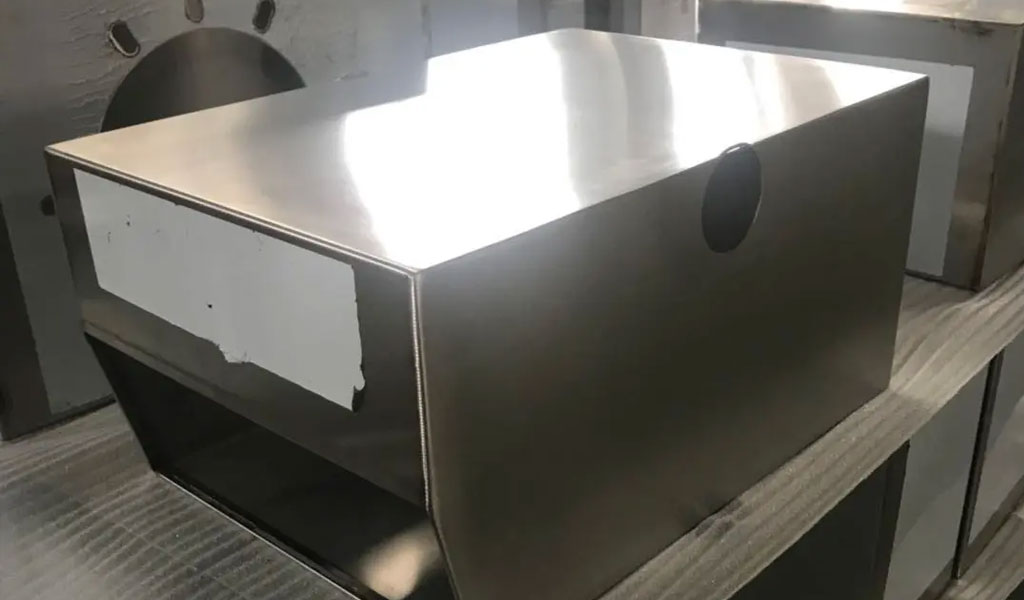
The decorative and protective effects of sheet metal fabrication on the surface of products are recognized by many industries. In the sheet metal fabrication industry, the commonly used surface treatment methods are electroplating, spraying and some other surface treatment methods.
- All electrochemical treatment should be carried out in the state of the parts, because the chemical solution during the treatment process will be trapped in the gap of the assembly and cause corrosion;
- Spot welded parts can be chemically treated, but not electrochemically treated (including electroplating and anodizing);
- Aluminum alloy castings cannot be anodized with sulfuric acid;
- Thin and long tubular parts (the length is greater than 2 times the diameter) are generally not suitable for electrochemical treatment, because there will be no film layer on the inner surface; (special measures can be taken to meet the requirements in special cases)
- After the parts with deep grooves or pores (generally refers to the depth greater than 2 times the diameter or opening width, but the excellent process is not limited by this), the inner surface of the parts will not be completely covered with the coating;
- It is best to carry out phosphating treatment before spraying steel parts to increase the adhesion of the coating;
- In order to improve the corrosion resistance of steel parts plated with bright nickel, copper or dark nickel can be plated first;
- Zinc-based alloys generally use electroplating as protective decoration. In order to improve the bonding force of the coating, it is generally necessary to pre-plated copper or nickel;
- Because most organic gases have a corrosive effect on zinc, the galvanized layer should be carefully selected in the design of sheet metal fabrication to be in contact with organic materials or assembled in the same closed body;
- For electroplated (oxidized) parts that require riveting, the fabrication procedure must be electroplating (or oxidation) first, and then riveting.