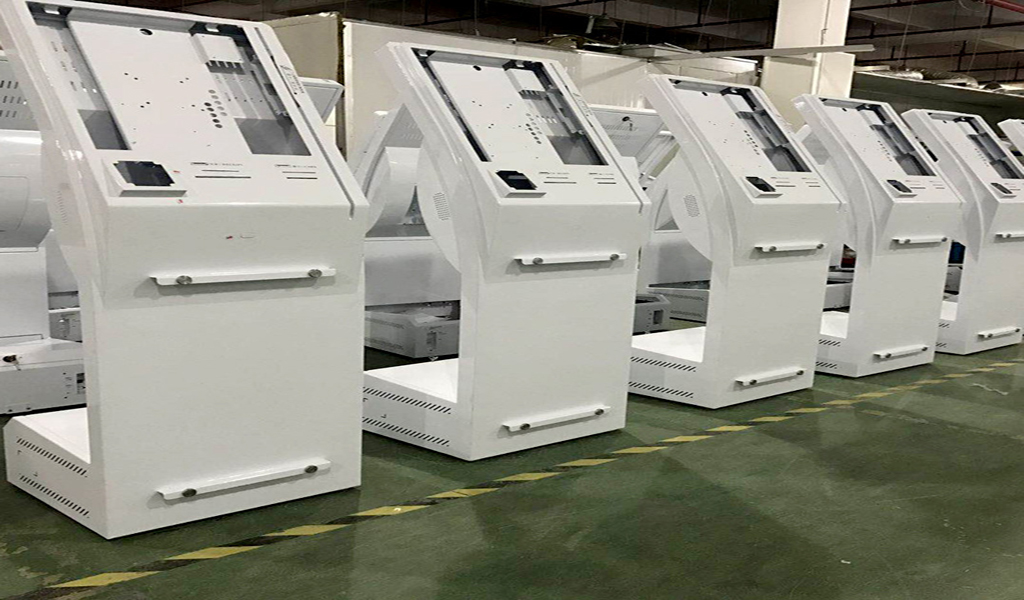
The basic process of sheet metal fabrication is divided into: blanking, bending, stretching, forming, welding. Among these five basic processes, each process must pay attention to the strict requirements of the process, and it must not be sloppy. A slight deviation in one process will affect the quality of sheet metal fabrication products.
- One, cutting. The methods of blanking fabrication include general punching, digital punching, shearing machine cutting, laser cutting, and air cutting. Among them, punching and laser cutting are the main methods of blanking sheet metal fabrication.
- Second, bending. There are many factors to be considered when bending, including the small bending radius of the bending part, the height of the straight edge of the bending part, the distance between the holes on the bending part, the process incision with partial bending, and the bending edge with a beveled edge should be avoided. Deformation area, design requirements for dead edges, process positioning holes added in the design, and when marking the relevant dimensions of the bending parts, the manufacturability and the springback of the bending parts should be considered.
- Three, stretching. When stretching, pay attention to calculating various data, including the size of the fillet radius between the bottom of the stretch piece and the straight wall, the fillet radius between the flange and the wall of the stretch piece, and the inner cavity diameter of the round stretch piece. , the radius of the corners between the two adjacent arms of the rectangular stretch piece, the relationship between the height and the diameter of the circular stretch piece without flanges, the dimension standards and precautions on the design drawing of the stretch piece, etc.
- Fourth, molding. After the sheet metal fabrication product is formed, it is necessary to perform some fabrication on the product. There are reinforcing rib structure, the limit size of convex spacing and convex edge distance, making shutters, and fabrication internal control flanging.
- Five. Welding. This is the last process of the automotive sheet metal fabrication process, and attention should also be paid to the welding method and process technology. The welding methods mainly include arc welding, electroslag welding, gas welding, plasma arc welding, fusion welding, pressure welding, and brazing. Among them, arc welding and gas welding are the main methods of sheet metal fabrication.
The four important steps of sheet metal fabrication are shearing, punching/cutting, folding and welding.
Sheet metal is sometimes also used as sheet metal. The word comes from the English plate metal. Generally, some metal sheets are plastically deformed by hand or die stamping to form the desired shape and size, and can be further formed by welding or a small amount of machining. More complex parts, such as chimneys commonly used in homes, tin stoves, and car casings are sheet metal parts.
Sheet metal fabrication is called sheet metal fabrication. Specifically, for example, the use of plates to make chimneys, iron drums, fuel tanks and oil cans, ventilation pipes, elbows and heads, Tianyuan places, funnel-shaped, etc., the main processes of automobile stamping parts are cutting, bending, bending, forming, welding, riveting etc., some knowledge of geometry is required.
