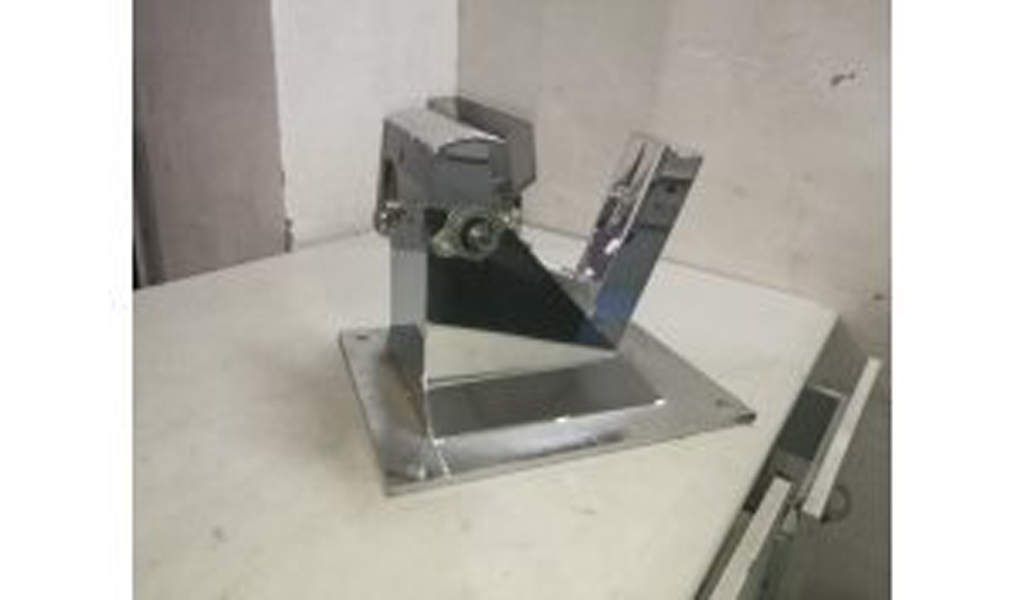
At present, there are many types of bending machines for automobile sheet metal fabrication, which can be divided into mechanical (servo motor) and hydraulic type according to the rotation mode. According to the control system, it can be divided into simple manual bending machine, ordinary china digital positioning bending machine, and process control digital full-function bending machine. According to the action part, it can be divided into 4-axis, 8-axis, 12-axis and other bending machines.
- 1. Before using the bending machine, you should check whether the power supply is connected, whether the air pressure is sufficient, whether the hydraulic pressure is sufficient, whether the machine is clean, and whether there are any obstacles in the slideway.
- 2. Turn on the power switch of the machine, start the oil pump and align the origin of the L-axis, D-axis, CC-axis and Z-axis to complete the starting process.
- 3. After installing the mold and selecting the mold, put the gear switch of the machine in the cutting position. After installing the base, the lower mold and the upper mold, put the switch of the machine in the inching or single-action position, and pedal The lift switch shakes the lift handle or knob to make the upper and lower molds merge and pressurize to align the zero point of the D-axis, and lock the lower mold to complete the mold loading process.
- 4. Recognize the drawing, understand the bending sequence and bending size, and start programming the bending machine. There are two input methods for programming, one is angle input and the other is depth input. We often use depth input method. First put the computer into the memory state, input the bending dimension L, D value, Z value, speed, time, times and other values. Then check and confirm the program, let the computer enter the running state after it is correct, and then use the scrap test to modify the program, so that the angle and size can be adjusted to the best state. Then carry out a trial folding of the product, and the trial folding product can be mass-produced after the inspection is correct.
- 5. If you want to increase the bending speed during the bending process, the gear switch can be single-acted or linked, but generally only single-acting is sufficient for safety. When bending long workpieces, the middle angle is often large, and the CC axis can be adjusted to change the middle angle to be consistent with the left and right sides. During the bending process, attention should also be paid to the central bending principle, which is an important prerequisite for ensuring the accuracy of the bending process. It is not allowed to bend at one end of the two ends of the bending machine, so that the angle is not only bad, but also damages the machine.
- 6. It is not allowed to turn off the power supply during short breaks, just turn off the oil pump, so as to save electricity bills, so as to avoid the need to re-work to the origin when going to work, save time and improve the utilization rate.
