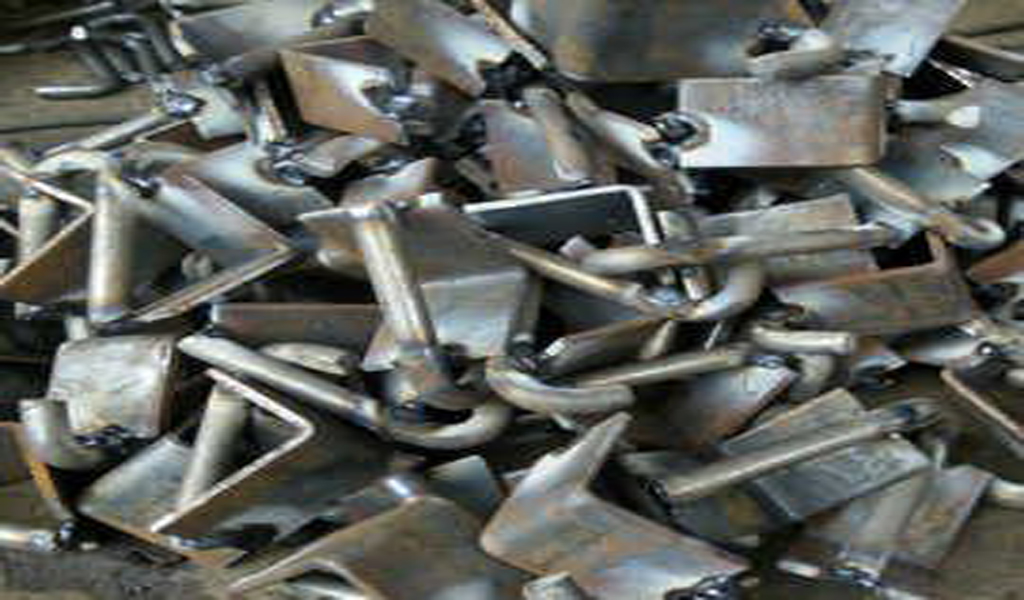
Stamping is a production technology of product parts with a certain shape, size and performance, by means of the power of conventional or special stamping equipment, so that the sheet is directly subjected to deformation force in the mold and deformed. Sheet material, mold and equipment are the three elements of stamping fabrication. Stamping is a metal cold deformation fabrication method. Therefore, it is called cold stamping or sheet stamping, or stamping for short. Rongzhi Auto Stamping says that it is one of the main methods of metal plastic fabrication (or pressure fabrication), and it is also subordinate to material forming engineering technology.
Of the steel in the world, 50-60% are made of sheets, most of which are finished products that have been pressed. Car body, radiator fins, steam drums of boilers, shells of containers, iron core silicon steel sheets of motors and electrical appliances, etc. are all stamped and processed. There are also a large number of stamping parts in instruments, household appliances, office machines, storage utensils and other products. Stamping is an efficient production method, using composite molds, especially multi-station progressive molds, which can complete multiple stamping technical operations on one press to complete the automatic generation of materials. The production speed is fast, the rest time is long, the production cost is low, and the collective can produce hundreds of pieces per minute, which is favored by many fabrication plants.
Compared with castings and forgings, automobile stamping parts have the characteristics of thinness, uniformity, lightness and strength. Stamping can produce workpieces with reinforcing ribs, ribs, coils or flanges that are difficult to manufacture in this skilled diameter to improve their rigidity. Rongzhi Auto Stamping said that due to the rejection of rough molds, the workpiece precision can reach micron level, with high precision and consistent specifications, and can punch out holes, bosses, etc. In actual production, technical tests similar to the stamping process are often used, such as deep drawing performance tests, bulging performance tests, etc. to test the stamping performance of materials to ensure the quality of finished products and high pass rate.
Stamping equipment usually adopts stagnation press except for thick plate forming with water press. Focusing on modern high-speed multi-station stagnation presses, the equipment is equipped with stagnation such as unwinding, finished product collection, conveying, as well as die storage and quick die change placement, and the use of computerized tube bundles can form passive stamping production with high production rate and high production rate. Wire.
The stamping direction of the part is the first problem to be encountered in determining the stamping process. It not only determines whether a satisfactory stamping part can be stretched, but also affects the number of process supplements and the shape of the pressing surface. Reasonable determination of the stamping direction of stamping parts should meet the following three requirements, Rongzhi automotive stamping parts analysis:
- (1) It can ensure that the punch can enter the die.
