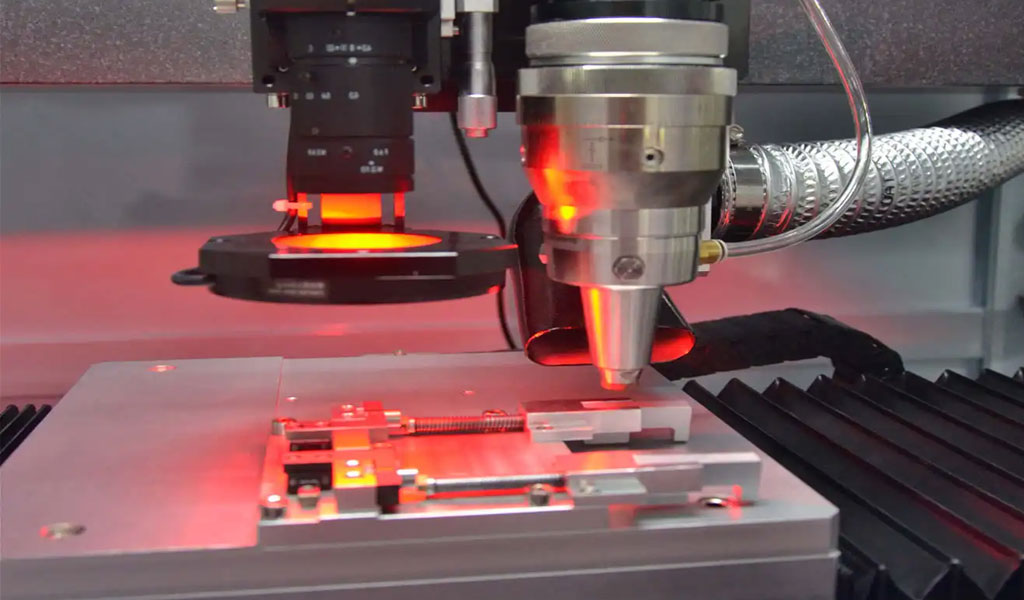
CNC Drilling Service In China
Drilling is the cutting process in which the workpiece does not move, making the cutter move, aligning the cutter center with the hole center, and making the cutter rotate. CNC Drilling is primarily done on CNC machines including CNC milling machines and lathes.
Pintejin use various types of CNC drilling machines including upright, bench, radial, which allows us to drill holes of both simple and complex patterns up to 7 cm in diameter.
Currently, our non-standard sheet metal parts with drilling are exported to America, Canada, Australia, United Kingdom, Germany, France, Sout Africa, and many other countries all over the world. We are ISO9001-2015 registered and also certified by SGS.
Our custom sheet metal service with drilling provides durable and affordable parts that meet your specifications for automotive, medical, aerospace, electronics, food, construction, security, marine, and more industries. Fast to send your inquiry or submit your drawings to get a free quote in the shortest time.Contact us or Email [email protected] to see how our people, equipment and tooling can bring the best quality for the best price for your custom sheet metal fabrication project.
-
Micro Laser Cutting vs Micro CNC Machining
-
What are the repair methods for car body sheet metal damage?
-
How to distinguish the pros and cons of automotive sheet metal parts on the market?
-
How about the application of cold stamping process in automobile stamping parts?
-
The principles that need to be followed in the fabrication of precision metal automobile stamping parts?
-
What are the principles for the selection of die for automotive stamping parts?
