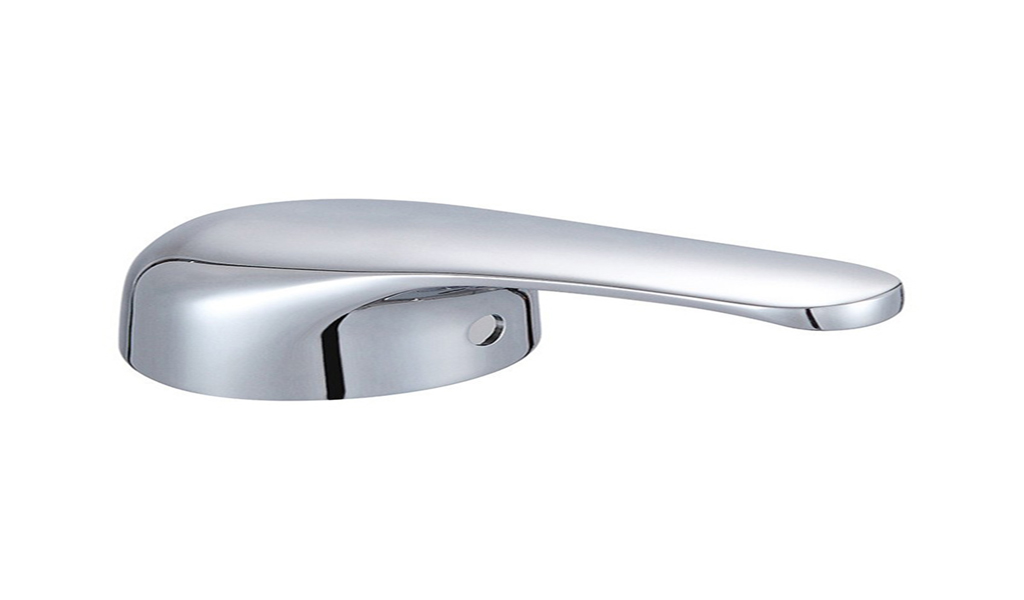
In terms of stamping forming process, auto parts can be roughly divided into three categories: ordinary parts, high tension parts, covering parts. Each type of parts has inconsistent formability, and everyone has a formability plan for each part. Different opinions, today I will talk about the understanding and opinions of the drawing die construction method according to my personal views and opinions, so that everyone can have a preliminary understanding of the drawing method.
Determination of stamping direction: First determine the stamping angle of the part. The principle of selecting the stamping angle should satisfy the forming of the part, the positioning of the sheet, and the utilization of the material (unreasonable stamping angle will increase the size of the sheet) .
The plane placement of the parts is determined: the principle of the plane placement angle of the parts is to save the size of the sheet, and the combination of the left and right parts should also follow this principle.
Determination of the shape of the material surface: the pressing surface is a part of the process supplement. When adding a supplementary surface for the process, the shape of the pressing surface must be correctly determined to make the feeding resistance of each part of the pressing surface as uniform as possible. To do this, it must be Ensure that the drawing depth in all directions is as uniform as possible, because only when the blank holder presses the drawn sheet on the die pressing surface without forming wrinkles and creases, can effectively ensure that the drawing does not crack and wrinkle. When determining the shape of the binder surface, the drawing depth should be reduced as much as possible to make the profile flat.
Determination of the process supplementary surface: First of all, it is necessary to know that the process supplementary surface is the part to be removed in the subsequent process, so the principle of process supplementation is: the drawing depth should be as shallow as possible without affecting the formability, which is conducive to vertical trimming as much as possible, and the process supplementary part It should be as small as possible, and at the same time, it can improve the plastic deformation of stretching.
Determination of drawbead position, size and quantity: the drawing direction, process supplement, and the shape of the binder surface are the prerequisites for determining whether a satisfactory part can be drawn, and the drawbead position and quantity are necessary. The main function of the drawbead is to increase the overall or local material deformation resistance to control the inflow of the sheet metal and improve the plastic deformation of the material. At the same time, it is also an effective method to prevent parts from wrinkling and cracking; the position, size and number of drawbeads should be analyzed according to the shape and drawing depth of each part.
