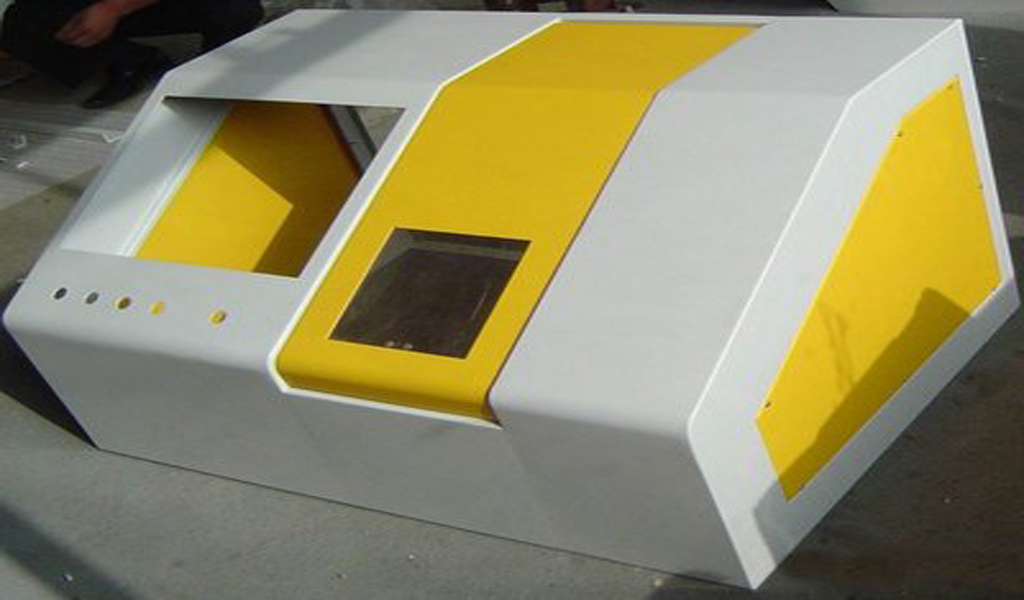
Sheet metal manufacturing is a crucial process in various industries, including automotive, aerospace, electronics, and construction. The demand for precision and efficiency in sheet metal processing has led to the development of advanced technologies, such as CNC (Computer Numerical Control) punching machines. These machines offer high accuracy, repeatability, and versatility, making them a preferred choice for sheet metal processing. One significant advancement in CNC punching technology is the application of micro-joint processing, which has revolutionized sheet metal manufacturing by enabling the production of intricate designs and reducing material waste. This article explores the application of micro-joint processing technology in CNC punching machines and its impact on sheet metal manufacturing.
Overview of CNC Punching Machines
CNC punching machines are versatile and automated machines used for cutting, perforating, and forming sheet metal components. They utilize computer-controlled programs to precisely move the punching tools and perform various operations on the sheet metal. CNC punching machines can handle different sheet metal materials, including steel, aluminum, and stainless steel fabrication, and are capable of producing complex shapes and patterns with high accuracy.
The Concept of Micro-Joint Processing
Micro-joint processing is a cutting-edge technique that involves creating small, strategically placed connecting bridges, or micro-joints, during the punching process. These micro-joints act as temporary supports to hold the cutouts in place until the end of the punching operation. Once all the cuts are completed, the sheet metal is easily separated by removing the micro-joints, leaving behind the desired finished part.
Advantages of Micro-Joint Processing in CNC Punching
The application of micro-joint processing in CNC punching machines offers several significant advantages:
1. Enhanced Design Flexibility: Micro-joint processing allows for intricate and complex designs, including intricate patterns, text, logos, and cutouts, which were previously challenging to achieve with traditional punching methods.
2. Minimized Material Waste: Micro-joint processing significantly reduces material waste as the small connecting bridges occupy a minimal surface area. This optimization leads to more efficient material usage and cost savings.
3. Improved Edge Quality: The use of micro-joints ensures that the punched edges are clean and free from burrs or deformations, resulting in higher-quality finished parts.