The Selection Of Hole Drilling Methods And Steps
The applicable range of hole drilling is as follows:
- Machining solid blanks of unhardened steel and cast iron, also available. For machining non-ferrous metals (but with poorer roughness), hole diameter <1 5mm~20mm
- Machining solid blanks of unhardened steel and cast iron, also available. For machining non-ferrous metals (but with poorer roughness), hole diameter > 15mm~20mm
- Various materials except hardened steel, blanks with cast or forged holes
Drilling Plan | Accuracy Class | Surface Roughness Ra |
---|---|---|
Drill | 11~13 | 50~12.5 |
Drill-Ream | 9 | 3.2~1.6 |
Drill A Rough Reaming (Expansion) – Fine Reaming | 7~8 | 1.6~0.8 |
Drill-Expand | 11 | 6.3~3.2 |
Drill – Expand – Ream | 8~9 | 1.6~0.8 |
Drill-Expand-Rough Reaming-Fine Reaming | 7 | 0.8~0.4. |
Rough Boring (Reaming) | 11~13 | 6.3~3.2 |
Rough Boring (Reaming) – Semi-Finishing | 8~9 | 3.2~1.6 |
Rough Boring – Semi-Fine Boring | 6~7 | 1.6~0.8 |
Drilling, Countersinking and Reaming Canned Cycle Commands
In CNC machining, some machining action cycles have been typicalized. For example, the actions of drilling and boring are hole position plane positioning, rapid introduction, work feed, rapid retraction, etc. In this way, the series of typical machining actions have been pre-programmed and stored in memory, and can be used with G codes. – One block call, which simplifies programming. This C code that contains a typical action loop is called a loop instruction.
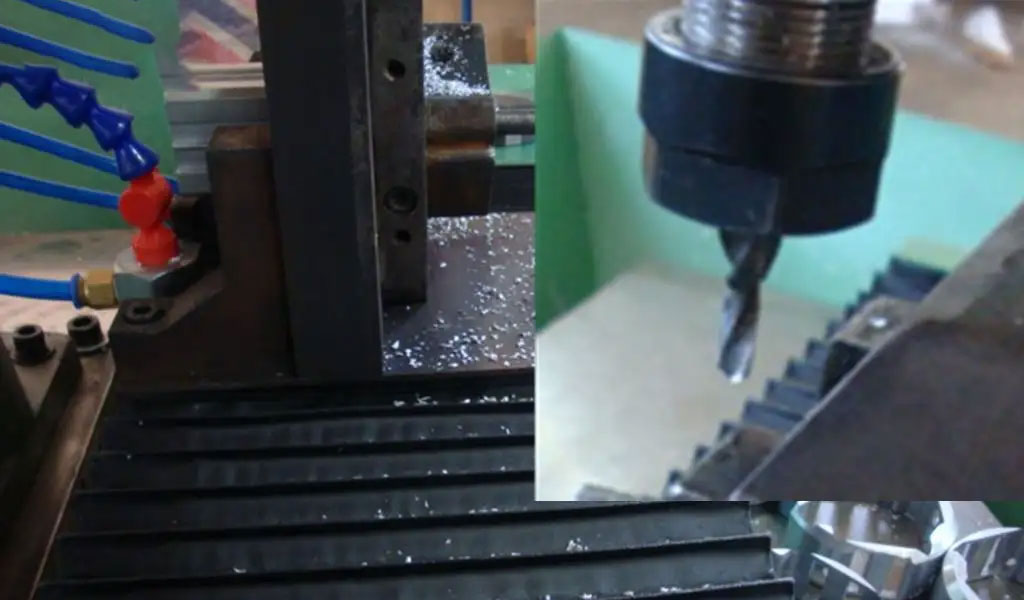
High Speed Deep Hole Drilling Cycle G73 And Deep Hole Drilling Cycle G83
Format G73X_Y_Z_R_Q_F_; This canned cycle is used for the intermittent feed of the Z axis, which is beneficial to chip breaking, and is suitable for deep hole machining, reducing the amount of tool retraction and enabling high-efficiency machining. The Q value is the feed depth (Q) each time, and Q is the incremental value in the command. The tool retraction is fast, and the retraction amount d each time, d is set by the system parameters. . Example: G98 G73 X10 Y20 Z-60 R5 Q10 F50
The difference from G73 is that it returns to the safety plane height after each infeed, which is more conducive to chip removal when drilling deep holes.
