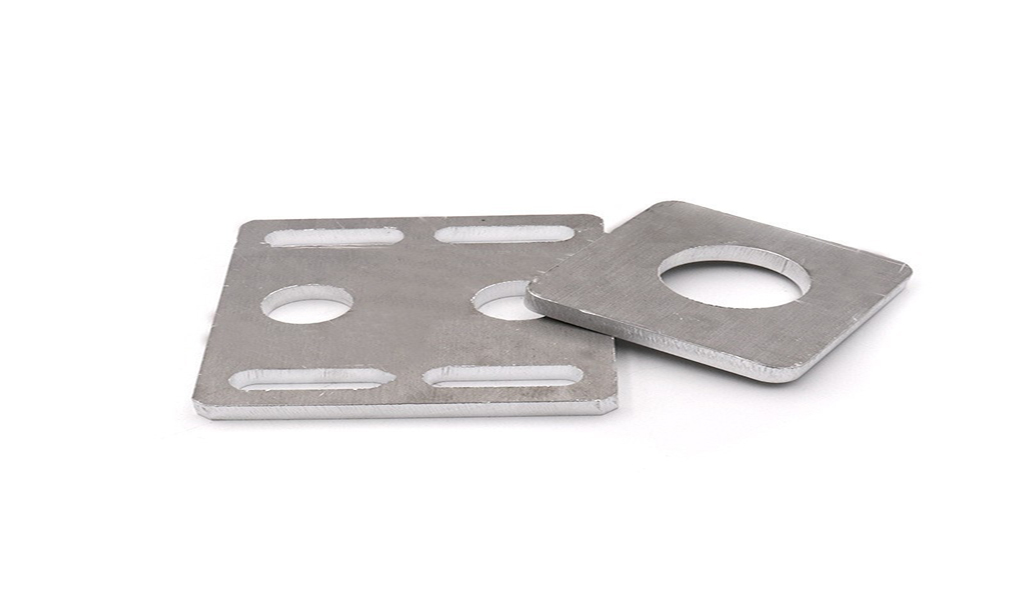
The quality inspection of automobile stamping parts needs to achieve: smooth surface, clear ridges, sufficient rigidity and dimensional stability, and no defects such as wrinkles, scratches, and bruises.
Common quality problems in the production of automobile stamping parts are: rough surface, insufficient dimensional accuracy, insufficient rigidity, surface cracking, indentation and other defects. In particular, problems such as indentation, scratches, and pitting are easy to occur, and defects such as indentation and pitting occur because the surface of the mold is defective or there are foreign objects or sand particles on the pressing surface or blank surface of the mold. In the production process of automobile stamping parts, there will be abnormal marks. When the surface is polished by the whetstone, bright spots, bright marks, etc. will appear. Scratches and bumps generally occur when workers are not careful during operation, and are also prone to occur during parts turnover. And the more turnovers, the more chances of bumps and scratches.
How to avoid similar situations and improve the quality of automotive stamping parts?
Causes and solutions of cracking: When the automobile stamping parts are stretched, the flange wrinkling and side wall wrinkling will occur due to compression deformation. To avoid this phenomenon, the internal tensile stress of the plate can be increased to eliminate the wrinkles. The blank holder force is increased by increasing the stretching rib, reducing the radius of the die fillet, adjusting the gap of the binder surface and the stretching gap. The tensile deformation force of the locally formed stamping part is higher than that of the side wall material, which will lead to bidirectional elongation and deformation. If the external material cannot supplement the interior, it will rupture due to excessive deformation. How to overcome this problem?
First of all, the blanking method is used to ensure the quality of the edge section of the blank, thereby improving the edge state of the blank. Appropriately increasing the size of the material can effectively determine the size of the concave flanging blank. If the blank size becomes larger or the shape is improper, it is necessary to change its size or shape, and adjust the stamping process to overcome edge cracking.
Secondly, the gap between the convex and concave molds should be uniform, and the rounded corners of the convex and concave molds should be appropriately increased, and the drawing process or the shaping process should be increased to ensure that the resistance of the material entering the mold is uniform and consistent, which can effectively overcome the shear rupture.
The reason for the rebound and the solution:
The springback of automobile stamping parts is due to insufficient plastic deformation of the material in the deformation zone due to improper technology and unreasonable mold structure. To solve this problem, we must first use a reasonable process method to improve the stress state of the sheet during the forming process, and secondly, it can also be solved by using the springback angle, springback radius, mold gap, etc.
