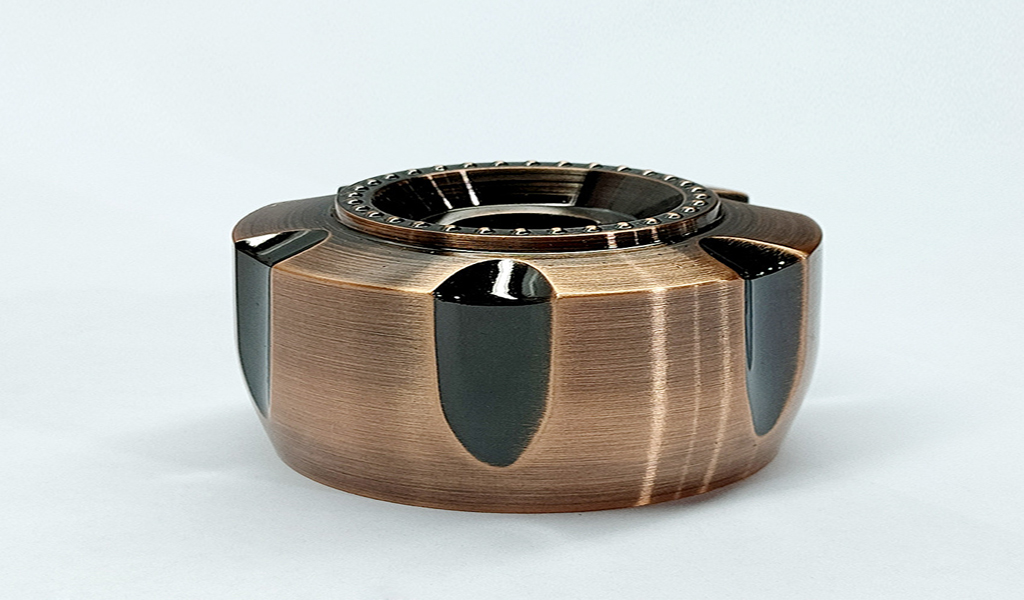
Automobile stamping parts indicate that stamping is mainly classified according to the process, which can be divided into two categories: separation process and forming process. The separation process is also called blanking, and its purpose is to separate the stamping parts from the sheet along a certain contour line, while ensuring the quality requirements of the separation section. The purpose of the forming process is to plastically deform the sheet without breaking the blank to make a workpiece of the desired shape and size. In actual production, multiple processes are often integrated into a workpiece. Punching, bending, shearing, stretching, bulging, spinning, and straightening are several main punching and separation processes.
Blanking is a basic stamping process that uses a die to separate materials. It can be directly made into flat parts or prepared for other stamping processes such as bending, deep drawing, forming, etc. wait. Blanking is widely used in automotive, household appliances, electronics, instrumentation, machinery, railways, communications, chemicals, light industry, textiles and aerospace and other industrial sectors. Blanking fabrication accounts for about 50% to 60% of the entire stamping fabrication process. Forming process bending: A plastic forming method for bending metal sheets, pipes and profiles into a certain angle, curvature and shape. Bending is one of the main processes widely used in the production of stamping parts. The bending of metal materials of automobile stamping parts is essentially an elastic-plastic deformation process. After unloading, the workpiece will produce elastic recovery deformation in the direction, which is called rebound. Springback affects the accuracy of the workpiece and is a technical key that must be considered in the bending process.
Deep drawing: Deep drawing, also known as drawing or calendering, is a stamping method that uses a die to make a flat blank obtained after blanking into an open hollow part. Thin-walled parts with cylindrical, stepped, conical, spherical, box and other irregular shapes can be made by deep drawing. When combined with other stamping and forming processes, parts with extremely complex shapes can also be produced. In stamping production, there are many types of deep drawing parts. Due to their different geometrical characteristics, the position of the deformation zone, the nature of the deformation, the distribution of the deformation, and the stress state and distribution law of each part of the billet are quite different, even in essence. Therefore, the determination methods of process parameters, the number and sequence of processes, and the principles and methods of mold design are different. According to the characteristics of deformation mechanics, various deep-drawing parts can be divided into four types: straight-wall revolving body (cylindrical part), straight-wall non-revolving body (box-shaped body), curved surface revolving body (surface-shaped part) and curved non-revolving body. type.
The drawing is to apply tension to the sheet through the drawing die, so that the sheet produces uneven tensile stress and tensile strain, and then the bonding surface between the sheet and the drawing die gradually expands, and the auto parts are completely connected to the drawing model surface. fit. The applicable object of the pulling shape is mainly the hyperbolic skin with certain plasticity, large surface area, gentle and smooth curvature change, and high quality requirements (accurate shape, smooth streamline, and stable quality). Due to the relatively simple process equipment and equipment used in drawing, the cost is low and the flexibility is large; but the material utilization rate and productivity are low.
Spinning is a metal rotary machining process. During the fabrication, the blank is actively rotated with the spinning die or the spinning head is actively rotated around the blank and the spinning die. body parts.
Shaping is to use the established abrasive shape to carry out secondary dressing to the shape of the product. Mainly reflected in the pressure plane, spring feet and so on. Refabrication is used when some materials have elasticity and cannot guarantee the quality of one-time molding.
