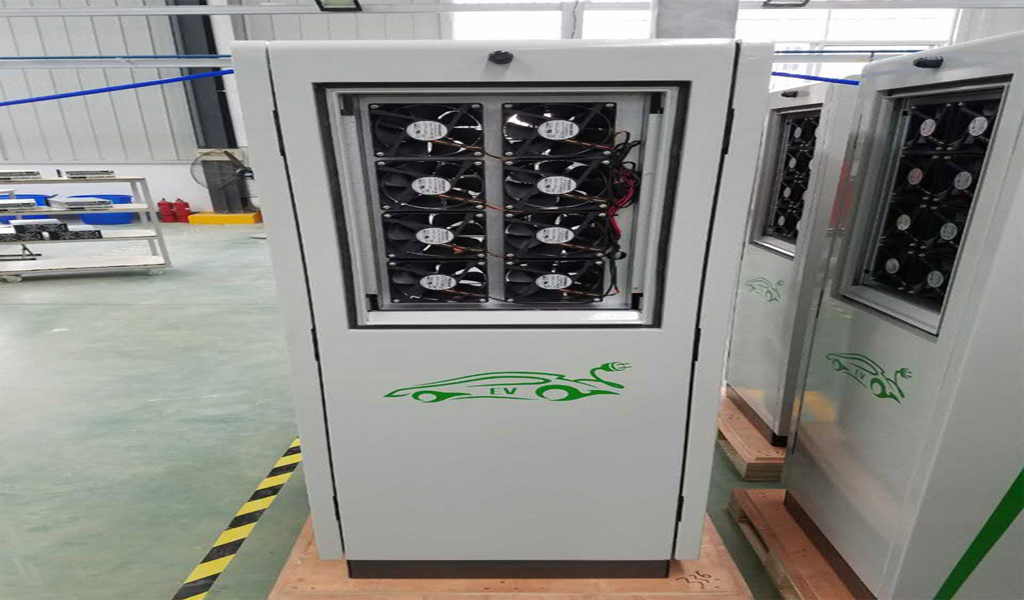
Stamping die is an important process equipment in stamping production for precision stamping parts fabrication plants. The durability of punches and punches is determined by the total number of parts punched by the punches under the condition that the punches and punches lose their working size due to frequent wear and tear after working for a period of time, and can no longer satisfy the technical conditions of the parts. From planning, machining, installation, adjustment to installation, a pair of punching die has many processes, long cycle and high fabrication cost. Therefore, for punching die, in addition to requiring high production efficiency and the punched parts fully meet the quality requirements and technical conditions, the punching die Durability itself is also important.
Stamping die is a special process equipment for fabrication into parts in cold stamping fabrication. It is widely used in process production, but there may be wear during the process of use. What should I do if the stamping die is found to be worn?
The quality of the working parts of the die and the surface quality has a very close relationship with the wear resistance, anti-cracking ability and anti-adhesion ability of the die, which directly affects the service life of the die. In particular, the surface roughness value has a great influence on the life of the die. If the surface roughness value is too large, stress concentration will occur during operation, and cracks will easily occur between its peaks and valleys, which will affect the durability of the die, and also It affects the corrosion resistance of stamping parts and directly affects the service life and accuracy of the die. For this reason, the following matters should be paid attention to:
- 1. Replace the worn stamping die guide components and punches in time.
- 2. Check whether the gap of the stamping die is unreasonable (small), and increase the gap of the lower die.
- 3. Minimize wear, improve smooth conditions, smooth plates and punches. The amount of oil and the number of oil injections depend on the fabrication conditions. For cold-rolled steel plates, corrosion-resistant steel plates and other rust-free treatment, oil should be injected into the mold. The oil injection points are guide bushes, oil injection ports, and lower molds. Use light motor oil. If there is rust treatment, the rust fine powder will be sucked between the punch and the guide sleeve during fabrication, resulting in dust and dirt, so that the punch cannot slide freely in the guide sleeve. In this case, if oil is applied, it will make the rust easier Therefore, when rushing this kind of treatment, on the contrary, the oil should be wiped clean, separated once a month, and the dust on the punch and the lower die should be removed with gasoline (diesel) oil, and then wiped clean before reassembling. This ensures that the mould has excellent smooth properties.
