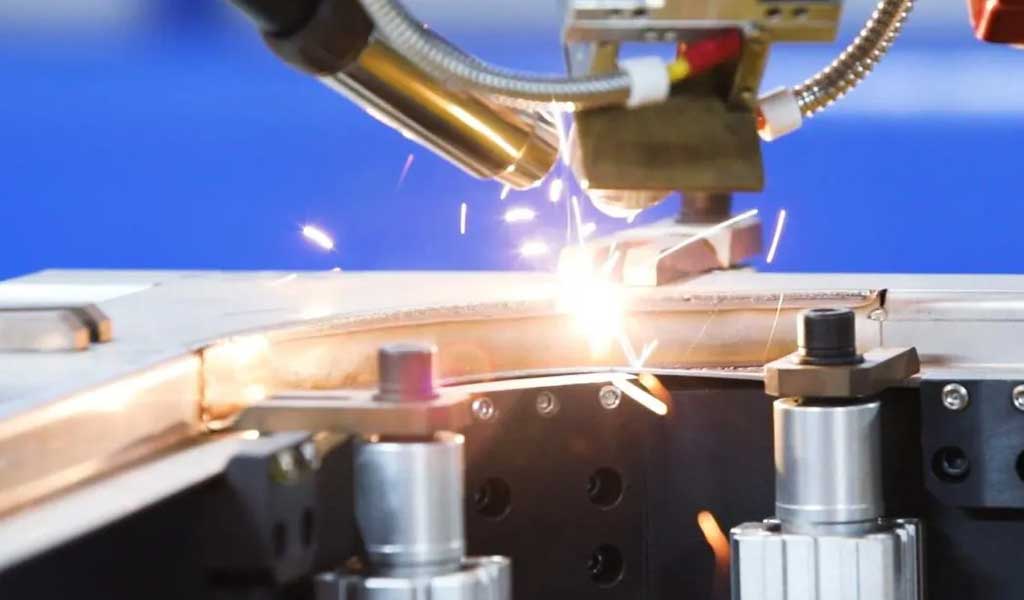
What does the word “sheet metal” remind you of? Most people would probably answer something like “baking pan” or “baffle plate”. That’s because they didn’t know what Herbert Staufer, Fronius International Head of High Power Welding, was doing at TRUMPF Australia’s production workshop in Pasching. The steel plate there is 4 meters long, 200 mm thick, and placed on the ground as high as ankles. With Fronius becoming one of the leading suppliers of hybrid welding machines, it is no surprise that Staufer knows this material like the back of his hand.
He usually travels to Pasching as a client, but has recently become a supplier for joint projects. Thomas Reiter, Staufer’s project partner and customer for sheet metal processing in Pasching, explained why Staufer was invited to the project: “We are going to weld these sheets and make the frame of the bending machine, which requires very specialized welding Technology.” To demonstrate the actual working conditions, the two put down the metal sheet and walked towards a gray wall that looked like the exterior of a production plant without windows, but was clearly inside the workshop. The TruDisk 8002 disc laser is leaning against the wall and looks small by comparison.
On the other side of the wall, the hydraulic system in the large laser safe room lifts and tilts the 20-ton steel plate to the desired angle. The beam is moved over the equipment, the robotic arm equipped with the hybrid welding head is extended, the first row of weld joints is slowly drawn, the material is heated with the laser, and then the main event begins: the laser beam and the metal active gas (MAG) Arc torches work together to weld the weld. These solder joints are up to 8mm deep and can eventually withstand up to 320 tons of pressure. This constant repetition enables the press brake to function properly throughout its service life.
Outside the laser room, Staufer and Reiter watched the process on a monitor. “We used to send the racks out for a whole week to be welded by hand! After that, we were determined to be more efficient,” says Reiter, who quickly discovered that laser hybrid welding was the right solution. “This welding process is much faster because we only need one pass, unlike arc welding, which has to be done bit by bit. And we can also preheat the material with a laser, and it’s easier to ensure quality with automatic processing.” This solution is Option A, and just in case, he also prepared Option B – an automatic solution that can be paired with traditional MAG welding robots. “But Option B requires a preheat unit and subsequent stress relief heat treatment,” Reiter said, so no one wants to use Option B. But there was a huge problem with Option A, as Staufer said: “We’ve delivered over a hundred laser hybrid horns, but the thickest sheet we’ve ever machined is only 10mm.”
Two years ago, Reiter and Staufer spent a lot of time in Fronius’ R&D laboratory, and a series of photomicrographs showed many small cracks and imperfections in the cutout of the weldment, rendering the weld unusable. They were also confident, Staufer recalls: “The 8-kilowatt laser power could easily penetrate 12mm of material, but we had absolutely no control over the small holes.” The cracks suggested that the problem was preheating. “With laser preheating, we were able to fully control the parameters, but no matter how we adjusted the temperature, the crack didn’t change at all.”
It seemed that option B had become the only option, but at a meeting TRUMPF came up with the idea of fundamentally adjusting the welding strategy, Reiter recalls with a smile: “Maybe it was because we were only close to giving up option A, so we Ask yourself: Do we really need that deep weld to achieve a perfectly stable interface?” So Staufer and his team of laser experts at Fronius began to gradually reduce the weld depth to 10mm, and they finally breathed a sigh of relief , the quality of the weld began to improve, “at 8 mm we finally got the desired welding results.” Staufer said.
With this phased victory, the project team began to address the next issues. “To optimize the welding process, the laser needs to contact the material at the right angle, but the robot is not flexible enough to reach every spot,” says Staufer. Fortunately, Staufer knows exactly how to solve this problem.
Raimund Geh loves this kind of challenge. His company, Femitec GmbH, located in Gersthofen near Augsburg, specializes in the design of welding systems. He explained his solution to the problem: “If a robotic arm with a laser hybrid welding head can’t reach the weld, we can do that.” His idea was to use a positioner with a chuck. “We were sure this would allow us to weld in a flat welding position.” Geh and his team developed a sophisticated simulation system to test their theory, and the next step is to put it into practice.
Yaskawa Europe Ltd is a leading drive technology, industrial automation and robotics manufacturer dedicated to turning company vision into reality. Project management leader Otwin Kleinschmidt tilted his palm to a critical 45-degree angle, then said with a smile, “The theory is simple, the positioner plus the chuck device, just bigger.”
The team’s first challenge was to design a hydraulic system that could withstand several tons of weight, with precise positions to the millimeter. “The only way to get the welding robot right on the welding path,” explains Kleinschmidt. Another challenge was coordinating the movement of the robot and the beam, but after 4 months of practice, everything was finally on track.
In Pasching, Staufer and Reiter are again looking at various machines. In front of them are workpieces on pallets, and cranes are helping production workers put sheet metal in place on the workbench, a process that takes two hours. This sounds complicated, but it is actually a very fast solution for the part being machined. Then, the positioner moves along the track to the laser safe room. After the welding robot is in place, the worker moves to the other end of the safe room to clamp the next frame to the second workbench. “With this system, we can weld more than 20 frames per week,” says Reiter. Staufer is also delighted: “We have been able to process different orders with this welding process.”