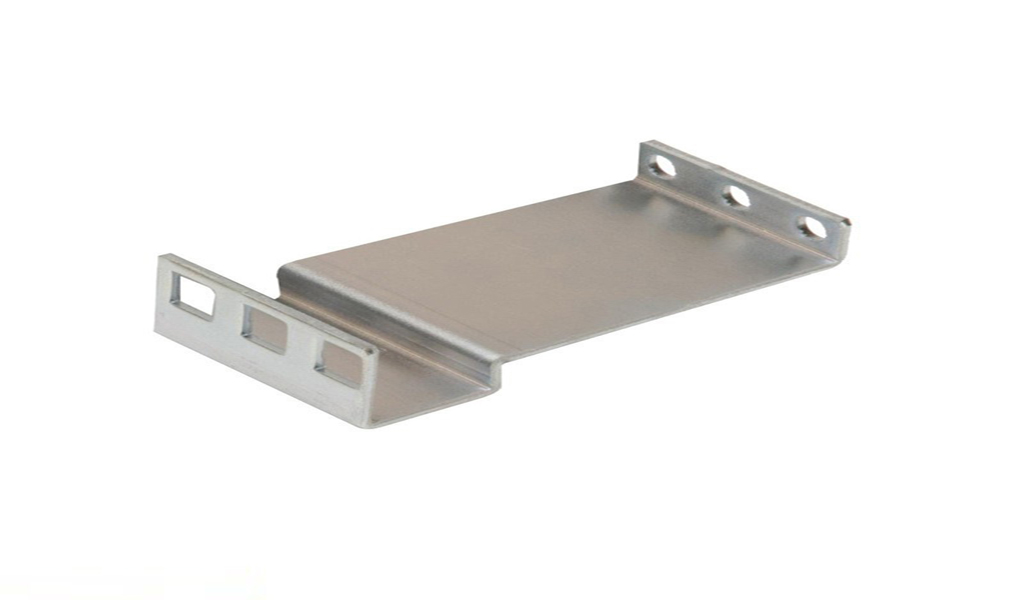
Sheet metal fabrication is a technical activity, and it is also an important technology that sheet metal technicians need to master. Whether the sheet metal products are formed depends on this process. The general processes of sheet metal fabrication are: metal cutting, cutting tools to remove excess metal layers from metal materials or workpieces, so as to obtain a fabrication method with a certain shape, dimensional accuracy, and surface roughness. Grinding, broaching, turning, milling, planing, drilling, is to deform the metal, stamping, cold rolling, cold drawing, extrusion, bending, of course, the corresponding hot fabrication, while forming the metal, can be used Work hardening increases the hardness and strength of parts, but reduces plasticity.
When it comes to the details, make fuel tanks, oil cans, ventilation ducts, iron links, refrigerators, washing machines, cars, computers. . These are actually all part of sheet metal fabrication. A simple summary of sheet metal fabrication is that the processes are shearing, edging, bending, bending, welding, and sheet metal fabrication personnel need certain geometric knowledge. Sheet metal parts are thin-plate hardware, which can be punched, bent, and stretched. parts processed by other means. Sheet metal is divided into precision sheet metal and ordinary sheet metal. Precision sheet metal is a high-precision sheet metal part, and its manufacturing is precision sheet metal fabrication. A simple definition is a part with a constant thickness during fabrication, corresponding to castings, forgings, and machining.
To distinguish the quality of automobile sheet metal parts, generally speaking, we can start from the aspects of packaging, weight, welding process, painting process and the degree of fit when loading. It is very difficult for ordinary car owners to distinguish whether the sheet metal parts are of high quality after delivery. It may be possible to distinguish from the packaging of the products in advance: the products produced by ordinary small factories will not print the contact information and factory address, while the regular manufacturers In addition to the contact information and factory address, there will also be steel stamps, qualifications and testing labels on the products. Even if consumers have problems in the future use process, they can also have a way to protect their rights.
Product weight is one of the inspection standards to measure the quality of sheet metal parts. In order to ensure the safety of automobiles, the steel plates used in automobile sheet metal parts must reach a certain weight. The weight of the original sheet metal parts and the high-quality sub-factory sheet metal parts should be almost the same, and if the sheet metal parts you buy are one-third lighter than the original sheet metal parts, then you will undoubtedly buy It will be the product of a small factory. As for the welding process, it is also a method to distinguish whether the sheet metal parts are from large manufacturers. The sheet metal parts produced by regular manufacturers will be mechanically cut and welded, and the welding points or trimmed edges will be smooth and will not leave rough cutting edges.