Bulging is a fabrication method that uses a mold to stretch and thin the sheet to increase the local surface area to obtain parts. Commonly used are undulating forming, bulging of cylindrical (or tubular) blanks and stretch forming of flat blanks. Bulging can be achieved by different methods, such as die bulging, rubber bulging and hydraulic bulging.
Flanging is a plastic fabrication method that bends the edge of the sheet blank or the narrow strip area of the edge of the prefabricated hole on the blank along a curve or straight line into a vertical edge. The flanging of automobile sheet metal parts is mainly used to strengthen the edge of the part, remove the trimming and make the part on the part that is assembled and connected with other parts or a three-dimensional part with complex and special shape and reasonable space, and at the same time improve the rigidity of the part. It can also be used as a means to control cracks or wrinkles when forming large sheet metal. Therefore, it has been widely used in industrial sectors such as automobiles, aviation, aerospace, electronics and household appliances.
Narrowing is a stamping method that reduces the diameter of the open end of the drawn flangeless hollow part or tube blank. The diameter change of the workpiece end before and after the necking should not be too large, otherwise the end material will wrinkle due to severe compression deformation. Therefore, shrinking the neck from a larger diameter to a small diameter often requires multiple shrinking.
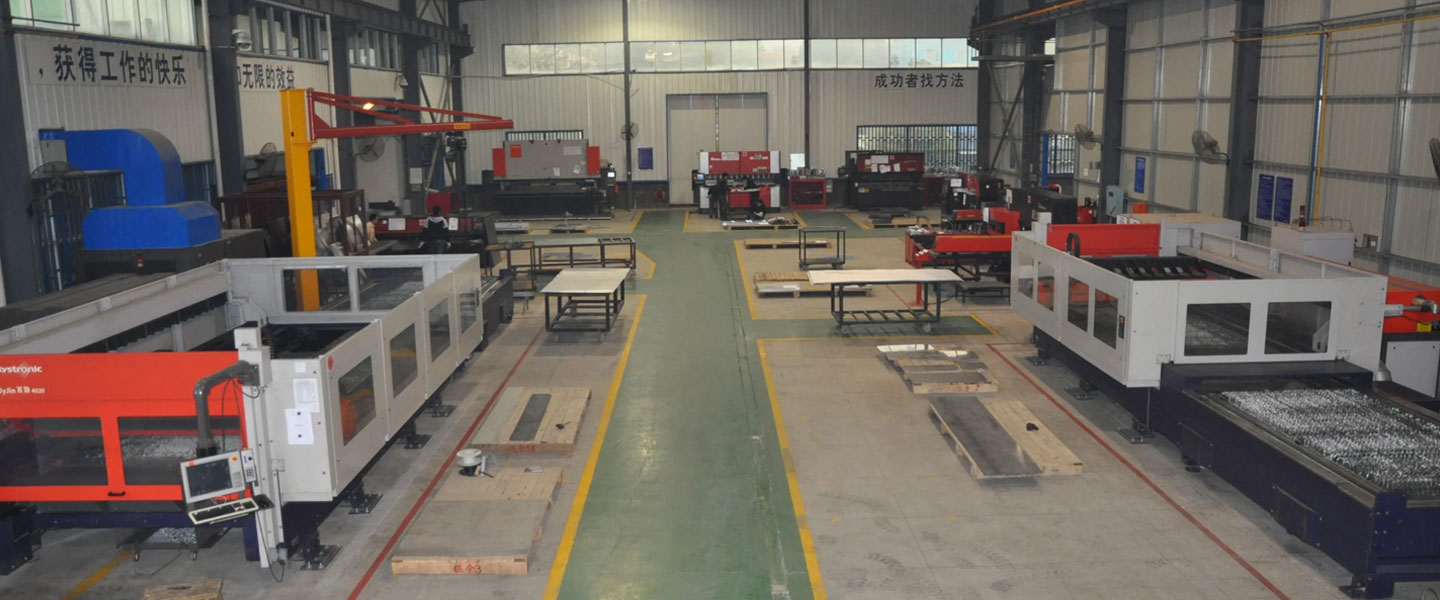
Pintejin Sheet Metal shop offers a cost-effective solution for a wide range of industries with our custom metal stamping and custom sheet metal fabrication capabilities. Our stampnig operations include a variety of sheet-metal forming manufacturing processes, such as punching, blanking, embossing, bending, flanging, and coining. Our professional, experienced and well-trained engineers can execute the complex metal stamping operations with precision and accuracy.
No matter what your metal fabrication needs are, Pintejin can offer the right solution: from single sheet metal part or sub-assembly of stamped metal parts to turnkey solutions for mechanical and electrical assemblies. We have the technology, equipment and the experience to fabricate customised metal products from aluminium sheet metal fabrication, steel, zinc plated steel, stainless steel sheet metal fabrication, brass and copper. Designs that require CNC machining of surfaces or components can be accommodated. We can supply polished, galvanized, zinc coated or powder coated finishes for any sheet metal work or stamped metal components. Coupled with our accurate and reliable metal fabricating equipment, we guarantee precision and repeatability in custom sheet metal work. You’ll be taking advantage of the best sheet metal fabrication china can produce.