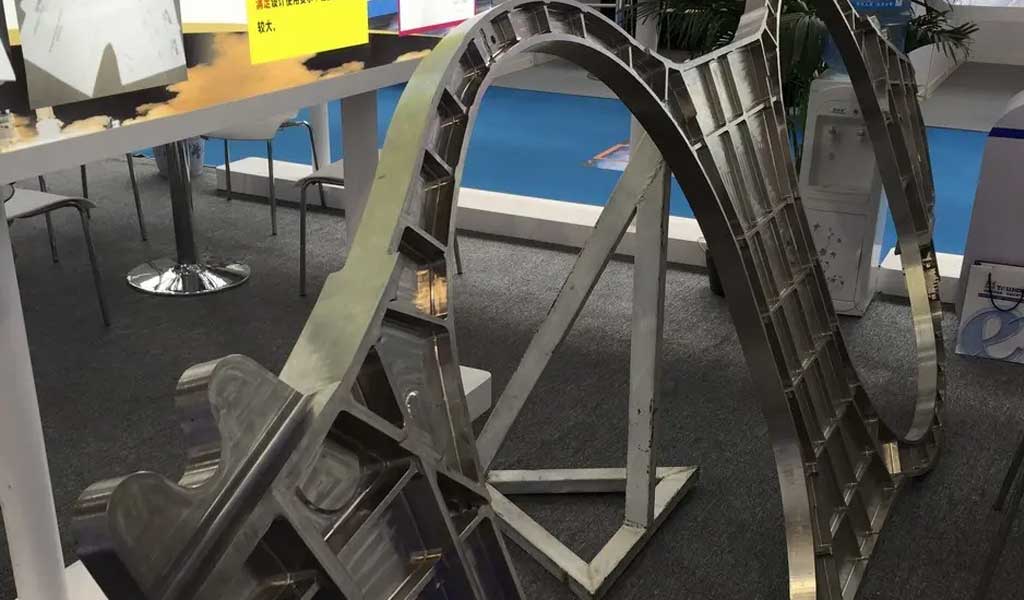
Since the invention of the first laser in the 1960s, lasers have been widely used in many fields due to their high directivity, high brightness, high monochromaticity and high coherence, and have become an ideal processing heat source. After the laser is focused, the power density on the spot can reach 104~1015W/cm2, and the metal material will heat up, melt or even vaporize instantly under the irradiation of high power density light. Therefore, by applying different power densities and heating time, the laser can achieve different processing purposes such as surface heat treatment, surface remelting, alloying, cladding, welding, cutting, drilling, surface impact strengthening, etc. It is a very ideal heating source. The surface modification technology of laser processing has been applied in the fields of aircraft structure and aero-engine manufacturing. Our country uses laser cladding technology to cast aero-engine turbine blade crowns and turbine guides, and successfully restore the shape, size and performance of damaged parts.
In recent years, with the rapid equipment of new aircraft, titanium alloys and composite materials have become the main structural materials of our military’s active aircraft. The laser is widely used in various fields due to its high directivity, high brightness, high coherence and other excellent qualities, and it will also play an important role in the field of aircraft structural repair.
The Application Of Laser Processing Technology
1 Laser heat treatment technology
When the laser beam moving at a certain speed irradiates the metal surface, the surface metal absorbs energy and then heats up rapidly. When the light spot moves, the base material absorbs the heat of the surface layer, so that the temperature of the surface metal drops rapidly at a very high speed, which is different from conventional quenching. Self-quenching. Due to the extremely high cooling rate of self-quenching, a surface modification layer with a special microstructure can be obtained, which has a good effect on improving the hardness, wear resistance, corrosion resistance and fatigue resistance of the metal. Laser heat treatment is the earliest developed laser processing technology, and now it has formed a relatively complete theory and engineering application technology. For carbon steel and alloy structural steel that can be phase-transformed, laser surface quenching can produce higher hardness than traditional quenching, and even has a certain strengthening effect on some low-carbon steel materials that do not have hardenability. Figure 1 shows the laser quenching effect of 35CrMo steel.
