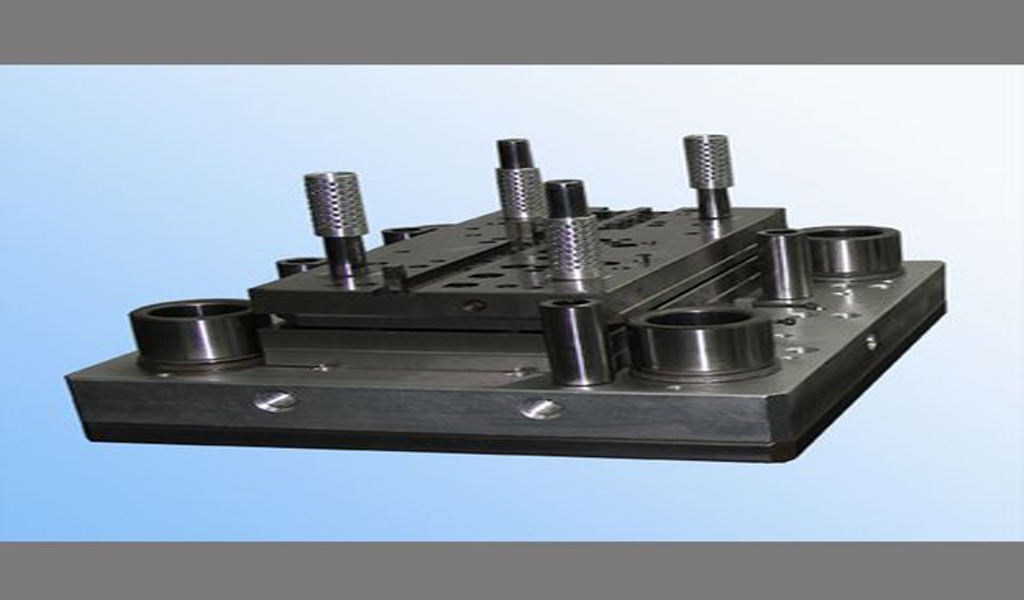
Ordinary drawing dies are mostly guided by guide plates or guide posts, while for drawing dies with large lateral force during the drawing process (referring to workpieces with asymmetric structure), the back block guide device can be used for guidance. The convex ribs are generally arranged in the blank frame, and the grooves corresponding to the surface of the die, that is, the concave ribs. The convex rod can also be set on the die surface, and the concave rod can be set on the blank holder ring.
The role of drawbeads. 1. Strengthen the ability of materials to control the flow of materials. 2. Increase the feeding resistance, so that the blank can bear enough tensile stress, improve the stiffness of the drawn part, and reduce the surface defects caused by springback. 3. Expand the adjustment range of blank holder force.
First of all, you need to know that the main role of “the bar of the spinnaker” is to increase the resistance of the material, so the “binder force” also plays the same role, these two complement each other and can reduce the bailholder force that adjusts the resistance of the large triangle Sail bars to achieve the same purpose.
Drawbead (groove) settings. The setting of the drawbead can increase the feeding resistance of the corresponding parts on the stamping surface and adjust the flow direction of the blank. However, if the position, number and shape of the drawbeads are not selected properly, satisfactory cover cannot be drawn. In general, the number and location of drawbeads mainly depend on the shape, relief characteristics and drawing depth of the cover layer.
For parts with large deep drawing, place 1-3 drawing beads in the straight line part, and no drawing beads in the arc part. When the drawing depth of each part of the same part is quite different, the deep drawing part is not provided with deep drawing ribs, and the deep drawing ribs must be provided with shallow ribs. The direction of the drawbead must be perpendicular to the direction of the blank flow.
Whether the drawbead is placed on the press cloth of the blanking ring or the press cloth of the die depends on whether the die is easy to adjust on the press. The drawbeads are generally placed on the upper pressing surface, and the drawbead grooves are placed on the lower pressing surface to facilitate material positioning. In order to ensure the reliability of the mold, in the process of mold debugging, it is often necessary to verify and adjust the drawbeads designed on the mold.
Among the many factors that affect the quality of automobile sheet metal parts, the influence of mold structure is very large. The forming effect of the deep drawing part is directly affected by the radius of the die, the geometry of the die workpiece, the guide mode of the die, the setting of the drawing rib (slot), and the size of the die air hole.
Determines the radius of punch and die fillets. The radius of the punch and die plays an important role in obtaining an ideal deep-drawn part. The two main defects of cover draws are wrinkling and tensile cracking. When the punch radius is too small: the bending deformation of the straight wall and the bottom of the billet increases, and the strength of the dangerous section is weakened;
When the radius of the die is too small, the tensile stress of the side wall of the blank will increase accordingly. Both of these conditions increase the draw coefficient and deformation resistance of the sheet, resulting in an increase in the total draw force and a decrease in die life.
