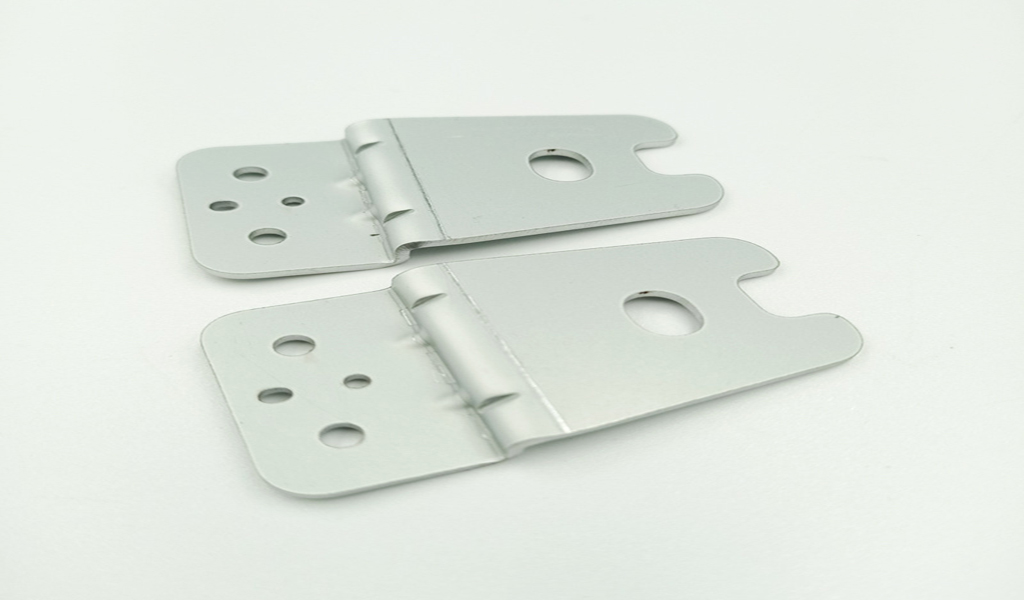
Mold assembly is a job with relatively high technical requirements. It requires experienced operators to install according to technical specifications. It is often necessary to repeatedly disassemble, flip, test, adjust, open and close mold parts, which is labor-intensive. Especially those progressive dies with complex structures and large stamping dies require a long time for the operator to debug. In order to improve the mechanization of mold assembly, assembly accuracy, and reduce manual assembly procedures. Mold assembly machines have been widely used abroad.
The mold equipment machine is actually a working platform for assembling various parts of the mold, which consists of a transmission mechanism, an upper table, a work table, and a bed. When assembling a large stamping die, first fix the die base on the working table, which is convenient for assembling various parts of the die. The slider on the upper table can be positioned according to the size of the upper die base, and the upper die base can be easily assembled by using the pressure plate and screws. fixed in the designated position.
The upper platen designed by the mold assembly machine can be turned 360 degrees at will, and can be lifted up and down through the four guide columns connected with the worktable and the bed, so as to facilitate adjustment of the upper and lower molds, mold clamping and adjustment of the gap between the concave and convex molds, solving manual assembly. Adjust the various problems of the die gap, and the die assembly machine is equipped with a test punch function, which can quickly find and solve problems during the assembly process. The mold assembly machine can also set the drilling function, so that the pin hole can be drilled immediately after the mold test is OK, and there is no need to go to the drilling machine for drilling operations, which improves the production efficiency.
When assembling the die for automobile stamping parts, it is necessary to ensure a certain gap between the concave and convex dies, and the gap needs to be symmetrical, so as to prolong the service life of the die and ensure the quality of the stamping parts. Some methods are listed below to ensure that the gap between the concave and convex dies is uniform.
- 1. Direct measurement, use measuring tools to directly measure the gap between the concave and convex dies. Due to the complex structure between the concave and convex dies, the measuring tool can only be used on stamping dies with a unilateral gap of more than 0.02mm. If the gap is too small, it will be difficult to Measurement.
- 2. For the reference measurement of the gasket, insert a paper or metal sheet of uniform thickness into the gap between the mating parts of the concave and convex die. Take the thickness of the gasket as a reference standard to ensure that the gap between the concave and convex dies is uniform.
- 3. Measurement by light transmission method, use light to illuminate the matching gap between the concave and convex dies, and determine whether the gap between the concave and convex dies is uniform by the size of the light gap that is transmitted through.
