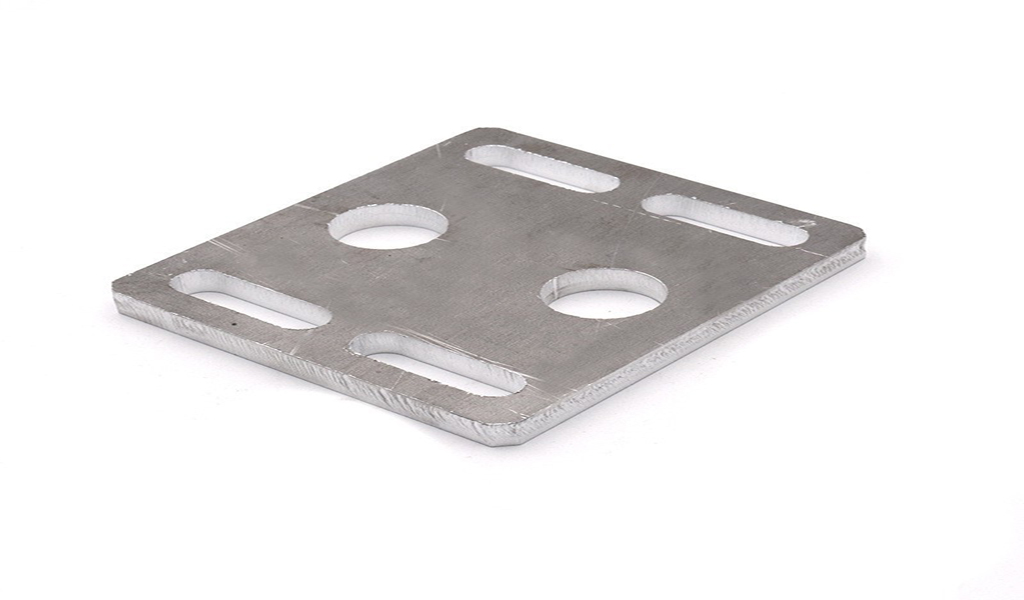
1. Basic coating of ferrous sheet metal
The ferrous metal sheet is easily oxidized and corroded gradually due to factors such as exposure to air or contamination of harmful substances, resulting in yellow rust spots and damage to the original coating layer. Especially in the parts processed by hammering, welding and other processes in the process of sheet metal work, it is more likely to damage the original coating protective layer and accelerate corrosion. Even if the paint film is sprayed, the paint film will quickly mix with The base coat comes off together. At this time, a thorough coating treatment must be carried out again.
Use a wire brush or iron sandpaper to polish and clean the surface of the ferrous metal sheet. The car sheet metal parts can use the widely used cleaning tool – nylon grinding disc to thoroughly grind and clean the metal surface. When dismantling and repairing the body (especially the accident car), the folded edges and lap joints of the sheet metal should be sprayed with a spray liquid specially used for rust removal, paint removal, and removal of oxidized slag and dirt before and after metal welding, or use A rust-proof primer with good rust resistance.
2. Basic coating of the joint surface of sheet metal parts
If the repaired car body is not subjected to anti-corrosion treatment, the cracks of the joint surface of the sheet metal parts will be oxidized and corroded due to the existence of various impurities and water vapor within a year or two, which will affect the strength of the welded joints. Therefore, welding zinc should be sprayed in time. agent.
Welding zinc agent (zinc-rich coating) is a new material specially used for anti-oxidation and rust protection of the joint surface of sheet metal parts. It has good electrical conductivity, high temperature resistance, and electrochemical cathodic protection. It can form a rust-proof protective layer between the welding joint surfaces of sheet metal parts, improve the ability of the parts around the solder joints to not be rusted, protect the solder joints, and ensure The strength of the repaired body is not inferior to the original body.