Improved Sheet Metal Drilling Process In Pintejin
Combination machine tool is a typical processing machine, it is used to process various parts like other machine tools. In the past, universal machine tools were widely used in production, but with the development of production, universal machine tools are increasingly unable to adapt to large-scale and integrated production. The cylinder block and gear box of the automobile cannot meet the design requirements well if they are processed by the universal machine tool. In this case, sheet metal drilling machine came into being.
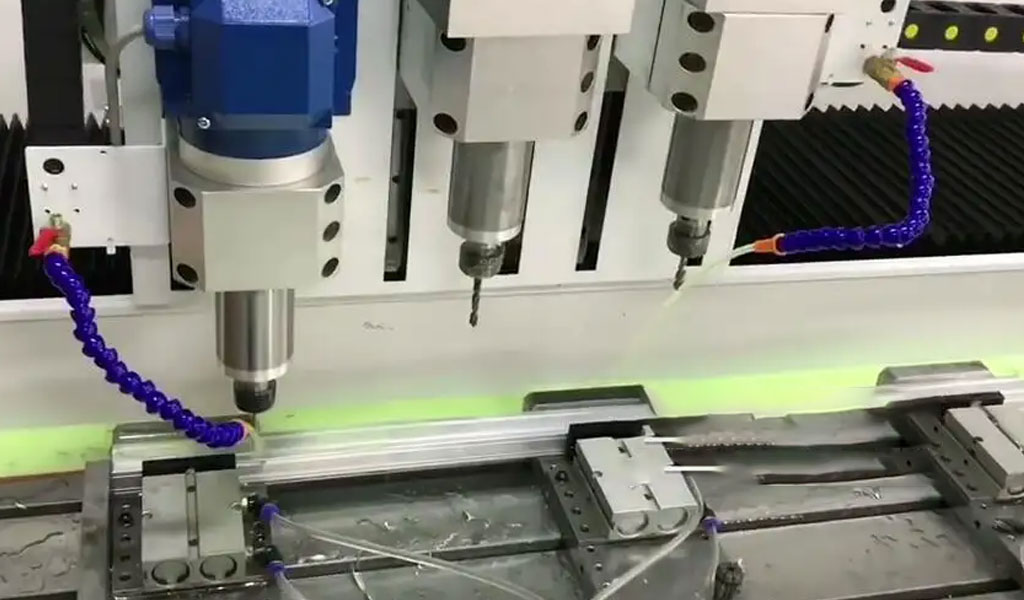
In the design of the sheet metal drilling machine, after the demonstration of the process plan, the selection of the processing method, and the determination of the model and configuration form, it is the overall design part of the combined machine tool. The specific work of the overall design is to compile “three pictures and one card”. That is to draw the processed parts diagram, processing schematic diagram, machine tool connection dimension diagram, and compile productivity calculation card. In this part, the processing method, tooling and clamping form, and cutting amount should be determined.Next is the design of the spindle box. The specific design steps are: draw the original basis for the design of the spindle box: determine the spindle structure and draw up the transmission system;
And the supplementary machining drawing of the headstock.The next step is to design the machine tool fixtures. The most important thing is to design suitable fixtures according to the structural characteristics and processing methods of the parts to be processed. At the beginning, several different schemes can be planned according to different design ideas. Finally, select the most suitable one, and then calculate the clamping force and positioning error on this basis, and finally draw the fixture assembly drawing.
Drilling holes in the solid part of the workpiece with a drill is called drilling. Drilling is rough machining, the achievable dimensional tolerance level is IT13~IT11, and the surface roughness value is Ra50~12.5μm. Due to the long length of the twist drill, the small diameter of the drill core and the poor rigidity, and the influence of the chisel edge, the drilling has the following technological characteristics:
- The drill is easy to deflect. Due to the inaccurate centering of the chisel edge, the drill bit is easy to be deflected when cutting in; and the rigidity and guidance of the drill bit…
- The aperture is easy to expand