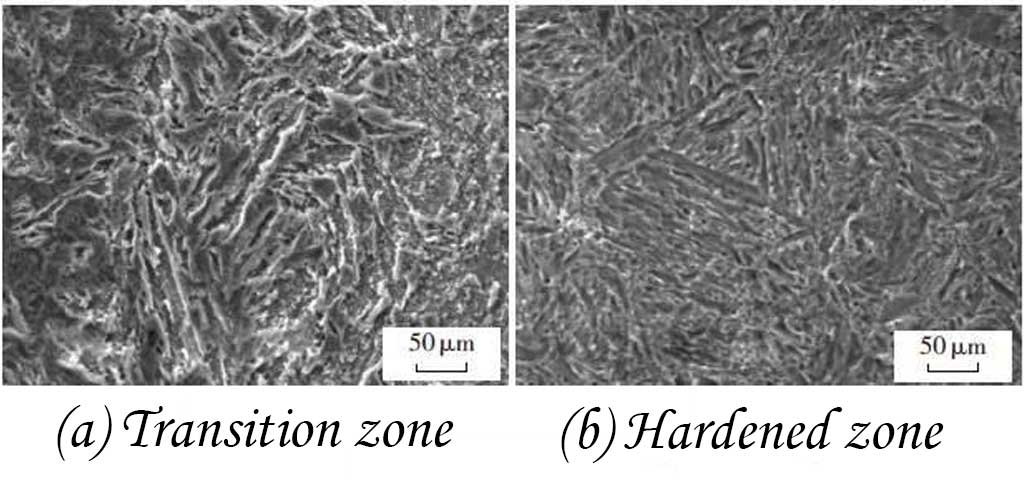
2 Laser surface remelting technology
Applying a higher laser power density than laser surface quenching to irradiate the metal surface will melt the surface metal. After the spot moves, the base metal absorbs heat to rapidly solidify the metal liquid in the molten pool, forming a strongly chilled solid solution with extremely fine grains and supersaturation. Microstructure, due to the effect of fine grain strengthening and solid solution strengthening, can significantly improve the hardness and wear resistance of the material surface. Studies have shown that through remelting, the hardness of aluminum alloys can be increased by 30% to 100%, which is the simplest laser processing technology, but the range of strengthening is limited. For aircraft structural aluminum alloy profiles and plates that are subjected to alternating loads, the fatigue quality of the overheated layer that must exist after laser remelting is the key to determining the service life of the structure. The effect of fatigue properties. For structural steel materials, the effect of remelting and hardening is significant. Figure 2 shows the microstructure of 45# steel in different regions of laser remelting. It can be seen from Figure 2 that the microstructure is converted from pearlite to martensite after laser remelting.
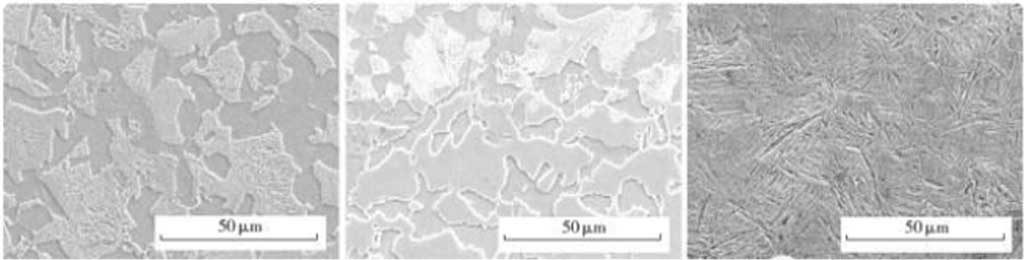
3 Laser surface alloying technology
When the laser melts the surface metal, the designed alloying elements are added to the molten pool, and the alloyed layer with the required properties can be obtained on the surface without changing the composition of the base alloy. This technology is very beneficial to the manufacture of parts requiring special performance, and can produce metal or composite parts with non-uniform materials and non-uniform properties that cannot be achieved by traditional manufacturing techniques. Due to the extremely high cooling rate of the molten pool during the laser surface alloying process, alloys and microstructures that are difficult to achieve under traditional metallurgical process conditions can be formed. Therefore, an alloyed layer with high hardness, wear resistance, good corrosion resistance and heat resistance can be formed as required. For aluminum alloys, laser surface alloying processes of various alloy systems have been tested, such as Cu, Fe, Si, Ni, Cr, WC, SiC, etc. Among them, the nickel-based alloy layer is dispersed with intermetallic compounds AlNi and Ni3Al phases, which have high hardness and wear resistance, but the alloy layer is brittle and has cracking phenomenon. There must be an alloying metallurgical process between the matrix and the cladding material at the interface of laser cladding. Figure 3 is the scanning curve of the alloying composition of the aluminum alloy.
