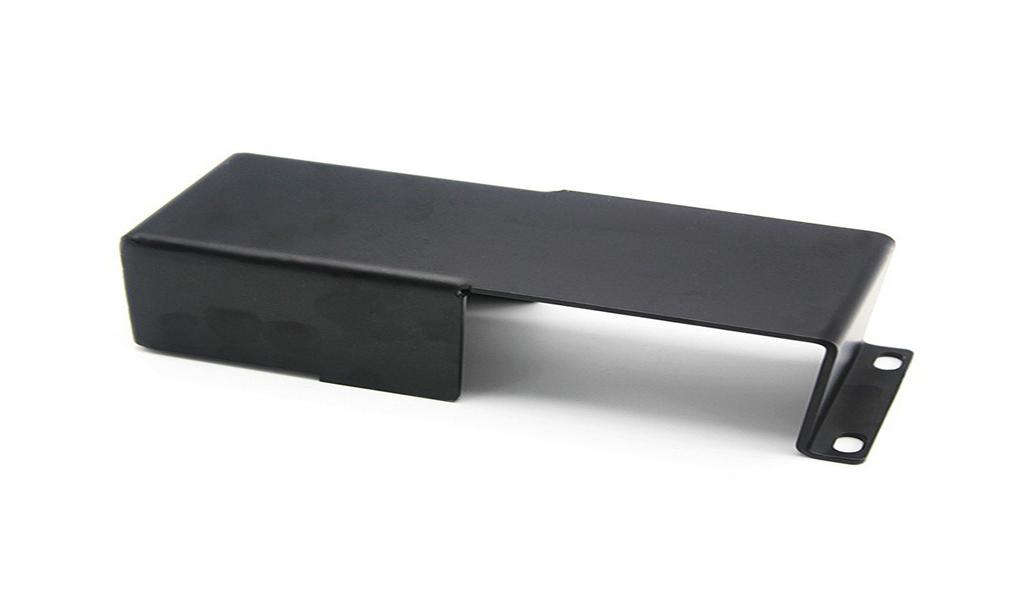
Stamping process is one of the fabrication methods to complete metal plastic forming. Usually, presses and dies are used to apply external force to plates, strips, pipes and profiles to cause plastic deformation or separation, so as to obtain workpieces of desired shape and size. Such as various covers on the body, interior supports, structural reinforcements, and a large number of auto parts, such as engine exhaust elbows and mufflers, hollow camshafts, oil pans, engine brackets, frame structures , horizontal and vertical beams, etc., are all developed by stamping technology in the direction of precision, multi-functional, high-efficiency, energy-saving, safe and clean production. The manufacturing process level and quality of stamping workpieces have a direct impact on the quality of automobile manufacturing to a large extent. Impact. The following introduces the development trend of automobile stamping parts process:
1. Adaptive selection of stamping process
The adaptability of the stamping process means whether the designed stamping parts meet the technological requirements of stamping fabrication in terms of size, dimensional accuracy and benchmark, structural shape, etc. Automotive stamping parts should have good craftsmanship and economy. The important indicators to measure their level are the number of stamping parts, the number and size of the body assembly, and the structure of stamping parts.
Reducing the number of steps in the stamping process means reducing the number of stamping parts, saving the number of tooling, simplifying the conveying device of the stamping process, reducing the operator and stamping area, which is an excellent measure to save investment and energy consumption. Moreover, modern automobiles manufacture a large number of high-strength steel sheets and galvanized steel sheets with coiled, thin-shell integral body structures, and require the application of new stamping processes.
2, the development trend of modern stamping technology
(1) Modular stamping technology
The outstanding advantage of modular stamping is that it can organically combine the flexibility of the stamping fabrication system with efficient production. Flexibility has a broad meaning, such as various requirements for the geometric shape of stamping parts, which can be obtained through free programming, which reflects the flexibility of the fabrication shape. Another example is that it is not only suitable for the production of large-scale single-variety stamping parts, but also has the advantage of small-batch and multi-variety fabrication, and also shows flexibility
(2) Sub-millimeter stamping technology
Sub-millimeter stamping technology means that the precision of the stamping parts of the automobile body is controlled within the range of millimeters, which is a very big improvement compared with the errors commonly used in the manufacturing industry in the past. This is a comprehensive project aimed at improving stamping quality and manufacturing technology.
The center of sub-millimeter stamping is the accuracy and sensitivity of the stamping parts. The accuracy is to control the dimensional accuracy of the stamping parts at the level of millimeter or sub-millimeter. The body covering parts have a large degree of segmentation, such as the use of integral left and right side panels and top cover panels. The meaning of sensitivity refers to including mold design, sample manufacturing and tooling preparation time to achieve the purpose of greatly shortening the manufacturing cycle of new models. The project includes integrated design of stamping and assembly, sensitive design and manufacturing of stamping system, and stamping process. Intelligent detection and monitoring, system-wide integration, etc.