In order to ensure that the car will not generate resonance, noise, etc. during the driving process, it is necessary to ensure that the cover has certain rigidity requirements. Under the condition that the structural size and shape of the cover are not changed, the greater the plastic deformation during the stamping and forming process, the better the stiffness. To ensure sufficient stiffness, in the design, the depth should be appropriately increased by stretching, or the process should be supplemented to increase. The plastic deformation is increased by means of stretching ribs, stretching sills, and increasing blank holder force, so as to improve the rigidity of stamping parts.
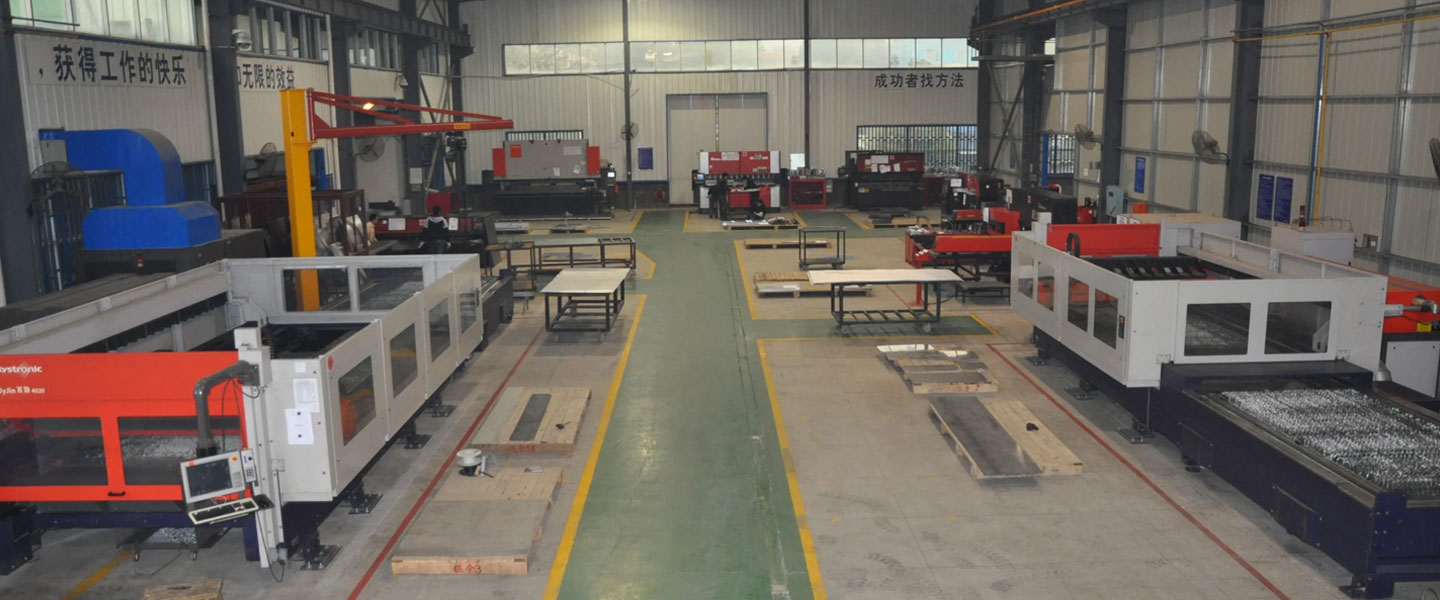
Pintejin Sheet Metal shop offers a cost-effective solution for a wide range of industries with our custom metal stamping and custom sheet metal fabrication capabilities. Our stampnig operations include a variety of sheet-metal forming manufacturing processes, such as punching, blanking, embossing, bending, flanging, and coining. Our professional, experienced and well-trained engineers can execute the complex metal stamping operations with precision and accuracy.
No matter what your metal fabrication needs are, Pintejin can offer the right solution: from single sheet metal part or sub-assembly of stamped metal parts to turnkey solutions for mechanical and electrical assemblies. We have the technology, equipment and the experience to fabricate customised metal products from aluminium sheet metal fabrication, steel, zinc plated steel, stainless steel sheet metal fabrication, brass and copper. Designs that require CNC machining of surfaces or components can be accommodated. We can supply polished, galvanized, zinc coated or powder coated finishes for any sheet metal work or stamped metal components. Coupled with our accurate and reliable metal fabricating equipment, we guarantee precision and repeatability in custom sheet metal work. You’ll be taking advantage of the best sheet metal fabrication china can produce.