- 4. The sharpening method is inappropriate, resulting in annealing of the mold and aggravating the wear and tear. A soft abrasive grinding wheel should be used, a small amount of knife cutting, a sufficient amount of coolant, and frequent cleaning of the grinding wheel
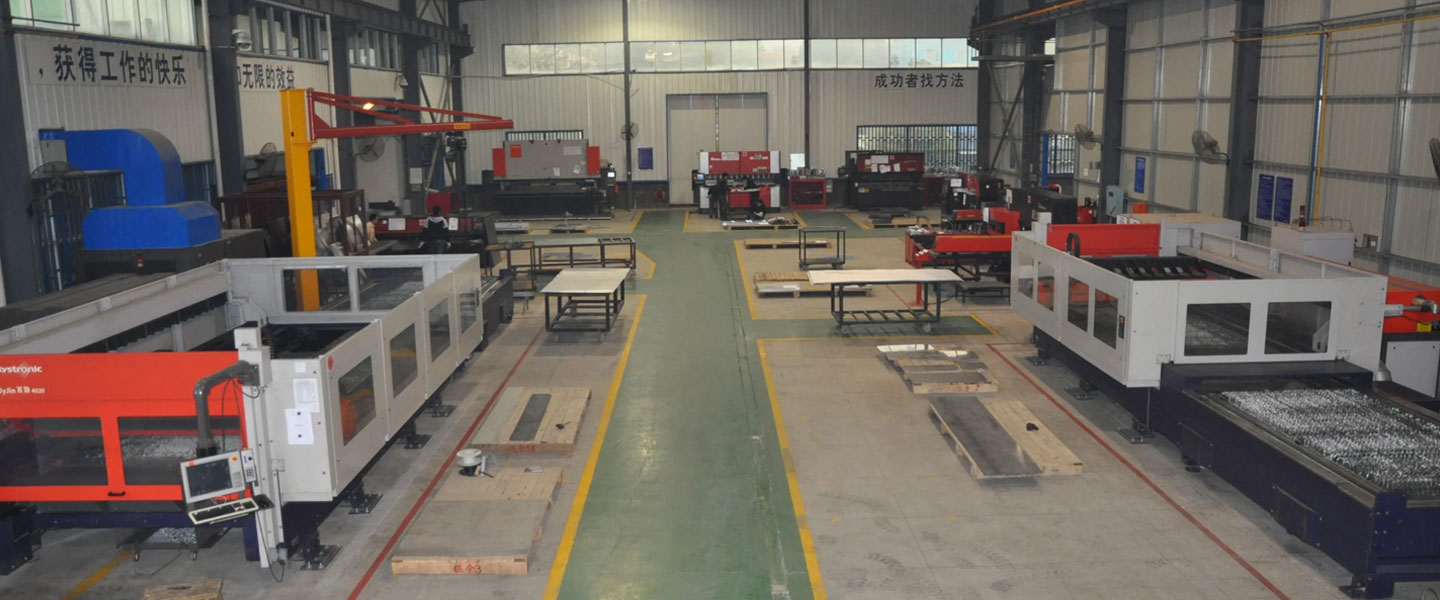
Pintejin Sheet Metal shop offers a cost-effective solution for a wide range of industries with our custom metal stamping and custom sheet metal fabrication capabilities. Our stampnig operations include a variety of sheet-metal forming manufacturing processes, such as punching, blanking, embossing, bending, flanging, and coining. Our professional, experienced and well-trained engineers can execute the complex metal stamping operations with precision and accuracy.
No matter what your metal fabrication needs are, Pintejin can offer the right solution: from single sheet metal part or sub-assembly of stamped metal parts to turnkey solutions for mechanical and electrical assemblies. We have the technology, equipment and the experience to fabricate customised metal products from aluminium sheet metal fabrication, steel, zinc plated steel, stainless steel sheet metal fabrication, brass and copper. Designs that require CNC machining of surfaces or components can be accommodated. We can supply polished, galvanized, zinc coated or powder coated finishes for any sheet metal work or stamped metal components. Coupled with our accurate and reliable metal fabricating equipment, we guarantee precision and repeatability in custom sheet metal work. You’ll be taking advantage of the best sheet metal fabrication china can produce.