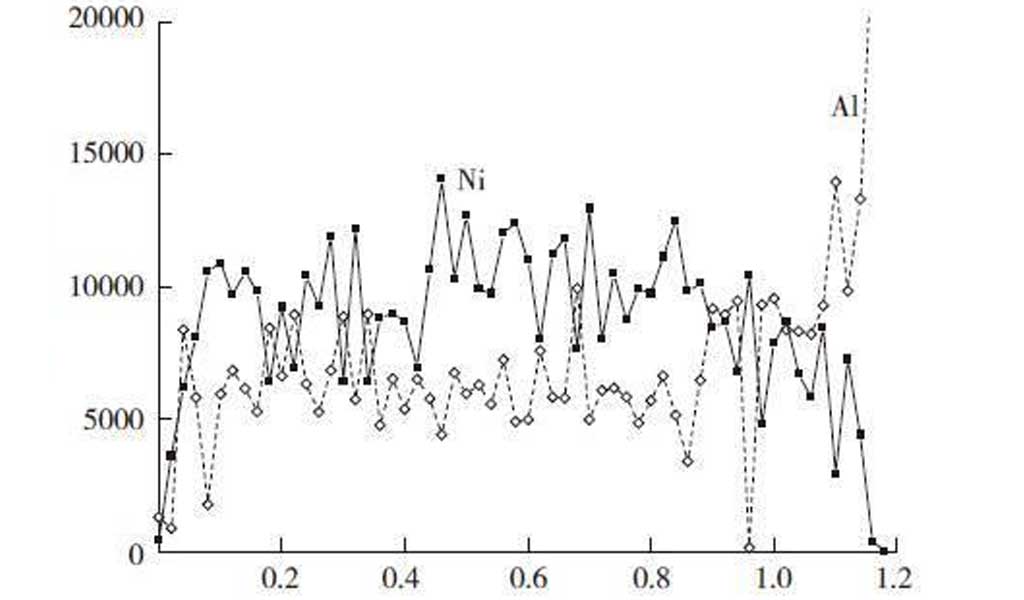
4 Laser welding technology
The high energy density of the laser can melt and vaporize the surface metal in an instant, which is an ideal energy source for welding, and an ideal weld with narrow width and small heat-affected zone can be obtained. At present, high-quality welds have been obtained in a variety of metals and under a variety of conditions, and it is a widely used laser processing technology. Laser welding is the most promising welding technology for deformed aluminum alloys with high strength and poor welding performance such as LY12 (2024) and LC4 (7075) commonly used in aircraft structures. Using continuous CO2 laser, Nd:YAG laser, semiconductor laser, and excimer laser as energy sources, researchers at home and abroad have achieved ideal welding of 2024, 7075, 6063, 5083, 5052 and other alloy plates with different process parameters, and carried out finite element analysis. Therefore, laser welding technology has a very broad development prospect in the field of aircraft structural repair, especially in the field of aircraft structural damage repair. Because of its fast welding speed and simpler construction than riveting, it is an ideal technology to replace the riveting process. For titanium alloys, superalloys and stainless steel materials, laser is an ideal welding energy source, which can form welds with small heat-affected zone, small welding stress, small deformation and high performance.
5 Laser Cutting Technology
Lasers can cut almost all materials, and can obtain high-quality kerf surfaces in different material cutting by choosing gasification, melting, oxidation cutting methods and process parameters. Laser cutting has small deformation, high precision, material saving, high cutting efficiency and little environmental pollution. In the field of aircraft structural damage repair, the application of laser cutting technology can quickly remove damaged and deformed structures, create construction conditions for the implementation of repairs, and save valuable time.