- (2) Make the area where the punch contacts the blank large. The larger the contact surface, the smaller the angle between the contact surface and the horizontal plane. The rougher is less prone to local stress overloads that cause parts to crack. When the material is stretched, the die attach performance is improved, and it is easy to obtain a complete punch shape, which is beneficial to improve the deformation degree of the part.
- (3) The feeding resistance of each part of the pressing surface should be uniform and reliable. Uniform drawing depth is the main condition to ensure uniform and reliable feeding resistance of each part of the pressing surface. The uniform feeding resistance of each part of the pressing surface is an important guarantee to ensure that the stamping parts are not wrinkled or cracked.
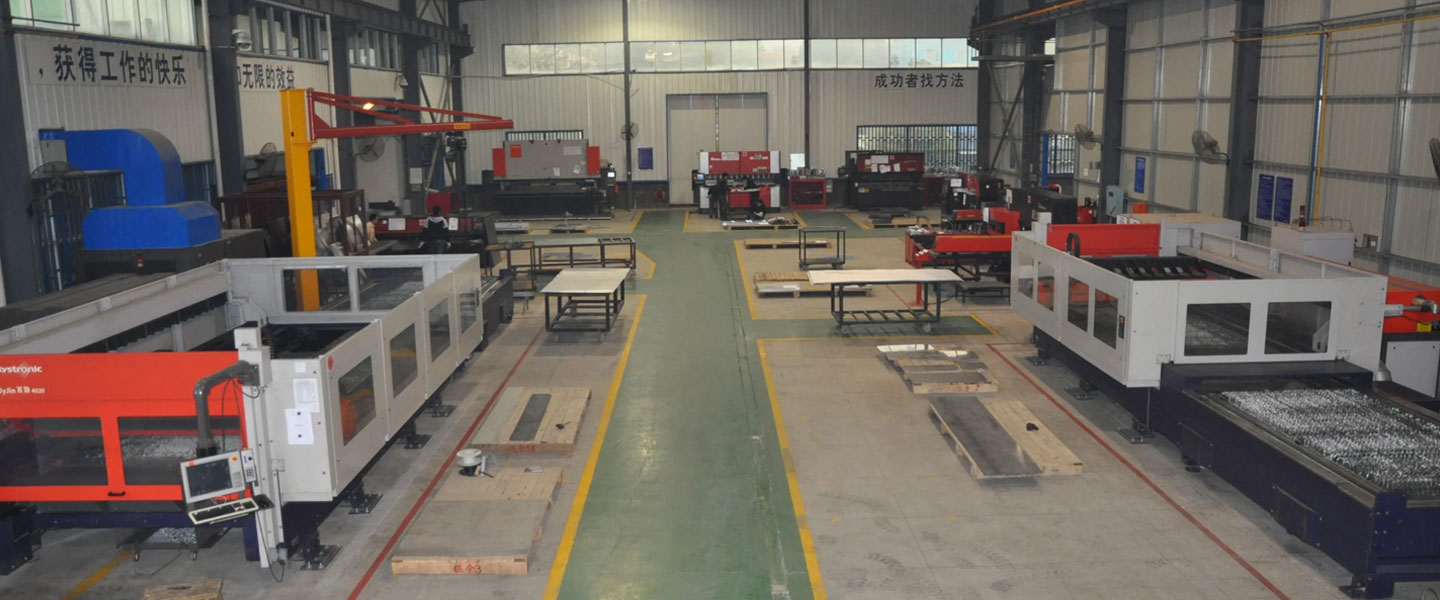
Pintejin Sheet Metal shop offers a cost-effective solution for a wide range of industries with our custom metal stamping and custom sheet metal fabrication capabilities. Our stampnig operations include a variety of sheet-metal forming manufacturing processes, such as punching, blanking, embossing, bending, flanging, and coining. Our professional, experienced and well-trained engineers can execute the complex metal stamping operations with precision and accuracy.
No matter what your metal fabrication needs are, Pintejin can offer the right solution: from single sheet metal part or sub-assembly of stamped metal parts to turnkey solutions for mechanical and electrical assemblies. We have the technology, equipment and the experience to fabricate customised metal products from aluminium sheet metal fabrication, steel, zinc plated steel, stainless steel sheet metal fabrication, brass and copper. Designs that require CNC machining of surfaces or components can be accommodated. We can supply polished, galvanized, zinc coated or powder coated finishes for any sheet metal work or stamped metal components. Coupled with our accurate and reliable metal fabricating equipment, we guarantee precision and repeatability in custom sheet metal work. You’ll be taking advantage of the best sheet metal fabrication china can produce.