3. Basic coating of plastic welding
Although the surface of the welded seam, solder joint and repaired steel plate has been polished and cleaned, there are still countless micro-invasive and irregular small bumps that are invisible to the naked eye, which are mixed with countless oxides, impurities, water vapor, etc. Ordinary putty or anti-rust paint has anti-rust function, but it can only prevent the intrusion of external rust and play a temporary sealing role. As long as it is exposed to moisture and other harsh environments, defects will appear quickly. Such as epoxy primer can play an effective protective role.
Epoxy primer is suitable for smearing on the seams of panels or lap joint surfaces after welding, grinding, heating and quenching, etc. It is a good rust inhibitor. Generally, the feather edge of the paint film on the edge of the repair part (that is, the groove of the paint film) is prepared, and the epoxy primer is applied after cleaning the surface, which can ensure that the panel after various treatments can be used for a long time. No rust, even if there is rust originally, it will prevent the expansion of the rust range.
4, the basic coating of the joints
For metal sheets that are directly coated without special sheet metal sealing treatment, the seams of auto parts outside the welding or lap joint surface will be eroded by various sundries, such as oil, coolant, sewage, etc. It deforms and cracks due to the vibration of uneven road surface, the anti-rust sealing line of interface is broken, and the function is lost. It is an indispensable process to apply special sheet metal sealant to the meeting and other parts of the sheet.
Sheet metal sealant is a non-corrosive polyurethane PU structural adhesive that can caulk, cover, bond and seal, and sometimes replace welding without damaging the paint. It has extremely strong adhesion, high strength after curing, strong and reliable, can enhance the strength of single-piece components and thin-shell body, and can maintain welding or lap joints, especially the inside and outside of wheel arches, chassis, trunk, and cockpit. Anti-corrosion function of the base plate and engine compartment.
5. Basic coating in the cavity of the box section member
During the overhaul of the car body, it will be found that the original sheet metal parts in the cavity of the box section member have been rusted and repaired due to accidents before, and the steel plate has become thinner and penetrated. infiltration and continuous expansion. These van-type cross-sectional members are often the main load-bearing members of the monolithic body, and they will have an important impact on the crashworthiness and durability of the car. Therefore, anti-rust treatment must be done for the box section or the cavity of the bag-shaped member.
Anti-rust protection wax inside the body is a good assistant for cavity protection. It has excellent permeability and can easily penetrate into all corners and joints. Automobile stamping parts are resistant to moisture and drainage, which can prevent the body from being sprayed with paint. The cavity is rusted and worn out, preventing rust inside the welding part of the body plate. In addition, when coating the inner surface of these plates, special spray bars and nozzles can also be used for coating. Ensure final repair quality.
6. Other functions of body base coating
1. Anti-vibration treatment at the junction of the skeleton and the skin
After the engine cover and luggage compartment cover are disassembled, body sealant must be filled between the skin and the inner lining before closing. This allows the folded skin to stick to the inner lining, otherwise the skin will loosen, there will be abnormal noises when opening or closing the hood or luggage compartment lid, and resonance sounds may also occur during driving.
2. Insulation, moisture-proof and noise-proof treatment of the underbody
On the upper surface of the body floor, the metal surface of the sheet metal components and the welding parts must be polished and sprayed with anti-rust primer. After drying, the sound insulation lining or sound insulation pad of the same type of the original body must be pasted to absorb the vibration and noise caused by the movement of the vehicle. generated noise.
For the lower surface of the body floor (the side outside the body), the exposed and repaired metal surface should be thoroughly polished and cleaned, the surrounding original paint that is about to fall off should be completely removed, and 1 to 2 layers of anti-rust primer should be sprayed. After drying, add MSP body sealant or similar products to the joint surface and the gap, and then spray the anti-rust and anti-collision primer. The underbody treated in this way can enhance the anti-corrosion performance and reduce the impact of stone hitting noise on the cabin.
With the continuous intensification of competition in the automobile market and the increasing updating of automobile manufacturing and repair technologies, the basic coating process has attracted great attention from automobile manufacturers and maintenance service personnel. A wide variety of coating materials with complete specifications and good functions will undoubtedly further promote the improvement of maintenance quality and prolong the service life of automobiles.