4. Reduced Deformation: Micro-joint processing minimizes the deformation of the sheet metal during the punching process, contributing to the overall accuracy and precision of the final part.
5. Faster Production Time: Micro-joint processing can speed up production cycles as it eliminates the need for secondary operations like deburring and separating parts, reducing overall processing time.
6. Enhanced Component Strength: The presence of micro-joints can provide temporary support to the sheet metal during the punching process, resulting in reduced chances of deformation and increased component strength.
Applications of Micro-Joint Processing in Sheet Metal Manufacturing
Micro-joint processing has found extensive applications in cabinet sheet metal manufacturing and more, benefiting a wide range of industries:
1. Automotive Industry: In the automotive sector, micro-joint processing is utilized to create intricate designs for components such as decorative trims, speaker grilles, and ventilation panels.
2. Electronics and Telecommunications: Micro-joint processing is used to manufacture electronic enclosures, control panels, and connectors, where precision and intricate designs are crucial.
3. Aerospace Industry: In the aerospace industry, micro-joint processing allows for the creation of complex and lightweight structures, including aircraft interior components and cabin panels.
4. Consumer Electronics: The application of micro-joint processing is evident in consumer electronics, such as smartphone frames, tablet casings, and computer bezels.
5. Construction and Architecture: Micro-joint processing is utilized to produce decorative architectural elements, perforated facades, and ornamental designs.
6. Energy and Renewable Sector: In the energy and renewable sector, micro-joint processing is employed to manufacture parts for solar panels, wind turbines, and battery enclosures.
The Micro-Joint Processing Workflow
The micro-joint processing workflow in CNC punching machines involves several steps:
1. Design and Programming: The initial step is to create a precise CAD (Computer-Aided Design) model of the desired component, including the micro-joints. Specialized software is used to generate the CNC program that will guide the punching machine.
2. CNC Punching Machine Setup: Once the CNC program is generated, the operator sets up the CNC punching machine by aligning the sheet metal and loading the appropriate tooling.
3. Micro-Joint Creation: During the punching process, the CNC machine creates small connecting bridges at strategic points, forming micro-joints that hold the cutouts in place.
4. Complete Cutting Cycle: The CNC punching machine continues the cutting cycle, perforating the sheet metal to produce the desired shapes and patterns.
5. Micro-Joint Removal: After all the cuts are made, the sheet metal is taken off the machine, and the operator carefully removes the micro-joints, freeing the finished parts.
6. Post-Processing: The finished parts may undergo additional post-processing steps, such as bending, welding, or surface finishing, to achieve the desired final product.
Considerations and Challenges
While micro-joint processing offers numerous advantages in sheet metal manufacturing, there are some considerations and challenges to be aware of:
1. Micro-Joint Placement: Proper placement of micro-joints is essential to ensure that they provide sufficient support during the punching process without causing interference or affecting the component’s functionality.
2. Material Selection: The choice of sheet metal material may influence the effectiveness of micro-joint processing. Different materials have varying mechanical properties that affect micro-joint creation and removal.
3. Micro-Joint Dimensions: The dimensions of the micro-joints must be carefully determined to strike a balance between providing adequate support and minimizing material waste.
4. Micro-Joint Removal Techniques: Developing efficient and reliable methods for removing micro-joints without damaging the finished parts is crucial for maximizing productivity.
5. Operator Training: Proper training of CNC machine operators is necessary to ensure that they understand the micro-joint processing workflow and can perform the necessary steps accurately.
Micro-joint processing technology has revolutionized sheet metal manufacturing, offering enhanced design flexibility, minimized material waste, improved edge quality, and reduced deformation. CNC punching machines equipped with micro-joint processing capabilities have become indispensable tools in various industries, enabling the production of intricate and precise sheet metal components. As the demand for high-precision and complex designs continues to grow, the adoption of micro-joint processing technology is expected to expand further, shaping the future of sheet metal manufacturing and advancing the capabilities of CNC punching machines.