- 4. Coat a layer of paint on the punch, the thickness is the matching gap between the punch and die, and then insert the punch. This method is simple and practical, and it is more suitable for stamping dies that cannot be adjusted with a gasket test.
- 5. Copper plating method, coat a layer of copper layer on the working end of the punch, the thickness is the matching gap between the punch and die, and then insert the punch. This method is similar to the coating method, and the copper layer can automatically fall off during the use of the stamping die.
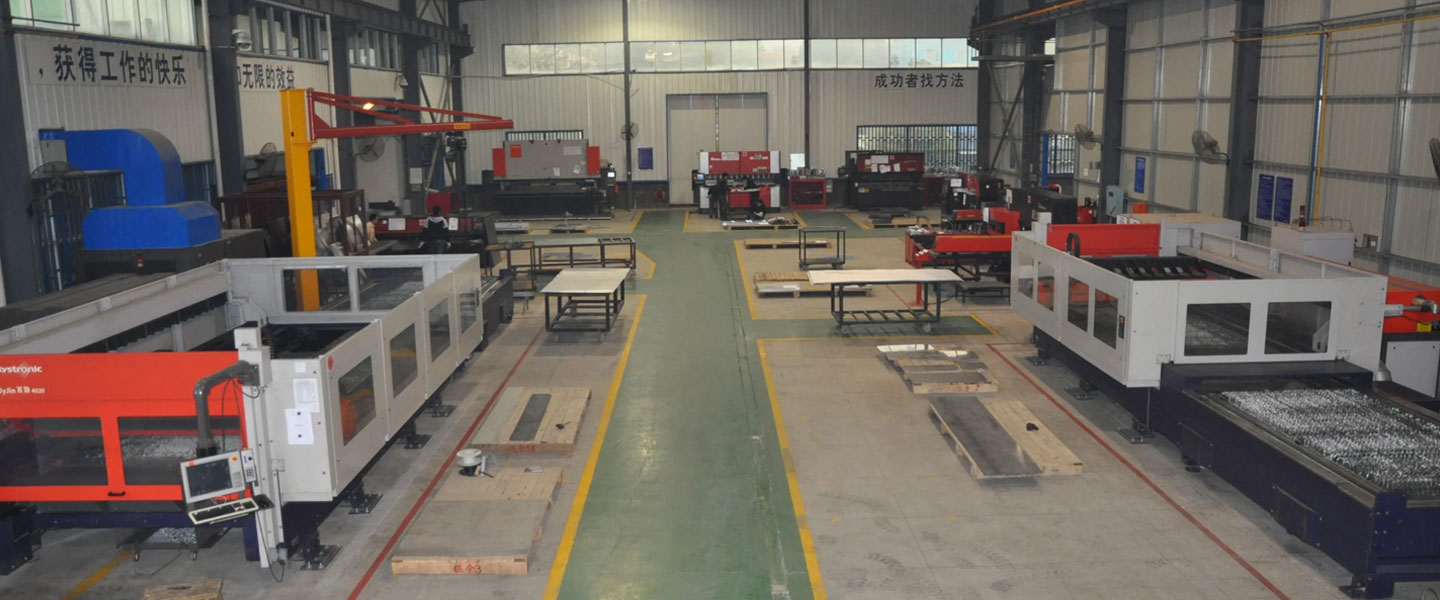
Pintejin Sheet Metal shop offers a cost-effective solution for a wide range of industries with our custom metal stamping and custom sheet metal fabrication capabilities. Our stampnig operations include a variety of sheet-metal forming manufacturing processes, such as punching, blanking, embossing, bending, flanging, and coining. Our professional, experienced and well-trained engineers can execute the complex metal stamping operations with precision and accuracy.
No matter what your metal fabrication needs are, Pintejin can offer the right solution: from single sheet metal part or sub-assembly of stamped metal parts to turnkey solutions for mechanical and electrical assemblies. We have the technology, equipment and the experience to fabricate customised metal products from aluminium sheet metal fabrication, steel, zinc plated steel, stainless steel sheet metal fabrication, brass and copper. Designs that require CNC machining of surfaces or components can be accommodated. We can supply polished, galvanized, zinc coated or powder coated finishes for any sheet metal work or stamped metal components. Coupled with our accurate and reliable metal fabricating equipment, we guarantee precision and repeatability in custom sheet metal work. You’ll be taking advantage of the best sheet metal fabrication china can produce.