
In the production process of automobile sheet metal parts, there are certain requirements for stamping technology and stamping dies. In high-speed stamping equipment and multi-functional stamping dies, only “high-speed” and “multi-functionality” cannot meet the production requirements. Only the continuous conveying of sheets to stamping machine tools and stamping dies is realized, and the stamped sheet metal workpiece can be The theoretical economic benefit can only be guaranteed when it is taken out of the stamping die and transported to the next stamping station in a very short time. Therefore, the correct stamping process should be: carefully analyze and study the stamping process of the entire sheet metal part, so as to ensure that the entire process from the time the sheet is loaded to the completion of the fabrication of the sheet metal part has an expected short production cycle, so as to achieve best efficiency.
Generally speaking, the working cycle of the stamping machine tool determines the production cycle of the stamping production line. The working time of the loading and unloading mechanism and the workpiece conveying mechanism of the stamping production line should be consistent with the stamping time of the stamping machine. In order to minimize or eliminate the auxiliary time of stamping machine tools and dies, the plate loading and unloading device and the workpiece conveying mechanism must be able to complete the loading and unloading and workpiece conveying tasks as soon as possible to reduce the downtime of the stamping production line.
Accurate positioning of the sheet: In the stamping production and fabrication of sheet metal parts, an important issue that needs to be paid attention to is the reliability of the stamping production process. Reliability refers on the one hand to trouble-free board loading and unloading, and on the other hand to the feasibility of the process technology. This must be done taking into account the performance of all equipment components and production components throughout the stamping line. Since punches and dies are usually not the focus of the problem, dynamic, reliable part positioning is very important.
Manipulator structure: It is composed of light structure steel pipe components, vacuum suction cups, vacuum devices, electromagnetic control valves, vacuum switches and other components. Since the manipulator is designed in strict accordance with the requirements of the workpiece and the user, a standardized manipulator connection interface is adopted in the design, and the special vacuum suction cup of the manipulator can be suitable for various workpieces. The company has accumulated rich experience in manipulator design in practice. The designed manipulator can completely match the plate and can be connected with the robot without any problem, with high rigidity and plate conveying accuracy. Since the arm of the manipulator is made of steel pipe structural parts, the weight of the motion control clutch, connecting parts and tie rods is greatly reduced, which further improves the motion performance of the manipulator and adheres to the acceleration and deceleration of plate workpiece transportation. Elastic jitter during movement.
The stamping production line not only has a high movement speed, but also requires a high positioning accuracy of sheet transport. Used for automatic loading and unloading on the stamping production line, the vacuum suction cup manipulator accurately transports the sheet in place according to the specifications of the sheet. Using the vacuum chamber stamping manipulator can easily achieve the purpose, the lucky star of the stamping line of automobile sheet metal parts.
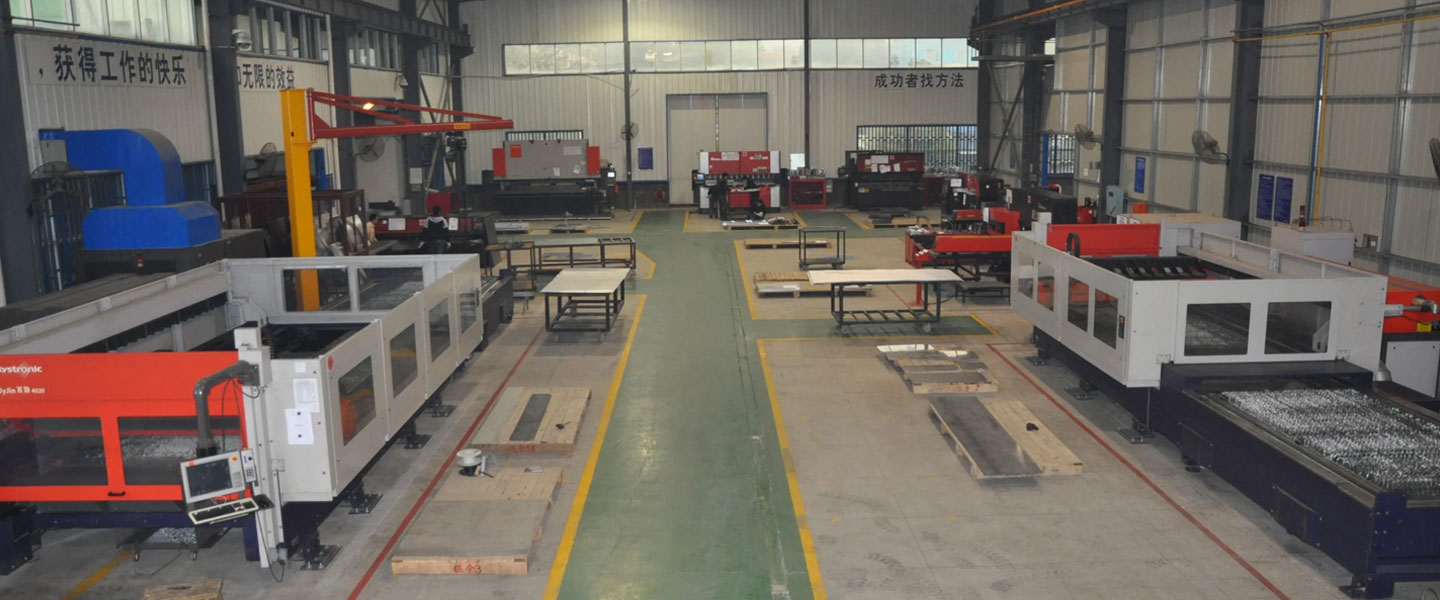
Pintejin Sheet Metal shop offers a cost-effective solution for a wide range of industries with our custom metal stamping and custom sheet metal fabrication capabilities. Our stampnig operations include a variety of sheet-metal forming manufacturing processes, such as punching, blanking, embossing, bending, flanging, and coining. Our professional, experienced and well-trained engineers can execute the complex metal stamping operations with precision and accuracy.
No matter what your metal fabrication needs are, Pintejin can offer the right solution: from single sheet metal part or sub-assembly of stamped metal parts to turnkey solutions for mechanical and electrical assemblies. We have the technology, equipment and the experience to fabricate customised metal products from aluminium sheet metal fabrication, steel, zinc plated steel, stainless steel sheet metal fabrication, brass and copper. Designs that require CNC machining of surfaces or components can be accommodated. We can supply polished, galvanized, zinc coated or powder coated finishes for any sheet metal work or stamped metal components. Coupled with our accurate and reliable metal fabricating equipment, we guarantee precision and repeatability in custom sheet metal work. You’ll be taking advantage of the best sheet metal fabrication china can produce.