After completing the above settings, enter the stamping AUTOFORM simulation analysis, and continue to debug by observing the wrinkling or cracking, strain, rebound and other parameters of the forming process, and finally get good results and enter the next process analysis.
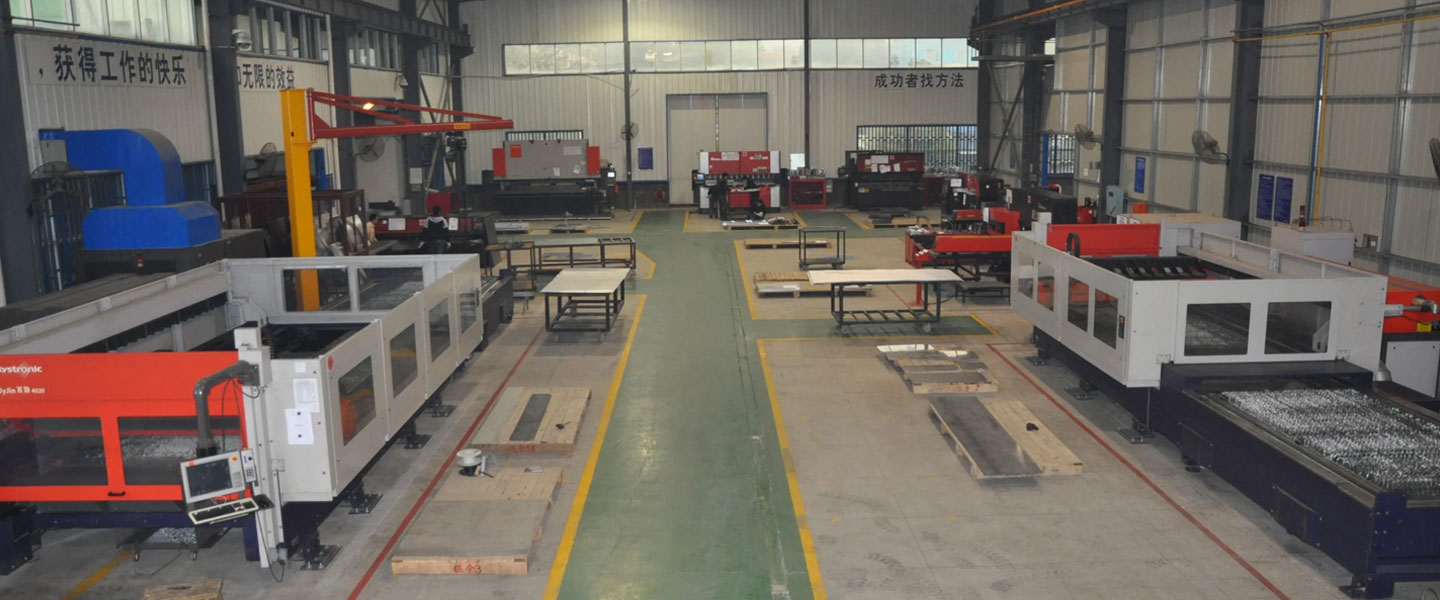
Pintejin Sheet Metal shop offers a cost-effective solution for a wide range of industries with our custom metal stamping and custom sheet metal fabrication capabilities. Our stampnig operations include a variety of sheet-metal forming manufacturing processes, such as punching, blanking, embossing, bending, flanging, and coining. Our professional, experienced and well-trained engineers can execute the complex metal stamping operations with precision and accuracy.
No matter what your metal fabrication needs are, Pintejin can offer the right solution: from single sheet metal part or sub-assembly of stamped metal parts to turnkey solutions for mechanical and electrical assemblies. We have the technology, equipment and the experience to fabricate customised metal products from aluminium sheet metal fabrication, steel, zinc plated steel, stainless steel sheet metal fabrication, brass and copper. Designs that require CNC machining of surfaces or components can be accommodated. We can supply polished, galvanized, zinc coated or powder coated finishes for any sheet metal work or stamped metal components. Coupled with our accurate and reliable metal fabricating equipment, we guarantee precision and repeatability in custom sheet metal work. You’ll be taking advantage of the best sheet metal fabrication china can produce.