Many car owners think that they need to be painted with the same color as the original car after the sheet metal parts, so they will ignore the painting process of the sheet metal parts when purchasing sheet metal parts, thinking that it is not important, but this idea is incorrect . In order to prevent oxidation and rust, the sheet metal parts need to be treated by painting before leaving the factory. Indeed, the painting process after replacing the sheet metal parts can also protect and prevent oxidation in addition to color matching. If it is a sheet metal part of a small factory, if there is uneven adsorption and foaming in the painting process during production, it will affect the effect of post-painting, which will cause it to fall off easily during use, cause rust, affect and destroy. The quality of sheet metal parts.
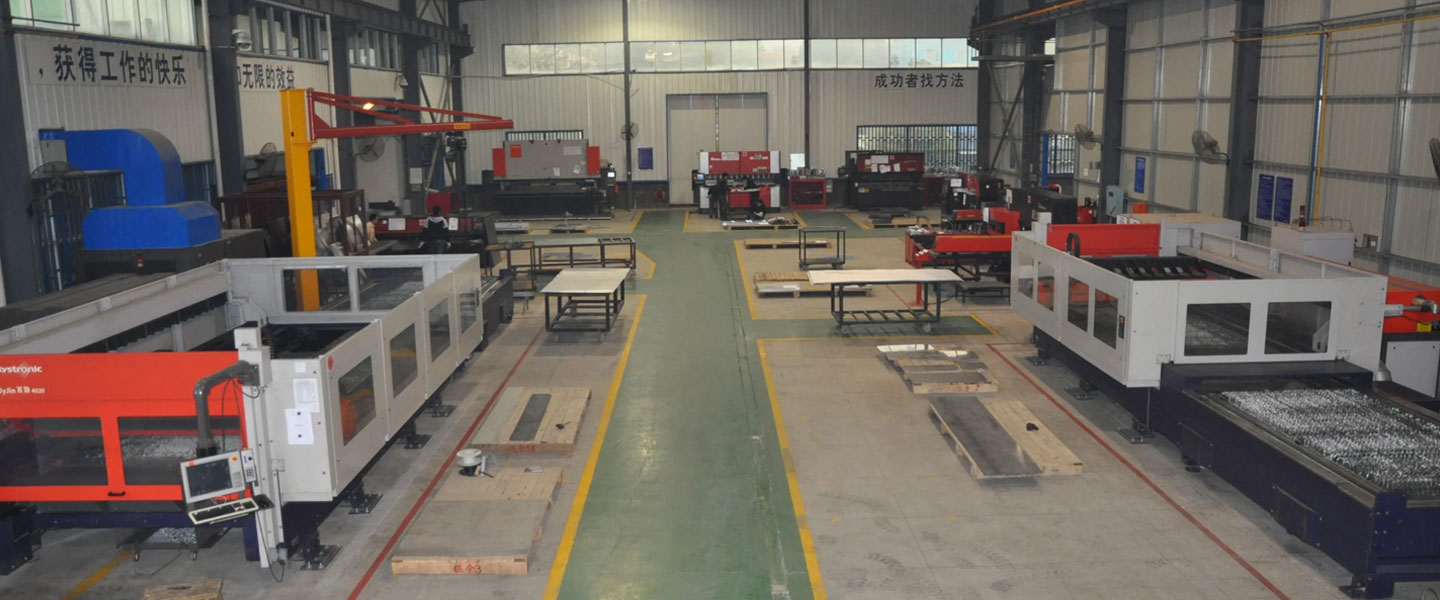
Pintejin Sheet Metal shop offers a cost-effective solution for a wide range of industries with our custom metal stamping and custom sheet metal fabrication capabilities. Our stampnig operations include a variety of sheet-metal forming manufacturing processes, such as punching, blanking, embossing, bending, flanging, and coining. Our professional, experienced and well-trained engineers can execute the complex metal stamping operations with precision and accuracy.
No matter what your metal fabrication needs are, Pintejin can offer the right solution: from single sheet metal part or sub-assembly of stamped metal parts to turnkey solutions for mechanical and electrical assemblies. We have the technology, equipment and the experience to fabricate customised metal products from aluminium sheet metal fabrication, steel, zinc plated steel, stainless steel sheet metal fabrication, brass and copper. Designs that require CNC machining of surfaces or components can be accommodated. We can supply polished, galvanized, zinc coated or powder coated finishes for any sheet metal work or stamped metal components. Coupled with our accurate and reliable metal fabricating equipment, we guarantee precision and repeatability in custom sheet metal work. You’ll be taking advantage of the best sheet metal fabrication china can produce.