienced and well-trained engineers can execute the complex metal stamping operations with precision and accuracy.
No matter what your metal fabrication needs are, Pintejin can offer the right solution: from single sheet metal part or sub-assembly of stamped metal parts to turnkey solutions for mechanical and electrical assemblies. We have the technology, equipment and the experience to fabricate customised metal products from aluminium sheet metal fabrication, steel, zinc plated steel, stainless steel sheet metal fabrication, brass and copper. Designs that require CNC machining of surfaces or components can be accommodated. We can supply polished, galvanized, zinc coated or powder coated finishes for any sheet metal work or stamped metal components. Coupled with our accurate and reliable metal fabricating equipment, we guarantee precision and repeatability in custom sheet metal work. You’ll be taking advantage of the best sheet metal fabrication china can produce.