- 7. When the product is finished or needs to be stopped after get off work, first put the lower mold in the low position, then turn off the oil pump, and then turn off the power supply. If the batch of products has been completed, the mold must be removed and put back on the mold frame and resumed operation. panel.
- 8. It is strictly forbidden to operate the bending machine in violation of regulations, so as to avoid unnecessary harm to people and equipment molds. Usually pay attention to the cleaning and maintenance of the machine, and develop a good habit of caring for the equipment and molds.
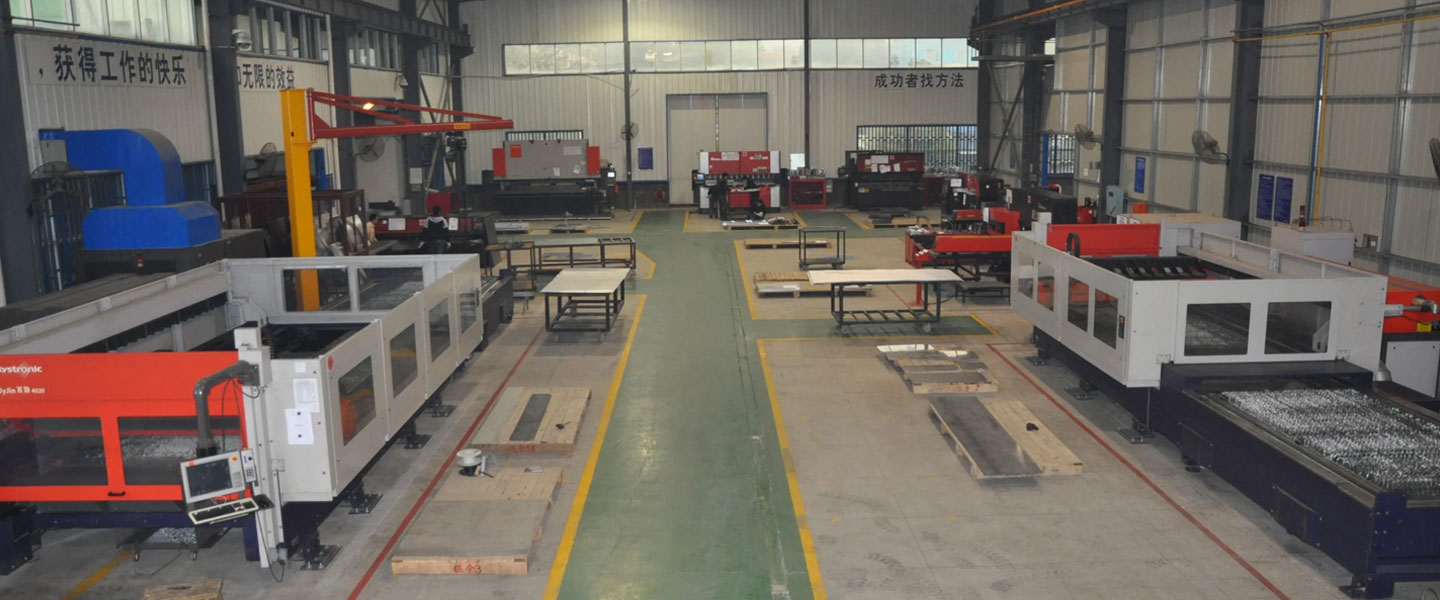
Pintejin Sheet Metal shop offers a cost-effective solution for a wide range of industries with our custom metal stamping and custom sheet metal fabrication capabilities. Our stampnig operations include a variety of sheet-metal forming manufacturing processes, such as punching, blanking, embossing, bending, flanging, and coining. Our professional, experienced and well-trained engineers can execute the complex metal stamping operations with precision and accuracy.
No matter what your metal fabrication needs are, Pintejin can offer the right solution: from single sheet metal part or sub-assembly of stamped metal parts to turnkey solutions for mechanical and electrical assemblies. We have the technology, equipment and the experience to fabricate customised metal products from aluminium sheet metal fabrication, steel, zinc plated steel, stainless steel sheet metal fabrication, brass and copper. Designs that require CNC machining of surfaces or components can be accommodated. We can supply polished, galvanized, zinc coated or powder coated finishes for any sheet metal work or stamped metal components. Coupled with our accurate and reliable metal fabricating equipment, we guarantee precision and repeatability in custom sheet metal work. You’ll be taking advantage of the best sheet metal fabrication china can produce.