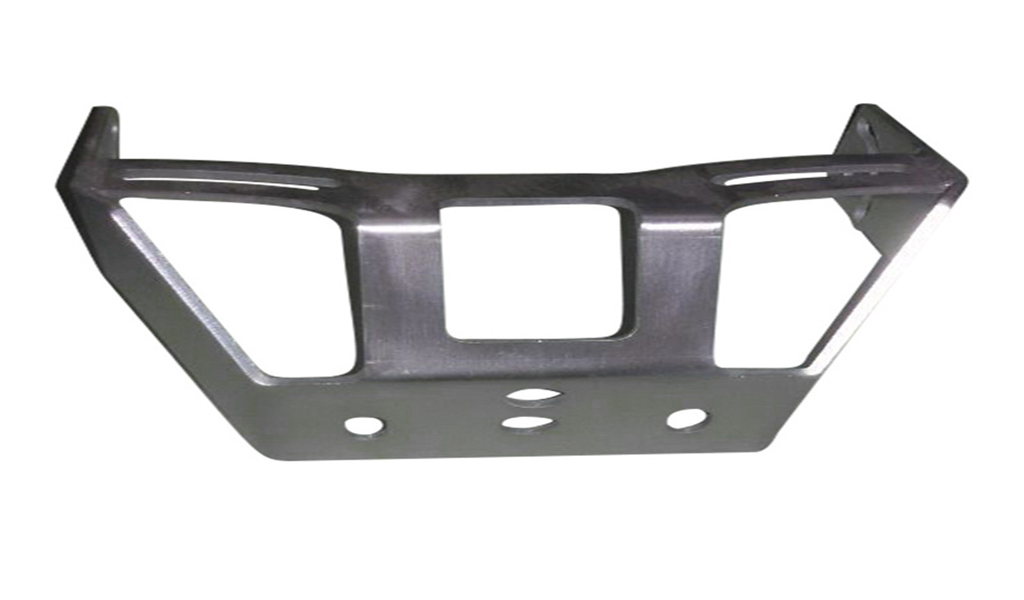
In recent years, the automobile industry has been continuously prospering. With the continuous development of the market, people’s requirements to resist the performance and quality of automobiles are also getting higher and higher. However, in the manufacturing process of automobiles, due to various reasons, the development cycle of automobiles has become longer, and the manufacturing difficulty is also very large, which also has a certain impact on the overall manufacturing progress and level of automobiles. Among them, automobile stamping parts. The manufacturing of automobiles is a serious key to the manufacture of automobiles, so various automobile manufacturers are gradually paying attention to the research and manufacture of stamping parts for automobiles. In the manufacturing process of automobile stamping parts, all the key points must be closely combined in order to effectively avoid various problems that may occur during the production process of stamping parts. The springback effect is also an aspect of improving the overall accuracy of the car. The following will briefly explain the types of springback results of automotive stampings, the reasons for the springback results and the factors that affect the springback.
1. A model of the springback defect of stamping parts of automobile sheet metal parts
The first is distortion defects, including shape distortion, shallow stretched piece distortion, multi-curve shape distortion, etc. Due to the presence of blanking force during the fabrication process, it will cause the shape distortion of the stamping parts during the fabrication process. During the blanking process, The blanking gap is unreasonable, so that one side of the material is compressed and the other side is stretched, so it will cause the shape of the stamping part to be distorted during the manufacturing process. There is also a large curve change defect. The reason for this type of environment is that the stress of the material is thicker. There are also warping defects, which may be edges or faces. The reason for this type of environment is that the void force and the reaction force are not in a straight line, resulting in torque, or the gap of some molds is too large. There are many other results, such as positive and negative springback defects, these defects will have a certain impact on the quality and accuracy of stamping parts, and some cannot even be reused, so the production process is advanced to find out the springback of automotive stamping parts The reason for the defect is very necessary.
2. Factors that affect the rebound
(1) Material properties of automotive sheet metal parts
Within the elastic limit of the material, the greater the degree of deformation of the material and the higher the compliance limit, the greater the elastic modulus of the material. During the fabrication of the material, the greater the elastic modulus of the material, the greater the resilience of the bending deformation. If the elastic modulus of the material is smaller, the degree of springback will be smaller during fabrication, and the ability to resist elastic deformation will be stronger.
(2) Bending center angle
The larger the value of the bending center angle, the greater the springback accumulation value, and the more serious the springback phenomenon will be. The deformation length of the stamping part increases with the increase of the bending center angle.
(3) Cavity environment of automotive sheet metal molds
When the mold is designed, a gap of twice the material thickness should be left in a certain working part to accommodate the product in the gap. In order to achieve better performance of the material, after the mold fabrication is completed, the parts of the mold should be researched and matched. Especially for bending molds, the larger the gap of the working part, the greater the springback. If the tolerance of the thickness of the sheet is larger, the springback will be larger, and the gap of the mold will not be very good. Good must.
(4) Must bend radius
The value of the certain bending radius is proportional to the springback value, so the greater the curvature of the stamping part, the more difficult it is to bend.
(5) Appearance of the whole machine
If the shape of the whole machine is different, the possibility of springback is also different. When the complicated bending stamping parts are bent and formed at one time, the stamping parts will be bundled with each other during the forming process and the friction force between the mold and the material will change the stamping. The stress situation of each part of the piece, so that the amount of springback changes.