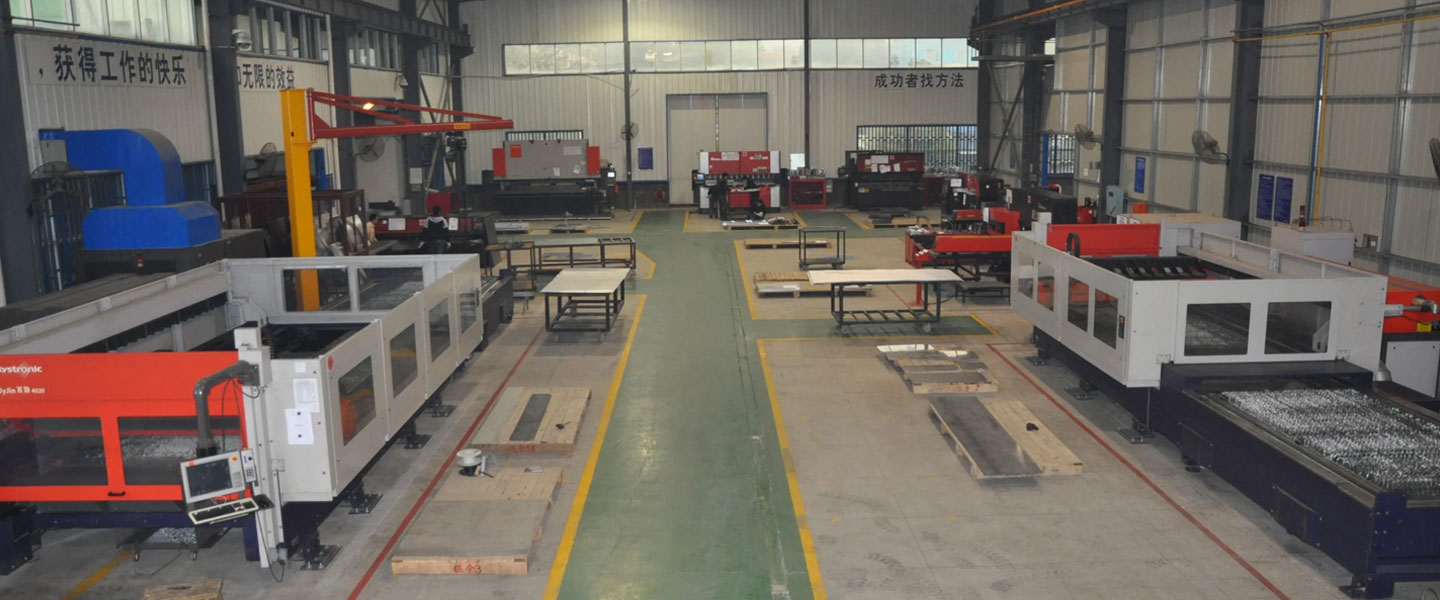
Pintejin Sheet Metal shop offers a cost-effective solution for a wide range of industries with our custom metal stamping and custom sheet metal fabrication capabilities. Our stampnig operations include a variety of sheet-metal forming manufacturing processes, such as punching, blanking, embossing, bending, flanging, and coining. Our professional, experienced and well-trained engineers can execute the complex metal stamping operations with precision and accuracy.
No matter what your metal fabrication needs are, Pintejin can offer the right solution: from single sheet metal part or sub-assembly of stamped metal parts to turnkey solutions for mechanical and electrical assemblies. We have the technology, equipment and the experience to fabricate customised metal products from aluminium sheet metal fabrication, steel, zinc plated steel, stainless steel sheet metal fabrication, brass and copper. Designs that require CNC machining of surfaces or components can be accommodated. We can supply polished, galvanized, zinc coated or powder coated finishes for any sheet metal work or stamped metal components. Coupled with our accurate and reliable metal fabricating equipment, we guarantee precision and repeatability in custom sheet metal work. You’ll be taking advantage of the best sheet metal fabrication china can produce.