(3) Special stamping forming technology
The technical requirements of modern automotive stamping parts are developing in the direction of complex structure, increased block size, more components on related sides, increased bearing capacity and strict internal stress restrictions. This requires and promotes the development of special stamping forming technologies such as hydroforming, precision forming, explosive forming, spin forming, dieless forming, laser forming and electromagnetic forming.
(4) Automatic monitoring of stamping process
Another important feature of modern stamping technology is the automatic monitoring of the stamping process to protect the quality of stamped parts. In the automatic detection and monitoring of sub-millimeter stamping projects, its research results include: 1. On-line transmission diagnosis and detection system for feature analysis of stamping process; 2. High-speed and non-contact stamping parts measurement system; 3. Die maintenance Scientific guessing system; 4. Online adjustment and compensation system for key parameters of stamping forming, etc.
The main reasons for the changes in the quality of the workpiece caused by the stamping process are the wear of the concave and convex dies, cracks and dislocation of the dies, etc. These small changes can be tracked and detected by high-resolution displacement transducers and stamping force transducers. Among them, displacement measurement is a very important measurement. The device is usually composed of a source installed above the mold and a receiving unit located below it. It can monitor deviation, track the whole process of fabrication, output monitoring information in time, and alarm and stop.
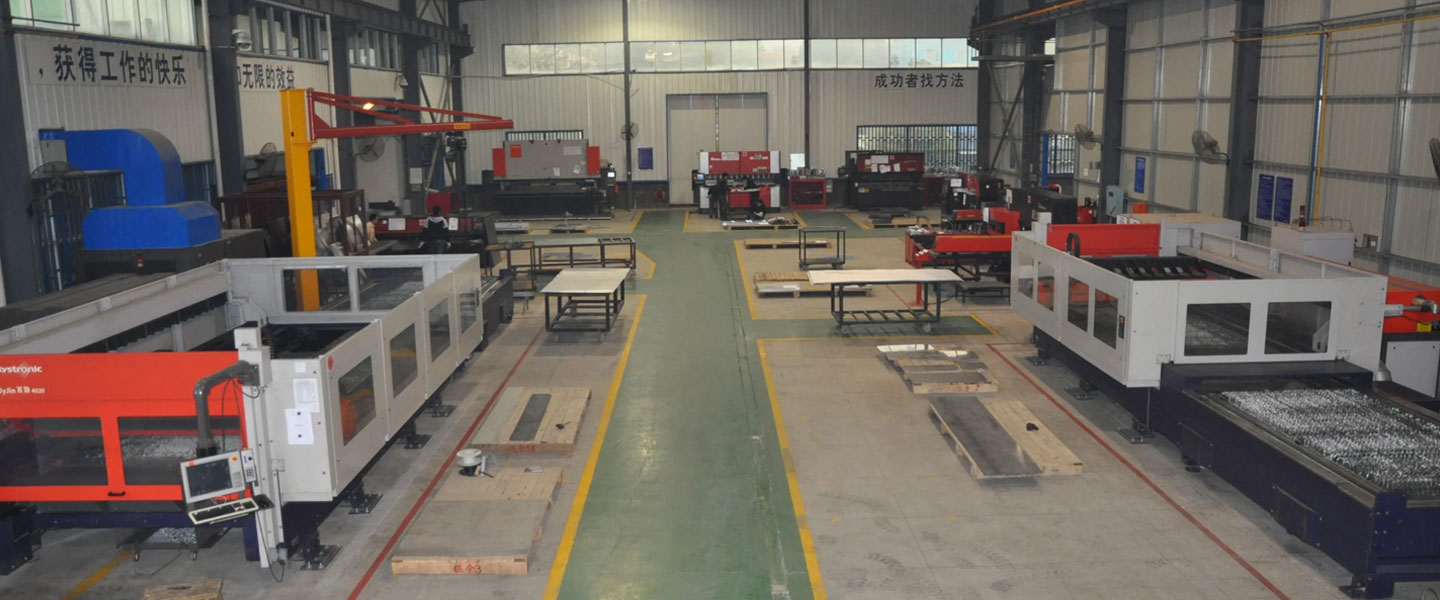
Pintejin Sheet Metal shop offers a cost-effective solution for a wide range of industries with our custom metal stamping and custom sheet metal fabrication capabilities. Our stampnig operations include a variety of sheet-metal forming manufacturing processes, such as punching, blanking, embossing, bending, flanging, and coining. Our professional, experienced and well-trained engineers can execute the complex metal stamping operations with precision and accuracy.
No matter what your metal fabrication needs are, Pintejin can offer the right solution: from single sheet metal part or sub-assembly of stamped metal parts to turnkey solutions for mechanical and electrical assemblies. We have the technology, equipment and the experience to fabricate customised metal products from aluminium sheet metal fabrication, steel, zinc plated steel, stainless steel sheet metal fabrication, brass and copper. Designs that require CNC machining of surfaces or components can be accommodated. We can supply polished, galvanized, zinc coated or powder coated finishes for any sheet metal work or stamped metal components. Coupled with our accurate and reliable metal fabricating equipment, we guarantee precision and repeatability in custom sheet metal work. You’ll be taking advantage of the best sheet metal fabrication china can produce.