(6) Forming process
The forming process of stamping parts is a serious aspect that restricts its springback value. Generally speaking, the springback effect of calibration bending is better than that of easy bending. Assuming that abnormal fabrication results are to be achieved in the production of the same batch of stamping parts, the bending force necessary for the calibration bending is much larger than that of the easy bending, so if the two methods adopt abnormal bending forces, the end-to-end results are also inconsistent. The greater the correction force necessary for correction and bending, the smaller the springback of the stamping part, and the correction of the bending force will make the outer and outer fibers in the deformation zone stretched to achieve the forming result. After the bending force is unloaded, the fibers on the inside and outside will extend, but the rebound direction of the inside and outside is the same, so that the outward rebound of the stamping part can be slowed down to a certain extent.
Other methods using cold stamping can process some materials with harder raw materials. Among them, steel plates and steel strips that are often used in the automotive field can be processed using this equipment. Now in the production of car stamping parts, less and less steel is used. On the one hand, it is because some raw materials composed of aluminum and carbon elements have stronger hardness, and after using this composite material, it can effectively reduce the weight of the car itself. The weight of the car has a very important effect on the consumption of less gasoline and diesel in the car. And after using this new type of composite material, the protection of the car body is also easier.
When using this cold stamping technology to make car stamping parts, the quality of the product must be strictly dealt with. Assuming that when using this technology to make stamping parts, it is not produced according to the requirements, and the workmanship does not meet the standards in production. The stamping parts produced in this way are likely to be unqualified in some aspects, which may shorten the service life in use. , and it is also easy to make the car dangerous in the process of traveling, injuring the industry or the loss of the body of the passengers in the car. Other assumptions produce substandard products, which can cause unnecessary waste to human resources.
Therefore, when selecting materials and fabrication operations for these automotive stamping parts, it is not only necessary to carefully select the raw materials used in the fabrication of these automotive stamping parts, but also to formulate a strict treatment system during the fabrication. , and also implement the relevant inspection rules. In this way, the quality problem of this middleware is controlled from the source.
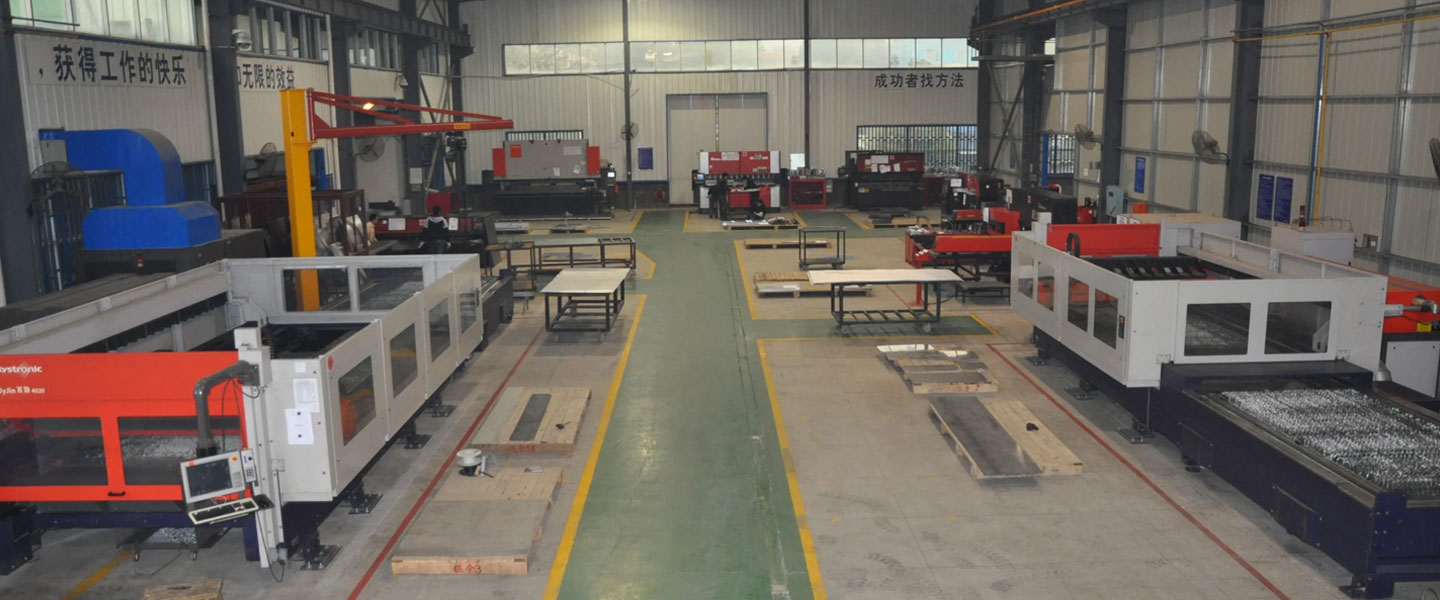
Pintejin Sheet Metal shop offers a cost-effective solution for a wide range of industries with our custom metal stamping and custom sheet metal fabrication capabilities. Our stampnig operations include a variety of sheet-metal forming manufacturing processes, such as punching, blanking, embossing, bending, flanging, and coining. Our professional, experienced and well-trained engineers can execute the complex metal stamping operations with precision and accuracy.
No matter what your metal fabrication needs are, Pintejin can offer the right solution: from single sheet metal part or sub-assembly of stamped metal parts to turnkey solutions for mechanical and electrical assemblies. We have the technology, equipment and the experience to fabricate customised metal products from aluminium sheet metal fabrication, steel, zinc plated steel, stainless steel sheet metal fabrication, brass and copper. Designs that require CNC machining of surfaces or components can be accommodated. We can supply polished, galvanized, zinc coated or powder coated finishes for any sheet metal work or stamped metal components. Coupled with our accurate and reliable metal fabricating equipment, we guarantee precision and repeatability in custom sheet metal work. You’ll be taking advantage of the best sheet metal fabrication china can produce.