Sheet metal parts are thin-plate hardware parts, that is, parts that can be processed by stamping, bending, stretching, etc. A general definition is a part with a constant thickness during fabrication. Corresponding to casting parts, forging parts , Machining parts, etc. For example, the outer iron shell of the car is a sheet metal part, and some stainless steel kitchen utensils are also sheet metal parts.
In the current 3D software, SolidWorks, UG, Pro/E, SolidEdge, TopSolid, etc. all have sheet metal parts, mainly through the editing of 3D graphics to obtain the data required for sheet metal parts fabrication (such as unfolding drawings, bending Line, etc.) and provide data for CNC Punching Machine / Laser, Plasma, Waterjet Cutting Machine (Laser, Plasma, Waterjet Cutting Machine) / Combination Machine and CNC Bending Machine, etc.
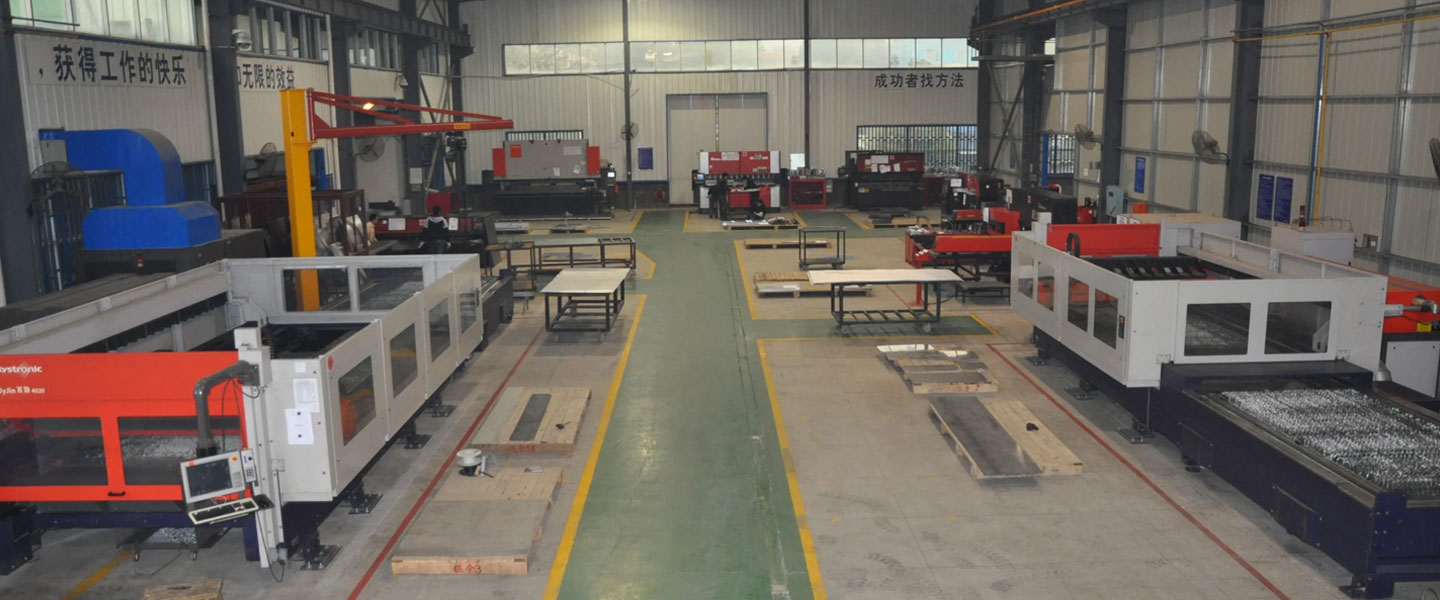
Pintejin Sheet Metal shop offers a cost-effective solution for a wide range of industries with our custom metal stamping and custom sheet metal fabrication capabilities. Our stampnig operations include a variety of sheet-metal forming manufacturing processes, such as punching, blanking, embossing, bending, flanging, and coining. Our professional, experienced and well-trained engineers can execute the complex metal stamping operations with precision and accuracy.
No matter what your metal fabrication needs are, Pintejin can offer the right solution: from single sheet metal part or sub-assembly of stamped metal parts to turnkey solutions for mechanical and electrical assemblies. We have the technology, equipment and the experience to fabricate customised metal products from aluminium sheet metal fabrication, steel, zinc plated steel, stainless steel sheet metal fabrication, brass and copper. Designs that require CNC machining of surfaces or components can be accommodated. We can supply polished, galvanized, zinc coated or powder coated finishes for any sheet metal work or stamped metal components. Coupled with our accurate and reliable metal fabricating equipment, we guarantee precision and repeatability in custom sheet metal work. You’ll be taking advantage of the best sheet metal fabrication china can produce.