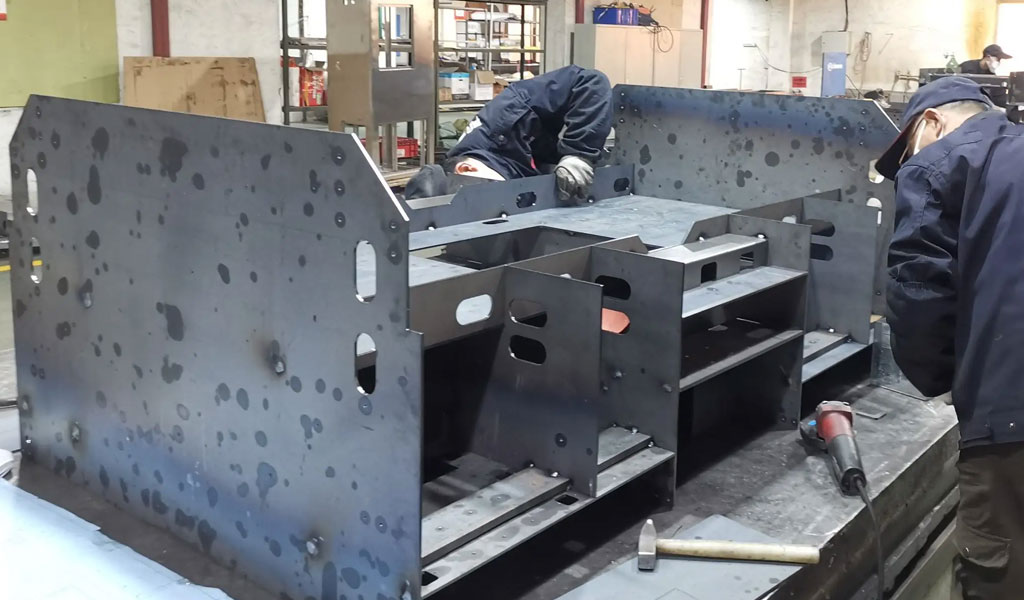
Sheet Metal Welding
Sheet metal welding fabrication is to weld multiple parts together to achieve the purpose of fabrication or to weld the edge seam of a single part to increase its strength. The fabrication methods generally include the following: CO2 gas shielded welding, argon arc welding, spot welding, robot welding, etc. The selection of welding methods in these sheet metal fabrication plants is based on actual requirements and materials. Generally speaking, the rental welding of robot electric welding machine is mainly used when the material is large and the welding seam is long.
Such as cabinet welding, robot welding can be used, which can save a lot of tasks and improve work efficiency and welding quality. CO2 gas shielded welding is used for iron plate welding; argon arc welding is used for aluminum plate welding.For a sheet metal fabrication factory, the fabrication process is indispensable for the welding process, because only through welding can multiple parts be combined together.
Sheet Metal Welding Services For Precision Sheet Metal Parts – China Industries Welding Parts Factory, Supplier
Sheetmetal.wiki – Pintejin provides best sheet metal welding services for the fabrication of both small and large series of sheet metal parts of any complexity. We use various types of industries welding machines including upright, bench, radial, which allows us to welding of both simple and complex up to 24 ft. length and 92 in. dia.. The sheet metal welding parts be made of metals and alloys (aluminium, steel, copper and others) and polymers. Our welding services provide us with the capability to complete your job in-house to our exacting quality standards. Our advanced sheet metal welding equipment is integrated with our sheet metal machine and allows us to efficiently and precisely welding your part, whether you require simple or complex welding patterns.
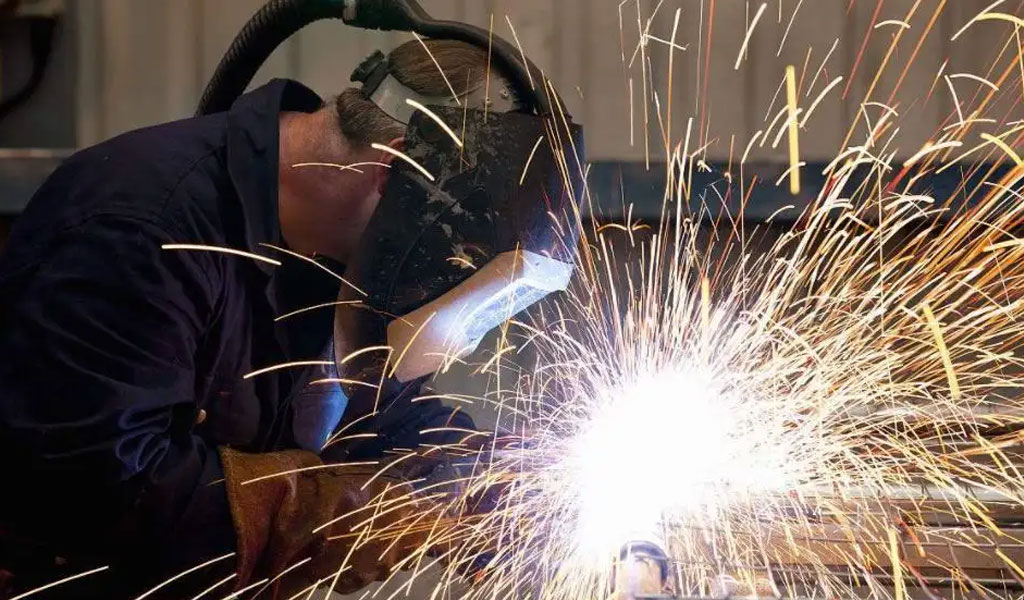
Currently, our non-standard sheet metal welding parts are exported to America, Canada, Australia, United Kingdom, Germany, France, Sout Africa, and many other countries all over the world. We are ISO9001-2015 registered and also certified by SGS.