If the radius of the punch or die is too large, the deformation resistance of the sheet material is small and the fluidity of the metal is good, but it will reduce the effective area of blanking and make the parts easy to wrinkle. Therefore, the deformation characteristics of the workpiece and the drawbead must be considered when determining the punch and die radii.
The geometry of the mold work part. The working parts of different shapes of molds also affect the quality of the drawn parts. The die is divided into two types: flat-head die and conical die. The use of conical dies generally provides greater resistance to buckling in the deformation zone of the billet, allowing relative thickness (t/D) relative to flat-end dies. Smaller blanks do not wrinkle.
Die-guided mode. The guide of the drawing die includes two directions: punch and blank holder, blank holder and blank holder. The rationality of the mold guide rail directly affects the reliability of the drawing. A reasonable and stable guide rail can ensure the uniformity of the mold circumferential gap and the coordination of the drawing surface, thereby ensuring the quality of the drawn parts.
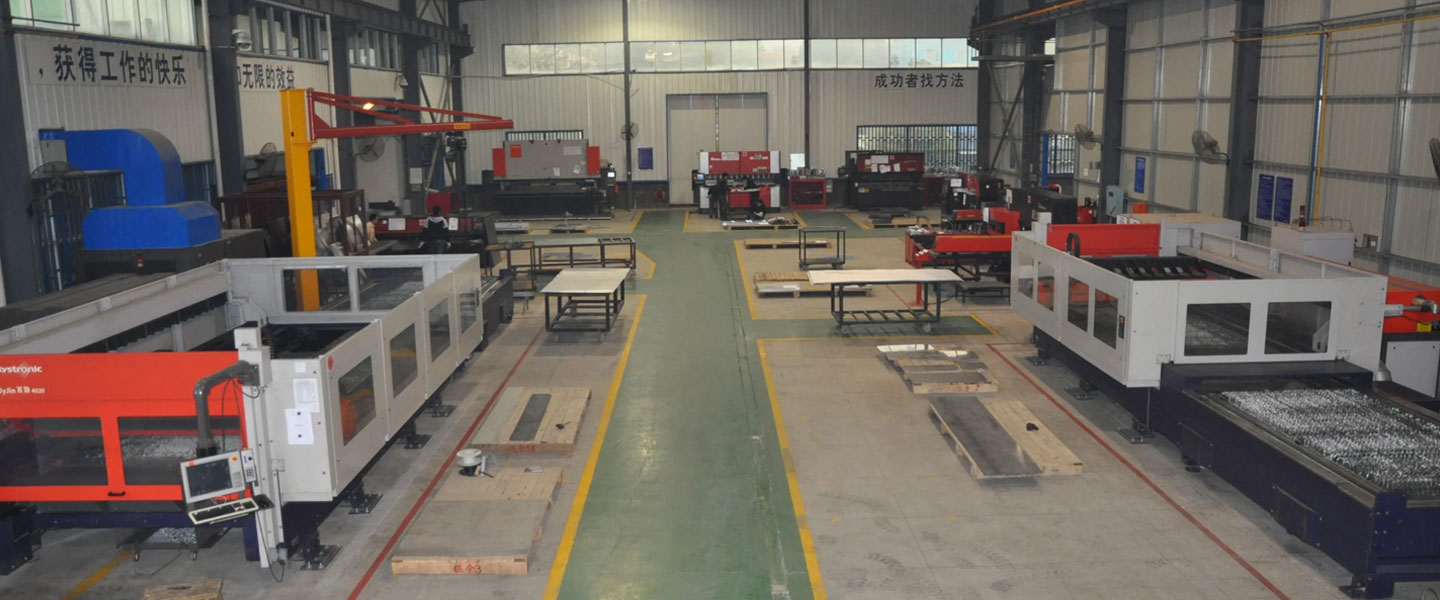
Pintejin Sheet Metal shop offers a cost-effective solution for a wide range of industries with our custom metal stamping and custom sheet metal fabrication capabilities. Our stampnig operations include a variety of sheet-metal forming manufacturing processes, such as punching, blanking, embossing, bending, flanging, and coining. Our professional, experienced and well-trained engineers can execute the complex metal stamping operations with precision and accuracy.
No matter what your metal fabrication needs are, Pintejin can offer the right solution: from single sheet metal part or sub-assembly of stamped metal parts to turnkey solutions for mechanical and electrical assemblies. We have the technology, equipment and the experience to fabricate customised metal products from aluminium sheet metal fabrication, steel, zinc plated steel, stainless steel sheet metal fabrication, brass and copper. Designs that require CNC machining of surfaces or components can be accommodated. We can supply polished, galvanized, zinc coated or powder coated finishes for any sheet metal work or stamped metal components. Coupled with our accurate and reliable metal fabricating equipment, we guarantee precision and repeatability in custom sheet metal work. You’ll be taking advantage of the best sheet metal fabrication china can produce.