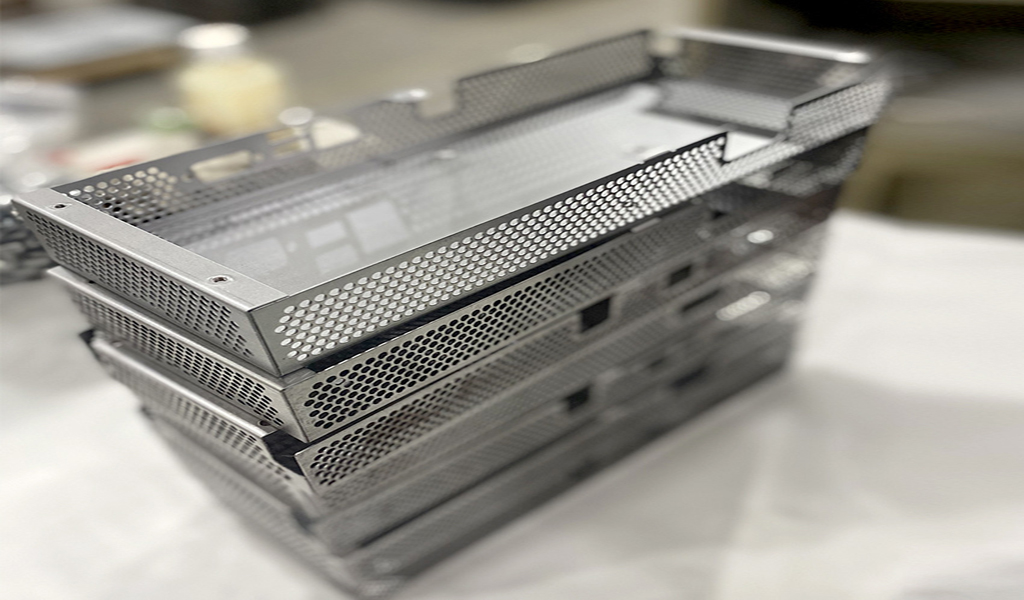
The production of automobile sheet metal parts mainly relies on molds to complete. In the whole cycle of model design, mold design, manufacture and commissioning, mold design, manufacture and commissioning account for about 2/3 of the time, which has become the main factor restricting the transformation of automobiles. This is because the sheet metal stamping forming process is a very complex plastic forming process, and many factors directly or indirectly affect the forming results.
The classical sheet metal forming theory can only analyze the sheet metal forming process of simple sheet metal parts such as bending parts and cup-shaped parts. It is powerless for sheet metal parts with complex shapes such as car covers. This makes the design of automobile molds so far mainly based on the designer’s experience and analogy. Due to the lack of more accurate and reliable quantitative analysis and calculation, the designed and manufactured molds must be modified through repeated pressure tests, and sometimes even the design of the original product is modified, and only qualified parts can be punched out after scrapping and remaking the mold.
This process leads to a huge waste of people, money, materials and time. In order to change the situation that the traditional experience and trial-and-error methods are not suitable for the development of the automobile industry, it is envisaged whether the stamping process can be simulated on the computer before the mold is put into manufacture, that is, the designed mold can be analyzed in a virtual environment. If feasible, go back to manufacturing. If not, then modify the mold design, or even modify the design of the original product, redesign the mold, and repeat the simulation analysis until it is feasible and then put into mold manufacturing. In this way, the huge waste caused by debugging with the actual manufactured mold can be avoided. This work is also known as computer-aided engineering analysis (CAE) of sheet metal forming.
Under the influence of the development needs of the automobile industry, foreign automobile manufacturers have invested heavily in this research work. With the development of finite element technology and the continuous progress of computer technology, developed countries in the world have successively developed some forming simulation commodity software for the analysis of sheet metal forming process. The widely used well-known software are:
- (1) The LS-DYNA3D software developed by Professor Hallquist of the Lawrence livemore National Materials Laboratory in the United States. DYNA3D is an early version of it.
- (2) PAM-STAMP software of French ESI company.