6 Laser shock strengthening technology
Laser shock strengthening technology is another material surface strengthening technology after shot peening and cold extrusion. When the extremely high power density and short pulse laser reaches the surface of the material, the material with low melting point will rapidly vaporize, and the surface material is equivalent to The instantaneous gasification of the explosion produces a shock wave that has a strong mechanical effect on the substrate. Therefore, a low-melting-point metal or non-metallic coating is preset on the surface of the material to be treated. After laser irradiation, the surface hardness of the material (more than 5 times) and surface compressive stress can be greatly improved, which can greatly improve the fatigue resistance of the substrate. have a significant effect. The research shows that the main mechanism of laser shock strengthening is that the dislocation density of the metal surface grains is uniform and greatly increased during the gasification shock wave, and the interaction of dislocation delivery and entanglement forms a uniform surface residual compressive stress, thereby reducing fatigue crack propagation. speed, and the life expectancy can be increased by more than 20% to 300%. It can be seen that this technology has broad application prospects, especially in special parts (such as rivet holes) that cannot be strengthened by traditional processes such as small holes, welds, grooves and other common aviation structures. Laser shock strengthening is a new technology that cannot be replaced by other processes. .
7 Laser surface cladding technology
Laser surface cladding is to pre-coat a layer of metal, alloy or ceramic powder on the surface of the metal substrate. During the laser remelting, the energy input parameters are controlled so that the additive layer is fully melted to make the substrate micro-melting and the substrate to achieve metallurgical bonding, thereby An additional cladding layer with the desired properties was obtained, and Fig. 4 shows the SEM analysis of the laser cladding layer.
Compared with laser surface alloying, this process avoids excessive melting of the matrix and maintains the properties and functions of the materials in the cladding layer. It is a very important surface modification technology, and it can be applied to aircraft structures to obtain huge technical benefits. This method has attracted extensive attention after it was successfully applied to turbine blades of large passenger aircraft engines in 1981, and has become one of the research focuses of laser surface modification at home and abroad. Aluminum alloy material has low hardness, and it is of great significance to clad a hard wear-resistant layer on its surface. But the difficulty is that aluminum alloys have high thermal conductivity and low melting point. The melting point of the cladding layer is usually much higher than that of the aluminum alloy matrix, so it is difficult to form an alloyed layer with low dilution and stable performance. Practice has proved that through strict control of laser process parameters, alloy surface layers that require functions and characteristics can be realized. Various alloy cladding experiments have been successfully carried out on aluminum alloy surfaces at home and abroad. Toyota has changed the engine valve seat from the original mosaic structure to direct cladding, which greatly improves the wear resistance, lubricity and thermal conductivity of the valve seat. In foreign countries, laser cladding is not only used for surface modification, but also for the repair of mechanical parts. Therefore, laser rapid prototyping technology (DMD, DMP) has been developed and studied for the direct manufacture of mechanical parts. For surface wear and corrosion damage of mechanical parts, laser multilayer cladding can be used to restore their size and shape. The US Navy has established a special laser cladding repair laboratory to successfully repair the corrosion damage of aluminum alloy structural parts of underwater equipment. For the common corrosion damage of naval aircraft, laser cladding technology has huge development and application prospects.
The Development Prospect Of Laser Processing Technology
Laser processing technology has largely adapted to the extensive needs of titanium alloy cutting, titanium alloy welding, and composite material cutting in modern aircraft repairs. As long as the power density of the laser and the speed of the spot movement are adjusted, a variety of processing purposes can be achieved, which is unmatched by traditional processing techniques. It can become the first-choice advanced emergency repair technology to make up for the shortcomings of traditional emergency repair technology, and it is also a promising emergency repair technology.
The surface modification technology of laser processing has been applied in the field of aero-engine manufacturing. Using laser cladding technology to cast the crown of aero-engine turbine blade, the axial dimension of the blade was successfully restored. In the field of aircraft structural repair, laser processing technology has begun to receive attention, and Canada has listed it as a technology of great value. However, for aluminum alloy, the main material of aircraft structure, laser processing is difficult due to its low boiling point, fast heat transfer, and low absorption rate of laser light, which is a recognized problem in the field of laser applications at home and abroad. If it can be successfully applied, it will have very high academic value and engineering application value.
In the research of laser repair technology, our navy has been at the forefront of the country. In 2006, the “mobile laser repair system” developed by the Naval Aviation Engineering Institute and other scientific research institutes has begun to distribute troops, creating conditions for the application of laser technology to aircraft structure repair and even wartime repair.