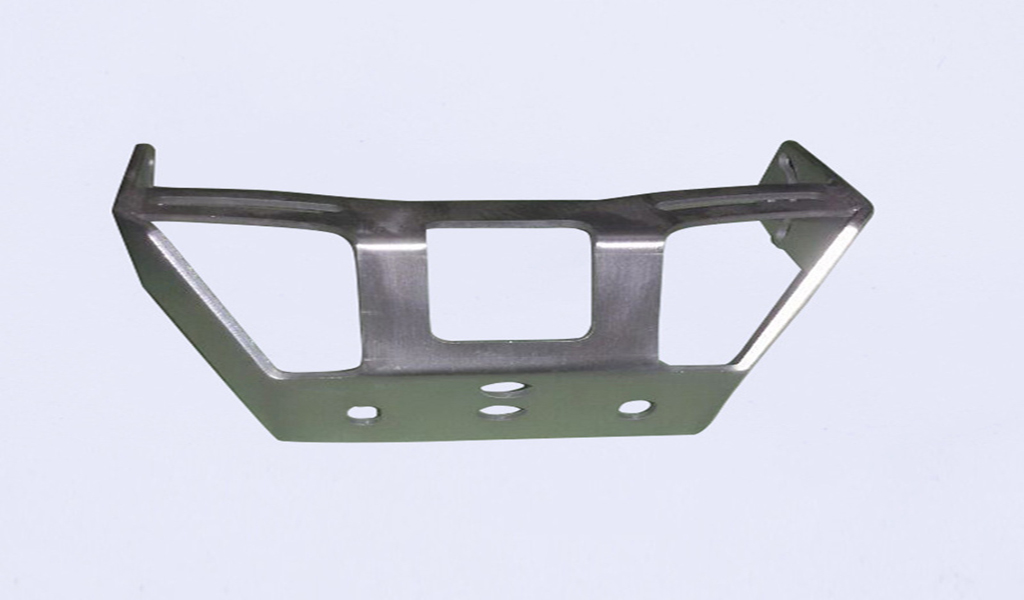
There are many reasons for the wrinkling of the stretched parts during the stretching process. The main reasons are as follows:
- (1) The drawing depth of the stamping part is too deep, which causes the sheet material to flow too fast during the feeding process of the part, resulting in wrinkles.
- (2) During the drawing process of the stamping part, the R angle of the die is too large, so that the punch cannot press the material during the drawing process, causing the sheet to flow too fast to form wrinkles.
- (3) The pressing ribs of stamping parts are unreasonable, the pressing ribs are too small and the position is incorrect, which cannot effectively prevent the sheet from flowing too fast and form wrinkles.
- (4) The pressure of the ejector rod is too small, so that the stamping part is not completely formed and wrinkles are formed.
- (5) The mold positioning design is unreasonable, resulting in the inability to hold the material during the drawing process of the stamping part or the pressing edge is too small, resulting in the inability to hold the material during the drawing process, resulting in wrinkling.
- (6) The gap between the convex and concave die is too large, so that the material cannot be pressed during the stretching process, resulting in wrinkling.
The above are the common causes of wrinkling in the stretching process of metal automobile stamping parts. Specific analysis is required in specific problems, and the specific reasons are found according to the specific conditions of stamping parts. The way to prevent wrinkling is to ensure that the die of the metal stamping parts can press the material during the stretching process to ensure a reasonable flow rate of the sheet material. When the stamping part flows too fast, it can cause wrinkling; on the other hand, if the sheet metal flows too slowly, it can cause the stamping part to crack.
Setting drawbeads on the binder surface is an effective and useful method to adjust and control deformation resistance. The draw bead can well adjust the flow of the material, so that the material flow resistance of each part in the drawing process is uniform, so that the amount of material flowing into the cavity is suitable for the needs of the part, preventing more wrinkling and less cracking The phenomenon.
For curved stretched parts with complex shapes, especially those with small flanges, drawbeads should be set to increase the radial tensile stress of stretching to control wrinkling; On the part with less stress, that is, the part where the sheet is easy to flow. For parts with smaller flanges, in order to set drawbeads, some materials (process supplementary materials) can be appropriately added, and this part can be removed when trimming. For drawing parts with large difference in drawing depth, the draw bead should be set in the part with less material feed, so that too much material in this part can be organized to be pulled into the cavity of the die, thereby preventing wrinkling.