- (3) OPTRIS software from DYNAMIC SOFTWARE, France. It was launched on the basis of PAM-STAMP. In fact, the latter two software are also developed on the basis of DYNA3D. They all use dynamic explicit algorithms. The Lawrence Livemore National Laboratory in the United States has also developed the LS-NIKE3D software using static implicit algorithm. In addition, there are DEFORM and MARC in the United States, AFORM and INDEED in Germany, and ITAS3D in Japan.
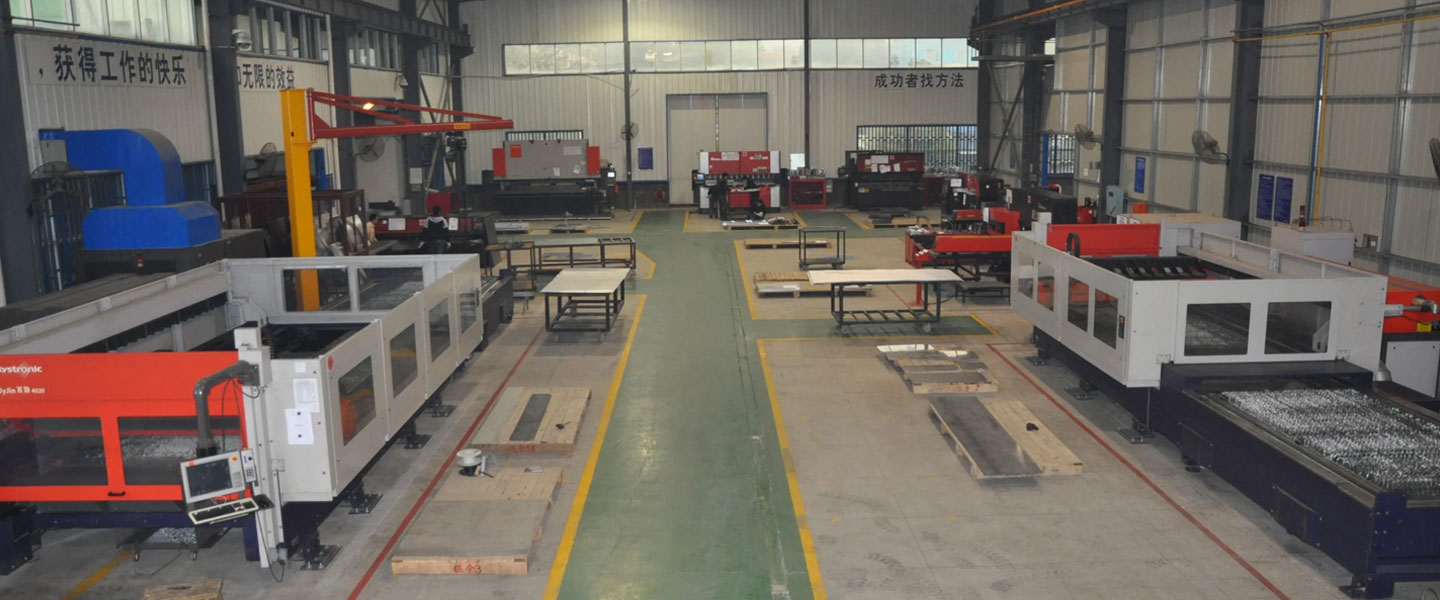
Pintejin Sheet Metal shop offers a cost-effective solution for a wide range of industries with our custom metal stamping and custom sheet metal fabrication capabilities. Our stampnig operations include a variety of sheet-metal forming manufacturing processes, such as punching, blanking, embossing, bending, flanging, and coining. Our professional, experienced and well-trained engineers can execute the complex metal stamping operations with precision and accuracy.
No matter what your metal fabrication needs are, Pintejin can offer the right solution: from single sheet metal part or sub-assembly of stamped metal parts to turnkey solutions for mechanical and electrical assemblies. We have the technology, equipment and the experience to fabricate customised metal products from aluminium sheet metal fabrication, steel, zinc plated steel, stainless steel sheet metal fabrication, brass and copper. Designs that require CNC machining of surfaces or components can be accommodated. We can supply polished, galvanized, zinc coated or powder coated finishes for any sheet metal work or stamped metal components. Coupled with our accurate and reliable metal fabricating equipment, we guarantee precision and repeatability in custom sheet metal work. You’ll be taking advantage of the best sheet metal fabrication china can produce.