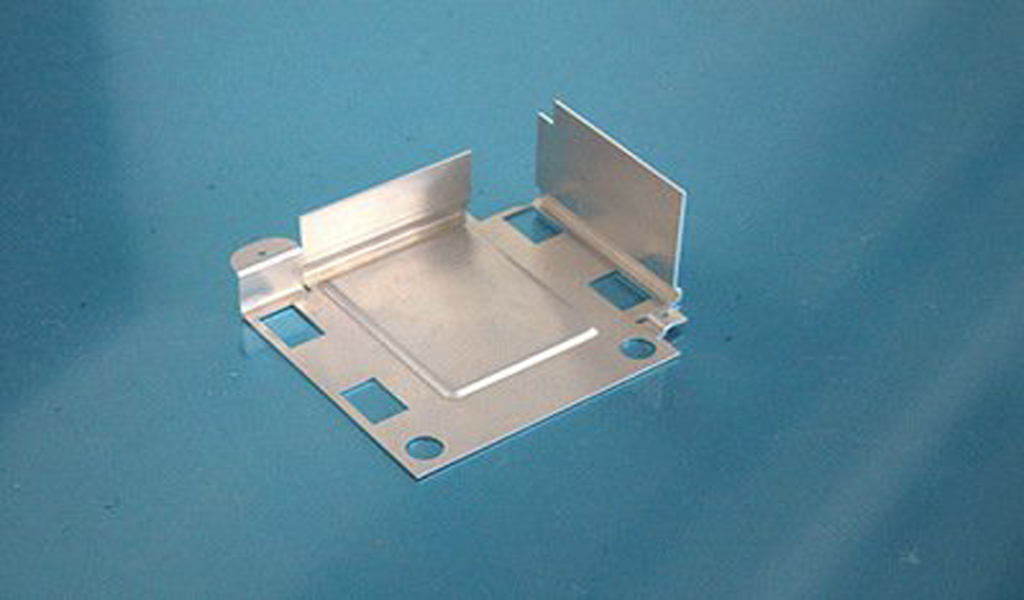
When we use Taicang sheet metal parts to process cabinets, we must not only master the size of the cabinet, but also check the shape of the equipment to ensure that it matches the selected bracket. A sturdy cabinet can hold up to 450 pounds, so check out the tools you use to get your sheet metal working equipment out. For example, a liftgate or a trolley. A good cabinet has wheels under it, so you just put the equipment in it and push the cabinet into place.
Measure the size of the room and the heights of the ceilings, doors, and elevators the cabinets pass through. In addition, considering the various types of equipment in the cabinet, make sure that the cabinet is placed close to the power supply, network cable sockets, and communication sockets. Check the angle at which the cabinet door opens when opening and closing the cabinet. The standard cabinet door opens on the right, and the door shaft is on the left, of course, the opposite is not excluded. All doors and side panels should be easily accessible for maintenance.
When you want to install equipment cabinets into an existing cabinet group, you can arrange the cabinets in a row next to each other, which is safe and neat. However, some cabinet groups cannot be added for various reasons, or only a few accessories can be added. A good model of the cabinet group should be sufficiently expandable with all the necessary hardware to remove the cabinet side panels and screw the cabinets to each other in a row.
Solutions to the Decrease of Machining Accuracy of CNC Machine Tools
Automobile sheet metal parts fabrication: the solution to the decline of the machining accuracy of CNC machine tools. The decline of machining accuracy of CNC machine tool parts is mainly due to the fact that the symmetry of the feed dynamic tracking error value between each axis is not adjusted in a good state.
There are two reasons for this failure: one is that the dynamic feed tracking error between each axis is not adjusted when the CNC machine tool is installed and adjusted; the other is that the transmission chain of each axis changes after the machine tool is used for a period of time ( Such as screw clearance, pitch error change, axial movement, etc.).
These two reasons can be solved by re-tuning and changing the amount of backlash compensation.
Sheet metal fabrication is one of the commonly used fabrication techniques, and it contains many processes, and welding is a part of it. For such a special workpiece as a sheet metal workpiece, what should be paid attention to when implementing welding technology?
There are many welding techniques involved here, including soft soldering and B hard soldering. The former is to use low melting point metal to bond two or more pieces of metal together, as long as the joint components are placed adjacent to each other, the joint is heated, and molten solder is injected into the joint; and the latter can obtain the joint strength. will be higher.
Observing these two welding techniques, the big difference is the melting point of the filler material injected into the joint. Although the welding strength of hard welding is relatively high, due to the high heat, the components may be deformed, melted or bent and warped. Corrosion and other undesirable phenomena. Therefore, the welding technology must be selected according to the requirements of the workpiece.
