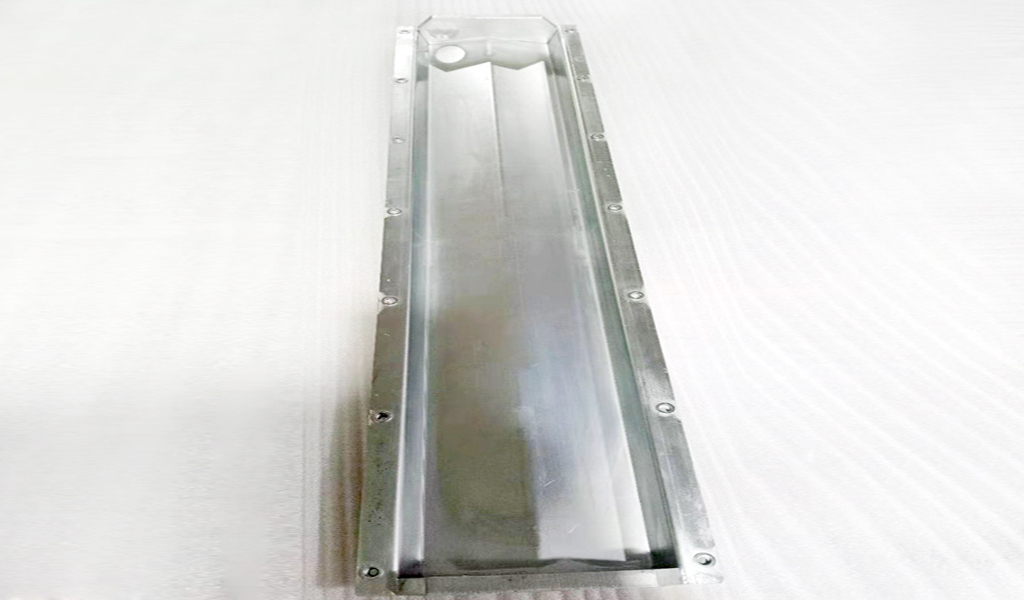
Sheet metal parts have the characteristics of being thin and easy to form, and can be formed into parts of various shapes. With the application of welding, assembly, riveting and other processes, the possibility of realizing multiple structures is given to the product. At the same time, these characteristics also cause the sheet metal parts to be more or less deformed to different degrees during the fabrication, such as bending deformation, torsional deformation, and concave-convex deformation. These deformations change the size or shape of the entire component, causing quality problems. However, the production process of sheet metal parts has its inherent laws. For the same type of products, according to the existing equipment, manpower, etc., the fabrication sequence can be flexibly adjusted, and a reasonable fabrication technology can be given. Therefore, choosing the correct process route is an effective measure to prevent and solve such problems.
Basic principles of sheet metal routing
The formulation of the process route must be combined with the shape of the product and the company’s existing fabrication equipment to meet the product quality requirements and ultimately achieve the goal of maximizing economic benefits. The formulation of the general process route of automobile stamping parts can follow the following principles: (1) to meet the product quality requirements, (2) to be economical in the product process route, (3) to provide optimization for subsequent processes, (4) to facilitate fabrication. Technologists’ focus on quality comes from their grasp of product structure, functionality and appearance, as well as their proficiency in equipment fabrication capabilities. Considering the relationship between the cumulative error of the whole machine, optimizing the product fabrication method to reduce the fabrication difficulty, and setting a relatively stable process route during mass production are three directions that need to be considered in process compilation.
Optimize product fabrication methods
The optimization of the fabrication method lies in the adjustment of its fabrication sequence or the improvement of the process, which is analyzed and explained by a simple example. For example, if a certain door panel is unfolded, the quality and time can be mainly considered when fabrication a single door panel. The general process plan is: shearing machine cutting → punching machine punching shape and inner hole → bending machine bending → welding four corners. Such a process plan saves time and effort, but if mass-produced, the damage to the punching tool will be aggravated, which will greatly increase the maintenance cost of the machine tool. In addition, if the programming program of automobile sheet metal parts is slightly wrong, it will cause irreparable losses. Since the function of the special-shaped part of this kind of door panel is to install the door suction, the following fabrication scheme is usually adopted when producing this kind of door panel in large quantities: cutting by shearing machine (three small pieces of door suction are cut separately) → punching the inner hole by punching machine → cutting angle → folding Bed folding test → Weld the four corners and the three door suction pieces. The improvement of this scheme not only saves the cost of raw materials and equipment maintenance, but also greatly reduces the error rate of programming.