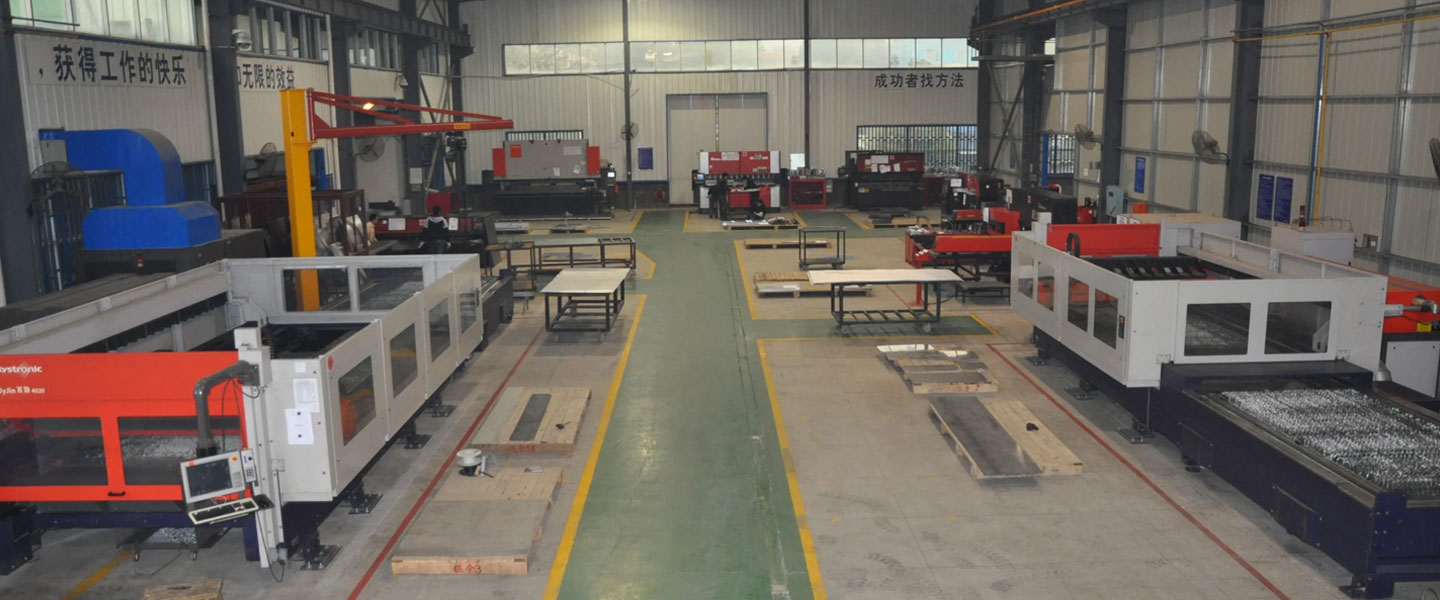
Pintejin Sheet Metal shop offers a cost-effective solution for a wide range of industries with our custom metal stamping and custom sheet metal fabrication capabilities. Our stampnig operations include a variety of sheet-metal forming manufacturing processes, such as punching, blanking, embossing, bending, flanging, and coining. Our professional, experienced and well-trained engineers can execute the complex metal stamping operations with precision and accuracy.
No matter what your metal fabrication needs are, Pintejin can offer the right solution: from single sheet metal part or sub-assembly of stamped metal parts to turnkey solutions for mechanical and electrical assemblies. We have the technology, equipment and the experience to fabricate customised metal products from aluminium sheet metal fabrication, steel, zinc plated steel, stainless steel sheet metal fabrication, brass and copper. Designs that require CNC machining of surfaces or components can be accommodated. We can supply polished, galvanized, zinc coated or powder coated finishes for any sheet metal work or stamped metal components. Coupled with our accurate and reliable metal fabricating equipment, we guarantee precision and repeatability in custom sheet metal work. You’ll be taking advantage of the best sheet metal fabrication china can produce.