Classification of sheet metal fabrication and welding methods:
- 1 Classification of welding methods: Welding methods mainly include arc welding, electroslag welding, gas welding, plasma arc welding, fusion welding, pressure welding, and brazing. The welding of sheet metal products is mainly arc welding and gas welding.
- 2 Arc welding has the advantages of flexibility, maneuverability, wide applicability, and all-position welding; the equipment used is simple, durable, and low maintenance costs. However, the labor intensity is high and the quality is not stable enough, which depends on the operator’s level.
- It is suitable for welding carbon steel, low alloy steel, stainless steel and non-ferrous alloys such as copper and aluminum over 3mm.
- 3 The temperature and properties of the gas welding flame can be adjusted. The heat source of arc welding is wider than the heat affected zone, the heat is not as concentrated as the arc, and the productivity is lower than other hardware.
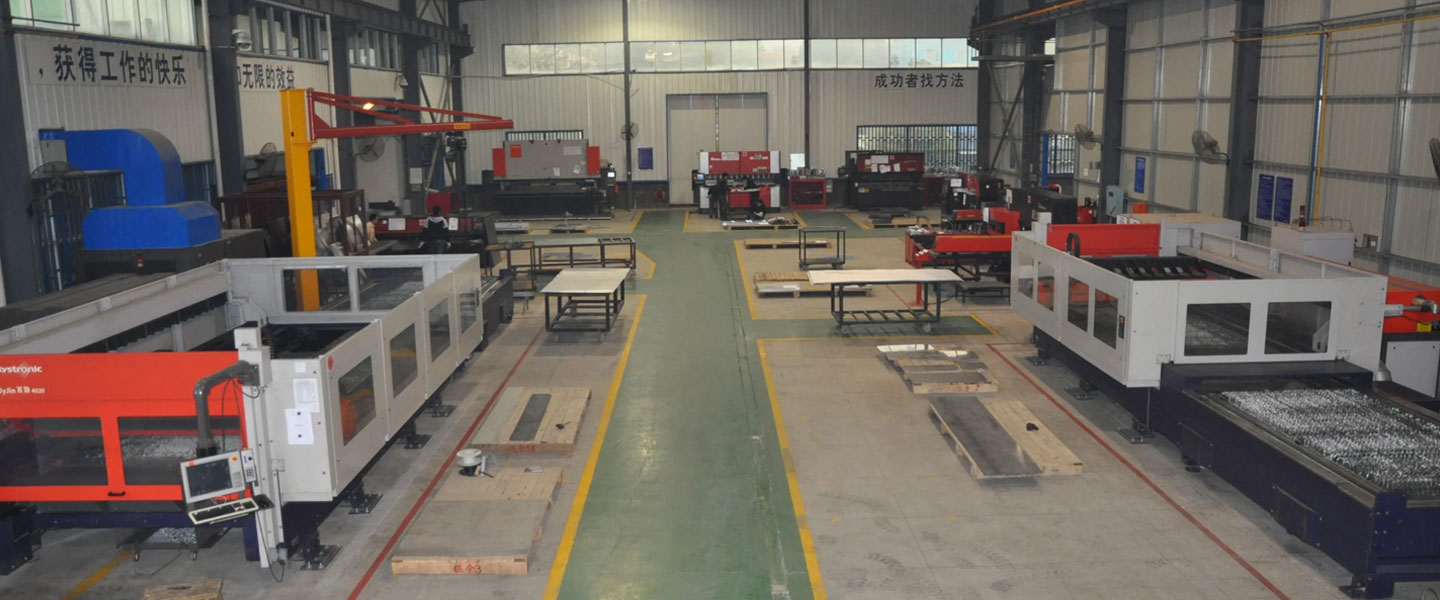
Pintejin Sheet Metal shop offers a cost-effective solution for a wide range of industries with our custom metal stamping and custom sheet metal fabrication capabilities. Our stampnig operations include a variety of sheet-metal forming manufacturing processes, such as punching, blanking, embossing, bending, flanging, and coining. Our professional, experienced and well-trained engineers can execute the complex metal stamping operations with precision and accuracy.
No matter what your metal fabrication needs are, Pintejin can offer the right solution: from single sheet metal part or sub-assembly of stamped metal parts to turnkey solutions for mechanical and electrical assemblies. We have the technology, equipment and the experience to fabricate customised metal products from aluminium sheet metal fabrication, steel, zinc plated steel, stainless steel sheet metal fabrication, brass and copper. Designs that require CNC machining of surfaces or components can be accommodated. We can supply polished, galvanized, zinc coated or powder coated finishes for any sheet metal work or stamped metal components. Coupled with our accurate and reliable metal fabricating equipment, we guarantee precision and repeatability in custom sheet metal work. You’ll be taking advantage of the best sheet metal fabrication china can produce.