Our custom industries welding service provides durable and affordable parts that meet your specifications for automotive, medical, aerospace, electronics, food, construction, security, marine, and more industries. Fast to send your inquiry or submit your drawings to get a free quote in the shortest time.Contact us or Email [email protected] to see how our people, equipment and tooling can bring the best quality for the best price for your custom sheet metal welding project.
-
What are the repair methods for car body sheet metal damage?
-
How to distinguish the pros and cons of automotive sheet metal parts on the market?
-
How about the application of cold stamping process in automobile stamping parts?
-
What are the technical characteristics of high-speed precision stamping parts?
-
Application of Micro-Joint Processing Technology of CNC Punching Machine in Sheet Metal Manufacturing
-
Do you know what is a car sheet metal part?
The Advantages And Disadvantages Of Sheet Metal Welding
Sheet metal welding fabrication is to weld multiple sheet metal parts together to achieve the purpose of fabrication or to weld the side seam of a single part to increase its strength. The advantages and disadvantages of sheet metal welding are as follows:
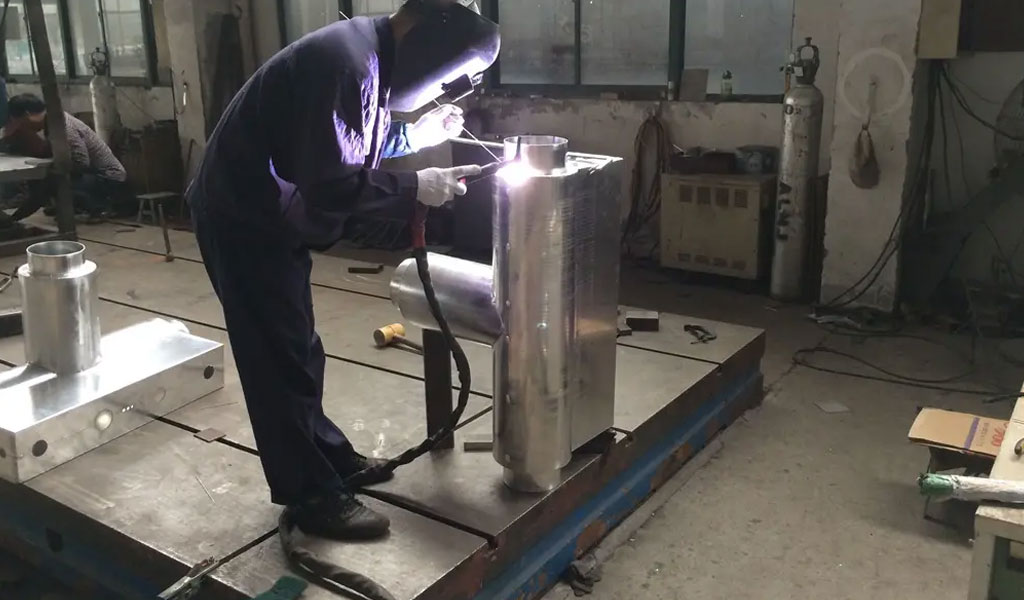
The Benefits And Advantages Of Welding
- Save metal materials and reduce structural weight
- Simplify fabrication & installation procedures & improve efficiency
- High structural strength and good joint sealing; provide greater flexibility for structural design
- It is easy to realize mechanization and automation
- Reduce production costs and save production costs
The Disadvantages Of Sheet Metal Welding
- The simple welding structure leads to large residual deformation and welding internal stress. Because most of the welding methods use partial heating, the welded parts after welding will inevitably have stress and deformation in the structure, which will affect the structural bearing capacity, processing accuracy and dimensional stability. At the same time, it will also lead to stress concentration at the junction of the weld and the weldment, which will affect the brittle fracture of the structure;
- There are a certain number of shortcomings in welded joints: such as cracks, pores, slag inclusions, incomplete penetration, and lack of fusion. Shortcomings can reduce strength, cause stress concentration, and damage weld fineness;
- The welded joint has a large functional non-uniformity, because the composition and metallographic structure of the weld are different from the base metal, and the internal stress of each part of the joint is different, so that the performance of the joint in different places is different;
- High temperature, strong light and some toxic gases occur during welding, which have certain harm to the human body, so labor protection needs to be strengthened.
The Fabrication Steps Of Sheet Metal Welding – How Sheet Metal Welding Works
The selection of sheet metal welding method is determined according to the actual requirements and materials. Generally speaking, argon arc welding is used for aluminum plate and stainless steel welding, and galvanized plate is used for two-protection welding. Bolts and nuts use resistance welding or pressure welding.