The fabrication technology of sheet metal auto parts is a relatively complex problem. This article briefly expounds the basic principles of process setting of general sheet metal parts, in order to find out the basic method of process setting. In short, as an engineer, you should establish a cost concept, integrate cost into the process, and look at the process from an overall perspective. setting process.
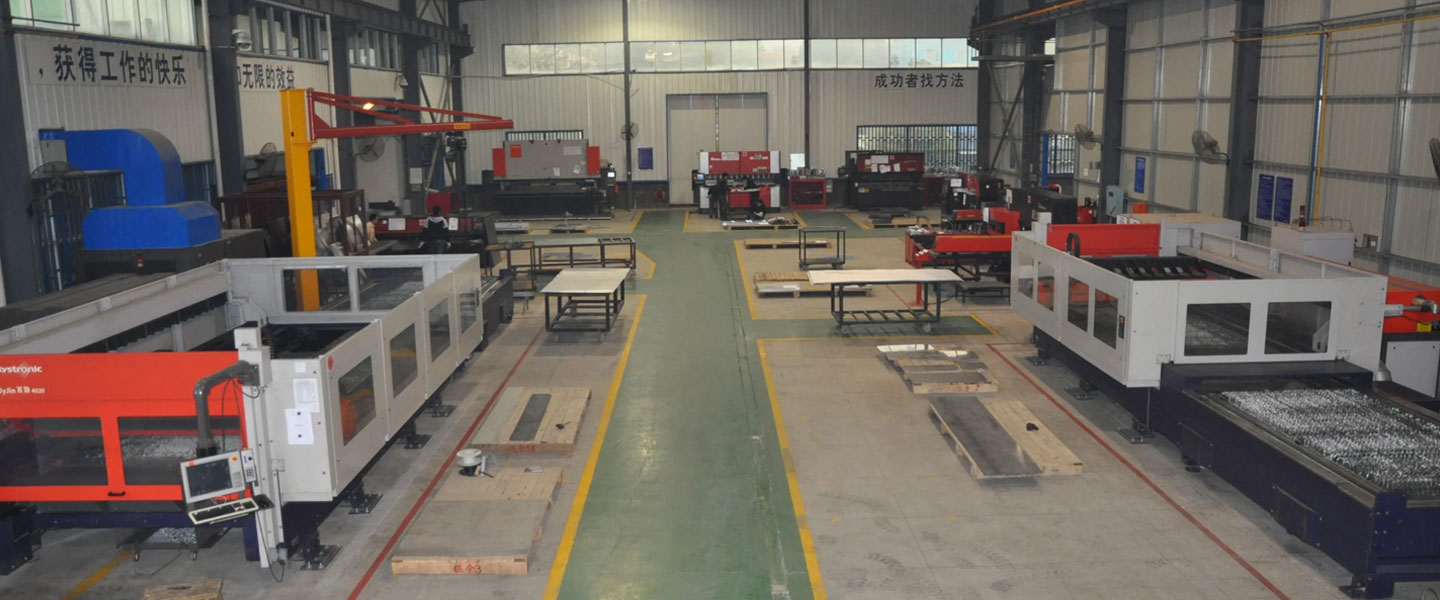
Pintejin Sheet Metal shop offers a cost-effective solution for a wide range of industries with our custom metal stamping and custom sheet metal fabrication capabilities. Our stampnig operations include a variety of sheet-metal forming manufacturing processes, such as punching, blanking, embossing, bending, flanging, and coining. Our professional, experienced and well-trained engineers can execute the complex metal stamping operations with precision and accuracy.
No matter what your metal fabrication needs are, Pintejin can offer the right solution: from single sheet metal part or sub-assembly of stamped metal parts to turnkey solutions for mechanical and electrical assemblies. We have the technology, equipment and the experience to fabricate customised metal products from aluminium sheet metal fabrication, steel, zinc plated steel, stainless steel sheet metal fabrication, brass and copper. Designs that require CNC machining of surfaces or components can be accommodated. We can supply polished, galvanized, zinc coated or powder coated finishes for any sheet metal work or stamped metal components. Coupled with our accurate and reliable metal fabricating equipment, we guarantee precision and repeatability in custom sheet metal work. You’ll be taking advantage of the best sheet metal fabrication china can produce.